Chemical Logistics: Shippers/Providers Achieve Perfect Chemistry
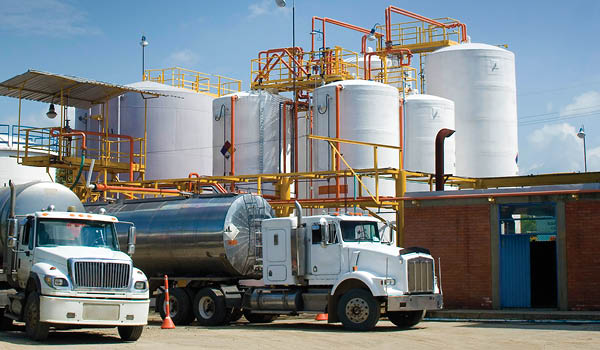
For the right blend of expertise, experience, and equipment, many shippers of chemical products turn to specialized carriers and 3PLs.
Getting the right product to the right place at the right time while controlling costs is a tough job for any shipper. When the product you handle is corrosive, combustible, poisonous, temperature-sensitive, or otherwise finicky about its environment, the challenge grows even tougher.
Complex Challenges, Sophisticated Solutions
Responding to Market Change
The science of chemical logistics demands blending specific elements—knowledge, experience, and specialized equipment—in precise combinations to achieve the desired reaction. So it’s no wonder many chemical companies rely so strongly on the bonds they’ve formed with their logistics and transportation service providers.
“The expertise they bring is the most valuable part of the relationship,” says Mike Rohrbaugh, manager of supply chain at Cincinnati-based Pilot Chemical Company, which partners with ChemLogix, a non-asset-based third-party logistics (3PL) provider and technology company based in Blue Bell, Pa.
One issue that sets chemical logistics apart from many other logistics disciplines is the potential danger posed by the cargo. “Transporting chemicals presents unique shipping requirements because of the inherent danger and potential impact on health, safety, security, and the environment (HSSE),” says Chris O’Brien, senior vice president at Eden Prairie, Minn.-based 3PL C.H. Robinson Worldwide, Inc., which provides transportation management solutions to chemical manufacturers through its ChemSolutions division.
Concerns about HSSE demand that chemical shippers comply with a slew of safety regulations beyond those that apply to shippers in general. The requirements start with federal rules for transporting hazardous materials. Vehicles hauling hazmat loads must carry placards to indicate their contents—for example, a toxic gas, a flammable liquid, or an explosive.
“Transporting chemicals presents unique shipping requirements because of the inherent danger and potential impact on health, safety, security, and the environment.” —Chris O’Brien, senior vice president, C.H. Robinson
Also, anyone who handles a hazardous load must be properly trained, certified, and equipped. “You’ve got to understand all the safety requirements for the kind of product you’re shipping,” says Ed Hildebrandt, senior vice president of operations at ChemLogix.
In addition to federal safety regulations, hazmat shippers also must comply with rules that vary as their loads cross state lines. “We need to plan which states we’re transporting product through, and know their requirements,” says Jeff Colonna, vice president of operations at Dupré Logistics, an asset-based logistics company based in Lafayette, La., that serves chemical shippers throughout the United States.
Then there are the safety rules that shippers and their customers create themselves. “Many of our major customers have extensive safety protocols for operating within their plants,” Colonna says. “Our employees must be well-versed in the operational and safety requirements, which are different for every customer.”
Carriers and 3PLs that manage chemical loads must implement stringent safety programs. The 3PLs also monitor safety at the carriers they employ.
“We pre-approve all transportation providers to ensure the appropriate level of driver training exists,” says Bob Shellman, president and chief executive officer at Odyssey Logistics and Technology (OL&T), a global 3PL in Danbury, Conn., with a strong chemical logistics practice.
Equipment used to carry chemicals also merits close scrutiny. “The valves on a bulk truck, for example, must have the appropriate safety inspections, so if a valve breaks off, the inner seals and valves will hold, and product won’t leak on the highway,” says Shellman.
