Intermodal Benefits Come Into Focus
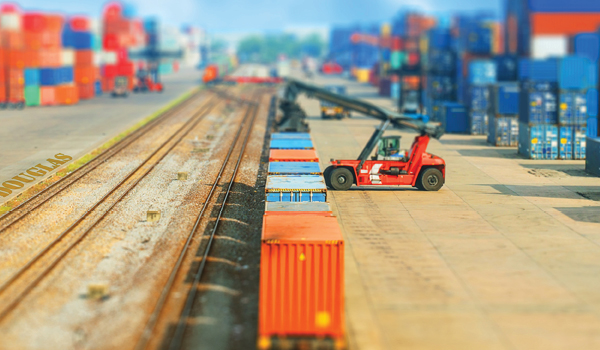
Intermodal is looking sharp to a growing number of shippers, thanks to tightening truck capacity, new service options, and infrastructure improvements.
Following a slow stretch in 2016, intermodal transportation is picking up speed in North America. Total intermodal volume in the second quarter of 2017 was 4.5 percent higher than in Q2 of 2016, according to the Intermodal Association of North America (IANA). That represents the strongest growth in three years, IANA says.
The biggest increase came in international intermodal freight; volume rose by 5.6 percent compared with 2016. But North American shippers have been moving more domestic containers and trailers, too. Volume for those boxes increased by 3.2 percent and 3.9 percent, respectively.
Intermodal volumes ebb and flow in response to several related forces: truck capacity, trucking rates, and general demand for transportation. Until recently, in the United States, those forces were working against the intermodal market. “Increased competition by way of surplus truck capacity, paired with only modest increases in consumer demand, have been a driving force behind these trends,” says Mark McKendry, vice president, intermodal at asset-based third-party logistics (3PL) provider NFI in Cherry Hill, New Jersey.
Today, the trucking market is starting to tighten. “As truckload spot pricing increases, shippers are once again looking to rail to save money and add capacity,” says Matthew Decker, vice president of intermodal at Chicago-based Coyote Logistics.
Coyote, owned by UPS, provides door-to-door intermodal solutions via its wholesale relationships with the railroads, as well as customized door-to-ramp solutions and drayage management, with services throughout North America.
The Price is Right
Shippers turn to intermodal when they’re looking for better prices, says Rick LaGore, CEO at Intek Freight and Logistics in Indianapolis. Intek provides door-to-door intermodal service through its direct relationships with the railroads. It also provides ramp-to-ramp service with drayage at either end, and it repositions sea containers.
“Not every rail intermodal lane will be able to save you money,” says LaGore. But when the origin and destination are reasonably close to intermodal terminals, that mode can provide advantages.
Today, shippers who keep an eye on over-the-road (OTR) capacity and pricing are especially concerned about what will happen after December 2017, when carriers must comply with a new federal requirement to install electronic logging devices (ELDs) on commercial trucks. The rule could force some carriers out of the market and—by monitoring hours of service (HOS) compliance more precisely—cut the number of hours that drivers are available to move freight. Those constraints could push more shippers toward intermodal.
Among shippers making that move could be companies that need to transport temperature-controlled products such as fresh produce, frozen foods, and pharmaceuticals. “Many shippers don’t know that temperature control is an option on intermodal,” says LaGore. The rails don’t carry a great many temperature-controlled intermodal containers today, he says. But service providers could start to boost those numbers as more shippers realize the value such boxes offer in certain lanes.
The pricing for temperature-controlled intermodal works out best when the origin and destination are both within 50 miles of a rail terminal. “More of this product will be moving between major cities, such as Los Angeles to Chicago, Chicago back to Los Angeles, or Seattle to Chicago,” says LaGore.
NFI customers that use temperature-controlled intermodal can monitor the condition of their products en route, and NFI makes sure those products stay in good shape. “Our state-of-the-art, telematics-equipped containers provide the ability to adjust temperatures remotely,” says McKendry. Customers also can get real-time reports on a container’s location and estimated time of arrival, plus a suite of diagnostic tools.
Rails Keep Getting Better
Along with better pricing, proliferating service options and improved performance are also drawing shippers toward intermodal. “The rails’ intermodal service is far better than it was from a historical perspective, even compared to five or six years ago,” says Decker. “Many lanes with competitive intermodal services simply didn’t exist a decade ago.”
Weather events in the West and significant network changes in the East accounted for a downturn in service quality in 2017, Decker says. But the railroads continue to make improvements, adding double tracking in new areas, adding or expanding terminals, and applying technology to make their networks operate smarter and faster.
