How You Can Respond to Lingering Port Congestion Problems
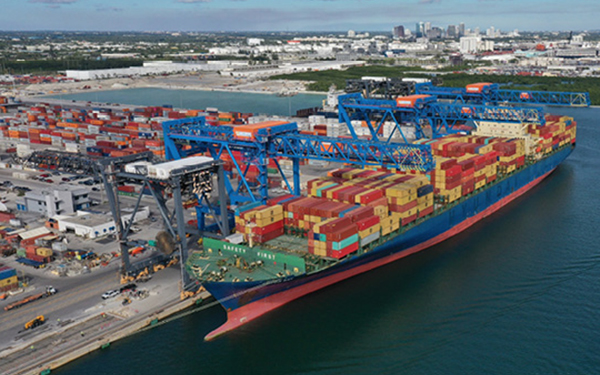
We’re not experiencing a traditional peak retail shipping season this year. If you’re a shipper and hoped the decreased volumes would transfer to the ports, hopes are fading that you’ll see relief there.
For months, retailers flush with inventory have been delaying and at times even canceling orders. And while consumer spending isn’t down, it has slowed, with people focusing their purchases more on essentials as they’ve faced inflation, volatile gas prices, and fears of a recession.
Still, despite these trends, U.S. ports remain congested and continue to snarl and slow supply chains. The question isn’t only what’s causing the congestion to linger, but also what can you do in response to it?
Contributing factors
One reason port congestion persists is because some retailers are reverting back to old practices.
During the pandemic, supply chain disruptions led to issues like empty store shelves for retailers and parts shortages for manufacturers. Goods needed to be moved with urgency, and one step that shippers took to do this was to switch from ocean to air shipments.
But now, many air shipments are returning to the ocean as shippers try to reduce costs. Some importers may even be happy to have goods spending some extra time in transit on the ocean given the challenges they face with excess inventory in warehouses.
Shifting freight strategies are also driving port congestion.
Continued congestion at the Los Angeles and Long Beach ports – combined with issues like ongoing contract negotiations with West Coast port workers – has led to freight being shifted to East Coast ports. Now, bottlenecks are occurring at these ports, too.
Consider that at one point this summer, more than 40 ships were waiting to berth at Savannah – a new record for the port. Wait times have also increased at this port from one day in May to more than 13 days in August.
A third contributing factor to the continued congestion is the shortage of chassis and rail cars. This summer, Los Angeles and Long Beach were experiencing dwell times of 16 days for rail cargo, while at Oakland it was up to 30 days.
Three steps you can take
Every supply chain is unique and as a result requires its own distinct strategy. But there are a few things you can do to manage through ongoing challenges at the ports.
First, look for ways to diversify your mode and port strategy. For example, maybe your warehouse is full but you still need to move goods. In this situation, using less-than-container-load (LCL) ocean shipping may be the best move for you. It can give you peace of mind that inventory is still coming in, but at the quantity that’s right for you.
LCL shipping also offers other benefits. It can provide cost savings, and space is typically more readily available for LCL shipments because you’re only looking for some available container space rather than an entire empty container. LCL shipping can also give you flexibility. One automotive parts importer, for instance, used LCL shipping to see how certain products performed before overcommitting to them.
Second, consider your inland strategies. An option like LCL shipping ultimately won’t bypass congestion at the ports. Inland point intermodal (IPI) and reverse inland point intermodal (RIPI) options can further diversify your shipping strategy and reduce delays at the port.
Some carriers are sending more 53-foot containers so cargo on 40-foot ocean containers can be efficiently consolidated and loaded onto trucks or trains for faster delivery to inland destinations. This has helped the carriers increase their container capacity by 25% in places like southern California while increasing the flow of cargo inland.
Third, use deconsolidation services at ports. These services break down containers or large shipments into smaller shipments that are organized based on factors like products, orders, or destinations. This can help make sure priority freight gets moved first.
Answers in your data
COVID has been dubbed a once-in-a-century event, and it has resulted in unique circumstances that shippers likely won’t experience as the norm going forward. Still, mining historical data for common themes or trends can equip you with insights for dealing with today’s challenges.
What’s more, supply chain tools are only getting better in their ability to help you see and predict what’s happening with global shipments.
For instance, amid the ongoing port congestion, some vendors have enhanced their transportation management system tools with enhanced vessel routing and tracking features. This can improve the efficiency and accuracy of port ETAs and allow you to receive automatic updates if changes are detected.
No relief in sight
There’s no easy answer for a problem like port congestion, but there’s also no reason for waiting to act on it. Diversifying your shipping strategy and leveraging data-driven insights can help you reduce delays and identify savings not only in this busy shipping season but also as you enter what could be another unpredictable year.