The Illuminating Power of Yard Management Systems
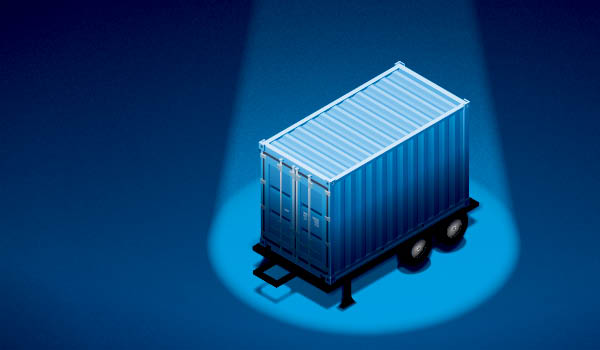
Trailer yards can be supply chain black holes between the visibility provided by transportation and warehouse management systems. Yard management systems shed light on trailer and shipment location.
Logistics technology solutions can reveal hidden bottlenecks and improve efficiencies. One such tool is a yard management system (YMS), which can help prioritize shipment arrivals, identify trailer contents, manage yard jockey activity, standardize yard processes, reduce the time needed to allocate vehicles to loads, and avoid unnecessary vehicle movements.
"Managing a trailer yard can pose significant challenges," says Nathan Harris, president of YardView, a Castle Rock, Colo.-based YMS provider. "Using a yard management system can help ensure workers don’t waste time hunting for trailers, or parking trailers in the wrong location. It shows the entire view of a yard, and helps companies manage operations more effectively. A YMS can play a large role in improving the overall flow of goods."
For shippers, YMS solutions deliver valuable information. "The difference between using a YMS and not using one is the difference between 2012 and 1512," says James Noseworthy, yard manager for Keene, N.H.-based C&S Wholesale Grocers, one of the largest U.S. grocery wholesalers. "Yard management systems take you out of the Dark Ages, providing visibility, downstream reporting, and complete control of assets—their location, condition, and contents."
This view into trailer yard operations has had a beneficial effect on some companies. "At the beginning of the supply chain, many companies control information through an enterprise resource planning (ERP) system," says Gregory Braun, vice president of business development at Montreal, Canada-based YMS vendor C3 Solutions. "On the other end of the production process, they use a warehouse management system (WMS). But before yard management systems existed, companies lost visibility from the time goods arrived in the yard to the time they were unloaded. Yard management systems give companies visibility to the whole process so they can better serve their customers."
Time is Money
When drivers arrive at warehousing facilities, their shipments often need to be unloaded within a specified time. If they aren’t, the carrier typically charges the distribution center a daily penalty.
"The faster trucks can be checked in, unloaded, and sent back on the road, the better it is for everyone," says Jon Donchey, chief operations officer at New York-based YMS provider Exotrac.
Yard management systems can improve shipment transfer in and out of the yard, promoting improved service levels, saving time and money, and enhancing the logistics process. In fact, a YMS can often boost a yard’s productivity by up to 30 percent.
"Many companies need to improve their yard operations’ efficiency and effectiveness," says Braun. "The most immediate need is to be able to better organize yard jockeys. A YMS tracks where trailers are, and where they need to go."
C&S Wholesale Grocers first experienced the benefits of a yard management system when it acquired a company in northern Pennsylvania that already had a YMS in place. The wholesaler then acquired another business that had purchased, but not yet implemented, a YMS. Realizing the benefits the first company was deriving, C&S decided to adopt the YMS for the new company, and to move forward with a multi-site configuration.
"Now the YMS is a tool we can’t live without," Noseworthy says. "Before we used it, if we needed to know how many refrigerated units were in a particular yard, we had to make phone calls and send yard jockeys to gather information. It could take a few hours to determine the answer. But by then, the answer may have changed.
"Integrating the YMS with the WMS gave us control and visibility we didn’t have before," he adds.
