How to Mitigate Supply Chain Disruptions
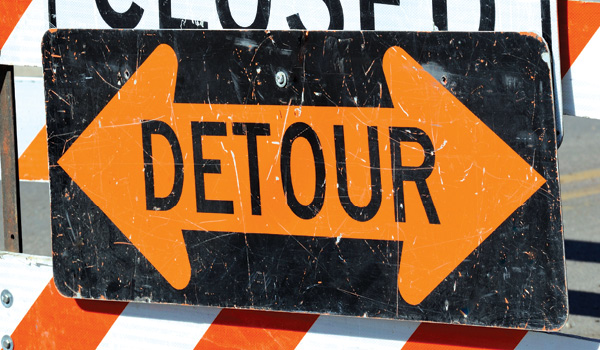
As supply chains trend toward demand-driven, lean inventory models to eliminate waste, reduce costs, and increase responsiveness, their exposure to risk grows. When natural disasters, political upheaval, labor strife, supplier failures, and countless other types of supply chain events arise, shippers need to react quickly—without incurring undue costs—to keep production in line with demand.
Companies often become vulnerable to supply chain disruptions when they don’t have a holistic view of their operations. It may be a matter of poor visibility among offshore suppliers, or not having adequate transportation flexibility to re-route shipments on the demand side—and countless areas in between. When exceptions occur and manufacturers are left without critical parts or retailers face stockouts, the risk of tarnishing brand value—or, even worse, losing customers—increases exponentially. A short-term supply chain glitch can have long-term repercussions to the bottom line if not handled quickly and effectively.
5 Risk Mitigation Considerations
Shippers should regularly evaluate their risk exposure and perform a cost/benefit analysis to ensure they have a resilient and responsive supply chain.
- Recognize risk factors. Prior knowledge about potential environmental, social, and political conditions can help companies prepare contingency plans. Having total supply chain visibility, whether it’s through an internal control tower approach or via a 3PL partner, can also help screen problems before they surface.
- Evaluate geographic coverage. Sourcing strategies are largely dictated by the complexity of a company’s supply chain. When critical parts are involved, a single-source strategy presents obvious problems when a manufacturing facility shuts down and the supply chain grinds to a halt. Companies need to assess their vulnerability if they cannot acquire certain components or parts. Do you have scalability to ramp up production in other locations to meet demand? Can you justify using a secondary or tertiary sourcing strategy, perhaps near-shoring closer to demand? Does it make sense to partner with a 3PL that can provide cover in case of a disruption?
- Build in transport flexibility. Shippers need flexibility to change routings, modes, and carriers, and stage/stockpile inventory. Proper risk management strategy favors redundancy—for example, having infrastructure and/or partnerships in place to pull shipments through different ports.
Companies should also consider how they structure transportation contracts. It may be economical to negotiate directly with carriers and lock up capacity, but that approach also limits shippers’ flexibility to shift capacity when problems arise. Some freight buyers will split their volumes among different carriers and third-party logistics intermediaries as a means to allay risk. - Leverage technology and social media. One benefit of social media is the ability to capture and vet critical information in real time. Some supply chains are using social networking in the cloud as a predictive analysis tool to identify problem suppliers before shortages are felt downstream in the supply chain. Cloud networking also provides a platform for facilities isolated or impacted by supply chain disruptions to more quickly get back on line; and for companies to on-board new business partners as need dictates.
- Lean on third-party logistics providers. Transportation and logistics outsourcing used to be a matter of divesting non-core need for economy purposes. Now risk aversion is also a primary driver. 3PLs have on-the-ground resources, local knowledge, and experience to execute contingencies and minimize risk.