On the Road | Morris, Illinois: Plastics, Pellets, and Pallets
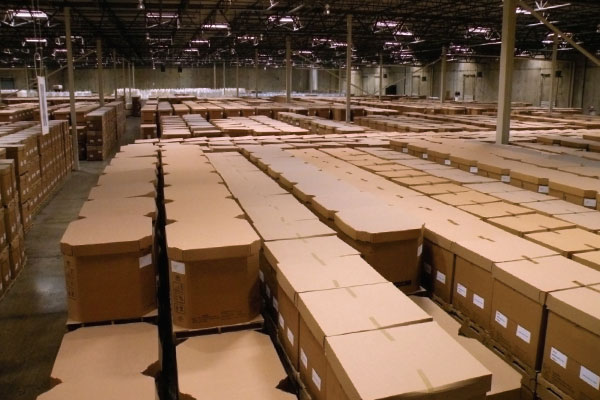
A&R Logistics’ Morris, Ill., dry bulk intermodal facility specializes in hauling plastics. Inbound Logistics Senior Writer Joseph O’Reilly tours the operation.
I had some inside information when I made arrangements with Jeff O’Connor, president of A&R Logistics, to visit its Morris, Illinois terminal—namely from IL publisher, Keith Biondo.
Keith had visited the intermodal facility earlier in the year and was so impressed with the operation that he suggested I include it in this article.
So my motivation was twofold: first, I was curious to see a business and facility so tied to a unique commodity—plastics—and with all the modal pieces in place; second, when the boss makes an unsolicited suggestion, you follow instructions first and ask questions later.
Look around. Within physical or visual reach is likely some type of plastic. You may find a polypropolene blend, for example, in your car’s cup holder or coffee maker’s carafe basket. Polyethylene terephthalate, commonly called PET, is a thermoplastic used in manufacturing bottles.
For all the things that exist in the world, there are as many permutations of plastics, polymers, and resins, in powder, flake, and pellet form. You’ll find as much, and more, in any number of drytainers, hopper cars, trailers, Gaylord boxes, and intermodal containers at A&R Logistics’ Morris, Ill., terminal and headquarters.
As a dry bulk specialist, A&R Logistics earned its stripes hauling plastics. The brainchild of CEO James Bedeker began in 1969 with three trucks, transporting product to and from LyondellBasell’s Equistar petrochemical plant—located within sight of the Morris facility. The carrier eventually began adding assets to the mix—first warehousing, then rail.
Today, A&R Logistics operates three domestic divisions including transport, global, packaging and warehousing, and manages a fleet of 820 tractors, 1,770 dry bulk pneumatic trailers, 10 warehouses, and 23 terminals across the United States.
The company has ventured into other dry bulk business such as grain, soybeans, corn, sugar, olive oil, and slag. It has expanded its value-added resources too, notably in warehousing. But when the light of day illuminates the darkened depths of a dry bulk tank, there’s no doubt. A&R is plastic to the core—down to the very last pellet.
Yard Conversion
A walk around the A&R yard offers an up-close and personal view of the many functions at play in the dry bulk business. Foremost, uniform hopper cars fill the line of sight. Canadian National is the primary rail carrier for A&R’s Morris facility, but CSX serves it as well. The 3PL does yard switching internally with its own locomotive. The bright blue GMTX engine sits idly by.
Railcars represent forward storage locations for A&R. So rail-direct delivery—taking pellets off line and delivering to customers via truck—represents about 90 percent of its business. On any day, the 3PL performs up to 125 rail-to-bulk truck transfers.
Beyond the tracks lie neatly organized colonies of drytainers and ocean intermodal boxes, owned by A&R and used predominantly for storage. To the left, a pair of Laurel and Hardy-like silos, one short and thick, the other towering and skinny, connect to a shed where trucks load grain.
Nearby, a shrinking slag pile with remnants of a much larger footprint, and human ones, too, draws curiosity. The U.S. Navy uses it as sandblasting material for cleaning ships. A&R turns the pile about twice a year.
