COVID-19 Resets: Logistics Draws the Line
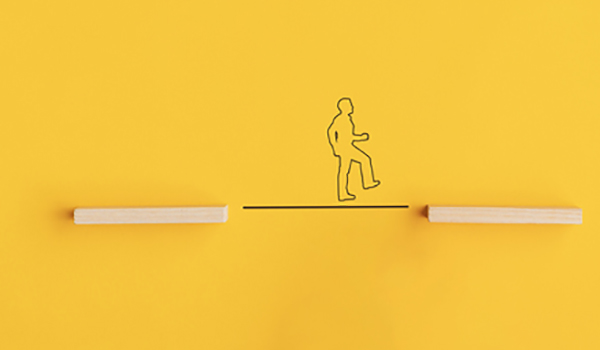
Adept pivots. Generous acts. Creative solutions. Logistics and supply chain companies put one foot in front of the other and face down a global pandemic.
Construction workers and outdoorsy types know Carhartt for its rugged apparel. “A hardworking brand for hardworking people,” is how William Hardy, senior vice president of supply chain, describes the company. When the Kentucky Department of Emergency Management asked Carhartt to make medical gowns and masks for those on the front lines fighting COVID-19, management and employees asked, “How quickly can we do it?” Hardy says.
Twenty-four hours after receiving samples, the company was manufacturing its own. Within four weeks, Carhartt was producing gowns.
To accomplish this, Carhartt created a new materials supply chain to find fabric that would be durable, but also light enough to be comfortable for healthcare workers. It turned to its existing suppliers, who then connected the company with vendors of the three fabrics ultimately used in the gowns and masks. “Everyone wanted to help even if we weren’t purchasing from them,” Hardy says.
As of mid-May 2020, Carhartt had made more than 50,000 medical gowns at its plants in Kentucky, Tennessee, and Mexico, and distributed them to healthcare providers.
The pandemic has brought out the best in many people and their organizations. Like Carhartt, supply chain organizations across multiple industries have donated generously, worked long hours, and crafted innovative ways to make and distribute essential supplies and food.
“The pandemic has shined a light on the supply chain,” says Joe Vernon, practice leader, supply chain analytics, with research firm Capgemini. “It’s moving from the second tier to the top tier of strategy.”
Shifting Production
Like Carhartt, numerous manufacturers pivoted from their usual production runs to create items desperately needed by front-line workers. For example, Boston-based New Balance is known for its athletic shoes and apparel. Yet when several healthcare groups reached out, management considered how the company could best leverage its manufacturing capabilities to assist in the fight against the pandemic. “We landed on masks,” says Dave Wheeler, chief operating officer.
New Balance employees consulted with experts from area hospitals and the Massachusetts Institute of Technology, and then worked over a weekend to create a prototype by Monday. By Friday, the masks were in production.
Two keys to the company’s rapid response were strong relationships with domestic suppliers and deep expertise in U.S. manufacturing. “We’ve invested a lot of money in domestic manufacturing,” Wheeler says, such as automated laser cutting equipment.
Once cut, the pieces needed for each mask are gathered and move through a heat press that binds them together, eliminating perforations that would result from sewing. Final products are automatically labeled and shipped from the company’s distribution center. New Balance is currently producing about 100,000 masks weekly and making them available at cost or as donations.
Stratasys launched its GrabCAD online community in January 2020 to enable engineers and designers to share designs, CAD files, and other information, says Scott Drikakis, healthcare segment leader with the Eden Prairie, Minnesota-based firm. It’s also helping Stratasys’ pandemic efforts.
Stratasys’ leadership, working with healthcare providers, knew the company could quickly create digital patterns for face shields and then produce the shields themselves. When Stratasys let its medical customers know what it was doing, it received 300,000 requests within 36 hours.
“We knew we needed assistance,” Drikakis says. So, he and his colleagues reached out to Stratasys’ other customers and business partners. More than 100 signed on to help make the shields.
Stratasys leveraged GrabCAD to route and track orders and shipments. “If we didn’t have GrabCAD, I’m not sure how logistically we could operate 100-plus companies accepting, fulfilling, and shipping orders,” Drikakis says. As of early May 2020, the companies had shipped more than 100,000 shields.
