Chemical Logistics: Delivering Solutions for a Complex Industry
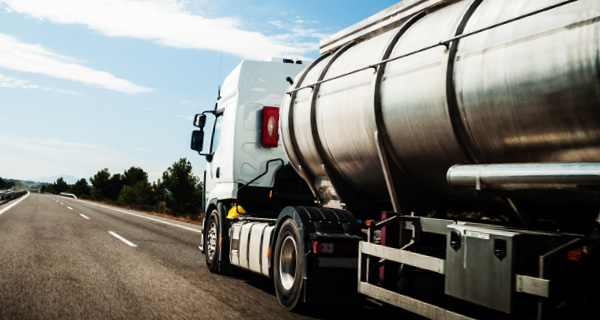
Chemical manufacturers—and the third-party logistics partners that serve them—tackle enormous challenges to keep the $770-billion industry moving.
From Tupperware to paint, shampoo to lawn care products, even food, chemicals are part of nearly every product lining home and office shelves. In their raw state, the chemicals used to make these everyday products include such diverse materials as corrosives, acids, pesticides, and plastic pellets.
The chemical supply chain comprises these and myriad other products, many of which require special care in handling, transporting, and storing to prevent safety hazards such as combustion, contamination, and spoilage.
The manufacturers, carriers, and third-party logistics (3PL) providers who store and transport these products must adhere to a complex web of ever-changing federal and state regulations aimed at minimizing the hazards for workers and the general public who might be affected if an accident occurs.
Because it is a high-risk business, chemical logistics requires flexibility and adaptability. “The chemical supply chain is long, volatile, and highly complex,” says Nathan Buelt, manager of chemical solutions for ChemSolutions, a subsidiary of C.H. Robinson, an Eden Prairie, Minn.-based 3PL. “There are numerous inputs, and many touches to the end consumer.”
The array of safety considerations and regulatory follow-through needed to store and transport chemicals makes outsourcing a popular choice for this sector.
“Chemical companies are adept at designing their products and manufacturing safely, while logistics companies offer the expertise required to safely navigate transporting and storing these potentially dangerous products,” says Glenn Riggs, senior vice president, North America logistics for Danbury, Conn.-based Odyssey Logistics and Technology, an asset-light company specializing in information and management.
Promoting Core Competencies
3PL providers offer chemical shippers a mix of services ranging from non-asset-based logistics management—which involves helping shippers find the best carriers and managing loads—to operating truck fleets and warehouses.
Keeping all parties focused on what they do best lies at the heart of chemical logistics outsourcing. “A manufacturer’s core competency is creating and manufacturing product,'” says Sean Strane, vice president for contract logistics services for Jacobson Companies, a Des Moines, Iowa-based 3PL. “A warehousing provider’s core competency is to effectively store, handle, and ship the manufacturer’s product.
“Outsourcing puts the responsibility for recruiting, training, and retaining employees on the logistics provider,” Strane adds. This eases the burden for manufacturers.
Chemical shippers who outsource logistics entrust their 3PL to stay on top of emerging issues that could potentially affect transportation operations, such as new driver regulations, and mitigate ongoing challenges, such as capacity shortages. 3PLs have proprietary processes to prevent improperly storing chemicals, and they screen thousands of carriers to ensure they hire only the best—those with the specific expertise in handling chemical emergencies and adhering to applicable regulations.
A Formula for Savings
Companies may also find it less expensive to outsource, particularly warehousing operations. “If all companies we serve operated their own warehouses, they would have much higher fixed costs,” says Jim Emmerling, senior vice president of business development at Weber Logistics, a Santa Fe Springs, Calif.-based 3PL specializing in serving the western United States.
“Most of our customers arrange transactional pricing,” Emmerling says. “Their costs can vary with the activity levels they are experiencing. When sales are up, transactions are up, and the amount they pay us is likely up. But it’s in scale to their increased revenues. If their revenues go down, their transactions and costs go down.”
Without outsourcing, however, those companies would face fixed warehousing costs that don’t fluctuate in accordance with profits.
“Warehousing infrastructure is expensive to maintain for many reasons,” explains Michael Waring, vice president of operations and customer development at Ontario, Calif.-based Pacific Coast Warehouse Company, a 3PL that operates its own facilities. “Safety and security, regulatory compliance, and structural requirements, such as in-racking sprinklers, all add costs.”
Outsourcing helps shippers navigate challenges such as short lead times, frequent change orders, and high variability, says Tracy Meetre, vice president of supply chain solutions for Logistics Management Solutions (LMS), a St. Louis-based non-asset 3PL. LMS specializes in working with shippers that maintain complex distribution networks—particularly those that transport products using multiple modes and need help consolidating freight or identifying other opportunities to make transportation more efficient.
Capacity Crunch
For small and large chemical shippers alike, outsourcing logistics helps manage challenges and identify new opportunities. Manufacturers and logistics professionals in all industries are grappling with capacity issues affecting the supply chain.