As one example, Decker points to CSX’s new terminal in Pittsburgh. “CSX also announced plans to build a Rocky Mount, North Carolina, facility, currently slated for a 2020 opening,” he says. “Whether it’s new facilities that reduce the length of drayage hauls, or new lane offerings between existing terminals, any increase in intermodal network density makes the service that much more attractive to shippers.”
Sometimes, a Class I railroad doesn’t even need to build a facility to make new options available. “CN [Canadian National] has been very creative, partnering with various shortline railroads to help them provide service in areas where they otherwise would not have a ramp,” says LaGore.
For example, through a partnership with the Indiana Railroad, CN now offers service from Canada’s West Coast ports to Indianapolis, letting shippers avoid the congestion they would encounter in Los Angeles-Long Beach and Chicago.
Intermodal Across the Border
Shippers that move freight between the United States and Mexico received good news in December 2016, when BNSF and Kansas City Southern jointly launched a new set of cross-border intermodal services. One new lane links Chicago and Dallas/Fort Worth with five-day-a-week service to and from Monterrey and San Luis Potosi or Toluca, with additional service to Laredo, Texas.
“These services provide transit times that are competitive with over-the-road options and, unlike truck shipments, they don’t have to stop at the border for customs clearance,” says Tom Williams, vice president, consumer products at BNSF. “Instead, shipments travel in-bond, clearing customs at origin and destination in Mexico.”
BNSF also started a new intermodal service in 2016 between the Northwest and Texas.
Besides adding terminals and routes, the Class I railroads also continue to upgrade their infrastructure. BNSF, for example, has been adding double track to its Southern Transcon—the corridor between southern California and Chicago—since 1992.
“In 2016, we constructed the new Pecos River Bridge and secondary mainline in New Mexico, so that we are 99.8-percent double tracked along this route,” Williams says. “This allows for increased volume and improved velocity and fluidity.” BNSF has also spent $5 billion over the past several years on maintaining and expanding its Northern Corridor, from the Pacific Northwest to Chicago.
Along with track improvements, terminal upgrades are crucial to fast, reliable intermodal service. BNSF has spent more than $1.2 billion since 2002 on projects to expand capacity and improve velocity at its intermodal hubs, says Williams. On the capacity side, it is adding more track, more cranes to load and unload trains, and more parking for trailers and containers.
BNSF is also implementing technology to speed freight in and out of its facilities. For instance, at its Phoenix, Houston, and St. Paul terminals, the railroad is adding new automated gate system (AGS) technology, with biometric driver identification, license plate recognition, and tire inspection portals.
“The AGS reduces the amount of time that a driver spends at our gate from three to five minutes to as fast as 30 seconds,” Williams says. Eighty-five percent of freight moving through BNSF facilities will go through an AGS when the technology is fully up and running at those three terminals.
Despite upgrades of that sort, terminal congestion continues to pose challenges for intermodal freight. “It’s a complex problem that’s connected to the shipping community’s seasonality and weekly patterns,” says McKendry. Some regions have seen improvement, but others, such as Chicago, continue to struggle due to the volume of demand and the concentration of the network in that area.
Moving With Precision
Promising solutions do exist. “Reservation systems, although imperfect, can help to give rails and port operators visibility to inbound and outbound truck arrivals,” McKendry says. “Precision railroading can lead to timely departure and placement of trains at terminals. Consensus on better rail routing around or through Chicago would also lead to reduced congestion.”
Precision railroading, a concept championed by Hunter Harrison, the new chief executive officer at CSX, operates trains on a tight schedule, regardless of whether they are empty or full. The move to precision railroading has gained a great deal of publicity.
“It has been off to a rocky start,” Decker cautions. “It is unknown whether those changes will pay off with long-term service improvements.”
While railroads improve their networks, 3PLs and intermodal marketing companies also work to give shippers more bang for the intermodal buck. NFI, for instance, promotes its use of containers that are built to sit on an intermodal well car, which allows for double stacking—a strategy the railroad can’t use when it loads an OTR trailer on a flatcar.
“Double stacking often carries significant economic advantages to the shipping community and to the railways themselves,” McKendry says.
Since UPS acquired it in 2015, Coyote Logistics has gained inexpensive access to intermodal containers that UPS needs to reposition, and which would otherwise move empty. Coyote has used those containers to help some customers.
For example, one major packaged foods shipper used to run truckloads from the Greensboro, North Carolina, area to Chicago and New Jersey. “UPS consistently had surplus equipment in Greensboro, and access to the Greensboro intermodal ramp, which, until recently, was exclusive to UPS,” Decker says. “Coyote put this excess capacity to use and created an intermodal solution that wasn’t previously available.”
Coyote offered similar help to an importer that used to truck high-value freight from PortMiami to a distributor in Alabama. The truckload service was much less expensive than the available intermodal option. But after several on-the-road cargo thefts, the shipper looked for an alternative.
