How to Counter a Hazy Warehouse Employment Outlook
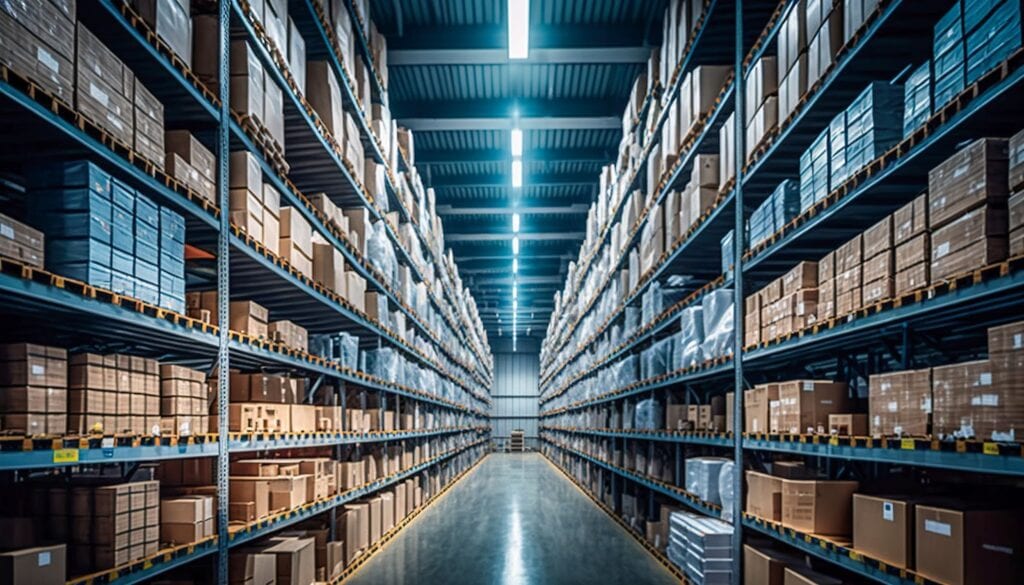
You don’t have to give warehouse managers the latest jobs report—they can tell you the state of the economy by looking out over the aisles. Customer demand continues to climb, the supply of potential workers remains stagnant, and the war to attract talent is fierce.
The first solution many supply chain leaders look at is money. That’s a fantastic start, but salary alone likely isn’t enough to keep employees for the long term. Warehouse managers must also consider the intangible benefits of the role. A few areas to start:
Get off on the right foot.
No supply chain leader considers their team “cogs in a machine.” But it’s understandable how, if not onboarded properly, employees could get that impression—sent immediately into a massive facility to complete repetitive tasks over long hours. Warehouses must dispel that notion from the minute new team members walk in the door.
Kenco launched the “First Year Experience” to immediately connect employees to their purpose within the warehouse. This comprehensive onboarding process fosters a sense of purpose among new employees, helping them understand how their job is critical to keeping our warehouses operating. By engaging employees early, warehouse managers can prevent employee feelings of being alone on an island.
Recognize the whole person.
Sometimes it seem as if the boundaries between our work life and personal life blur. Warehouses must not only recognize these boundaries, but also support their employees outside the facility.
Shift flexibility can be a good place to start a benefits initiative. Just because established shifts work well for your warehouse doesn’t mean your employees’ calendars fit neatly into those 8-hour windows. Leaving some wiggle room in the calendar can open up recruitment to a whole range of potential employees.
Potential employees also want an employer who will further their professional development. Tuition assistance or reimbursement have become popular options in the past decade, with many companies now offering students support. A tuition program is ultimately a win-win—the employee feels valued, while the knowledge they gain can help drive process improvement, and even prepare the employee for a management role.
Lend a helping hand.
For those who aren’t deeply familiar with warehouse operations, stories of repetitive stress injuries and harsh work environments can be a turnoff. But automation has made picking and packing tasks safer and far less strenuous.
Take telematics and location-tracking tools. Telematics devices allow fleet managers to monitor how material handling equipment is operated throughout the warehouse—ensuring unlicensed employees can’t drive vehicles, or malfunctioning vehicles are detected and kept off the warehouse floor. Real-time location services can set virtual “perimeters” to ensure no heavy equipment ends up in employees’ paths.
Bottom line: an investment in automation is an investment in labor recruitment and retention efforts.
Become the warehouse employees flock to.
By introducing benefits that support employees’ lives outside the warehouse, and technology that simplifies their job inside the warehouse, you’ll find that your employees are far more satisfied and, in turn, your hiring efforts are far more sustainable.