Logistics Grads Suit Up for the Future
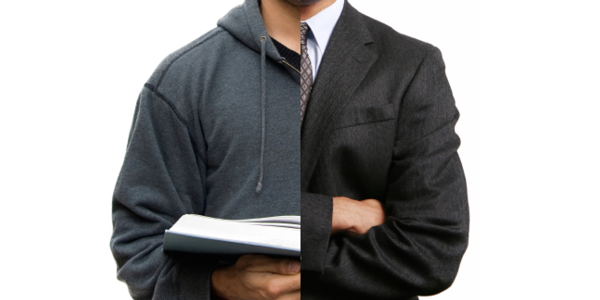
Universities and corporations are working together to arm logistics graduates with the skills they need to move from the classroom to the conference room.
With global trade likely to rise more than threefold to $27 trillion by 2030, logistics professionals are in high demand, according to Winning the Talent Race, a report by professional services firm PwC.
In fact, the U.S. logistics sector is expected to create more than one million job openings between 2013 and 2016, according to the U.S. Department of Labor.
Yet a significant gap exists between the skills logistics companies need, and those today’s college graduates bring to the table.
"The success of companies such as Walmart demonstrates the growing importance of supply chain and logistics, but education has not kept up with this shift," says Raymond Boykin, Ph.D., a member of Prince George, Va.-based Commonwealth Center for Advanced Logistics Systems (CCALS). "Many schools aren’t educating students about the importance of logistics in today’s global economy."
Many employees in the transport sector have medium or low qualification levels, according to the PwC report, and the sector’s need for better-educated workers is increasing.
"Ensuring enough skilled candidates are available—along with suitable advancement options for talented staff—won’t be easy, but it is critical to future success," says the report. "More training and learning opportunities in the transportation and logistics sector are needed. Such programs could help increase the available labor pool."
But generating more skilled workers is not solely an education issue. "Schools and industry need to work together to make a difference," says John Taylor, associate professor and chair of the department of marketing and supply chain management at Wayne State University’s School of Business Administration in Detroit. "Educational institutions can’t do it alone. They need to work closely with businesses to understand their issues and needs."
Working Together
Building the new logistics workforce is truly a team effort. "Companies, schools, governments, and nonprofits must do more to identify, recruit, train, and employ skilled workers," says Dr. Sime Curkovic, professor of supply chain management at Western Michigan University (WMU) in Kalamazoo, and the director of the integrated supply management program.
"Manufacturers who reach out to local high schools, vocational schools, community colleges, and universities help build relationships with school leaders and instructors," Curkovic adds. "This outreach also helps companies shape training programs to ensure they teach relevant skills to future workers."
An array of collaborative logistics education programs—involving public schools, universities, government agencies, and corporations—already exists in the United States. For example, Purdue University in West Lafayette, Ind., and Ivy Tech Community College in Carmel, Ind., recently received nearly $900,000 in grants to address the skills gap and technical demands in Indiana’s supply chain, logistics, and manufacturing operations workforce. Through the project, the schools will provide a diverse population of college students with a direct pathway for earning both their associate’s and bachelor’s degrees in the field of technology-based logistics.
The grants will also fund projects such as working directly with Indiana’s K-12 schools to inform students about educational and career opportunities in logistics; developing curricula for Ivy Tech and Purdue; and implementing an outreach and recruitment program to encourage Ivy Tech associate’s degree students to continue their education.
Other universities are focusing on introducing project-based work and internship opportunities specifically aimed at providing students with real-world logistics experiences. At WMU, several corporations provide students with hands-on lean manufacturing projects for coursework and training.
The university has been working closely with industry for five years, and students have completed more than 100 projects. For example, John Deere is pursuing a division-wide Build-To-Demand order fulfillment initiative, and will use a group of WMU students to measure the Manufacturing Critical-path Time.
Filling the Labor Pool
"The partnership with industry came about because WMU met with businesses, and saw the demand," says Curkovic. "Kalamazoo is not a huge geographic area, but it is surrounded by many companies that recruit heavily from our supply chain program. The industry representatives want to ensure that students graduate with an understanding of key logistics challenges, and are prepared to begin work at a company knowing how to do things better, faster, and cheaper.
