5 Types of Risk in Supply Chain Management
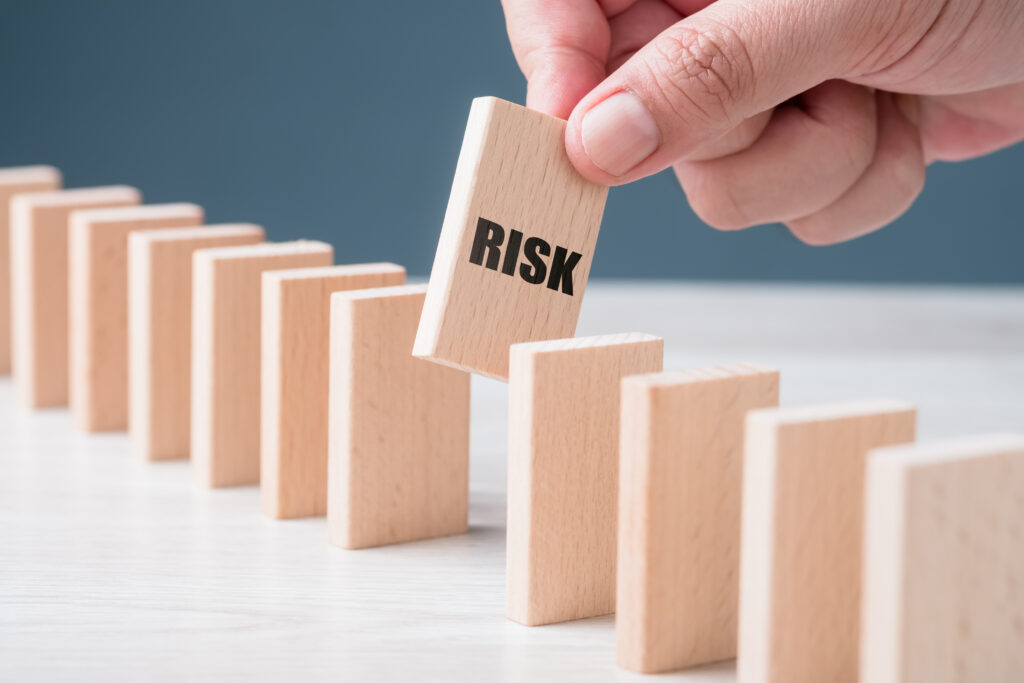
This guide breaks down five types of risk in supply chain management, showing how environmental risks, financial threats, and market shifts can hit operations hard.
Supply chain risk means any unexpected event that can disrupt operations or delay the flow of goods and services. These risks can hit at any point across the supply chain network, whether it’s a flood wiping out raw materials or a supplier risk event causing a production stop.
Today’s businesses must deal with internal and external risks, prioritizing supply chain risk management. This guide covers the types of risk in supply chain management and explains how to spot and handle top supply chain risks before they snowball.
The goal is simple: help companies build a resilient supply chain by managing supply chain risk effectively across the entire supply chain.
Why Risk Management Matters in Supply Chain Operations
Unexpected supply chain disruptions raise costs, delay shipments, and reduce efficiency. Production delays or missed deliveries cause a ripple effect across supply chain operations, making it harder to meet deadlines or manage inventory properly.
These issues hurt business operations and put pressure on the bottom line. Disruptions impact a company’s financial performance by increasing overhead and reducing output. Customers grow frustrated when deliveries run late or product quality drops.
Missed timelines damage trust and brand reputation. Without a focus on supply chain risk management, companies risk losing both profits and long-term business continuity.
How Supply Chain Risk Impacts Businesses
Storms destroy factories. Strikes halt shipping lanes. A sudden geopolitical risk can trigger trade wars or restrict access to key materials. Any one of these events disrupts the flow of goods and hits companies hard. Natural disasters slow down manufacturing or destroy infrastructure.
Supplier failures cause production stops. Political instability triggers new tariffs or regulations. These problems lead to lost revenue, longer lead times, and rising costs. Supply chain risks also limit flexibility, especially in global supply chains with fewer alternatives.
