Value Chain vs. Supply Chain: Key Similarities and Differences
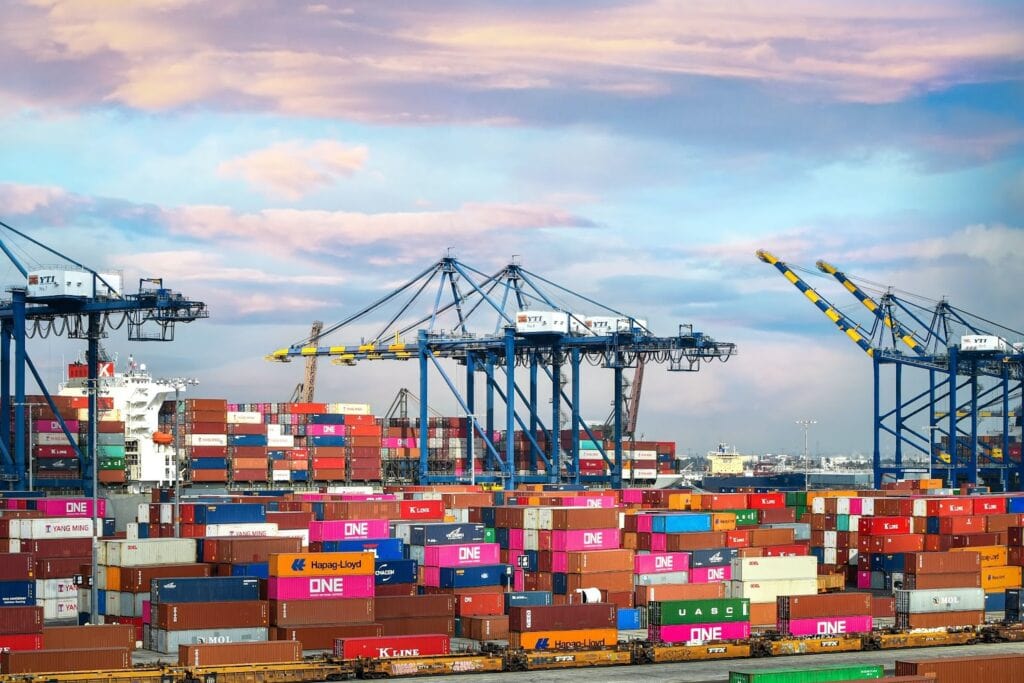
In business management, understanding the concepts of value chain and supply chain, as well as their similarities and differences, is crucial for optimizing operations and achieving a competitive advantage. Both these terms are often used interchangeably, but they represent distinct aspects of operational management.
We’ll explore why organizations must focus on value chain analysis and supply chain optimization to ensure seamless customer experience while efficiently acquiring goods and delivering finished products. This article will explain similarities and differences between the Value and Supply Chain to help propel your organization.
What Is a Value Chain?
Michael Porter introduced the value chain concept in his 1985 book, Competitive Advantage: Creating and Sustaining Superior Performance. A value chain refers to the series of activities that businesses perform to create, produce, market, deliver, and support their products or services. These activities add value at each stage of the process, ultimately resulting in the final product or service offering for customers.
A well-designed value chain can help organizations optimize operations and achieve competitive advantages.
Primary Activities
- Inbound logistics: This involves receiving raw materials from suppliers and storing them until they’re needed for production.
- Operations: This includes all processes transforming inputs into finished goods or services.
- Outbound logistics: Once products are completed, this component deals with warehousing, packaging, transportation, and distribution to customers.
- Sales & marketing: This covers everything from promoting products/services through various channels (eg, advertising), managing customer relationships (CRM),to pricing strategies that help drive sales revenue growth over time.
- Maintenance & support services: This consists of providing after-sales support like warranty repairs, maintenance contracts, technical assistance, etc., ensuring long-term client satisfaction, thus building loyalty and brand reputation.
To better understand how value chains work within an organization’s structure and identify areas for improvement or optimization, it is essential to analyze each component individually and collectively. By doing so, businesses can pinpoint where they excel and what needs to be addressed to achieve sustainable growth over time.
What Is a Supply Chain?
A supply chain refers to the network of activities, organizations, resources, and technologies involved in creating and delivering products or services from suppliers to customers. It encompasses all stages of production, including procurement of raw materials, manufacturing processes, transportation logistics, warehousing operations, distribution channels, and retailing.
The Components of a Supply Chain
- Procurement: The process by which businesses acquire raw materials or components needed for their product offerings from various suppliers.
- Manufacturing: In the transformation stage, inputs such as labor and machinery convert raw materials into finished goods that can be sold in the market.
- Distribution: The movement of finished products through various channels like wholesalers or retailers before reaching end-users (customers).
- Retailing: The final step is where customers purchase online or at brick-and-mortar stores based on their preferences.
The Role of Partnerships in Supply Chains
Ensuring smooth functioning across all stages within a supply chain ecosystem requires effective collaboration among its members. Organizations often form partnerships with key players like suppliers (strategic supplier relationships) or third-party logistics providers (3PLs) to optimize operations, reduce costs, and enhance overall efficiency. These collaborations can increase visibility across the supply chain, enabling businesses to make more informed decisions and better manage risks.
