Expedited Carriers: The Fast and the Furious
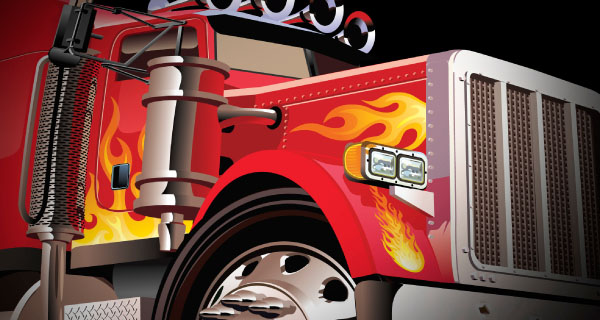
Logistics technology helps turbo-charged expedited carriers move freight for shippers with an extreme need for speed.
In the adrenaline-fueled, high-stakes world of expedited deliveries, excuses don’t go over well. Shippers who choose expedited services have an urgent need for their freight to be in the right place at the right time, so if a provider misses a delivery window, the ramifications can be explosive.
Take the example of a tire retailer planning a weekend sale. Rather than incur the costs of stocking extra inventory and taking up valuable floor space to meet expected customer demand, the retailer will likely contract with an expedited provider to deliver tire shipments in time for the sale. If the provider fails to get the inventory there on Friday, the retailer will face the wrath of tire-less customers over the weekend.
When it comes to expedited transportation, it’s fast—or furious. So how do expedited providers ensure that they can offer quick, on-time deliveries and continue to meet shipper needs throughout the life of those shipments? Increasingly, the answer is technology.
Expedited providers have widely embraced technology. As a result, internal systems that help carriers plan and manage their expedited business; mobile solutions that enable surface and airfreight operators to communicate while shipments are in transit; route optimization and navigation software; and customer-facing solutions offering tracking and tracing capabilities, have become commonplace.
"Technology is a must-have for expedited shipments. Shippers will not use an expedited carrier that doesn’t at least utilize a Qualcomm system in their tractor-trailers," says Paul Simmons, vice president, Team Expedited for Green Bay, Wis., trucking company Schneider National, referring to the popular in-cab system that many providers use to communicate with drivers on the road.
The range of available technologies differs from provider to provider, but technology increasingly helps expedited carriers keep freight moving at full speed. For shippers, the key benefits these technologies bring include receiving more effective and proactive customer service; better on-time delivery rates; and the peace of mind that comes with improved cargo security.
So what exactly are today’s expedited providers offering when it comes to technology? Inbound Logistics checked in with five leading expedited carriers to see what technologies they are utilizing and offering to freight buyers—and what shippers can expect to gain from these high-tech investments.
Con-way Truckload: Technology as Safety Net
When you promise on-time expedited service that is "second to none"—as Con-way Truckload President Herb Schmidt describes his expedited offering, which makes up 15 to 20 percent of the company’s business—you need to make sure you can back up that claim. For Con-way, technology serves as that backup. "We utilize a variety of technologies as a safety net to make certain we are delivering the service we say we will," Schmidt explains.
The company’s technology safety net begins with Qualcomm units in every truck that allow two-way data interchange between Con-way drivers and the company’s centralized operations center—open 24/7/365—in Joplin, Mo. Data transmitted through the Qualcomm units flows into the operations center and, thanks to Con-way’s proprietary internal software, transmits the information to rolling ETA screens so dispatchers can monitor driver progress.
"We track every load in our system from origin to destination, and if a driver begins to run behind schedule, we see a warning on the screens in our ops center," Schmidt explains. "We contact the driver to see what is going on, and we can notify the customer if there will be any delays."
Con-way planners use another operations screen to ensure that any trailer decoupled from a tractor—over a holiday or a weekend, say—is re-dispatched within a predetermined time. The company also relies on internal technology solutions to determine if it has the proper lane density to accept an expedited shipment in the first place.
