10 Challenges in Retail Warehousing
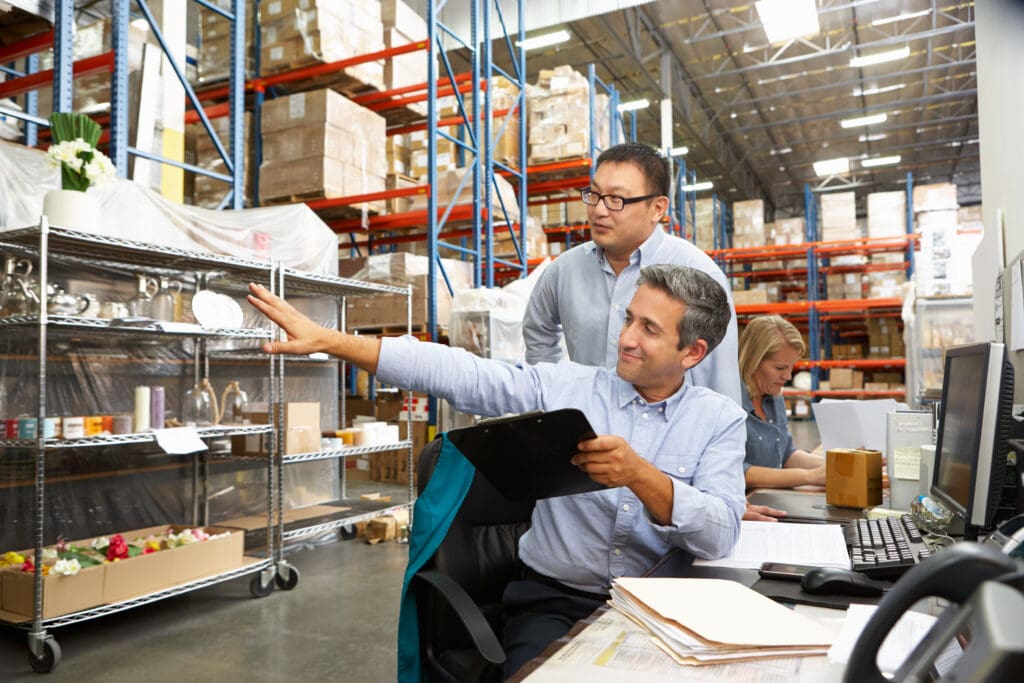
Embracing solutions like automated systems and strategic space utilization are essential steps in overcoming warehouse management challenges and enhancing the performance of retail warehouses.
Today, warehouse managers are grappling with unique issues, primarily driven by external factors such as the recent pandemic, fluctuating customer demands, and widespread labor shortages.
These elements have transformed retail warehousing, highlighting the need for an efficient warehouse management system.
For instance, during the pandemic, many retail warehouses saw a significant shift in operational dynamics. This led to an urgent demand for an enhanced warehouse and robust inventory management system.
These changes have underscored the importance of adaptive warehouse operations. Integrating automated systems in distribution centers is no longer a luxury but a necessity to keep up with the escalating pace of retail warehousing.
10 Critical Warehouse Management Challenges
When navigating retail warehousing, warehouse managers face challenges, each demanding strategic solutions. Understanding and overcoming these challenges is essential for operational success.
We focus on providing actionable insights that help enhance warehouse operations and effectively meet evolving customer demands.
1. Mismanaged Inventory Data and Stock Counts
Accurate inventory management is pivotal in retail warehouses. Mismanaged inventory data and incorrect stock counts can lead to significant issues in warehouse management, affecting everything from supply chain efficiency to customer satisfaction.
For example, inaccurate stock levels can result in overstocking or stockouts, disrupting the retail supply chain. The solution is leveraging advanced warehouse processes that ensure real-time tracking and data accuracy.
Automated systems play a crucial role here, integrating RFID technology or barcode scanning to streamline inventory counts.
This technological integration enhances operational efficiency and minimizes human error, ensuring warehouse managers have accurate data for decision-making.
2. Location, Placement and Floorplan Efficacy
The strategic location and efficient layout of retail warehouses are fundamental for optimizing warehouse processes.
Poor floorplan efficacy can lead to inefficiencies in space utilization, hindering operational efficiency. For instance, a poorly designed warehouse floorplan can result in longer pick times and increased labor costs.
The key to overcoming this challenge is effective warehouse space management, utilizing layout designs that maximize space and facilitate easy movement of goods.
Retail warehouse managers should consider implementing warehouse solutions that provide insights into the best layout practices, including the optimal placement of high-demand items.
Such strategic planning not only improves the flow of warehouse operations but also enhances the overall efficiency of the retail warehouses.
3. Poor Labor Management
Effective labor management is a cornerstone of successful supply chain management. In retail warehouses, poor labor management can lead to decreased productivity, increased operational costs, and lowered morale among staff.
Challenges include understaffing, inefficient task allocation, and lack of proper training. To address these issues, warehouse managers must implement comprehensive labor management strategies.
This involves using warehouse processes for optimal staff scheduling, and balancing labor needs and warehouse demands. Additionally, investing in staff training programs enhances skill levels, improving operational efficiency.
By focusing on efficient labor management, retail warehouses can ensure a more responsive and agile workforce, crucial for meeting the evolving demands of the retail warehouse.
4. Bad Process Implementation and Inventory Management
In retail warehousing, the effectiveness of warehouse operations heavily depends on sound process implementation and robust inventory management.
Poorly implemented processes can lead to operational inefficiencies, causing delays and errors in the supply chain. For example, a lack of standardized procedures for stock replenishment can result in inventory discrepancies.
The solution is to adopt comprehensive warehouse management strategies that streamline processes and support accurate inventory tracking.