To further ensure chemical loads’ safety, carriers and 3PLs operate programs based on standards established by the chemical industry. C.H. Robinson, for example, is certified as a Responsible Care Partner under the American Chemistry Council’s RC14001 specification.
“Each C.H. Robinson employee in the ChemSolutions group completes a certification training program before handling chemical shipments,” says O’Brien. “In addition, C.H. Robinson has developed proprietary software that houses an HSSE management system and tracks chemical shipments.”
Safety comes first in storage buildings, too. “Fire suppression systems must be compatible with the types of chemicals stored in the facility,” says Mike Gingerella, vice president, client solutions at 3PL Weber Logistics, which operates a 250,000-square-foot warehouse for packaged chemicals in Santa Fe Springs, Calif.
A chemical warehouse must meet the local fire department’s standards for firewalls and fire doors, and each storage room should be surrounded by a berm. “If chemicals leak, the berm keeps them contained to the room in which they’re stored,” Gingerella says.
In addition to keeping their own operations safe, some service partners also help chemical shippers with internal safety programs. ChemLogix, for example, offers compliance audits.
“We evaluate a company’s existing practices and compare them to what best-in-class shippers are doing,” Hildebrandt says. “Through this comparison, we help the shipper identify and fill gaps in its logistics processes.”
A&R Global Logistics, a non-asset-based 3PL that manages plastics and other chemicals, holds an annual quality and safety conference for its carriers. “We invite some of our customers as well, and we discuss safety and quality issues, especially those that have risen recently, so we can learn from one another,” says John Ciszek, chief operating officer of A&R Global Logistics.
Security Concerns
Along with safety, companies that manage chemicals must keep a close eye on security. Complying with U.S. Drug Enforcement Agency regulations for controlled substances has long been a safety and security concern. Since the Sept. 11, 2001, terrorist attacks, the U.S. Department of Homeland Security (DHS) has imposed new, more stringent regulations.
“If someone is ordering or handling excess volumes of certain types of chemicals, DHS wants to know,” Gingerella says. The agency also conducts regular inspections of facilities used to manage chemicals, and reviews all the related documentation. “Complying with multiple agencies is complex, but important,” he notes.
Some of the products chemical shippers move can be used as ingredients in illicit drugs or chemical weapons. “We need to understand the regulatory issues related to those types of products, so we can ensure they aren’t accidentally shipped to companies that may use them for illegal purposes,” says Shellman.
In addition to staying abreast of where they may or may not ship certain products, service providers address security by ensuring chemical loads reach their destinations intact.
“Any time a customer entrusts a load to us, it is under a Dupré employee’s care, custody, and control,” says Colonna. If the load travels via dry van or reefer, the trailer’s doors are locked and sealed. Also, the company’s Qualcomm TrailerTracs system allows it to monitor the exact location of every shipment in the supply chain.
Making Matches
While it takes great care to keep hazardous loads safe and secure, it requires specialized equipment to move any kind of chemical, hazardous or not. Different chemicals have different properties and needs, so it’s crucial to match each product with the right container.
The tank trucks that transport bulk liquid chemicals over the road come in different sizes and configurations, single- and multi-compartment versions, and other variations. One factor that determines the kind of tank used is the product’s viscosity and density.
If the truck stops short at a traffic light, for example, the momentum of the liquid in the tank causes a “sloshing effect” that might propel the truck into the intersection.
“One way to minimize safety issues is to keep the vessel as full as possible,” Hildebrandt says. This requires knowing the product’s density, and putting it in the correct size tank.
A tank used to transport chemicals might unload at the top, bottom, or center. “The tanks also have special hoses and fittings,” Hildebrandt says. When transferring the liquid for storage, the fittings must match the equipment available for unloading at the storage tank. There are many options, and it is important to choose correctly.
“As many as 170 accessorials could be involved with shipping a liquid product,” Hildebrandt says. “That’s why it’s difficult for shippers to manage this process and keep everything under control.”
