10 Tips for Managing Inventory Effectively
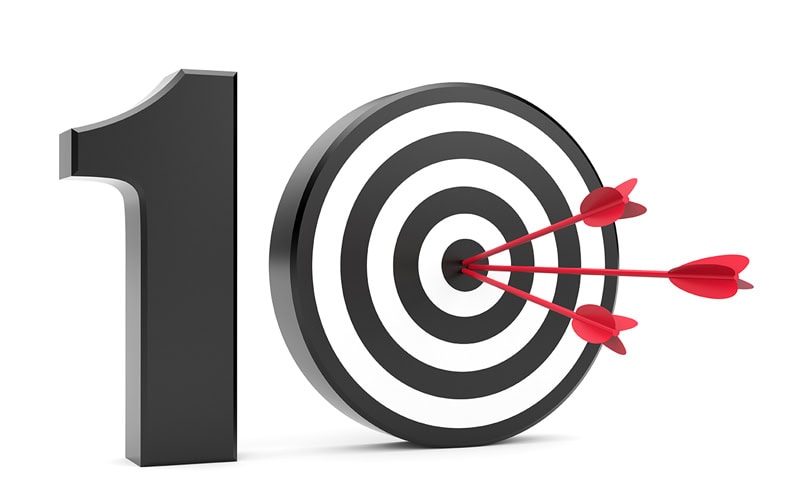
Effective inventory management starts with a proactive philosophy. Here are 10 steps to take that can help you improve accuracy, increase efficiency, and control costs.
1. Implement robust receiving procedures. Effective inventory management starts with accuracy and efficiency on the inbound side. When shipments from vendors arrive, verify that you received what you ordered, in full and undamaged. It’s critical to identify any issues quickly. Once you receive an order, you’ll have limited time to make a claim.
2. Guard against errors. Establish a proactive maintenance program to identify any errors that may occur within the four walls of the warehouse. Structure the program so that cycle-counting (proactive inventory audit) is based on the most important criteria.
3. Establish inventory hierarchy. Typically, inventory hierarchy involves ranking SKUs or SKU categories based on their value, velocity, seasonality, or other priority. Organize your inventory into high (A), medium (B), and low movers (C). Then align processes accordingly to ensure that you count on the appropriate frequency.
Ideally, the frequency should be commensurate with how often SKUs are touched since each touchpoint is an opportunity for error. You might count A’s monthly, B’s quarterly, and C’s annually to ensure your program creates the most value.
4. Minimize product hold time. The longer products sit in the warehouse, the greater the cost of goods sold (COGS). To preserve the margin potential of inventory in the warehouse, maximize storage density and increase inventory turns. The greater your turns, the lower your COGS.
5. Consider rotational strategies. First In, First Out, for example, can minimize overall inventory costs over time. First Expire, First Out can minimize the risk of obsolescence. Deploy the appropriate rotation strategy for each part of your business.
6. Leverage information systems. A robust ERP or WMS can streamline and automate inventory management, taking human decision-making out of the equation, which also helps reduce labor costs. If your inventory supports orders for multiple sales channels, it’s especially important to use robust, intuitive systems that can handle that level of complexity.
7. Utilize technology to optimize processes. Systems can also improve specific processes. With cycle-counting, for example, a WMS can validate a physical inventory count. Using a double-blind process and supervisory re-count for two-way validation significantly improves accuracy. Advanced automation and robotics can help to ensure accurate order processing, which is directly tied to inventory management. Autonomous mobile robots and lighted pick/put solutions help get orders out the door accurately while ensuring that accurate inventory is maintained in the warehouse.
8. Capture post-mortem data. Establish a process for follow-up once an order ships. You want to learn about any issues, resolve them quickly, and ensure a good client experience. Any discrepancies or adverse findings create data points that you can act on. That data capture is critical, as it helps identify the root cause of the issue.
9. Address shrinkage issues. By keeping a close eye on the data, you can identify inventory inaccuracies and trends. This iterative process can help you to reduce shrinkage and manage risk over time. Inventory accuracy tracking can’t be out of sight and out of mind. Daily metrics tracking helps to identify and address problems quickly.
10. Establish a continuous improvement program. A continuous improvement program is essential for effective inventory management. By improving productivity, accuracy, and consistency, Lean methodologies can help to drive cost savings and operational excellence.
SOURCE: Zachary Purdom, Regional Senior Director of Operations, Saddle Creek Logistics Services