Distribution Pivots
As stay-at-home orders proliferated throughout the United States in March and April 2020, many restaurants closed and consumers overran grocery stores.
C&S Wholesale Grocers partnered with several food service companies. Warehouse and delivery employees from these firms temporarily transferred to similar job functions within C&S while remaining employees of their respective companies.
“These partnerships allow C&S to alleviate a potential worker shortage stemming from increased food retail demands,” while also providing temporary work opportunities for other individuals, says Mike Duffy, chief executive officer of C&S.
The restaurant shutdowns also left many growers with excess products. Produce distribution firm Pacific Coast Fruit Company, through a contract from the U.S. Department of Agriculture, is working with local nonprofits to distribute more than 800,000 boxes of produce and dairy products to families in need.
As a first step, Pacific Coast contacted the growers with which it had relationships, as well as other growers, such as dairy farms, to determine those that were interested. It also identified interested nonprofit organizations, determined the number of boxes they could safely store and distribute, and evaluated access to their facilities.
“Some pickup locations anticipated more than 500 cars picking up boxes,” says Sara Thompson, director of purchasing and wholesale sales with Pacific Coast. Thompson and her team then organized equipment, drivers, and drop-offs.
Another challenge was making sure growers and producers had enough product to ship, with little notice. The project has also been a “great reminder that with a project this large, you need to have good relationships with your growers and manufacturers,” Thompson says.
“When you see the overwhelming number of cars and people waiting at a drop site for our truck to bring the boxes, it’s humbling,” she adds.
3PLs Show Their Strength
Given the heightened focus on supply chain resulting from the pandemic, many third-party logistics (3PL) providers have supplied expertise and systems. Oren Zaslansky, chief executive officer and founder of Flock Freight, realized early in the pandemic that sales for some of Flock’s clients would spike, while others likely would see a drop. Using SIC codes, he and his colleagues were reasonably able to predict which fell into each group.
Flock Freight asked customers apt to need extra support, such as those shipping personal protective equipment (PPE), how they could help. For instance, some needed to move smaller quantities into the supply chain more quickly than they normally would.
Zaslansky then asked some other customers if they could manage slightly longer delivery times, often in exchange for slight discounts. All agreed. “People were looking for opportunities to be part of the solution,” he says.
Omnae, a startup focused on supply chain management technology, had previously partnered with manufacturers in Asia to build custom products. As the pandemic took hold, Omnae’s employees, many of whom had taken time off, went back to work. Within a few weeks, they’d launched a medical supply sourcing business and identified factories that could produce masks, PPE, and other items.
Employees quickly became experts on specifications and certifications, and on distinguishing real products from counterfeits. The company’s freight forwarder allocated some of its reserved future capacity to Omnae’s shipments, ensuring the products would be expedited.
During the course of several weeks, Omnae delivered or donated 400,000-plus units of PPE to healthcare providers. “It was an absolute whirlwind,” says Dan Lionello, chief executive officer and founder of the Vancouver, British Columbia-based firm. Employees have since shifted back to the company’s primary business.
Moving medical equipment into hospitals in Manhattan is challenging any time. Amidst a pandemic, it becomes even more fraught. To minimize the risk of exposure, engineers couldn’t enter the hospitals to calibrate the equipment, as they normally would.
Pilot Freight Services arranged for a client’s medical equipment to be delivered to a Pilot facility in New Jersey; engineers would test it there. Pilot then repackaged the equipment and transported it to Manhattan, where it could be put into immediate use. “We were flexible and came up with solutions,” says John Hill, president and chief commercial officer with the Glen Mills, Pennsylvania-based firm.
Navigating Turbulence
The drop in passenger flights resulting from the pandemic also cut airfreight capacity, as much air cargo transport occurs in passenger planes. To mitigate this, DHL Global Forwarding U.S. established dedicated charter flights for shippers moving PPE and medical supplies. For instance, it’s providing charter flights from Europe to the United States for Getinge, a manufacturer of ventilators based in Sweden. It’s also helping fast-track the priority shipments through customs.