ChemLogix also helps chemical shippers manage railcar fleets and maintenance. “We track inspection time requirements to ensure railcars are stopped for inspection, so they’re not sitting unused and out of compliance,” Hildebrandt says.
Dupré Logistics provides a variety of logistics and transportation services, as evidenced by its broad range of trailing equipment, including crude, chemical, and gasoline tankers; dry and temperature-controlled vans; reefers; and flatbeds.
“Dupré designs a logistics solution that considers shippers’ various needs, and typically results in custom-building equipment for that application,” says Colonna.
Equipment used to move dry bulk chemicals also needs special fixtures for loading and unloading. “Most plastics trailers have blowers and vacuums,” says Ciszek. Drivers responsible for transferring plastic pellets from a railcar to the truck attach a hose between the two. “They plug it in, then vacuum the product out of the railcar.”
Employees transferring those plastic pellets—or anyone else involved in moving chemical products—must fully understand the product to handle it correctly.
“If you use too much pressure, the plastic can melt, creating strands and clumps,” says Ciszek. The correct pressure depends on the properties of the product being transferred, the distance over which it is being blown, and, if the driver is transferring it to a silo, the height of the storage facility.
“Typically, chemical products move from a processing plant to a customer who has an immediate need for them. One delayed truck could shut down an entire plant.” —Jeff Colonna, Dupré Logistics
To avoid contamination, it’s also crucial to clean tanks and containers thoroughly before filling them with another product.
Some chemicals require special treatment during transport. “If the product being loaded is a reactive product,” says Shellman, “the appropriate inhibitors must be included to prevent polymerization, which is an expansion of the product that can cause a leak or issue.”
A chemical warehouse also must accommodate products with diverse characteristics. Weber’s facility has 13 rooms, including spaces dedicated to flammables, corrosives, oxidizers, and toxins. Some rooms are temperature-controlled to protect chemicals sensitive to heat or cold.
“Maintaining the correct temperature helps expand the product’s shelf life and keeps it at peak performance,” Gingerella says.
Even ordinary supply chain challenges take on complexity when the products in question are chemicals. “Typically, chemical products move from a processing plant to customers who have an immediate need for them,” says Colonna. This creates time constraints on the supply chain.
“One delayed truck could shut down an entire plant, so systems must be in place to ensure carriers deliver the results the shipper expects,” he adds.
Tight Deadlines, Scarce Capacity
Guaranteeing those results can be tough in a segment of the transportation market where capacity is especially tight. In the dry bulk segment, for example, most carriers are small companies that operate only 50 to 60 trucks. “And they’re not growing,” Ciszek says. “They’re not adding terminals, drivers, or equipment.”
Training drivers to handle a specialized commodity is difficult, and it is also hard to secure loans for pressurized tractor-trailers outfitted with blowers and other special equipment. So the pool of trucks and drivers available for hauling dry chemicals isn’t likely to increase.
“The driver shortage is magnified for us because we’re transporting hazardous chemicals,” says Joel Bishop, purchasing and transportation manager for the water treatment chemicals division of GEO Specialty Chemicals in Little Rock, Ark. “Drivers must do more than operate trucks—they also carry a responsibility for safety.”
Burgeoning demand is putting greater pressure on this limited supply of equipment and drivers. Plastics manufacturers are generating more product, so there is more to haul.
Because natural gas—an important raw material for plastics—is inexpensive right now, many plastics manufacturers have expanded their operations. “But carrier capacity isn’t growing with them,” Ciszek notes.
Natural gas has also created capacity problems for companies that ship bulk liquids, because drilling in the Marcellus Shale has attracted hordes of tank trucks and drivers to Pennsylvania and Ohio. “That has been a huge drain on the already finite driver pool,” says Hildebrandt.
Divide and Conquer
Tricky as it is to ensure a steady supply of tank trucks, it can be even trickier to obtain enough trucks with tanks divided into multiple compartments. There simply aren’t many of them on the road, and demand is growing.