Tight capacity has left some shippers with too few transportation and warehousing options for processing the volume of product pouring into the market. These capacity issues are of particular concern for the $770-billion chemical industry, which is projected to grow four percent in 2014, according to Chemical Week.
Adding pressure to the constraints is a burgeoning natural gas industry—shale oil produced through hydraulic fracturing, also known as fracking. The growing sector is absorbing capacity, overloading an infrastructure still catching up from a recession-induced pause. Throw into the mix increasing government regulations, and you get a sense of the challenges facing chemical shippers.
Consider driver capacity issues. High turnover industry-wide, and an aging workforce, have reduced the number of truckers on the road. The average age of truckers is 47, according to the Bureau of Labor Statistics, and not enough new drivers are entering the industry to replace those who are retiring.
Meanwhile, truck driver turnover hovered above 90 percent in the fourth quarter of 2013, although 2012 and 2013 saw rates as high as 98 percent, according to the American Trucking Associations. Turnover exposes the supply chain to risk, which 3PL providers must work to mitigate—particularly in chemical logistics, which requires specialized drivers.
“Companies don’t hire average drivers for chemical operations—they require a higher grade,” says Jim Barnett, vice president of operations for Lafayette, La.-based Dupré Logistics, an asset-based logistics provider.
Chemical shipment drivers are more experienced and skilled, and must pass rigorous background checks, undergo federally certified training, and complete in-house training with the company they work for. Not all drivers meet these high standards, leaving the chemical vertical with a very small slice of a dwindling pie of available drivers.
Despite industry-wide turnover, carriers and 3PLs work to minimize churn. “Recruiting and training new drivers is expensive,” says Earnie Seibert, vice president of sales and marketing for Dupré. “3PLs and carriers have to ensure employees are up to speed on proper procedures.”
Meanwhile, drivers are able to cherry-pick the types of work they want to do. “Many drivers would choose to haul a less-dangerous product than chemicals,” Seibert says. “Employers must provide incentives for dealing with this complex, difficult environment.”
The Hours-of-Service Impact
Additional regulations coming down the line could shrink the number of available drivers even further. A big change came in 2013 when the Federal Motor Carrier Safety Administration (FMCSA) issued Hours-of-Service (HOS) regulations limiting the number of hours a driver can spend behind the wheel.
The rules cap driving time to 11 hours, and work days to 14 hours. The Department of Transportation (DOT) says the changes impact only the most extreme schedules—about 15 percent of all drivers.
Mike Hogan, vice president of sales and marketing at Elgin, Ill.-based transportation and warehousing provider A&R Logistics, says the HOS rules resulted in a six-percent productivity drop at A&R, although the 3PL’s safety rating increased. “In theory, we have to hire six to 10 percent more drivers,” he says.
For many carriers, the HOS rules have both positive and negative aspects. “We support the new limits because they promote safety on the roads,” Meetre says. “But they also affect our ability to recruit drivers, some of whom view the rules as the government’s attempt to limit their ability to make money.”
The federal rules could also lead to new technology—electronic logging devices (ELD)—being installed in trucks. The logs track hours for each driver, monitoring time behind the wheel and at rest to ensure compliance with the HOS rules. Historically, those hours have been recorded in a logbook, but that method is being left behind as some companies, including A&R Transport, adopt the new technology.
ELDs: Intrusive or Efficient?
A new sweeping federal transportation bill, Moving Ahead for Progress in the 21st Century, could mandate the use of ELDs. This possibility generates mixed reactions from drivers.
“Some drivers who were drawn to the field because it allows them to be independent view ELDs as intrusive,” Riggs says. “Other drivers appreciate that they no longer have to deal with the hassle of keeping a paper log.”
While driver shortage issues impact all logistics operations, other regulations directly affect chemical shipments. In 2011, FMCSA passed new rules that changed the definition of a tank vehicle to include intermediate bulk containers, also known as totes, which are used to transport chemicals.
The change requires drivers to apply for tank vehicle endorsements. Originally, states had until July 2014 to comply with the new rule; however, the FMCSA extended the deadline until 2015.
Some states have already implemented the new rules, which has led to inconsistent enforcement. Although the idea behind the regulation—ensuring drivers have appropriate endorsements to promote safety—is sound, the uncertainty of the new regulation’s timing and impact is hurting the industry, C.H. Robinson’s Buelt says.
“The cost of the endorsement is not the issue—it’s the time required to obtain it,” Buelt says. “The endorsement may not add significant value for carriers if they can’t charge a premium for a certified driver.
“Increased regulation will further tighten the market,” he adds.
Working Within Limitations
Shippers will feel the effects of the driver shortage in other ways. “As regulations tighten, the driver pool decreases, resulting in less storage capacity and delayed shipments to end customers,” explains Sean O’Laughlin, director of warehouse operations for Jacobson Companies.
Waring agrees. “The cost of transporting chemical goods is rising because there aren’t as many qualified DOT/hazmat-compliant transportation companies or drivers.”
The tight environment has prompted Dupré to develop stronger partnerships with carriers and its own drivers. “Qualified employees and transportation companies are becoming scarce,” Seibert notes. “More chemical shippers are considering longer-term logistics partnerships, and more creative ways to operate differently.”