"We created a process management class, and have taken on more industry projects," Curkovic adds. "We are no longer just talking about these concepts in the classroom—we are applying them in the workplace."
One WMU project involved Portage, Mich.-based Mann-Hummel USA, an original equipment supplier to the international automotive and mechanical engineering industries. The company was experiencing huge growth, and running out of material storage space at its Portage production facility.
To manage this growth, Mann-Hummel was using an off-site warehousing strategy incorporating just-in-time Lean methods such as kitting, kanban, and regular milk runs to bring materials to the plant. This strategy was working well for the company, but it offered room for improvement.
A group of WMU students, led by Curkovic, collaborated with Mann-Hummel to define a set of plastic hand totes that could be employed to store 250-plus raw materials the company uses in production. The project included measuring repackaging times and costs, determining which hand totes worked best for each raw material, and obtaining a quote from a product manufacturer for the estimated number of containers necessary to implement the hand tote system.
"Most students don’t have work experience to include on their resume when they graduate, but collaborative projects open doors for them to gain that experience," says Curkovic. "And many companies evaluate students as potential future employees."
Another WMU project involved Battle Creek, Mich.-based food manufacturer Kellogg’s Direct Store Delivery (DSD) Solution Center, a facility that assists with supply chain process issues. The solution center’s analysts mainly focus on solving day-to-day issues with the delivery of Kellogg’s snack products. It is a sector of the company that is vital as Kellogg’s continues to acquire more business.
Delivery refusals, driver delays, and order status are frequent problems that DSD Solution Center analysts must resolve. The WMU team was asked to find opportunities for process improvement, and time and cost savings.
After some research and hands-on experience in the solution center, the WMU team identified both simple and complex solutions, including a new call center phone system, a truck driver instruction sheet, additional staff, integrated information database systems, and eliminating static routes.
Building Beneficial Relationships
Wayne State University’s School of Business Administration is currently collaborating with Detroit automaker General Motors to introduce students to the issues and challenges involved in producing vehicles.
For the Wayne State University/General Motors Supply Chain Case Competition—which recently completed its third year—business students from across the country came to Detroit for an in-depth look at the supply chain systems that support the automotive industry. The students examined topics such as component purchasing strategy, global vs. domestic sourcing, risk management, and battery production locations.
"The competition presents an opportunity to showcase Southeast Michigan’s automotive industry and supply chain management careers, as well as provide students an outstanding real-world educational experience," says Taylor. "Additionally, students were able to interview with automotive companies, and participate in several panel sessions on supply chain careers.
"The auto industry has a huge need for students," he adds. "We have to make sure we are getting the best students in front of industry leaders to ensure those matches happen."
At Ohio State University in Columbus, the Fisher College of Business works with several companies as part of its supply chain management program. The college hosts both a global supply chain forum—which consists of 12 companies that help guide research and curriculum—and the Center for Operational Excellence, which has 38 member companies and is instrumental in shaping the school’s supply chain curriculum. The college also operates a successful internship program.
Plugging into Industry
"We seek industry guidance in devising our curriculum and executing our programs," says Dr. Thomas J. Goldsby, professor of logistics at Ohio State University. "We plug in to industry any way we can, whether it’s inviting guest speakers to campus or through class projects. These experiences allow students to learn about business and the real logistics challenges companies face."
Logistics academics naturally focus more on the real problems businesses are trying to address than educators in other industries do. "We are fortunate to be in a field that has a good working relationship with industry," Goldsby says. "Businesses are interested in our curriculum and the research we do on campus, and they want to be part of both."
Other types of organizations are also working to bridge the talent gap between logistics companies and educational institutions.
CCALS, for example, is a collaborative effort between business, government, and several Virginia universities. Formed in December 2012, CCALS strives to improve the technological, mechanical, and human factors that enable logistics. Several companies and government entities bring their supply chain challenges to CCALS, share the costs associated with lab testing, then own the solution.