“Some of our customers—particularly the distributors—are trying to transition to a just-in-time environment,” says Rohrbaugh at Pilot Chemical, which supplies specialty chemicals to makers of detergents, personal care products, lubricants, latex applications, and other products.
The switch to a just-in-time supply chain dictates more frequent deliveries of smaller quantities—for example, three 15,000-pound loads per week instead of one 45,000-pound load. The most efficient way to meet that need is to deliver several products at once, which creates demand for multi-compartment shipments.
To help shippers avoid the capacity crunch and meet service obligations, 3PLs rely on their extensive carrier and customer networks. The 3PLs use those networks, for example, to build continuous loads for their carriers.
“When we’re handling multiple shippers and carriers, we can connect the dots to fill trucks, giving shippers the capacity they need at the lowest possible cost, and keeping trucks moving,” says Ciszek.
Knowledge is Key
Access to scarce capacity is just one benefit chemical shippers gain from 3PLs and carriers that understand chemical logistics inside and out. Because they work with so many customers—and, in the case of non-asset-based 3PLs, so many carriers—those partners’ knowledge base runs both broad and deep. They stay updated on safety requirements, industry best practices, market activity, and industry conditions that affect their customers.
“Service providers must keep abreast of all regulations, new equipment, and best practices for managing the process,” says Hildebrandt. A chemical company’s own logistics professionals might know a great deal, but their experience will be limited to the issues they have faced on the job.
“If you don’t have critical mass inside your own logistics organization, you will never be able to keep up with what’s happening in the market,” he adds.
Every 3PL customer benefits from the knowledge their 3PL accrues while working with all its other customers.
Pilot Chemical, which outsources all its freight management to ChemLogix, has benefited particularly from the 3PL’s knowledge of market trends. For example, ChemLogix made sure the shipper always had enough trucks when capacity tightened in 2007 and 2008.
As the economy started to improve, the 3PL helped Pilot obtain more favorable freight rates. Then, as carriers started to consolidate, shrinking the pool of trucks again in 2009, ChemLogix advised Pilot to add a new carrier to its roster.
“They made suggestions so we could be proactive and do business differently, which ensured we would be in a better position to serve our customers,” Rohrbaugh says.
For GEO Specialty Chemicals, Dupré Logistics provides a dedicated fleet to move shipments of liquid aluminum sulfate from 14 manufacturing plants to paper mills, municipalities, and other industrial customers. Dupré also backhauls sulfuric acid to those plants.
The logistics partner has helped GEO optimize its transportation network to create money-saving efficiencies. Dupré also ensures GEO’s hazardous chemicals are transported safely.
Many newer safety regulations—such as those covered by the Federal Motor Carrier Safety Administration’s Compliance, Safety, and Accountability (CSA 2010) initiative—are complicated. Dupré understands those rules well.
To further ensure compliance with federal regulations, Dupré has taken the additional step of implementing electronic driver logs.
Tackling the Tactical
Although shippers of all kinds rely on the broad knowledge and market clout of their service providers, 3PLs and carriers with expertise in chemical logistics offer additional advantages.
“A lot of logistics departments are resource-starved,” says Ciszek. That makes it hard for them to give enough attention to matters such as regulatory compliance.
“We can provide the resources to perform audits, for example, which many customers don’t have the time or personnel to complete,” he adds.
Shippers that manage their supply chains in-house typically spend a lot of time focusing on items that require a tactical response, such as tendering orders, tracking shipments, and resolving claims.
“New approaches to outsourcing are helping chemical manufacturers drive down costs in the short term by eliminating tactical responses, which, in turn, allows time to focus on strategic needs,” says O’Brien. “That helps them build smarter, stronger supply chains for the long term.”
Relying on a 3PL or carrier with the right knowledge, experience, and resources also frees companies to focus on their main line of business.
“We decided to outsource because we’re a chemical company, not a transportation company,” says Rohrbaugh. While Pilot’s employees possessed the expertise required to handle logistics, they had other duties to attend to as well.
