Pharma Supply Chains Get Technology Booster
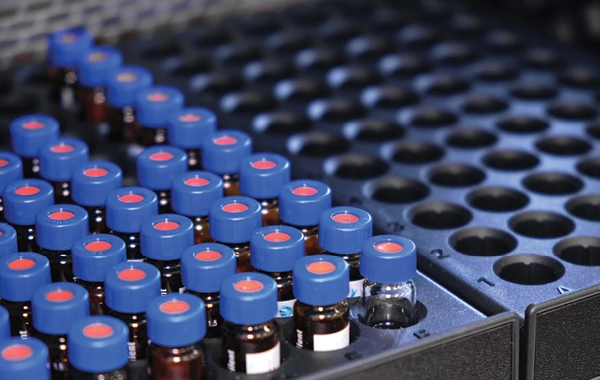
Pharmaceutical and life sciences supply chains receive a healthy dose of innovation and automation solutions—boosting visibility, traceability, and productivity.
Until recently, companies planning for resilience and business continuity tended to focus on relatively localized events, like a hurricane hitting the Gulf Coast of North America and disrupting traffic and power, or an Icelandic volcano erupting, forcing air traffic to reroute. Although the human and financial toll might extend for months, the events themselves typically conclude within hours or days.
No more. “The pandemic changed our thinking about how to manage resilience,” says Steve Simco, head of logistics and distribution, North America, with Camelot Management Consultants. “It’s the Great Depression of risk issues, and it’s not going to leave peoples’ minds for a while.”
The pandemic’s continued impact has been particularly pronounced in the pharmaceutical and life sciences logistics sector, where products are critical to life and health. Many products also are perishable, highly regulated, and require temperature-controlled and sanitized environments. “Life sciences supply chains require a unique level of accountability, visibility, and traceability,” says Andrew Wang, director of healthcare and industrial with Locus Robotics.
In addition, skyrocketing freight costs have compelled pharmaceutical companies to better understand this expense, Simco says. That’s a shift, given that freight costs historically have been a relatively small percentage of the price of pharmaceutical goods.
Together, these forces are helping to drive the U.S. pharmaceutical logistics market, which topped $23 billion in 2021, and is forecast to reach a compound annual growth rate of 7.4% through 2030, according to Grandview Research. The increasing global production of COVID-19 vaccines and demand for over-the-counter medicines and supplements also are propelling the industry.
The expanding prevalence of biopharmaceutical products, which are made from living cells or organisms, is also shaping the pharmaceutical logistics market. Many of these products require temperature controls. The global biopharmaceutical market, valued at $28.7 billion in 2021, now accounts for 20% of the pharmaceutical industry, according to Straits Research.
Supply Chain Disruptions Inject Innovation
The factors that contributed to the recent disruptions are influencing which solutions companies are turning to in their attempts to improve their supply chains. One cause of the supply chain challenges has been an “inability to forecast extreme demand fluctuations,” says Tim Vadney, a director with West Monroe, a digital services firm. The lack of accurate demand signals also prompts some companies to simply “buy heavy,” he says. These larger purchases boost congestion at ports and distribution centers.
Although the pharmaceutical industry was an early adopter of enterprise resource planning (ERP) systems, these solutions generally don’t include suppliers in the flow of transactions, which would help ensure all partners across a supply chain have a reasonably accurate handle on supply and demand.
To remedy this, some software providers are extending ERP functionality to companies’ supply chain partners over the web.
“You have planning that feeds to purchasing, that feeds to demand, and then to an API (active pharmaceutical ingredient) supplier,” Vadney says.
This flow of information offers buyers better visibility and more data they can use to decide whether to accept or reject, for instance, changes in materials or work order completion dates. Similarly, pharmaceutical companies are investing more in planning technology, such as software that incorporates algorithms to more accurately forecast supply and demand.