The Role of Supply Chain Risk Management
Effective chain risk management means identifying threats early and acting fast. Teams review weak spots, build backup plans, and create smarter systems that keep things moving even during a crisis. Strong supply chain risk management builds a more resilient supply chain.
Companies use risk identification tools and share data across departments. They look beyond day-to-day tasks and prepare for worst-case events. In return, they respond faster, incur lower expenses, and protect brand trust. That’s how managing supply chain risk gives a competitive edge.
Common Types of Risk in Supply Chain Management
Main supply chain risks fall into broad categories that impact how products move, get made, and reach the customer. Understanding each risk type helps supply chain teams plan better and reduce downtime. Here are the five key areas:
Environmental Risks
Storms, floods, and wildfires can damage factories and delay shipments. Extreme weather events threaten transport routes and block access to raw materials. On top of that, changing environmental regulations can slow production or raise costs.
These environmental risks often strike without warning, especially in regions with unstable climates. Businesses relying on single-source vendors or tight delivery windows face the biggest challenges. To mitigate supply chain risks, companies must build flexibility, use backup routes, and work with alternative suppliers across their supply chain network.
Operational Risks
Breakdowns in equipment, poor supplier relationships, and internal mismanagement create operational risks that slow things down. A late shipment or a bad production batch can delay an entire order. Errors in supply chain planning, lack of training, or system outages also stop progress.
These risks grow when supply chain visibility is low or teams fail to share updates. Quick response plans and routine checks improve outcomes. Strong collaboration with supply chain partners helps prevent repeated issues and builds reliability in modern supply chains.
Financial Risks
Currency swings, payment failures, and weak supplier finances fall under financial risks. Global inflation or price hikes in materials increase the cost of doing business. A supplier that can’t cover costs may fold without notice, affecting the company’s supply chain.
Businesses exposed to one market or vendor carry extra risk. Smart companies manage this by using financial instruments, tracking supplier health, and keeping reserves. Regular supplier assessments and working with multiple suppliers help keep operations stable during unexpected downturns.
Geopolitical and Regulatory Risks
Political instability, sanctions, or shifting trade laws create delays and increase costs. A policy change can shut down exports or block critical parts at customs. Geopolitical risk also includes strikes, regional conflict, or diplomatic tensions that slow movement across borders.
These risks hit global supply chains the hardest, especially when businesses rely on one region. Flexible sourcing, clear compliance protocols, and strong local partnerships lower the impact. Proactive companies build contingency plans that support supply chain continuity when policies shift overnight.
Demand and Supply Imbalances
A sudden sales surge or supply shortage throws plans off balance. Without real-time data, companies either stock out or over-order, tying up cash in excess inventory. Forecasting errors and a lack of predictive analytics worsen these mismatches.
Gaps in supply chain visibility make response times slower. Better demand tracking, agile production systems, and stronger coordination across departments prevent disruptions. Teams that monitor trends closely and talk regularly spot issues early and adjust fast.
Internal vs. External Supply Chain Risks
Every supply chain faces challenges from both inside the company and from outside forces. Knowing the difference between internal supply chain risks and external supply chain risks helps teams respond faster and improve overall supply chain resilience.
Both risk types play a major role in shaping supply chain performance and long-term success.
Internal Risks
Problems that start within the organization often disrupt core processes. These issues usually relate to systems, people, or decisions made during supply chain operations.
- Production delays: Missed deadlines or slow output cause bottlenecks across the supply line.
- Inaccurate data: Bad forecasting or outdated systems lead to poor decisions and wasted resources.
- Poor communication: Gaps between departments or unclear updates cause avoidable mistakes.
- System failures: Breakdowns in software or hardware interrupt workflows and stop shipments.
Strong planning and open collaboration reduce supply chain vulnerabilities from internal sources.
External Risks
Outside threats can hit without warning. These external risks often come from market conditions, suppliers, or global events.
- Supplier defaults: Vendors go out of business or fail to meet delivery promises.
- Customs delays: Border holdups slow international shipments and disrupt schedules.
- Pandemics: Health crises reduce workforce availability and break global networks.
- Fuel cost changes: Rising energy prices raise transport costs across the supply chain.
Tracking both risk types helps companies create solid mitigation strategies and maintain business continuity in uncertain markets.
