3 Top Emerging Automated Solutions
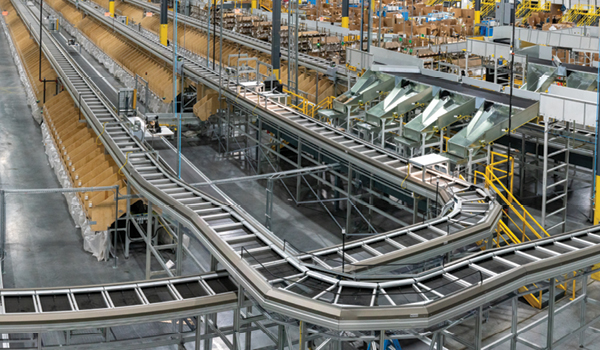
Within the four walls of distribution centers (DCs), more automated alternatives are replacing traditional labor-intensive process and material handling strategies. Operations leaders are beginning to automate and upgrade specific aspects of their DC operations that are bowing under the weight of e-commerce pressures.
Companies are increasingly integrating three leading forms of automated solutions in their warehouses. These emerging solutions present attractive and attainable returns on investment.
1. Automated storage and retrieval systems (AS/RS). A flexible and highly scalable solution, automated storage and retrieval systems can pick cases and containers from storage and transfer them to correlating automation systems or to picking stations for fulfilling orders.
A more configurable option compared to traditional systems, robotic solutions can integrate a range of products while saving warehouse space and increasing product storage density. The system can be implemented quickly, even with existing workflows, and integrates with traditional and mobile automation solutions.
Automated storage and retrieval systems also benefit the human workforce. The capabilities of AS/RS reduce the amount of manual labor for employees, thus reducing the risk of injury. With less time spent on labor-intensive tasks, resources can be better allocated to focus on strategic aspects within the warehouse.
2. Autonomous mobile robots (AMRs). AMRs enable operators to transport products and deploy workers efficiently, helping to reduce walk and vehicle drive times. Autonomous mobile robots have demonstrated their value in a variety of ways in the warehouse, including:
Pallet conveyance via autonomous forklift: Pallets can be loaded/unloaded autonomously and moved between the floor and/or pick-up and delivery (P&D) stand transfer locations.
Picking and cart transport: AMRs offer productivity and efficiency benefits by automating the movement of carts used to transport picked orders and returns.
Automated machine tending: AMRs with an in-line conveyor or custom attachments can be used to transport parts and products between manufacturing equipment. They can also transport goods/pallets to and from palletizers/depalletizers, replenish an AS/RS, and supply a flexible link between various conveyor systems.
AMRs can be combined with order-picking technologies such as hand scanners or voice systems to increase safety, productivity, and efficiency.
3. Warehouse execution systems (WES). Conventional fulfillment strategies are no longer viable, as consumer demands continue to rise. However, integrating multiple automated systems into a warehouse’s day-to-day operations can further complicate things. A decision made in one automated system can create a domino effect of inadvertent consequences in other systems, leading to inefficiency and a lack of productivity.
Enter warehouse execution systems, which employ and utilize data science techniques that allow data to be available from virtually every spot in the warehouse. This provides visibility and insights into the interplay taking place between automation systems.
Visibility into the solutions enables the software platform to use dynamic real-time decision intelligence that coordinates contrasting automation systems, so companies can execute and achieve the desired strategies and results.
These three automated solutions help support efficient operations by owning the tasks that are tedious and exhausting for human workers, increasing efficiency and productivity.