Alternative Routing: Go Another Way
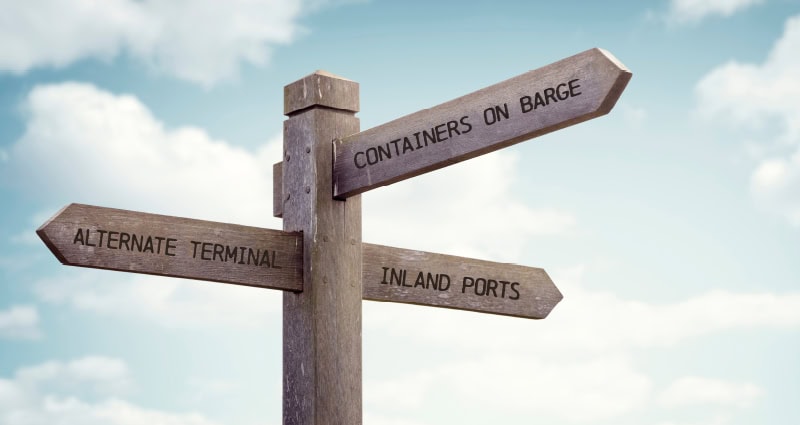
In the face of constant supply chain disruptions and unexpected events, shippers must be ready to reroute at a moment’s notice. Finding the road—or waterway— less traveled can sometimes make all the difference for transportation success.
Disruption from Hurricane Beryl, which ravaged parts of Texas in mid-July 2024, was one of the latest events forcing shippers and carriers to consider alternative routes for getting products to their final destinations. The storm knocked out power for more than 2.5 million homes in Texas and flooded roadways caused major transportation delays for regional shippers.
The supply chain has been hammered by recent weather events like this—plus everything from geopolitical issues to port shutdowns to congestion pricing—all compelling shippers to look at different ways of moving freight.
Supply chain resiliency is the common buzzword for being prepared to react to disruptions, but how do companies put that into practice?
One way is to develop alternative routes or a backup to standard transportation plans. While an alternative route includes basic steps like steering a load to a different highway or port, there’s more to it. Seeking an alternative route may also encourage a different way of operating that can transform supply chain strategies.
Diversify and Be Flexible
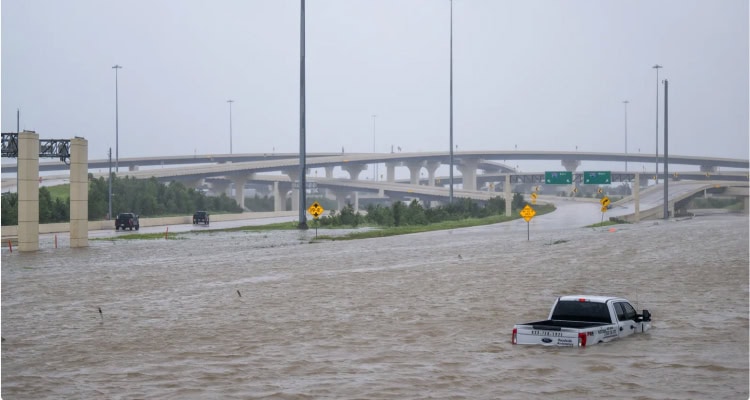
Hurricane Beryl flooded highways in Texas, forcing shippers to consider alternative routes. These types of disruptions compel shippers to examine new strategies for moving freight.
During and after the pandemic, freight shifted from West Coast ports to East Coast ports as carriers and shippers searched for a way to bypass congestion. While that trend has reversed to some extent, it’s still a common tactic for those seeking alternative routes.
More recently, with ocean lane disruptions in the Suez Canal and the Port of Baltimore, flexibility in routing has been critical.
“Diversification of routes helps build resiliency,” says Larry Mason, vice president of operations for Averitt, a large regional carrier. “You can’t change your plan the day something happens with nothing to fall back on.”
Complacency can be a barrier to rethinking your strategy.
For instance, despite chronic problems at West Coast ports, many shippers are still reluctant to consider alternative destinations, notes Bryn Heimbeck, co-founder and president of Trade Tech, a global logistics platform.
“I ask companies why they don’t consider sending shipments through Seattle or straight into Chicago, and they come up with 1,000 reasons,” he says. “Transportation managers have to be open to reasonably viable alternative routes.”
As trans-Pacific container volumes continue to recover to the point where congestion at West Coast ports may return, it’s a signal to consider alternative routing once again.
“It’s time for shippers to ask, ‘How can we transport loads to Chicago without going through Los Angeles?’” Heimbeck says. “They have to be ready to push the Seattle button instead of the L.A. button.”