“They didn’t have time—and we didn’t have the resources—to manage all this ourselves,” he says.
Chemical companies that outsource some or all of their supply chain activities can concentrate on their core business. “By integrating our people and systems, we design a specific solution that will create operational efficiencies and financial savings that allow our customers to be more profitable,” says Colonna.
When shippers and service providers develop the right kind of chemistry, the results can be spectacular.
Complex Challenges, Sophisticated Solutions
Numerous challenges have prompted specialty chemicals manufacturers to seek help from third-party logistics providers (3PLs) in recent years. Greater supply chain complexity; the need to comply with ever-more stringent trade, security, and environmental regulations; changing patterns of production and consumption; and the continual drive to operate more productively and profitably are just a few of those challenges.
Such complex demands require sophisticated solutions. “Notwithstanding pressure to reduce costs in the short term, 3PL assistance typically goes well beyond finding the cheapest transportation rates available. It encompasses optimizing supply chains and overall logistics processes for even larger, longer-term savings,” says Arnie Bornstein, a spokesman for Philadelphia-based BDP International, whose company—a non-asset-based 3PL—includes a division focused on chemical logistics.
One case in point is a U.S.-based specialty chemicals company whose products include plastic additives, flame retardants, pool and spa products, seed treatments and miticides, urethane polymers, and components for lubricants. As the company started to expand its Asia-Pacific operations, it needed to add warehouses to its network, increase control over and visibility into logistics processes, improve efficiency, and reduce costs.
The company turned to BDP for help, working with the 3PL’s Singapore operation. Today, BDP manages two warehouses in Singapore for the customer—one for chemicals and hazardous cargo, and the other for chemicals and general cargo.
BDP also manages a bulk shore tank storage and distribution center in Taiwan for the customer’s petroleum additives unit, plus the warehousing and distribution operations in Shanghai.
Thanks to these services, the shipper can now bring products closer to its Asia-Pacific customers, which gives it better control over shipments and inventory, according to the chemical company’s regional logistics director.
“Shipments are turned around more quickly because much of the inventory is in Asia,” Bornstein says. “Products can arrive in Singapore from the United States and be re-exported to other locations in the region within days.”
Using the BDPSmart customer service portal, the shipper can follow cargo through every milestone as it executes an international order.
Rather than simply seeking the lowest transportation rates, the chemicals manufacturer has gained measurable results by taking central control over its global business units to improve shipment visibility and optimize expenditures. The company is also looking both upstream and downstream to monitor the performance of various points in its supply chain.
“This ultimately improves productivity and profitability,” Bornstein says.
Responding to Market Change
Faced with the chemical market’s demand fluctuation and unpredictability, many chemical companies seek ways to better manage overhead costs such as warehousing and distribution. National third-party logistics provider WSI has helped a number of chemical companies consolidate their storage and labor needs, reduce costs, and boost operating flexibility.
For example, one of the world’s leading producers of polymers and high-performance plastics has, in recent years, spun off several business units and reconfigured its supply chain. The company found it no longer had the volumes to support its large West Coast distribution center, and turned to WSI for help. WSI assumed operation of the facility, giving the customer much-needed flexibility in storage volume and handling capacity.
“The facility was a fixed cost. We took over the operations and made it a variable cost,” explains WSI spokesperson Rob Kriewaldt. “We helped the customer dramatically reduce costs, while utilizing excess capacity in the facility for other customers and expanding our offerings to include import/export services due to the facility’s strategic location.”
Similarly, when the customer wanted to downsize its East Coast distribution operations, it closed a New York City area facility and moved into a WSI location in Allentown, Pa. “They wanted flexible space and labor costs,” Kriewaldt says. “We’ve given them the ability to grow and shrink their space as needed, as opposed to having a fixed cost every month.
“The chemical industry is cyclical,” he adds. “Our services allow chemical shippers to tailor their costs to the ups and downs of their business cycle.”