Greater Focus on Agility, Visibility, Resilience, Safety
The recent upheavals have also heightened focus on improving an organization’s supply chain agility and responsiveness. “Those conversations have moved front and center,” says Pankit Bhalodia, managing director, healthcare and life sciences, with West Monroe.
More pharmaceutical supply chains have begun transitioning away from a reliance on spreadsheets. As they do, they’re investing in the infrastructure and training needed to more effectively manage risks and compliance.
“This is a huge uplift from where things have been,” Bhalodia says.
Another area of focus is visibility. “It’s not enough to know your supplier has safety stock,” says Vishal Bhandari, partner in the health practice of global consulting firm Kearney. “Companies also need to know how the products will get to their operations.”
Pharmaceutical companies are investing in more robust inventory management strategies and real-time tracking, as well as stronger risk management for their upstream supply base, including beyond their immediate suppliers.
Efficiency and safety also are driving investments. “We’re starting to see larger investments by healthcare companies focused on improving supply chain and logistics efficiency and safety, and reducing human error,” Wang says.
While many healthcare and pharmaceutical companies had been investing in automation on the pharma side—for instance, in pill dispensing solutions—they’re now investing in their supply chains. These investments also are a tactic for managing through a tight labor market.
Not all changes are focused on technology. More companies are rethinking their manufacturing and supply chain networks. In part, that’s due to governmental regulations that are encouraging greater onshore production of critical medicines. “Both the United States and the European Union are advancing regulations on this front,” Bhandari says.
The goal is to reduce dependence on China. Concerns about cost, as well as a desire to develop domestic production capabilities, thus boosting supply chain resilience, also are behind this push.
Steady Supply Chain Improvement
The raw material shortages, port congestion, reduced flights, border closures, and other disruptions to the pharmaceutical supply chain due to COVID are less severe and less widespread, says Adalheidur Palmadottir, vice president of business development with Controlant, a leader in solutions that provide real-time supply chain visibility.
“Furthermore, measures put in place to counteract COVID-driven disruptions are gaining traction,” she adds. “These include the development and uptake of new, smarter technologies in the pharmaceutical supply chain, from sourcing and production to last-mile delivery.”
In addition, technological advances enable more reliable and traceable logistics, with significantly less leeway for human error. “Technology is reducing human handling across the whole sector, making for a more predictable, dependable cold chain,” Palmadottir says.
Many companies also are assessing and evaluating the lessons they learned during the pandemic to determine which are worth maintaining. “Companies that had to scramble for two years to keep the supply chain operating are now trying to figure out what to take forward,” Vadney says.
As a result, the condition of the supply chain now, versus 12 months ago, is vastly different. “We expect to keep moving toward greater digitalization in the coming year,” Palmadottir says. “Achieving this will require action, including greater collaboration among suppliers, manufacturers, logistics service providers (LSPs), carriers, governments, and healthcare facilities.”
Resilience is key, given ongoing challenges, including the need to adapt to the emerging post-COVID supply chain ecosystem, and to be in a constant state of readiness for continued disruptions, such as outbreaks of new COVID variants.
Controlant: Providing Valuable Information in Real Time
Controlant has been a pioneer of real-time supply chain monitoring for 15 years. The company’s automated visibility and tracking solutions use data from IoT-enabled loggers, which track a product’s location and condition throughout its journey. “So far, we have successfully delivered over 5.7 billion COVID-19 vaccine doses to over 60,000 destinations in 185 countries with a 99.99% success rate,” Palmadottir says.
“Our logger technology is groundbreaking, but the value in Controlant’s solution comes from turning real-time aggregated data into actionable insights,” says Palmadottir. “This is what gives pharmaceutical supply chain managers the power to make strategic decisions that strengthen their supply chain. The logger is a means to an end, providing valuable information in real time.”
Conventional loggers store information that can only be accessed post-shipment. Controlant’s solutions alert stakeholders to any quality issue—as the problem occurs. This enables them to mitigate any negative impact and prevent costly waste.