Technology Offers Alternatives
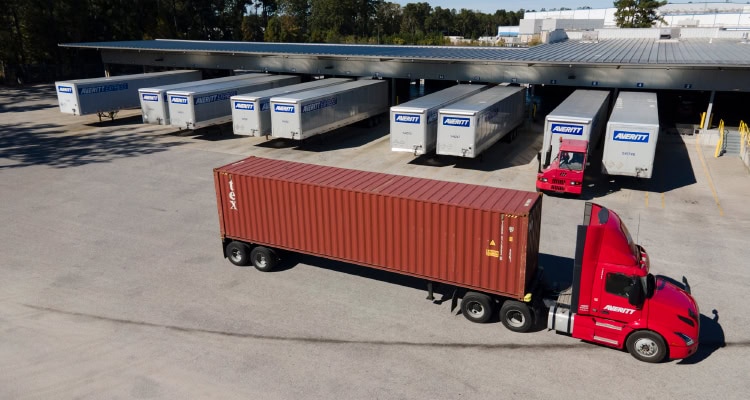
Averitt uses AI-enhanced decision-making technology to help shippers make rapid, network-wide adjustments and select alternative options in response to disruptive events.
Technology is becoming a reliable tool to uncover alternative routes and practices.
Tactical solutions such as load and route optimization help carriers operate more efficiently, while AI-enhanced decision-making can speed up reaction time to external events like weather and economic disruptions.
“In the past, it would take 24 to 48 hours to make adjustments in response to a disruptive event. Now, we can do it on the fly,” says Mason. “We use these technological resources to react immediately and change plans in a split second.”
If a hurricane hits South Florida, for example, Averitt uses tools that implement a network plan to revise operations not only in Florida but also in adjacent affected states.
“That way, the terminals in Atlanta or Nashville don’t become overloaded,” Mason says.
Rerouting With Automation
The company can make similar adjustments and find alternative routes in the case of road closures. Previously, if a portion of a major highway were to shut down, Averitt employees would respond by making a variety of phone calls and coordinating manual route adjustments.
Today, thanks to technology, managers can indicate that the highway is closed at a particular mile marker, and the system works through the network to make adjustments, reroute trucks, and alert terminals along the impacted path.
The ability to make such rapid network-wide adjustments helps Averitt respond to customers hit by last-minute disruptions, too. When their regular carrier went on strike, one shipper called to see if Averitt could handle 400 extra loads to Chicago.
“We rely on the technology to sift through all the data in the system and tell us how to handle each situation,” Mason says. “The technology won’t give us the resources to move those loads, but it does give us the planning ability to adjust to that particular network or area of the country.”
With load planning technology, alternative options arise at the granular level of individual crates and pallets, enabling users to analyze shipment weight and dimensions to stack as much merchandise into trailers as possible without causing damage or reaching overweight status. Using load planning tools, companies can group products on the right truck to ensure the most efficient delivery route.
Averitt also uses the latest routing technology to optimize urban logistics by routing around traffic tie-ups and short-term road closures to ensure drivers stay on schedule in busy cities.
“These tools can change everything in a fraction of a second,” Mason says.
Similar tech is available for last-mile parcel delivery, enabling drivers to adjust pickup and delivery windows on the go in order to avoid disruptions.
Software firm ORTEC’s last-mile delivery solution, for example, considers inputs such as traffic patterns, delivery windows, vehicle capacities, and real-time updates to dynamically adjust routes to minimize delivery time and cost while maximizing labor and fuel efficiency.
With these kinds of solutions, shippers can offer real-time visibility and tracking capabilities to monitor delivery status and provide customers with accurate ETAs.
“Improved visibility for last-mile delivery service is vital for customers who want real-time updates and accurate delivery time windows,” says Jeff Bailey, CEO of ORTEC Americas. “Companies that still rely on outdated systems for route planning, order management, and communication are falling behind in efficiency and customer trust.”
On the ocean shipping side, the days of memorizing paper sailing schedules are long gone. Instead, optimization tools analyze data for possible alternative routes and pricing, and present the best options based on speed or price.
“Humans are great thinkers, but machines have a better memory by a longshot, so we balance the strengths of one versus the other to weigh the options,” Heimbeck says. “A machine can tell you what’s available, but the human has to make the decisions.”
Inland Waterways for the Win
One increasingly attractive alternative transportation strategy is to move containers on barges along inland waterways.
The Port of New Orleans, for example, is home to one of the most successful container-on-barge (COB) operations in the country; it logged more than 20,000 container moves in 2023.
On average, the service—operated by Ingram Marine Group—moves 30,000 TEUs per year between New Orleans and the Port of Greater Baton Rouge, as well as ports in Memphis and St. Louis, according to Ronald Wendel, acting president and CEO, Port of New Orleans.
Plastic resin manufacturers clustered around Baton Rouge are the primary users of the service. Outbound containers are loaded on container ships for export, and empties are returned in bulk instead of one at a time. For these companies, moving containers this way not only provides an alternative transport route, but also reduces costs and greenhouse gas emissions.