“Miami to Jacksonville happened to be an empty-reposition lane for UPS,” Decker says. “Coyote used that empty intermodal capacity and dedicated a competitive drayage option from Jacksonville to the distributor in Alabama.” The solution cost about the same as OTR and offered tighter cargo security.
Rail Takes Ports Inland
One more force that has made intermodal attractive to shippers in recent years is the development of new inland ports—rail terminals that provide manufacturing plants and distribution centers with easy connections to major seaports.The South Carolina Ports Authority (SCPA) has operated an inland port in Greer since 2013. In March 2017, it broke ground on a second facility, Inland Port Dillon.
Inland Port Greer extends the Port of Charleston’s operations 200 miles into the interior. “Any time you can build infrastructure related to short haul, containerized rail to have overnight train service, that’s a good thing,” says Jim Newsome, SCPA’s president and CEO.
A base of eight to 10 customers close to Greer, plus the presence of a Norfolk Southern (NS) line, encouraged the SCPA to develop Inland Port Greer. One of those key customers was BMW Manufacturing.
“BMW had signaled a willingness to NS to shift their containerized volume to short-haul rail,” Newsome says. “We said, ‘We have some property in Greer, and we’d like to build an inland port.’ That’s how it started.”
BMW’s plant in Spartanburg, South Carolina, next door to Greer, is its largest manufacturing facility in the world. In 2016, it assembled about 411,000 vehicles. The plant imports components from Europe through the Port of Charleston. It also uses Charleston to export car assembly kits—painted bodies and all the necessary components—to Russia, Brazil, Thailand, and other markets where import regulations encourage companies to do final assembly at local plants.
Before the SCPA developed the inland port, BMW used trucks to move containers to and from Charleston.
A few years ago, however, shipment volumes reached a point where intermodal made better economic sense. “BMW was looking to move freight from the road to rail, NS was ready for this business, and the SCPA was ready to expand its business into an inland port,” says Alfred Haas, department manager, material and transportation control at BMW Manufacturing in Spartanburg.
NS moves about 250 containers from the port to Greer for BMW each night. Thoroughbred Direct Intermodal Services, an NS subsidiary, manages BMW’s inventory at the inland port, delivering components to the assembly line as needed. “We give a signal to the inland port, and they pick up the sea container and put it on a chassis,” Haas says. “We have agreed on about a 90-minute window to move the containers to our place and get them unloaded so that parts are being used several hours later on the assembly line.”
Reducing Costs and Footprint
The logistics partner also delivers parts from Spartanburg to a BMW consolidation center, where it loads and delivers sea containers to Inland Port Greer for rail transfer to the Port of Charleston.
Besides saving money, BMW has reduced its carbon footprint by switching from OTR to intermodal. “With 250 trucks moving two ways, we achieved a tremendous reduction in CO2 emissions by bringing those trucks onto the rail,” Haas says.
Facilities at Inland Port Dillon will be similar to those at Inland Port Greer—a set of long concrete pads with lift machines along the mainline rail network. The new port is on the CSX line that runs between Charleston and Rocky Mount. Retailer Harbor Freight Tools will serve as the anchor customer in Dillon, receiving cargo that it imports through the Port of Charleston.
The Dillon region is also home to several exporters, such as companies that produce wood pulp and agricultural products, that could send containers on the rails back to Charleston.
“It’s important to have a reasonably balanced flow of containers,” Newsome says. Too heavy an emphasis on either imports or exports at an inland port can drive up costs, as empty containers need to be relocated.
The inland ports are part of the SCPA’s ongoing strategy to encourage and attract intermodal shipping. “When I joined the port in 2009, we were doing only 12 percent of our volume by intermodal container rail,” Newsome says. “Now we do 22 percent on much higher volume.”
Because the Port of Charleston doesn’t have on-dock rail facilities, it started its own rail drayage program, controlling and coordinating all container movements to and from the railroads. “We made it easier for shipping lines to do rail via our port,” Newsome says. “We’ve grown from about 80,000 rail intermodal containers per year to about 300,000.”
Along with the new Inland Port Dillon, intermodal shippers can look forward to a new facility at the Port of Charleston itself. This is a container transfer facility under construction by the Palmetto Railway, a short-haul line owned by the state of South Carolina. It will be close to the new Hugh K. Leatherman, Sr. container terminal, which the SCPA expects to open in 2019.
“This facility will have a private access road to the intermodal transfer facility,” Newsome says.
Thanks to developments such as the ones in South Carolina, plus the efforts of the railroads, and ongoing concerns about trucking capacity, even more shippers could soon include rail intermodal in their strategies for cost-effective transportation.