Balancing Shipping Costs with Inventory Carrying Costs
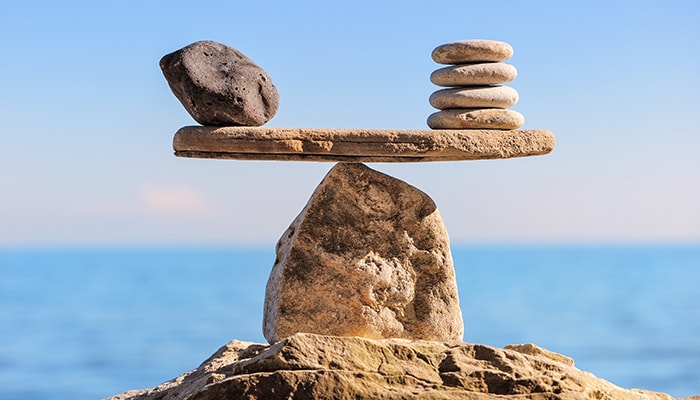
Shippers must learn how to navigate the new balancing act between just-in-time and just-in-case demands, especially as the shipping market increases in complexity. Just-in-time logistics will stay with us in the coming years, but it will be augmented by a slight increase in just-in-case inventory, depending on the industry.
However, creating better resilience is far more complex than simply holding more inventory. In this new world of an adjusted version of just-in-time shipping, there is no such thing as a one-size-fits-all solution.
Manufacturers face rising pressures in the form of tightening profit margins and more precise shipping windows. Shipping costs have increased, but so have inventory carrying costs. Manufacturers need to balance this. Efficiency and reliability are key to their long-term success.
It is critical that manufacturers and retailers work with companies with the capacity, flexibility, and understanding to fine-tune shipping needs to fit changing circumstances. When models change, flexibility becomes the most important attribute.
To manage trucking disruptions, shippers should make sure their carrier’s fleet, tools, staff, and procedures are calibrated to meet the needs of this new era. Are they building additional capacity before it is needed? Do they stay ahead of demand?
Shippers will be best served by carriers that carry excess capacity, maintain open lines of communication, and maximize flexibility at every stage of their logistics operations.
Deployed together, these solutions can bulletproof supply chains against future challenges as well as the approaching complexity crunch.
— Steve Hartsell, VP of Sales and Incoming Senior VP of Sales, Old Dominion Freight Line