COB Gets a Boost
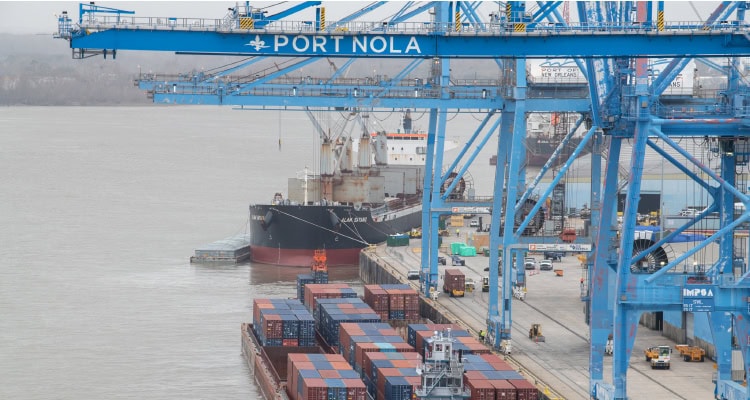
Container-on-barge (COB) services are gaining traction as a popular alternative. The Port of New Orleans moves 30,000 TEUs each year via COB service and is upgrading its capabilities.
New Orleans is well situated to expand its container-on-barge services thanks to its location at the mouth of the Mississippi River and connections to six Class I railroads. A new $1.8-billion terminal, which includes container-on-barge provisions, is under construction at Port of New Orleans.
The COB service will also get a boost thanks to a bridge project taking place over the next several years on I-10 between Baton Rouge and New Orleans. “Getting trucks off the road will benefit traffic and environmental issues, and we can keep the COB momentum going,” Wendel says.
Transit time is a concern for shippers, however. Moving a container from New Orleans to St. Louis on a barge takes six to eight days, while a container can reach Chicago in 24 hours by rail.
“There needs to be a critical mass of volume for COB to be a true multimodal solution,” Wendel says.
Ingram also offers similar COB services through the Port of Mobile, moving 36 loaded and 48 empty containers on each barge. Containers can travel from there to cities in Alabama, Indiana, Kentucky, Mississippi, Missouri, Ohio, and Tennessee.
On the James River in Virginia, a tug-barge container service operates between Richmond and Norfolk, taking more than 120,000 trucks off of I-64 each year and providing area shippers with an effective alternative transportation option.
Other inland ports also offer alternative routing around congested terminals and highways. The new Port of Nevada, for instance, alleviates shipping delays along I-80, flowing containers from the Port of Oakland into northern Nevada via intermodal. The rail service bypasses traffic in the Bay area, and saves shippers from worrying about potential road closures due to construction along the heavily traveled route as well as weather delays through mountainous areas.
Cross-Border Connections
Another group of shippers keen to include alternative routes in their transportation plans are companies starting or increasing their nearshoring operations in Mexico.
Trucking and intermodal services offer multiple options for cross-border moves. Averitt is building capacity for transloading trucks at its service centers at the border to move product more efficiently to the U.S. interior. An Averitt warehouse in San Antonio draws traffic from congestion in El Paso and Laredo, two of the most active border crossings.
PortMiami is one U.S. East Coast port working to increase container capacity from Mexico to help shippers bypass congested Texas border towns. The water route can save $2,000 per container and takes three days less than the highway option, according to PortMiami officials.
Additionally, Mexico has planned a $2.8-billion project to transform the Isthmus of Tehuantepec into a 188-mile rail corridor between the Gulf of Mexico and the Pacific Ocean. The isthmus represents the shortest distance between the two bodies of water, and the plan’s goal is to divert traffic from the drought-plagued Panama Canal.
Organizers predict the corridor could handle up to 1.4 million TEUs per year by 2033. In comparison, the 50-mile-long Panama Canal handles about 14,000 vessels and 8 million TEUs each year.
The corridor could draw freight from vessels that use the canal and provide an alternative when events disrupt trade flows.
Collaborating for Solutions
Improving supply chain resilience by evaluating alternative routing should be an ongoing process. Forward-thinking shippers, carriers, ports, and regional planners are working on strategic approaches to make it easier for alternative routes to be an effective component of the global supply chain.
Automotive Innovation
Stress on the global roll-on/roll off (RoRo) fleet and a shortage of multi-level rail car capacity has many automotive shippers looking for alternative solutions. Global forwarder D.P. World has developed a new technology that can help alleviate some of these concerns by shipping a greater volume of finished vehicles in fewer containers.
Traditional 40-foot containers typically hold three vehicles at most. D.P. World designed a new “cars in containers” program for 53-foot containers that can hold up to five cars. The multi-level intermodal containers transport autos from assembly plants in Mexico via rail to destinations such as Los Angeles, Chicago, Detroit, and Toronto.
Transitioning vehicles to containers can help alleviate the capacity shortage, although the per-unit price is higher for containers compared to more traditional modes of moving automobiles, says Christoph Seitz, global vice president, finished vehicles for D.P. World.
“We anticipate the 53-foot solution will enable an additional 30,000 vehicles to be moved between Mexico and the United States/Canada, at a time when RoRo and multi-level railcar capacity is constrained,” he says.