"Our goal is to work together on solving industry issues such as supply chain risk and disruption, distribution and transportation networks, and logistics security and information technology systems," says Boykin. "But we also seek to develop talent, so when a participating company needs employees with specific skill sets, they know where to find them.
"CCALS brings universities and companies together," he adds. "The companies inform the universities as to what skill sets they need from graduates, and the universities adjust to meet those needs."
Creating a Win-Win
Another organization working to bridge the logistics talent gap is the Transportation Club of Atlanta, which recently launched a program to provide paid internships for students majoring in logistics at Clayton State, Georgia Southern, Georgia Tech, or Kennesaw State. Companies including Unisource, Coca-Cola, Home Depot, and Rubbermaid have signed on to participate in the summer 2014 program.
"Employment is one of the biggest problems in Georgia," notes Jeremy Estep, president of the Transportation Club of Atlanta. "Many organizations want to hire students, but don’t have the resources to go out to the universities to recruit. Our goal is to act as an intermediary, and facilitate that process."
The program is a win-win, Estep notes. "The companies win because they get transportation, logistics, and supply chain interns who want to be in this industry," he says. "Companies are exposed to up-and-coming talent, and can identify students with management potential, perhaps saving the expense of formally hiring someone who wouldn’t have worked out.
"Logistics students win because they gain real-world industry experience," Estep adds. "When these students graduate, they will be a hot commodity because they have both education and experience."
Another aspect vital to the future of logistics is raising the sector’s profile in the education system. Many students are not aware of logistics and its potential as a career field, because many high school level career development programs do not include logistics and transportation.
Part of WMU’s program involves outreach to local high schools. "We introduce junior high and high school students to supply chain management through some classroom exercises," says Curkovic.
CCALS offers a dual-enrollment program in which high school and community college students can take, and receive credit for, Virginia State logistics courses. "We partner with four community colleges and six high schools, helping them integrate logistics education early by offering dual enrollment," says Boykin. "It is important to introduce students to logistics before college, because by that point, many have already decided where they will focus their studies."
On the other end of the spectrum, several universities are investing in continuing education and/or graduate programs to help logistics professionals keep up with changing industry demands. For example, WMU recently launched an executive education program in which industry managers team with faculty, alumni, and current students to help solve real-world logistics challenges. In some cases, the university is finding this model financially beneficial.
"We ask logistics managers about their challenges, and whether we can help with specific projects," says Curkovic. "The executive education projects have gone so well, some managers are willing to pay us with some of the cost savings we generate for them. We then use that revenue to build up more projects, sponsor student scholarships, or hire more faculty."
Mastering Competitive Advantage
Industry professionals often teach executive education and graduate-level logistics courses, allowing for further cross-pollination.
"The logistics and supply chain sector gained a head start over other industries because collaboration is ingrained in it," says Carole Bennett, M.B.A. director of program development and marketing at the Georgia Tech Supply Chain and Logistics Institute in Atlanta. For example, professionals from Florence, Ky.-based logistics provider LeanCor teach the institute’s professional certificate series classes.
"Schools with a tradition of working with industry will be better at producing students with the skill sets needed in the future," Bennett notes.
Many universities and businesses claim the general population lacks awareness about logistics and how it touches every part of our lives. Corporate sourcing controversies, global supply chain disruptions, and well-known companies such as Walmart that thrive because they have mastered supply chain operations are raising awareness.
"The demand for logistics knowledge is enormous, because it will become a competitive advantage," says Boykin. "Many manufacturing companies are trying to cut costs anywhere and everywhere they can, and they are beginning to see logistics and distribution as a source of low-hanging fruit.
"Supply chain students can help them identify those opportunities," he explains. "Putting students to work in real-life logistics scenarios enables them to respond to industry needs and help identify solutions."
By working together, education, industry, and other partners may help bridge the gap between what logistics companies need and the skills today’s college graduates bring to the table. Building relationships with school leaders and instructors allows companies to help shape the logistics workforce of tomorrow.