Stack, Store & Transport: The Indispensable Pallet
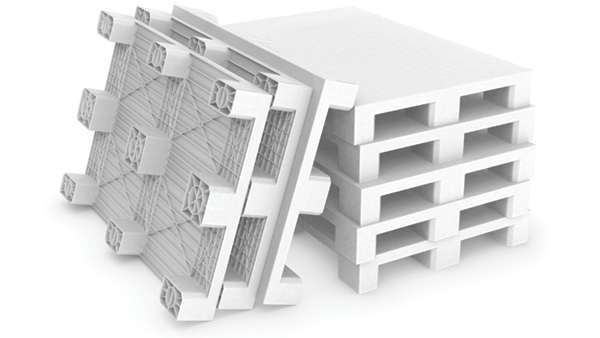
Pallets are a vital piece of warehouse equipment for storing and moving products.
If asked to name their materials handling MVP, many warehouse managers might cite a sophisticated sortation system or pick-to-light solution. Few would think to praise the humble pallet—but just try to run a consumer goods, food and beverage, or other typical supply chain without them.
Pallets are a vital piece of warehouse equipment for storing and moving products. And while they may seem simple, pallets come in a range of shapes, sizes, and materials. In the past, cost was often a primary consideration for businesses choosing pallets. But today, shippers are evaluating additional factors. Pallet type and quality can significantly impact safety, loading and unloading time, and product quality.
Companies that use pallet systems strategically can reduce transport costs and promote supply chain efficiency. Conversely, the wrong pallet choice can translate to distribution and delivery slowdowns. To avoid that problem, businesses need to ensure they choose the type of pallet best suited to their operations.
Material Issues
In some industries, pallet choice depends on the product. For example, the food and beverage, electronics, and pharmaceutical industries often have specific shipping requirements. Pallet type for these products can carry greater importance because of the emphasis on sanitation, consistency, and safety.
Another primary consideration is the pallet material. Wood is the most traditional type of pallet, and the most popular. Less expensive than plastic or aluminum, wood pallets are strong and durable, and handle heavy loads well. The downside is wood pallets can require special heat treatment, fumigation, or fire-retardant applications for certain shipment types or for international transportation.
"Unlike plastic, wood is all-natural, fully repairable, recyclable, and biodegradable," says Adrian Potgieter, senior vice president of sales for Irvington, N.Y.-based PECO Pallet. "PECO’s sturdy wood block pallets are built from high-quality #2 grade Douglas fir and Southern yellow pine lumber sustainably forested in North America."
No chemical treatments or hazardous materials are used on PECO pallets, and all retired materials are recycled into mulch, bark, or livestock bedding. In addition, PECO’s wood block pallets can hold up to 2,800 pounds, can be safely stacked in overhead racks, and don’t slip in refrigerated areas.
Jump Into the Pool Party
Wood block pallets are stronger and more durable than conventional stringer pallets. PECO Pallet maintains a large pool of reusable, four-way, wood block pallets that are leased to manufacturers and retailers throughout North America.
"Renting block pallets can offer a number of advantages over purchasing single-use stringer pallets, such as less hassle managing pallet inventory, fewer distributor rejections, less risk to people and products, and improved environmental sustainability," says Potgieter. "All of these factors can add up to savings."
To maintain quality and reduce customer costs, participants in PECO’s pallet program ship only to authorized distributors who also participate. The distributor or retailer notifies PECO when pallets are ready to be picked up, then a carrier returns the pallets to the depot to be cleaned and inspected, and repaired as needed.
Many big-box retailers such as Costco and Walmart specify that partners participate in a leased-pallet pool. To get their products into these stores, manufacturers and suppliers must use four-way block style pallets.
Offering their own unique advantages, plastic pallets have been gaining in popularity during the past several years.
"Reasons for choosing plastic pallets over wood include reusability, light weight, and recyclability," says Curt Most, global sales manager for Oconomowoc, Wis.-based reusable packaging company ORBIS Corporation. "All the plastic pallets we offer are recyclable. Broken plastic pallets can be ground up and re-used to make new pallets, rather than going to a landfill."
While plastic pallets cost significantly more than their wood counterparts, they offer durability and cost-per-trip advantages.
"When companies choose plastic pallets, it’s no longer a commodity, it’s an investment," says Most. "Instead of renting an $8 wood pallet, they own a $50 plastic pallet. But it will last for several years, as opposed to several trips."