All around, A&R’s pneumatic bulk tank trailers and flat bed chassis used to transport drytainers are poised and posed in various stages of progress. A few are tilted to load; some are detached and idle; still others are being readied for cleaning.
Vessels moving or storing plastic pellets need to be clean, dry, and odor-free to prevent contamination. A&R staff is vigilant about properly cleaning and inspecting equipment to the point of testing virtually every unit and providing inspection certificates and samples to customers.
Bumper stickers on A&R’s trailers convey as much: “Right Railcar?” “Purge After Loading;” “Check, Check, and Recheck.”
Excessive heat is another area of concern for temperature-sensitive cargo such as plastic pellets. Conveyance creates higher temperatures, which is problematic for a product that has varying melt points. So James Bedeker engineered a solution. On the trailers, air-conditioning units help control temperature variation and expedite the loading and unloading process.
Taking on the Eliminator
But all is not what it seems in the yard. The red intermodal containers stacked inconspicuously in the background hold A&R’s secret weapon—the “Eliminator.”
Simple but effective is the best way to describe the 40-foot ocean containers imbedded with 1,500 cubic feet of aluminum lining—essentially a tank within a box. The invention, also created by Bedeker, does just what its name implies. It eliminates the need for disposable liners, as well as the dwell time of rail cars on track.
“We’re merely changing the address of the inventory,” says Rich Kennedy, yard operations manager, as a Kalmar lift truck places an Eliminator down for inspection. “One rail car has one address—five Eliminators have five addresses.”
With its hatch removed, and a discharge hose hooked up to a hopper car, the vessel has the look of an aluminum heart pumping plastic through the system. Using pneumatic suction, A&R can remove 800 to 1,200 pounds of pellets each minute out of rail cars—which equates to 2.5 hours per unit.
This efficiency and convenience helps the 3PL meet the plastics industry’s stringent demand for just-in-time (JIT) movements, explains Jeff O’Connor, president, A&R Logistics.
“Plants demand compliance because they are very process-driven. There are variables in terms of reliability and delivery to customers. Delivery time, plus or minus 15 minutes, must be exact. Standards are tight,” he adds.
For longtime customers such as LyondellBasell, the Eliminator fits right into their supply chain strategy. A&R manages approximately 75 percent of the Houston-based petrochemical manufacturer’s moves in North America and provides some packaging and warehousing services. It generally ships full rail cars from plants, but many times customers can’t take rail cars or rail car quantities. So the Eliminator system helps LyondellBasell better manage inventory, build loads, and turn equipment.
“We have a hopper car network of around 9,500 units—which is quite large,” observes Nathan Buza, manager of commercial logistics, LyondellBasell. “The faster we turn these cars, the fewer we need, and the less cost we have tied to these assets.”
One hopper car feeds about four bulk truckloads. So instead of waiting for a corollary number of trucks to come in and unload a train unit, the Eliminator allows shippers to re-task assets without lengthy dwell periods. “With the Eliminator, we can turn cars in three or four days versus sometimes as many as 30 days,” adds Buza.
The system also allows A&R and its customers to blend materials for the end user and fully utilize inventory. “For example, after unloading a rail car into bulk trucks, there might still be 1,000 or 2,000 pounds left over,” explains Buza. “How do you manage that heel? Do you send it back to the manufacturer? This can create problems. With the Eliminator, excess inventory is stored, then used to top off other trucks as they come in.”
Big Box Storage
Unlike the red ocean containers stacked in A&R’s yard, there’s no mystery about what’s in the boxes crowding the warehouse. Corrugated Gaylord containers filled with different types of plastics are stacked three and four high—pallets sandwiched between—and feature customer names such as Forest Hill, Equistar, and Flint Hills.
The warehouse floor is spotlessly clean. A box not quite overflowing with floor-swept pellets serves as another reminder. So do the slick spots on the floor. It’s slippery sterile.
