Too Hot. Too Cold. Just Right.
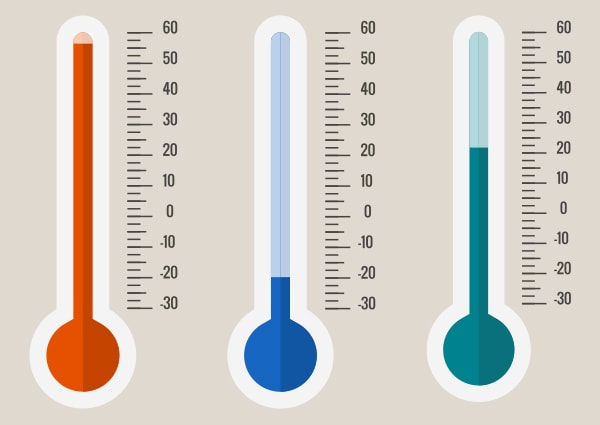
Flowers, pharma, chemicals, and other perishable products require temperature-control solutions with various degrees of difficulty.
You might be shipping vaccines to a pharmacy or a human organ to a transplant center. Maybe it’s chemicals to a semiconductor plant, or Valentine’s Day flowers to someone’s home.
Many products other than food demand careful temperature control. Let them get too warm or too cold and you render them useless.
Techniques for handling those products vary, depending on the commodity and volume involved. In some cases, you pack the product with coolant in an insulated box. In others, you need a trailer, shipping container, or warehouse with temperature control equipment.
You might also need a monitoring device, perhaps with a network for transmitting real-time alerts, and a process for addressing any problems that arise.
Here’s a look at what it takes to maintain the cold chain for products other than food, including some of the newest solutions available today.
Couriers for healthcare
Hospitals and medical labs often rely on couriers to transport organs, tissues, specimens, vaccines, and other temperature-sensitive products. Shippers usually provide their own packaging and coolant, adding data loggers to monitor temperature.
“We can also supply those things if that’s what the shipper wants,” says Matt Straub, executive vice president at Pillow Logistics in Indianapolis, whose customers include two major hospitals and several independent labs.
In either case, products should be packaged to maintain the cold chain for 24 hours, even if the scheduled transit time is much shorter. That’s to provide extra protection in case of a delay.
At Courier Connection, a delivery service based in Atlanta, healthcare clients also take the lead in maintaining the cold chain.
“They have a temperature-monitoring unit inside, and they package the product themselves, sometimes with dry ice, sometimes with wet ice,” says John Lauth, the company’s founder and CEO. If vaccines or other pharmaceuticals become too cold, that can be just as harmful as too warm, so the temperature must stay within a specific range.
That’s fairly easy in a courier vehicle with functioning heat and air conditioning and a well-trained driver. But recipients also need to handle the insulated packages correctly. Courier Connection learned this lesson the hard way when a driver delivered a shipment of vaccines to a security guard at a hospital on a Friday, after the pharmacy had closed.
The guard told the driver he had put the package in a cooler. “In reality, he just put it inside the pharmacy,” Lauth says.
By the time the pharmacist retrieved it, the vaccines were too warm, and the hospital refused them. Courier Connection and the hospital administration agreed to tighten their delivery protocol for the future. “Under no circumstances do we deliver to anyone other than pharmacy personnel who will put it away,” Lauth says.
Super-cool
Shippers such as those who use Pillow Logistics or Courier Connection can choose from many different temperature monitoring devices at a variety of price points. “They range from $30 to thousands of dollars, depending on what you need,” says Straub.
The options expanded even further in 2022 when Tive, a vendor of shipment tracking technologies, debuted a new device for pharmaceutical, biological, and gene cell therapy companies.
Tive’s previous tracker monitored temperatures from -30 C to +60 C. But its new Solo 5G tracker captures temperatures as low as -100 C for dry ice shipments and -200 C for cryogenic shipments, which use liquid nitrogen as a coolant.