“Our relationships with not only airlines, but also with customs helps expedite these valuable shipments,” says David Goldberg, chief executive officer.
As the severity of the pandemic became clear, Federal Emergency Management Agency (FEMA) began routing planes filled with PPE and other essentials through several airports, including Rickenbacker International Airport in Columbus, Ohio, a cargo-only airport.
“Some people wondered why FEMA was sending shipments to Ohio,” says Bryan Schreiber, manager of air cargo business development with Columbus Regional Airport Authority. “We’re well equipped to handle those shipments quickly and efficiently.”
When PPE is arriving, trucks are at the dock and the freight is on the road about six hours after it lands. At some airports, this could take a day or two.
Truckers keep rolling
The nation’s 3.5 million truck drivers move more than two-thirds of all goods (by weight) in the United States. While the volume of long-haul trips has dropped by about one-third during the pandemic (see chart), trips of less than 100 miles more than doubled, according to the American Transportation Research Institute (ATRI). Anecdotal evidence suggests this has been driven by the need to move consumer products from regional warehouses to stores, ATRI notes.
Along with food and household goods, truckers are moving medical equipment. When Aultman Orville Hospital had to move hospital beds—each weighing 500-plus pounds—as well as IV poles and other equipment from the University of Akron-Wayne College to the hospital, they couldn’t turn to their own employees. Many were already dedicated to delivering PPE within the Aultman Orville system. “Our first call was to PackShip USA,” says Angela Caldwell, chief operating officer of the hospital.
PackShip USA freed up five employees to move the equipment quickly and safely, says Aaron Nussbaum, director of logistics and operations. He credits their success to a well-trained staff with experience moving high-value, fragile, and bulky items.
Changing Supply Chains
Even as many companies and countless employees worked tirelessly and devised ingenious ways to help in the fight against COVID-19, the pandemic also “created a new awareness of the volatility and uncertainty of the supply chain requirements,” says James Tompkins, Ph.D., and founder and chairman of Tompkins International, a supply chain consultancy.
Rather than a return to an old normal or even a new normal, supply chains will move to “the next normal,” Tompkins says. “The most important element for the supply chains of the future will be optionality—the ability to pivot from one option to the next to address changing market and customer demands.” That will require agility, flexibility, and visibility, he adds.
To be sure, many organizations had already been moving to digitized, smarter supply chains. Yet, few previously had reason to feel a sense of urgency.
“Companies didn’t understand how such a disruption would highlight their inability to operate at velocity without tools like digitization,” which allow them to work from exceptions, rather than adjusting for each order, says Cyndi Lago, vice president of supply chain at Capgemini.
Another coming shift in some industries will be greater use of near sourcing, or working with vendors close to where the company’s products are sold, Lago predicts. More companies will likely work with multiple suppliers.
When the pandemic subsides, supply chain organizations will face numerous challenges. They can take pride in the work they’ve done to meet the challenges arising from the COVID-19 pandemic.
“At a time when a lot of people were scared and hunkering down, we had a purpose,” Lionella of Omnae says. “Everyone knew they were doing something to help others and went above and beyond.”
A Safe Bet
Along with extraordinary efforts to move essential products, supply chain organizations are implementing new processes and tools to keep their drivers safe.
Truck drivers may pass through more than one dozen states in a single week, says Steve Syfan, executive vice president with Syfan Logistics. Once they arrive at a shipping office, they often interact with employees to obtain additional instructions and complete various forms.
While the company provides truckers with masks and gloves, he would like to see drivers remain in their trucks during pickups and deliveries to further reduce the risk of inadvertently spreading any virus with which they may have been in contact. Communication and document transmissions, such as bills of lading, would be completed electronically. “The driver won’t be exposed and neither will the people in shipping and receiving,” he says.
Currently, many big companies can transmit electronic bills of lading, but some smaller ones can’t. Making this shift would likely take several years and require the support of regulators and elected officials. Syfan adds that he has been in contact with state and national leaders and most are “100% on board,” he says.
“Everyone now uses electronic logging devices and has adjusted to them. They could also adjust to electronic billing,” he says. Along with keeping everyone safer, the change would boost efficiency.