A YMS can also significantly reduce labor and administrative costs. Exotrac, for example, uses cloud-based software for its real-time logistics solution, which includes client-level customization, as well as bar-code and GPS technology. Using handheld mobile scanners and trailer identification, companies can customize the specific data they receive.
"It took one facility four hours every morning to conduct yard checks," says Donchey. "Using a YMS reduced that time to 90 minutes. Yard jockeys can spend a lot of time looking for a specific trailer, but with a YMS, they know exactly where it is. It’s easier to keep track of details."
Cost Considerations
For some companies, cost can be a deterrent to implementing a YMS. Today’s tight economy can make it difficult to justify the investment. But while a YMS used to require a significant cash outlay of up to $500,000, costs have come down, putting a YMS in reach for many companies. Additionally, many businesses can quickly achieve return on investment.
"As a function, yard management tends to get overlooked, compared to warehouse or transportation management," says Dr. Aleks Gollu, founder and chief technology officer of PINC Solutions, a Berkeley, Calif.-based company whose clients include SC Johnson, Kraft Foods, and Cost Plus World Market.
"Warehouse and transportation management are low-hanging fruit—direct budget line items people can track," Gollu continues. "Yard management, however, can be a black hole—the part of the supply chain network where inefficiencies persist."
A closer look at inefficiencies buried in the yard reveals significant impact on the entire supply chain. "When drivers arrive at a facility with a trailer, they often spend two to three hours checking in," Gollu notes. "But driver time is at a premium—the average driver is worth $50 per hour. Inefficient yard management that causes you to detain a driver longer than needed costs money."
Minimizing Losses
Without a YMS, trailers can become lost in the yard. If a trailer contains time-sensitive product such as produce, the result can be a complete loss. "A good YMS maintains product visibility and improves yard jockeying system efficiency," says Noseworthy. "Not knowing where a product is—even for a few hours—occurs much less frequently."
Prioritizing trailers is easier with this visibility. "A YMS helps you see the total picture. What trailer has been sitting for three weeks? Which one is loaded with food and needs to be handled right away?" explains Harris. "It gives you thorough visibility of what is going on in the yard. You can see if units are damaged, and address problems faster. The YMS greatly improves communication between departments and processors in the yards."
Yard management systems take users out of the Dark Ages, providing visibility, downstream reporting, and complete asset control. — James Noseworthy, yard manager, C&S Wholesale Grocers
Shippers that use YMS solutions stand to gain significant advantages. "We implemented a yard management system because we had issues tracking trailers," says Scott Fisher of fresh meat product supplier Farmland Foods, which uses YardView. "It was inefficient to track 200 to 400 trailers manually."
Farmland Foods implemented YardView on two campuses, each with multiple facilities. "Knowing where shipments are, and being able to get them out the door faster, has made us about 30 percent more efficient," Fisher says.
The Big Picture
Yard management systems not only provide visibility into the yard, but also help companies see the big picture. Rather than working in silos, workers view the entire supply chain process, which can help them identify potential delays to improve overall efficiency.
"Forward visibility is one of the greatest benefits of a YMS," says Noseworthy. "Everyone in the process sees the big picture, instead of just knowing their own part and having to communicate the old-fashioned way to find out what other areas are doing."
Connecting the dots effortlessly benefits the entire organization. "The YMS provides visibility that gets everyone on the same page, no matter where they are in the supply chain," says Harris. "Workers may not understand that if they make a mistake, it can affect the jobs of three other people downstream.
"Tracking processes manually can cause communication breakdowns that create big problems," adds Harris. "But a YMS automatically generates information and directs workers correctly. There is no mix-up in communications as in the past. The system creates accountability."
"The benefits of YMS come down to visibility, communication, and accountability," agrees Donchey. "It also helps to have some metrics. What can we learn about our operations using the YMS solution’s reporting capability?"
Thanks to the light YMS solutions shed on yard operations, companies can more clearly see opportunities for improvement through the whole supply chain.