"You have to have a Plan B when you’re moving expedited goods. You can’t rely on delivering a shipment in a lane where you can’t recover the load if there is mechanical failure or driver illness," Schmidt says. "We need to make sure we have a lot of trucks in those lanes so if an exception does occur, the nearest truck is not 250 miles away."
Con-way also utilizes route optimization and navigation software. But while the carrier uses these tools to suggest routes and fuel stops, the drivers—who work in teams for expedited deliveries—decide the final route. Schmidt has not yet found a commercial navigation and routing system that doesn’t run into pitfalls, such as sending a driver under a bridge that is not tall enough to accommodate a truck.
The company has also switched drivers from manual to electronic logs as a way to monitor hours of service and improve driver safety. The logs also provide a benefit for shippers, because the data allows Con-way to know at all times the number of hours a driver has available. "It prevents us from accepting a load that could put a driver out of compliance and potentially delay the shipment," says Schmidt.
Next up on the provider’s tech list are two tools that will improve customer service capabilities: selective geofencing—its planners are automatically notified if a trailer strays outside a preferred route—and tracking devices embedded in trailers to provide extra safety for high-value loads. Schmidt expects to have both technologies in place in 2012.
Con-way also uses technology to make its expedited data available directly to shippers via a Web portal where they can watch their loads move across the country. The portal can be customized to specific shippers’ needs and most shippers access the site to get regular updates, Schmidt notes.
"But many of our customers don’t bother with it because they know we are monitoring every load and will contact them if there is a problem," he explains. "Shippers don’t want to spend a lot of time watching loads—they want the provider to do that, and to pick up and deliver on time as promised. If we can’t do it, they will find someone else who can."
FedEx Custom Critical: Unified Technology Yields Results
Making good on its old slogan "Relax, It’s FedEx," FedEx Custom Critical uses a wide range of technologies to retain tight control over its expedited shipping options. The company maintains a unified technology backbone that provides support across all its expedited offerings, which include surface, air, and white-glove services.
"Our internal system allows us to reach across all the FedEx companies to determine the best option to meet a shipper’s expedited needs," explains Jason Frederick, managing director of operations for FedEx Custom Critical, based in Green, Ohio. Through its Expedited Freight Services (EFS) tool, FedEx Custom Critical can quote shippers on several different expedited options to see which time and cost parameters make the most sense.
"EFS also allows us to see where we can book space on FedEx trucks or planes," he adds. "It keeps all the information under one umbrella, and lets us be sure we can deliver what we promise to shippers."
Using advanced planning technology also helps the company understand where its assets are, where its customers are shipping to and from, and how to marry that information. "It is very difficult to always have trucks located exactly where a shipper needs them, so we use our technology to be as efficient as we can, and try to plan as best we can to provide quality service to our customers," says Frederick.
In addition, FedEx’s unified technology helps it better serve shippers when issues do occur. If a load begins as a regular shipment via FedEx Freight but runs into bad weather, for instance, a customer service agent can intervene by transferring that shipment to the Custom Critical division, and expediting delivery. "We can navigate electronically through all our divisions to give shippers the most up-to-date information possible," Frederick notes.
The company also employs technology to provide what Frederick calls "custodial control" over its shipments. Using satellite- and cell-compatible Qualcomm units in each truck, FedEx Custom Critical monitors shipments continually and proactively contacts shippers and consignees if a delivery is running more than 15 minutes late.
Custom Critical also uses the Qualcomm units to send audio and video messages to its 100-percent owner-operated fleet, to track drivers’ hours-of-service status, and to provide origin and destination addresses and directions.
"We’ve seen great efficiency gains from the built-in navigation system," Frederick says, noting the company’s nearly 99-percent on-time rate. "And, we can ping drivers through Qualcomm to determine their location so we can communicate to shippers exactly where a truck is at all times."