Most of those super-cooled materials travel by air. “It would be hard to maintain that very low temperature for more than one week,” explains Alex Guillen, global subject matter expert, life science and pharmaceuticals, at Boston-based Tive. That rules out long over-the-road journeys or ocean transportation.
Tive won approval for its trackers from 130 airlines, a step that is necessary because the trackers use GSM wireless technology to transmit data in real time. Because that activity can interfere with airline communications, Tive’s tracker stops transmitting while in the air.
“The internal sensors recognize by acceleration that it’s in an aircraft, and then the tracker goes into sleep mode,” Guillen says. “It records the temperature, shocks, and all the other data, but it does not transmit that information to the cloud.”
When the plane lands, the sensors recognize that they’re back on the ground and resume transmissions.
When a package is on the road or waiting at the airport, and the Tive tracker finds that the temperature has gone out of range, it notifies the shipper or its logistics partner via text or e-mail.
Then, either the customer takes action, or Tive’s managed services team works with the courier company to correct the problem. Shippers can also check on their products at any time. “They can go into our portal and find out the status of the shipment,” Guillen says.
Insights From Across the Chain
Carrier Corporation, a global heating and cooling systems company, provides solutions for maintaining and monitoring the cold chain. Along with food and beverages, companies use the systems when transporting pharmaceuticals, biologics, lab samples, diagnostic materials, chemicals, and flowers.
One of Carrier’s newest cold chain solutions is Lynx, a cloud-based visibility platform that monitors temperatures and related data from across an entire supply chain.
“The platform offers all stakeholders the ability to securely and seamlessly connect and share data, hardware, services, and applications to deliver more efficient and intelligent cold chain operations at scale,” says Alice DeBiasio, vice president and general manager, digital solutions and Sensitech, at Carrier Refrigeration in Palm Beach Gardens, Florida.
For example, Carrier’s Lynx Fleet solution, based on the platform, collects thousands of data points from all the equipment involved in maintaining the cold chain—from the temperatures in cargo areas to performance data for refrigeration equipment.
“It then distills, analyzes, and consolidates this critical data into different insights, so fleet managers can quickly spot assets that may require special attention and make appropriate and informed decisions to optimize business operations,” DeBiasio says. Managers access this information via a dashboard.
Examples of the insights a company can gain through the Lynx dashboard include information on how much fuel it’s using to run refrigeration assets; visibility on battery and power management and alerts about anomalous conditions; and alerts to prevent catastrophic failures, such as the shutdown of a refrigeration unit.
Stay in spec
Rinchem, an Albuquerque-based logistics company that specializes in chemicals, handles a variety of temperature-sensitive materials, many of them used to make semiconductors.
Depending on the chemical’s characteristics and the shipper’s specifications, a product might need to stay at about 70 F, in the 35 F to 45 F range, or in the -13 F to + 5 F range.
To maintain the right temperatures in different parts of a warehouse, Rinchem installs redundant HVAC or refrigeration units. “If a unit goes down, the room itself doesn’t go down,” says Zach Tabor, Rinchem’s director of operations. “We also have technicians on contract to service these units within two hours.”
A temperature monitoring system senses imminent problems and automatically alerts the people who need to know, 24/7. “We get an e-mail or text, and we have an answering service on call,” Tabor says. At some facilities, managers can log in from home to assess the situation and make adjustments.
Rinchem also must maintain the cold chain for chemicals in transit, with journeys that could extend across the globe and take as long as 70 days. A shipment might pass through several climate zones—for example, when traveling from the Pacific Northwest to Texas. The temperature strategy needs to adjust to those changes.
A breakdown while in extreme conditions can be dangerous for chemicals that won’t tolerate too much heat or cold. “Sometimes we have only minutes, up to a few hours, to fix it,” says Dustin Miles, vice president of global transportation at Rinchem. “If we don’t, the load goes out of spec.”