Fantastic Plastic
Plastic pallets also tend to cause fewer warehouse handling injuries, because they are free of splinters and nails. Plastic pallets also offer bar-coding and tracking capabilities via RFID, allowing manufacturers and retailers to follow their pallets anywhere in the supply chain.
ORBIS’s plastic pallets come in three types: nestable, stackable, and rackable. Nestable pallets fit inside each other, condensing the amount of space they require. This type of pallet is often used in distribution applications.
"Grocery stores often choose nestable pallets because they are typically the least expensive, and can take a beating," says Most. "There are no bottom runners to break off, and no bottom base, so they are easy to use in tight spaces."
Nestable pallets can also help reduce transportation costs and gain significantly more space. "A typical truck fits about 500 wood pallets," says Most. "But about 1,200 nestable pallets fit on a truck. That makes a huge cost difference."
Stackable pallets are similar to wood pallets in that they are constructed with a bottom deck. This type of pallet is beneficial for manufacturers who double-stack loaded pallets on top of each other.
Finally, rackable pallets can go into an edge-rack application, where the edge of the pallet sits on steel or fiberglass bars with the product on top and no support underneath. Different models can bear maximum loads of 750 to 3,000 pounds.
Although he extols the virtues of plastic pallets, Most admits wood pallets will always have a place in warehouse operations.
"Wood is a good choice in some circumstances—for food companies shipping products cross-country, for example," he says. "It could be difficult and costly to get that pallet back to its origin."
A company that uses plastic pallets, and has a system for getting them returned easily, can create a closed-loop system. "A grocery store chain, for example, can get products into its DC, divide the shipment, and send it to different stores," Most explains. "The stores will collect the plastic pallets, then ship them back within the same controlled environment."
Automation Nation
Another key factor to consider when choosing a pallet is current and future automation needs. E-commerce growth is driving the need for greater DC efficiency, which automation can help improve—if implemented strategically. Pallet management is an important, but often overlooked, component of that strategy.
Most suggests companies looking into automation take pallets into consideration early on. "Identifying how a new pallet fits into the automation setup is critical," says Most. "Automating a system to specific requirements, then upgrading pallets to meet those specs, may cause a company to incur unwarranted costs.
"It is better when we work with the company and the automation builder to develop a solution that will maximize the return on investment," he adds.
For some companies, pallet choice comes down to the storage and retrieval systems its warehouse uses. Using the wrong pallets could jam warehouse equipment.
"Plastic pallets are extremely consistent in size and shape," says Most. "Because they come out of a mold, they all weigh and look the same."
Maintaining pallet quality is another challenge. PECO Pallet ensures the quality of its entire pallet pool by inspecting all pallets every time they cycle through a depot, using the strictest repair specifications in the industry.
Managing inventory and ensuring there are always enough pallets to meet customer demand—which can fluctuate both seasonally and regionally—can also pose a challenge to pallet providers.
"PECO Pallet has expanded throughout the United States, Canada, and Mexico," says Potgieter. "The company now operates more than 580 strategically located depots, manufacturing sites, and storage locations. PECO’s logistics experts use sophisticated high-tech tools to track pallet flows throughout the network, and ensure we are able to deliver pallets on time."
PECO Pallet strives to consistently deliver high-quality pallets and outstanding customer service. "Shippers can order pallets online for delivery within 72 hours, with no extra sorting required," Potgieter notes. "And PECO’s fixed, all-in-one price per pallet makes budgeting easy, with no surprise charges or hidden fees."
Future Alternatives
The future holds both challenges and opportunities for the pallet industry. For example, pallet manufacturers are using other types of materials, such as aluminum, with good results. PECO is conducting ongoing research and development for both all-plastic and hybrid wood/plastic pallet models.
"Alternative pallet materials and formats continue to generate interest, especially with recent lumber price increases," says Potgieter.
In the future, Potgieter foresees a shift away from the traditional vendor-customer relationship toward more of a partnership model. PECO Pallet already utilizes this approach, sometimes even assigning a PECO representative to work on-site at a customer’s facility. Rather than simply delivering pallets on demand, PECO’s service and operations professionals work closely with both renters and retailers to find innovative ways to reduce costs and improve efficiency throughout the entire supply chain.
"Nothing is worse than seeing a product through from inception to shipment, only to find it damaged or unusable at delivery," says Most. "They may not get a lot of attention, but pallets are a critical logistics element. High-quality pallets are exceptionally engineered and designed products that perform as integral components of the supply chain."
Ultimately, manufacturers must choose the pallet system that works best for their products. Fortunately, they have many options. Taking the time to weigh the pros and cons of the different options can go a long way in making transport and storage processes more efficient.