To better serve verticals such as the pharmaceutical industry, where temperature-sensitive expedited shipments are the norm, FedEx Custom Critical uses AmeriScan units in all its temp-controlled trucks. The units monitor the temperature in the trucks and communicate the data to Custom Critical servers, ensuring that shipments remain in specified temperature ranges during transit. Shippers can track temperature data online, and, upon delivery, can receive a printout showing temperature information throughout the life of the shipment—critical information for FDA compliance, Frederick notes.
Ultimately, FedEx Custom Critical views technology as a competitive advantage and a way to boost shipper satisfaction. "We continue to look for new technologies that will update our business and improve the expedited service we can offer to shippers," Frederick says.
Old Dominion freight line: High-Tech Means High Visibility
If expedited carriers don’t have the technology offerings that shippers need to help manage their supply chains and customer expectations, then they simply cannot deliver a fully integrated expedited solution," says Chip Overbey, senior vice president of marketing, pricing, global, and strategic development for Old Dominion Freight Line.
Delivering that fully integrated expedited solution is key for the Thomasville, N.C.-based carrier, which offers a wide range of expedited specialties, including guaranteed, on-demand, white-glove, trade show, and airfreight services.
"Technology also allows us, as a provider, to manage internal systems effectively and stay ahead of the communication curve," Overbey adds.
One way Old Dominion does that is by giving shippers ample access to shipment information via its secure ODFL4ME portal. Shippers can log on to originate and track an expedited shipment, create documents and specialized reports, and send and manage shipment communications.
Old Dominion also provides expedited shipment data in numerous formats that are compatible with shippers’ legacy systems, transportation management system products, and other software solutions. "Many shippers like to have freight information fed electronically to their system so they can update their own internal reporting," explains Overbey.
The carrier also utilizes a slew of what it calls "operational technologies" that help support the communication, visibility, and planning of its expedited operations. The lineup includes handheld computers that drivers use to capture real-time information during pickups and deliveries; a Descartes routing system that helps reduce transit times; RFID tags that help the company monitor equipment location and freight movement; and a dock yard management system that transmits the status of any shipment moving through Old Dominion’s system at any given time.
"Our state-of-the art technology enables us to manage equipment and shipments more efficiently while consistently providing shippers with on-time, safe service and access to real-time information so they can deliver on the promises they have made," Overbey notes.
Schneider National: Technology PLUS Processes EQUALS Security and Satisfaction
Schneider National takes a slightly different approach when it comes to the importance of technology in expedited shipping. The carrier, which utilizes a two-driver team for every expedited delivery, views technology as a way to enhance service safety and reliability—but knows that technology alone is not enough.
"What allows us to best serve shippers is the way we use our technologies internally. Technology is great, but without good processes, procedures, and execution, it may not mean a whole lot," explains Paul Simmons, vice president, Team Expedited. "We couple our advanced technology capabilities with disciplined processes around how we manage the business."
Before an expedited freight shipment goes out, for instance, team leaders, drivers, and customer service representatives have a discussion to make sure everyone understands the details of the delivery.
In addition, data collected from the customer on each shipment is sent to drivers via the Qualcomm units in Schneider’s trucks, and is visible to dispatch and customer service groups at headquarters, as well as to driver managers, who are located in the field.
"Our driver managers are held accountable for understanding where their drivers are and what is happening with each load," Simmons notes. "And because we all use the same tool and see the same information, it is easy to communicate about shipments and be proactive if we need to notify shippers."
Schneider also takes that communication directly to customers, offering an online portal where shippers can access tracking and tracing information on expedited shipments.
Simmons views the team-driver approach as another smart process that works hand-in-hand with technology to ensure safety for high-value expedited loads. "Safety is a huge focus for shippers. Having two drivers in the truck means when they stop to refuel or use the restroom, the cargo is never left unattended," he explains.