Risk Identification and Assessment
Spotting trouble early keeps operations running and limits damage. A smart supply chain risk assessment improves decision-making and supports faster response times. Early detection also strengthens supply chain risk management and helps teams build a stronger risk management plan.
Mapping the Supply Chain
Visualizing every link in the chain improves awareness of where risks hide. Supply chain mapping reveals how each step connects, helping teams find weak spots, plan better, and reduce delays across the network.
Understanding upstream and downstream paths highlights weak spots and gives supply chain leaders the insight needed for better control. A full map also guides efforts to mitigate supply chain risks and align backup strategies.
Predictive Analytics and Monitoring
Using predictive analytics helps teams spot patterns and flag trouble before it starts. Real-time data tracking highlights delays, performance issues, and trends, allowing faster responses and smarter decisions across the entire supply chain.
Continuous monitoring allows teams to shift resources, avoid disruptions, and reduce exposure to potential risks. These tools also help companies avoid repeat issues and gain cost savings over time.
Working with Supply Chain Teams and Managers
Close coordination with supply chain managers gives visibility into ground-level problems. These teams identify delays, vendor issues, or system gaps early, helping prevent disruptions and improve decision-making throughout the supply chain.
Collaboration also encourages better feedback loops, stronger supplier relationships, and smarter decisions. Input from frontline staff often leads to faster fixes and more effective risk management.
Mitigation Strategies for Supply Chain Risks
No company can fully avoid supply chain risks, but smart mitigation strategies reduce the damage when disruptions strike. Risk mitigation focuses on staying prepared, acting fast, and cutting the impact of delays, shortages, or breakdowns.
Top companies don’t chase perfection. They build flexible systems that adapt under pressure. A good plan supports supply chain resilience and improves long-term performance.
Build Resilience Through Diversification
Relying on one supplier or source increases business risk. A single failure can halt operations. Working with multiple suppliers from different regions lowers exposure to supplier risks and strengthens supply chain stability.
Sourcing from regional suppliers creates options during border closures or local problems. Diversification also shields the company from pricing swings or sudden supply chain disruptions.
Maintain Safety Stock and Contingency Plans
Holding extra safety stock protects against demand spikes and shipping delays. Contingency plans help companies reroute shipments or switch vendors quickly, keeping operations running smoothly during unexpected supply chain disruptions.
These buffers help maintain flow even when natural disasters or labor shortages hit. Good planning avoids stockouts, keeps customers happy, and reduces downtime across the supply chain.
Strengthen Supplier Relationships
Strong partnerships improve supplier performance and boost coordination. Open communication, regular updates, and shared planning tools keep vendors aligned with business needs and help reduce delays or missteps in the supply chain.
Good relationships also speed up recovery during emergencies. When problems come up, trusted suppliers respond quicker and support smoother resolutions, helping maintain a competitive advantage.
Improve Visibility and Communication
Clear, real-time updates help spot issues early and fix them fast. Better supply chain visibility lets teams track each stage, from raw materials to delivery, reducing delays and improving response times across operations.
Connected systems and strong communication also reduce surprises. Transparent workflows limit confusion and keep supply chain managers informed, especially during peak pressure.
Creating a Risk-Ready Supply Chain Strategy
Solid risk management starts with structure. A working strategy connects systems, people, and processes. Teams need clear rules, the right tools, and ongoing training to handle disruptions. Every part of the chain must know its role when risks show up.
Core practices include:
- Set clear risk management practices.
- Define roles and protocols across departments.
- Use tools to monitor supply chain vulnerabilities.
- Invest in training and decision-making frameworks.
These steps support faster action and build a smarter, more resilient supply chain that can handle real-world stress.
Conclusion
Every business faces challenges that can disrupt even the most well-structured supply chain. This guide broke down the types of risk in supply chain management, showing how environmental risks, financial threats, and market shifts can hit operations hard.
Different types of supply chains face unique challenges, which makes tailored planning essential. Companies that invest in supply chain risk management gain control over uncertainty and reduce costly surprises.
Strong risk management practices, clear planning, and smart tools help teams prepare for supply chain disruptions—from natural disasters to cybersecurity risks. A proactive risk management plan built around early action and team alignment allows businesses to mitigate risk and handle such risks with confidence.