Bud Snodgrass: Oils Well That Ends Well
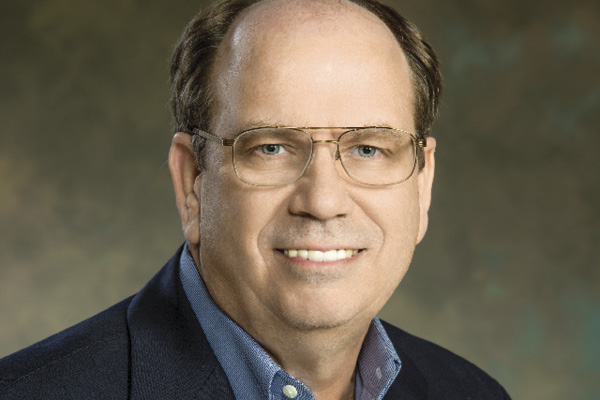
Bud Snodgrass is director of logistics at Universal Lubricants in Wichita, Kansas. He joined the company in 2013.
Responsibilities: Distribution, including warehousing and customer service at 17 distribution centers; all inbound and outbound transportation.
Experience: Several positions in marine claims, scheduling and distribution, sales, and other areas, Koch Industries; account executive, Trane – Asset Management Services; vice president of global logistics, The Coleman Company; director of North American operations and supply chain, Elmer’s Products; managing director, Zesta Golf
Education: BBA, Wichita State University
Universal Lubricants creates its products from recycled oil that we collect from other petrochemical companies throughout the United States. We have it tested, then ship it to our re-refinery in Wichita.
There, we create EcoClear, an extremely pure, water-white base oil, which we sell to other manufacturers and use as the basis for our own products. We sell our products through a variety of channels for use in manufacturing, agriculture, transportation, and other industries.
I’m responsible for the company’s transportation, which includes shipping used oil to the re-refinery, moving product to our 17 warehouses, and distributing from there to customers. We use a range of equipment, from 53-foot vans to bulk trucks to rail cars.
For many shipments into or between our own facilities, we use commercial carriers. But we also operate a fleet of about 240 power units and 80 trailers to transport product from our distribution centers.
This is the first job where I’ve been responsible for a sizable fleet employing drivers on the payroll. Driver retention and equipment maintenance are big challenges in our industry, but the biggest challenge we face is safety.
Transportation and distribution operations comprise a lot of moving parts—workers driving forklifts, picking product, and maneuvering trucks into tight spaces at customer facilities. Promoting safety in that environment is a continuous effort.
One strategy we use is behavioral safety training. Employees commit to pointing out unsafe practices so we can correct problems. Getting workers involved is key to creating a safe environment.
One satisfying period in my career is the four years I spent at the Coleman Company, a camping equipment manufacturer. The company was in trouble at the time, and a friend I had worked with at Koch Industries recruited me to help improve Coleman’s operations—an effort that included moving some manufacturing to China.
We spent two years in what I call painful reorganization. One major challenge was building a department to unite demand planning and supply planning, to ensure Coleman would always have products where it needed them, when it needed them.
A personal challenge was taking on responsibility for managing customs, which I had never done before. It took a while to get all our processes in place. Then, about one year into the project, U.S. Customs and Border Protection announced it would audit us. Eventually, we hired a manager to help ensure compliance.
We endured a lot of pain, and worked many long hours. But through some heroic efforts, we were able not only to save an iconic brand, but also to keep the company in business. Coleman is doing very well today, and I am proud of the role I played in that accomplishment.
The Big Questions
How do you unwind?
I work out, play basketball with my sons, and go golfing with friends.
When you were a child, what did you want to be when you grew up?
My dad made a career in the Air Force, so through much of my childhood I wanted to be a fighter pilot, then a commercial airline pilot.
What does it take to build a great logistics team?
Through its communications and actions, a logistics team must make sure customers know how much you care about them. You have to align with excellent partners to help serve those customers, and you have to treat partners as well as you do customers.
What work-related mistakes have you found most instructive?
Ego lies at the root of many mistakes. Developing a continuous improvement culture begins with checking your ego. When you realize that everybody is working to find the best answer, not advocating their version of the right answer, it becomes easier to solve problems and minimize errors.