On the technology side, Schneider uses Qualcomm units in the trucks and tracking devices on each truck and trailer so it knows where its drivers, assets, and cargo are at all times. "If a truck is stolen and disconnected from the trailer, we have an easy way of finding the trailer," Simmons says. "We have recovered pilfered loads due to our trailer-tracking technology.
"Having technology that allows us to communicate at any time with the driver in the truck and lets us track where every tractor is, gives shippers a level of comfort and awareness that their product is in safe hands and that we will pick up and deliver on time without loss or damage," he adds.
Schneider also utilizes the popular electronic on-board recorders to log driver hours and information, which again helps the company boost safety—for drivers and for shipments. In addition, Simmons says the company constantly evaluates new security technologies such as high-tech trailer locks and tracking devices to be sure it can offer shippers the most updated security tools.
UPS: Technology Across Modes
Who hasn’t shipped or received a package via UPS? The company’s integrated approach to technology means that the experience for individual consumers and multinational corporations shipping expedited freight across the globe is pretty much the same.
"We continue to invest substantially in technology to make the shipper experience seamless," says Scott Aubuchon, director of international airfreight marketing at UPS. "Whether they ship a letter or a 1,000-pound pallet—via ground or air—shippers can access the same options, service, and technology."
That integrated approach to technology appears throughout UPS’ numerous expedited options, which include express, time-definite, and critical services for surface freight; and express and critical airfreight options. Regardless of the expedited option a company selects, it can access the Atlanta-based delivery giant’s wide lineup of customer-facing shipping systems.
Options include WorldShip—a downloadable software application that allows users to book shipments, generate shipping labels, and send e-mail notifications; ConnectShip, a more advanced solution for multi-carrier expedited shipping; and CampusShip, a secure, Web-based shipping system that lets companies with multiple facilities ship documents, packages, and heavy freight from any location and offers shipment data that integrates with a company’s backend systems and processes. In addition, users can book and track single expedited shipments via UPS Internet Shipping.
These customer-facing technologies also help UPS gain internal efficiencies. "Our solutions automate the shipping process for shippers, and generate notifications internally to our systems so we know when a new order has been created, and when shipments are ready for pickup," says Aubuchon.
Once an expedited pickup order is initiated, UPS’ internal operational systems kick-start the various behind-the-scenes tasks that go into every shipment, such as identifying space requirements on a truck or a plane; dispatching a driver; and notifying the appropriate party at the arrival destination. Once an expedited shipment is in motion, additional technology keeps things moving smoothly.
The ubiquitous handheld devices that UPS drivers carry—officially known as Delivery Information Acquisition Devices (DIADs)—communicate a plethora of information back to UPS.
"As soon as a driver picks up the freight and punches the information into the DIAD, we know its exact size and weight," explains UPS Freight spokesperson Ira Rosenfeld. "So before the driver gets back to the terminal, we’ve already planned how we will load the truck, where we will place the shipments, and how we will move them as quickly as possible."
"Meanwhile, as a shipment moves from the shipper’s dock to our operation to the airport, those become milestones that are visible in our tracking and tracing systems," Aubuchon adds.
Expedited shippers can log on to the UPS Web site for tracking and tracing information, or can use Quantum View, UPS’ Web-based visibility platform that gives users visibility to both inbound and outbound shipments, as well as customs brokerage and scheduling information.
"Quantum View gives shippers a dashboard for small package, airfreight, ground, and ocean shipments; they gain visibility to exactly where their shipments are at all times through that portal," explains Aubuchon.
Companies sending expedited shipments via UPS can also use mobile technology solutions to track shipments, receive rate quotes, and find UPS shipping locations. The company offers downloadable mobile apps for BlackBerry, iPhone, and Android, as well as a mobile Web site with the capability to create and track shipments, and estimate rates and transit times.
"Ultimately," Aubuchon notes, "our goal is to use technology to enhance expedited shipping and make the process as seamless and efficient as possible for shippers, who depend on expedited transportation to remain competitive in their own business."