Beyond efforts to prevent contamination, “responsible care” is a big part of the plastics supply chain, says Norm Buck, director of customer service and logistics administration, A&R Logistics. “We have trays underneath rail cars to catch over-flow spillage. We also have a responsibility to report any spills. A sweeper frequently circulates the warehouse, and a filter in the drainage catches any plastic pellets before they enter the water system.”
To one side of the facility, paired silos positioned next to a rail siding are vacuum-sucking pellets from a rail car into boxes for packaging. Gaylord containers with bags inside rotate one-by-one along a conveyor belt as they are filled from above. A&R can transfer one train car compartment—a hopper has four—from bulk to box in 1.5 hours.
The soundscape is loud, filled with the hum and whir of the vacuum discharge operation. You can hear the pellets pinging though the industrial hose, and feel the vibration to the touch. Moving away from the packaging operation, layers and rows of cardboard dampen the noise.
The stacks of Gaylord boxes are purposed much like the drytainers and Eliminators outside in the yard. Product is placed in containers and customers have visibility to that inventory. As demand dictates, boxes are moved out by truck. If necessary, shippers can go from bulk to box storage back to bulk for redistribution—but adding touches is not the norm.
Manufacturers often use a blend of plastics in production—materials with different colors, textures, and heat points. Ordering volumes are equally flux. A customer might buy one type of pellet in bulk and order smaller shipments of another. A&R can deliver to customer preference—by rail car, tank truck, TL, LTL, in bags, boxes, and sacks.
The Morris facility is primarily used for regional distribution, serving customers within a 300- to 350-mile radius. But there are exceptions. Near one loading dock where LTL shipments are staged, a skid of shrink-wrapped boxes sits waiting for special delivery to Cologne, Germany. In another corner, imported bags of PET wait to be moved or dumped and consolidated in a hopper car.
A&R uses another part of the warehouse for storage. “Pure warehousing is a value-added service for us,” says Buck. “Moving from one medium to another opened an opportunity and we took it.”
The Sum of its Parts
A&R has grown into a full-service third-party logistics provider with a similar logic and linear progression. James Bedeker built the business by meeting a specific industry need—transporting plastics—then added resources into the mix as customer demand expanded.
Today, the Morris terminal is the convergence of A&R’s business units—logistics, transportation, packaging, and warehousing. The conveyance is the key, as the multitude of railcars and trucks outside the facility demonstrate. These multimodal capabilities allow A&R to explore cargo opportunities beyond simply plastics.
But the less-apparent details stand out. A&R’s innovative Eliminator system and trailer cooling units, and strict attention to cleanliness and safety, are the value-adds that make its transport parts gel. For shippers, finding a solution that meets a specific need is important. But finding a 3PL that can mold assets and services into a unique blend is paramount.
Learning about the plastics industry and seeing A&R Logistics’ business firsthand, I discovered an uncanny similarity between the two.
I suppose you are what you carry.
Plastics can be fixed and malleable, pure or blended. The 3PL’s value proposition shares a similar mix of qualities.
Its fixed assets—trucks, trailers, containers, track, warehouses, and terminals—each serve a specific and commoditized need. With its intermodal accessibility, warehousing footprint, and innovative inventory management tactics, A&R can also help customers blend these resources to unique specifications.
There’s no steadfast way to describe everything A&R can do – except perhaps to say it’s plastic.
Plastic Irony
It’s amazing how a moment’s glance can take your mind spiraling through a supply chain. Seeing sample jars filled with different colors and variations of plastic pellets, powders, and flakes commingling with a bottle of spring water on A&R Logistics’ boardroom table says it all—source to shelf in a split second.
I’m struck again in the warehouse as I watch plastic pellets pour into plastic bags—and raise my plastic pen to put that observation to paper. A mental photograph is worth an immeasurable number of words at A&R’s Morris facility.