Logistics Plus Warehousing Team Solves Client’s Off-Site Warehouse Inventory & System Issues
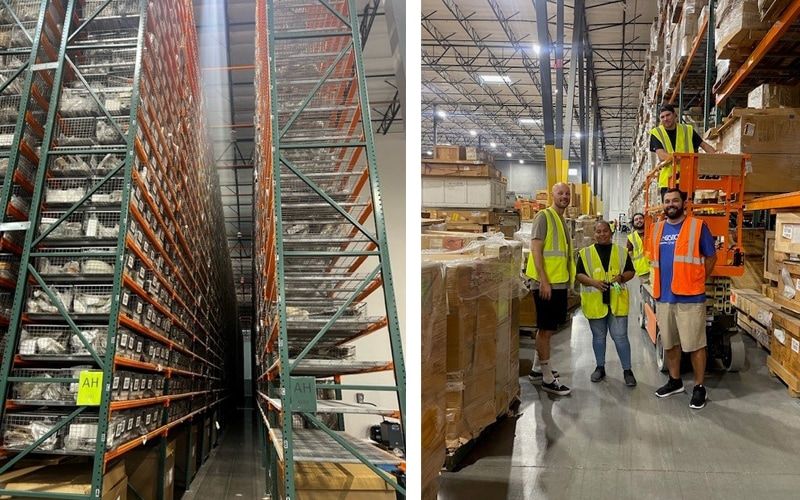
Logistics Plus finds a way to “yes” by springing into action and sending employees to help solve inventory and system issues at a client warehouse.
THE CHALLENGE
Logistics Plus (LP) is a leading worldwide provider of transportation, warehousing, fulfillment, global logistics, business intelligence, technology, and supply chain solutions.
A United States-based aircraft parts supplier approached Logistics Plus with a warehousing challenge. The client moved into a new 550,000-square-foot warehouse earlier in the year to handle the storage and fulfillment of their products.
The client started running into inventory issues and incorrect reporting in their warehouse management system (WMS) only a few months after beginning operations. So, they called Logistics Plus for help.
THE SOLUTION
Within three days of being asked to help solve the issues, LP sent 10 of its own warehouse employees from its West Coast warehouses (Phoenix, AZ and Chino, CA) to work on-site at the client’s warehouse until the issues were identified and solved.
The LP team started by breaking the project down into three phases. Phase 1 was identifying the root problem. LP determined the warehouse’s rotating temporary workers were not appropriately trained in using the WMS, and the inventory wasn’t properly flagged nor scanned into the system when it arrived or left the warehouse. Phase 2 of the project involved going through the warehouse and re-scanning every piece of inventory. As pallets were scanned, the team flagged all items that were not in the proper location.
After the inventory was accounted for, and issues were flagged, Phase 3 began. This involved moving all of the flagged inventory to the proper location and entirely re-staging the product. Additionally, the inventory that was incorrectly tagged was sorted by location codes. Tags were also added to different locations of the pallets so that each item could be easily identified and located. After this was completed, the team updated the client’s WMS to reflect actual inventory levels.
THE RESULTS
With LP’s rapid response time and warehousing expertise, the client now has complete and accurate visibility of its inventory levels. The warehouse is staged in sections to allow the warehouse workers to quickly scan, identify, and pull products from the proper locations.
The LP team will remain on-site for the foreseeable future until the client is comfortable with the system and process that was put into place. Logistics Plus continues to grow its relationship with the client and remains ready to assist with any new supply chain challenges.
As a 21st-century logistics company, Logistics Plus was able to leverage its can-do culture to help fix the client’s inventory issues within a matter of days.
To learn more:
[email protected]
1-866-LOG-PLUS (564-7587)
www.logisticsplus.com