Like its warehouses, Rinchem’s over-the-road trailers and ocean containers are equipped with remote monitoring systems that send alerts if conditions start to move in the wrong direction. On the road, a driver might make a correction, Rinchem might summon an equipment supplier to make a repair, or an employee might use the system’s remote capabilities.
“We can do a diagnostic and try on our own to reset the temperature to ensure it stays on spec,” Miles says.
When containers on the ocean start to move out of spec, Rinchem works with the steamship lines to make adjustments.
Getting a Grip
While many solutions focus on maintaining the cold chain once a product is in transit, Miami-based Grip Shipping takes a different approach: It helps companies plan how to execute specific temperature-sensitive shipments. The goal is to choose the right packaging, carrier, and route to make sure that perishable e-commerce shipments arrive in top shape, given the conditions they are likely to encounter.
“The shipping solution needs to be dynamic,” says Juan Meisel, Grip’s founder and CEO. Weather can change, freeway traffic can grind to a halt, or the carrier that always delivers promptly on Tuesday tends to run late on Friday.
“You can’t rely on flat logic, where you say everything from Point A to Point B is always shipped in a specific way,” he says.
Many of its customers sell food, but Grip also serves companies that ship insulin, flowers, and plants to consumers. Flowers and plants require sophisticated solutions because so many variables—temperature, humidity, time in transit, and more—can affect their condition.
For instance, in some regions, winter temperatures can swing from 60 F one day to -10 F the next. “Based on where you’re delivering the box, you see the pattern and adjust for those conditions,” Meisel says.
When an e-commerce merchant gets an order for flowers, for example, the order management system shares the details with Grip’s solution. Grip’s software analyzes all the relevant details, such as the capabilities of various carriers, the types of packaging the shipper has available, the product’s requirements, and the weather forecast. Then it makes a recommendation.
“We say, ship it from this building, with this carrier and this service, with this amount of refrigerant if they’re adding any,” Meisel says. Grip might also recommend adding a wet pack to the flowers to keep them hydrated during a long transit in hot weather.
In addition, Grip captures the feedback that consumers send to sellers, using data about the success of the delivery to inform future recommendations.
Whether the shipment involves one dozen fresh roses, a carton of vaccines, or a truckload of chemicals, when process and technology come together to keep product at its optimal temperature, that’s a truly cool outcome.
Beyond Dry Ice
For most new vaccines and other medical products that require ultra-low temperatures, the standard shipping solution is an insulated container stocked with dry ice. But dry ice comes with some serious drawbacks.
“It’s very difficult to get dry ice outside industrialized countries,” explains Peter Michael Hansen, head of global applications for Secop, a Flensburg, Germany-based company that makes compressors for cooling systems. “For example, it is almost impossible to transport COVID vaccines deep into Africa or other places with dry ice.”
Because it’s made of carbon dioxide that evaporates while in use, dry ice also harms the environment, Hansen adds.
With those and other challenges in mind, Secop and B Medical Systems, a producer and distributor of medical grade transport and storage solutions, have teamed up to create a new kind of medical transport box. Instead of passive cooling with dry ice, the new UT31 box uses a pair of battery-driven compressors, made by Secop, to keep product chilled inside a rotomolded insulated box created by B Medical Systems.
The UT31 will be a mobile ultra-low temperature freezer with a small capacity. The compressors are designed to take the temperature down to -122.8 F and keep it there, regardless of conditions outside.
While the box is in transit, the shipper can arrange to plug it into the vehicle’s battery. “There is no risk of a power disruption that might destroy the vaccine,” says Vittorio Iormetti, head of cooling technology and testing at B Medical Systems in Hosingen, Luxembourg.
The unit includes a remote temperature monitoring device that tracks the temperature inside the box and other conditions, such as remaining battery power and location based on GPS coordinates. The unit transmits this data in real time and sends alarms if anything goes wrong.
“We can access that information through the web,” Iormetti says. “It warns the shipper about what’s happening with the product.”