“We coined the term ‘cold chain as a service,’” Palmadottir says. “We help customers automate their business processes and optimize communication through technology to make their operations significantly more secure, reliable, and cost-effective.”
Controlant’s clients can review data retrospectively too, analyzing the information to optimize transportation modes, routes, or providers, or to compare the effectiveness of different packaging methods, among other things. The resulting insights help safeguard product integrity and reduce waste.
Products Delivered Safely
Every year, up to 35% of the world’s vaccines degrade due to temperature excursions. “Of the millions of vaccine deliveries that Controlant has monitored, this degradation is less than 1%,” Palmadottir says. Knowing that close to 100% of products will safely reach their destination has implications a long way upstream, as companies that need to fill orders are no longer compelled to over-produce, consequently reducing waste and manufacturing costs.
Controlant’s pay-per-use solutions can easily be scaled up or down, Palmadottir says. They can be integrated with a company’s ERP or other software system to streamline communications and provide a single source of truth. The loggers also can be recalibrated and reused, cutting down on supply chain waste.
The increasing population is straining global logistics and the supply chain as a whole. “Greater and greater demand means sourcing more raw materials, constantly ramping up production, and moving and delivering more products to more destinations,” Palmadottir says.
That’s prompting an increasing premium on space and time.
“The days of loggers that need manual inspection are numbered,” Palmadottir adds. “Controlant is working on a solution that goes even further toward addressing this challenge, as well as getting us one step closer to true end-to-end monitoring.”
Locus Robotics: Powerful Automation
Locus Robotics, based in Wilmington, Massachusetts, develops powerful autonomous mobile robots (AMRs). Known as LocusBots, they are designed for on-time healthcare fulfillment. Its experience in this sector is deep and expanding—it has tripled just in the past year—and clients include many top healthcare companies, Wang says.
“We’re experienced, proven, and a leader in providing AMRs to the healthcare supply chain sector,” he adds.
The Locus solution is customized for each client, which can include healthcare, medical device, and pharmaceutical companies, as well as hospitals and distributors.
By deploying robots in their distribution and warehouse operations, pharmaceutical and life sciences companies can alleviate labor challenges and ensure on-time shipping. The robots’ accuracy and ability to capture and validate serial and lot numbers mean the right products get to the right patients at the right time.
Locus solutions also maintain product traceability and enable compliance with serialization requirements. In order to bring current and new associates up to speed quickly, training on the solution typically takes just minutes.
LocusBots improve healthcare fulfillment in several ways. By optimizing material movement, they can drive productivity gains of 200 or 300%, without increasing the number of workers or the size of workspace.
“We increase pick and put-away efficiencies,” Wang adds.
Real-time data alerts supply chain professionals to changes in volumes, allowing the organization to efficiently scale the solution up or down to meet demand fluctuations. The robots themselves can easily be moved across multiple sites, and can shift between picking approaches, including batch and discrete order picking. They also can work with a variety of containers and totes.
The acquisition of Waypoint Robotics in September 2021 enhanced Locus’s ability to move larger, heavier loads, as well as smaller ones, Wang says. Waypoint’s Vector and Max robots are powerful, industrial strength, and designed for the warehouse and materials handling industry.
Waypoint’s solutions, now part of Locus Robotics, also are interoperable with Locus AMRs.
Increasing Productivity
A number of healthcare companies have benefited from implementing Locus AMRs.
One healthcare distribution center, for example, implemented six robots within an 18,000-square-foot life sciences center, integrating it with the company’s warehouse management system. The productivity increase was so pronounced that the center boosted its AMR population to 56 robots working across 99,000 square feet. Locus implemented this larger solution within 90 days.
With the AMRs, the center was able to process more than double the volume of orders it had been handling previously, with no change in headcount. Productivity rates now top 150 units per hour. On top of that, cycle time was cut in half. This ensures products move quickly to their destinations.
“We help customers meet their service level agreements,” Wang says. “And we make sure healthcare professionals have the supplies they need.”