Implementing automated systems for inventory control ensures real-time data accuracy, enhancing warehouse management and meeting customer demands more effectively.
5. Insufficient Picking Standards and Quota
Setting and maintaining high picking standards is crucial in retail warehouse management. Insufficient picking standards and quotas can significantly impact the efficiency of warehousing operations.
For instance, low picking accuracy can lead to incorrect orders being shipped, affecting customer satisfaction and the retail stores. To combat this, warehouse managers must establish clear picking protocols and invest in training for staff.
Utilizing advanced warehouse management systems that guide pickers through the most efficient routes and methods can also improve accuracy and speed.
This focus on optimizing picking processes directly contributes to improved operational efficiency in retail warehouses.
6. Inability to Meet Seasonal and Supply Chain Demands
Retail warehouses often face the challenge of adapting to fluctuating seasonal demands and dynamic supply chain requirements.
The inability to scale operations up or down as needed can result in stockouts or overstocking, disrupting retail warehousing. Effective warehouse management involves forecasting demand using historical data and market trends.
Warehouse managers should leverage warehouse management systems for predictive analytics to anticipate and prepare for demand shifts.
Additionally, flexible staffing and scalable storage solutions ensure that retail warehouses can efficiently adapt to changing demands, maintaining operational efficiency throughout varying seasonal peaks.
7. Complicated Product Mix
A complicated product mix poses significant challenges in retail warehouse management. Diverse product ranges require nuanced inventory management and space utilization strategies.
For example, managing a mix of perishable and non-perishable goods demands distinct storage conditions, complicating warehouse operations. The solution involves adopting flexible inventory management software for various inventory types.
These systems aid in optimizing warehouse space and ensuring products are stored under appropriate conditions, thereby maintaining operational efficiency and meeting diverse customer demands in retail warehousing.
8. Lack of Quality Control
Quality control is paramount in maintaining the integrity of the retail warehouse. In retail warehousing, a lack of stringent quality control measures can lead to the distribution of defective or unsuitable products, damaging brand reputation and customer trust.
Implementing rigorous quality checks and adopting warehouse management systems that track product quality throughout the supply chain is essential.
Regular training on quality standards for warehouse staff ensures consistent product quality, enhancing customer satisfaction and reinforcing the efficiency of warehouse operations.
9. Antiquated Software
Using outdated software in retail warehouse management can significantly hinder operational efficiency and supply chain visibility.
Antiquated systems often need more capabilities to handle the complexities of modern warehousing operations, leading to inefficiencies and errors.
Upgrading to modern warehouse management software that offers real-time data, advanced analytics, and integration with other supply chain components is crucial.
These advanced systems streamline warehouse operations, improve inventory management, and enhance overall supply chain efficiency, keeping pace with evolving retail warehouse demands.
10. Mismanagement of Third-Party Opportunities
Effective collaboration with third-party vendors is crucial in optimizing retail warehouse operations. Mismanagement in this area can lead to retail warehousing disruptions and increased operational costs.
For instance, better coordination with third-party logistics providers can result in timely shipments and inventory discrepancies.
To address this, retail warehouses should focus on building strong relationships with reliable partners and use warehouse management systems for seamless integration with third-party services.
This ensures better coordination, timely deliveries, and enhanced supply chain efficiency, ultimately benefiting the overall performance of retail warehouses.
Warehouse Management Challenges and Fleet
An efficient fleet can significantly disrupt supply chains, leading to delayed deliveries and customer satisfaction.
This inefficiency often stems from outdated vehicles, poor route planning, or mismanagement of fleet resources, impacting retail warehousing operations.
Implementing third-party logistics (3PL) services can be a strategic solution. 3PL providers offer specialized fleet management, leveraging advanced technology for route optimization and timely deliveries.
Third-party logistics (3PL)
Third-party logistics (3PL) refers to outsourcing logistics and supply chain tasks to specialized companies. Services include transportation, warehousing, and order fulfillment.
3PLs help businesses scale operations and efficiently save costs, allowing them to focus on core activities and improving overall operational efficiency in retail warehousing.
Warehouse Management and Automation
The integration of automation in warehouse management brings transformative impacts. Automated systems, such as robotic picking or automated storage and retrieval systems (AS/RS), greatly enhance operational efficiency and accuracy in retail warehouses.
These technologies streamline warehousing operations, reduce manual labor, and minimize errors, leading to more efficient inventory management and faster fulfillment of customer demands.
However, automation also presents challenges, including high initial investment costs and the need for skilled staff to manage and maintain these systems.
Despite these drawbacks, the benefits of improved speed, accuracy, and efficiency in warehouse operations make automation a compelling choice in a modern warehouse management system.
Frequently Asked Questions
What are the challenges in warehousing?
Warehousing challenges include inventory management, maintaining operational efficiency, optimizing warehouse space, and adapting to evolving customer demands and supply chain dynamics.
What’s the #1 challenge warehouse managers face?
One of the primary or common warehouse management challenges is ensuring efficient warehouse management and balancing cost, speed, and accuracy in retail warehouses.
What is the role of warehousing in retailing?
Warehousing plays a crucial role in retailing by storing goods, managing inventory, and ensuring timely distribution to meet customer demands in the retail warehouse.
How can technology improve warehousing operations?
Technology like Warehouse Management Systems and automation tools can greatly improve efficiency by optimizing inventory tracking, reducing errors, and speeding up processes.
Warehouse Management Challenges Resolved
Addressing these challenges in retail warehousing is key to ensuring a seamless and efficient retail supply chain.
By focusing on effective warehouse management, optimizing warehouse processes, and leveraging warehouse management software, warehouse managers can meet customer demands while maintaining operational efficiency.
Embracing solutions like automated systems and strategic space utilization are essential steps in overcoming warehouse management challenges and enhancing the performance of retail warehouses.