Supply Chain Visibility
Visibility in a supply chain is crucial for organizations as it allows them to track the movement of goods and information throughout their network. Enhanced visibility facilitates firms in discovering potential delays or inadequacies within their procedures, ensuring that goods are supplied punctually and of high quality.
Value Chains vs. Supply Chains Key Differences
We will examine the key differences between value and supply chains. While both concepts are crucial for businesses to understand, each has distinct functions and components that set them apart.
The Difference in Focus
The primary difference between these two terms lies in their focus. A value chain focuses on creating value at each stage of a product’s lifecycle, from inception to customer experience. Activities such as creating, advertising, aiding customers, and more are all considered in the value chain.
On the other hand, a supply chain refers to the processes involved in acquiring goods or raw materials from suppliers through order fulfillment and delivery of finished products to customers. The main goal here is to ensure efficient movement of goods while minimizing costs associated with production and transportation.
Sources of Competitive Advantage
The sources from which organizations derive competitive advantage also differ within these two frameworks:
- A company can achieve a competitive advantage through its value chain by offering superior customer service, creating innovative products or services, or developing effective marketing campaigns that resonate with its target audience.
- In a supply chain context, competitive advantage may stem from establishing strong relationships with suppliers to secure favorable pricing and terms, implementing efficient inventory management systems, or streamlining order fulfillment processes to reduce lead times.
Operational Management vs Customer Experience
The final key difference between value chains and supply chains is their respective emphasis on operational management versus customer experience:
- A value chain analysis focuses on understanding how each activity within an organization enhances the overall customer experience—this includes tangible product features and intangible aspects such as brand reputation and after-sales support.
- A supply chain optimization effort primarily targets improving internal operations related to procurement, production scheduling, and transportation logistics—all aimed at reducing costs while maintaining high levels of product quality and availability for customers.
Value Chains vs. Supply Chains Key Similarities
We’ll analyze the likenesses between value chains and supply chains – both vital for firms to comprehend to enhance their processes, diminish costs, and improve customer satisfaction.
A Focus on Efficiency
Both value and supply chains emphasize the importance of efficiency in business processes. By streamlining various activities within each chain, companies can minimize waste, lower costs, and improve overall performance. Streamlined efficiency is paramount in the modern, rapidly-evolving business landscape.
Interconnected Activities
Value and supply chains involve related activities contributing to the final product or service delivered to customers. In both cases, these activities must be carefully managed to ensure they work together seamlessly while maximizing value creation at each stage.
The Role of Stakeholders
In both value chain management (VCM), and supply chain management (SCM), stakeholders play an integral role in ensuring success throughout the process. These stakeholders may include suppliers, manufacturers, distributors, retailers, and end-users, who all have specific roles within either system.
Why You Need to Focus on Both
Understanding and overseeing value chains and supply networks is essential for organizations hoping to streamline their activities, cut expenses, and improve client fulfillment.
Complementing Each Other for a Holistic Approach
A value chain focuses on creating value through various business activities, while a supply chain emphasizes the efficient flow of goods from suppliers to customers. By combining these two approaches, organizations can develop a comprehensive view of operations that enables them to identify areas for improvement or innovation.
Better Decision-Making with Data-Driven Insights
Focusing on value and supply chains allows companies to gather data-driven insights from each aspect of their operations. For example, businesses can make informed decisions about where resources should be allocated or which processes need optimization by analyzing this information in tandem with one another—such as by comparing customer feedback against supplier performance.
Increase Competitive Advantage Through Collaboration
When teams responsible for different components within the value chain work alongside those involved in SCM, it fosters cross-functional collaboration that promotes efficiency improvements throughout an organization.
Improve Customer Satisfaction and Loyalty
A well-managed value chain ensures that customers receive high-quality products or services, while an efficient supply chain guarantees timely delivery. By focusing on both aspects simultaneously, businesses can consistently meet customer expectations – leading to increased satisfaction levels, repeat business, positive word-of-mouth marketing opportunities, and long-term loyalty.
FAQs
FAQs about value chains and supply chains can help comprehend these ideas.
Is value chain another name for supply chain?
No, the value chain and supply chain are not interchangeable terms. While both concepts involve a series of activities within an organization, they have different focuses. The value chain is centered on creating customer value through key components (eg, logistics, marketing). The supply chain is concerned with streamlining production and distribution operations to ensure that goods are delivered from suppliers to customers.
What are the three types of supply chains?
The three main types of supply chains include:
- Lean Supply Chain: This type emphasizes reducing waste by streamlining operations to increase efficiency.
- Agile Supply Chain: An agile approach prioritizes flexibility in response to market changes or disruptions. (source).
- Hybrid Supply Chain: A hybrid supply chain combines the best of both lean and agile approaches. It balances efficiency with adaptability to create a more resilient and responsive system (source).
Conclusion
Understanding the differences and similarities between value and supply chains is essential for businesses to optimize their operations. Both involve a series of activities that add value to products or services, but they have different focuses.
Businesses can gain an advantage in the competitive marketplace by understanding the distinct elements of value and supply chains to recognize where they may increase effectiveness and cut costs while enhancing customer satisfaction.