Instead of working with carriers and drivers in a transactional relationship, Seibert says developing partnerships, and focusing on creating good working conditions, can help chemical shippers secure capacity in today’s tight market.
“Shippers are learning that providing dedicated business attracts more drivers,” Barnett says. “The dedicated environment allows us to recruit more effectively.”
Other ways of creating a good work environment include offering hourly wages as opposed to mile- or load-based pay, and incentives based on productivity.
The driver shortage has led some carriers to reexamine scheduling. “All customers want their load delivered Monday morning,” says Hogan. “That’s physically impossible.”
A&R Logistics works with chemical shippers to expand their delivery windows, so instead of expecting deliveries at 7 a.m. each day, shipments might be received later in the day, or even at night.
Even if a company has enough drivers to meet demand, it might not have enough trucks. Chemical shipments often require specialized equipment, and availability can be an issue.
The large investment required to put more trucks on the road—around $250,000 for a tractor-trailer—means businesses will need to make serious investments before the capacity issues abate.
Transportation isn’t the only link in the supply chain under strain. Warehouse space suitable for storing chemical products is also at a premium.
“I attribute the tight capacity to three causes,” says Rob Kriewaldt, director of client solutions for WSI, an Appleton, Wisc.-based logistics provider. “First, construction virtually stopped in 2008 because of the recession. It is just now starting to pick up, but investors are still cautious.” Recently, industrial real estate absorption has been occurring at two to three times the rate of construction nationally.
Second, regional U.S. economic growth is creating scarcity in certain areas. For example, the booming Houston energy market is consuming capacity there, with industrial real estate being used to store products made from oil and natural gas, or other inputs associated with the process. Despite limited local warehouse availability, the demand is higher than ever, creating an industrial vacancy rate of about five percent. Demand is finally driving a large amount of new construction in this market, but space will remain tight for some time.
“Finally, abundant energy has fueled a huge resurgence in manufacturing in the United States, especially in the Midwest,” Kriewaldt says. Products such as industrial machinery, iron castings, and car parts are consuming warehouse space, putting capacity at a premium. Increasing numbers of new chemical plants are taking advantage of affordable energy.
“For the first time in years, manufacturers are growing their domestic production volumes and reducing imports,” says Rick McIlveen, vice president of business development for Jacobson Companies. “This is creating a need for more warehouse space, and the supply of ready-to-use buildings is tight—especially buildings already retrofitted to store chemicals. Lease rates and term requirements are starting to climb.
“Warehouse capacity shortages are caused, in part, by developers’ reluctance to build on speculation of future need, and, in some cases, an inability to secure financing,” McIlveen adds.
Feeling the Pinch
In areas such as Houston, on the edge of South Texas’ Eagle Ford Shale, petrochemical has tapped out available space. But Los Angeles and other commerce centers are also feeling the pinch. “The Los Angeles warehousing market is very tight,” Kriewaldt says. “New construction hasn’t caught up with demand yet.”
When the economy first started to rebound, construction was delayed until available space was absorbed. In robust economies such as Houston, real estate developers were taken by surprise when the energy market quickly surged. New buildings take 18 to 24 months to complete, and the lag time has made warehouse space difficult to find.
In Houston, for example, less than three million square feet are under construction in a market that has more than one billion square feet already occupied. Nationally, warehouse availability is approaching 10 percent, down from a peak of more than 14 percent at the height of the recession.
“Accommodating growth is our major challenge right now,” Waring says. “The demand exists, but finding facilities suitable for storing chemical products is difficult, because many facilities must be retrofitted or custom-built to handle chemical goods.”
Warehouse capacity in the chemical industry is even more complex than in other industries. “Available buildings that have all the appropriate hazard classifications are rare,” says John Rantz, a distribution center manager for Weber. “It is even harder to do a complete startup of a chemical facility in California, because it is difficult to get the necessary permits. And if you locate an existing facility with enough space, completing all the required modifications is expensive.”
Energy Boom Fuels Growth
One factor that has greatly impacted the chemical supply chain in recent years is the shale oil market. Since 2010, more than $100 billion in U.S. shale-related chemical manufacturing investment has been planned, according to the American Chemistry Council (ACC).
Much of this investment lies along the Gulf Coast, with South Texas’ Eagle Ford Shale region projected to yield more than seven million cubic feet of gas per day in July 2014, according to the U.S. Energy Information Administration (EIA). By 2040, shale gas will account for 50 percent of domestic natural gas production, EIA predicts.
“Shale gas is a game changer for the chemistry industry,” reported the ACC in a written statement to the U.S. Senate Committee on Commerce, Science, and Transportation. “It holds the promise of a renaissance of chemical manufacturing in the United States, and will dramatically improve our competitiveness globally.”
Although it may help promote U.S. economic growth, the boon is a significant factor in constricting transportation capacity, with shale oil and fracking materials consuming space in rail cars and tank trucks, as well as attracting drivers.
“Transportation capacity is the biggest issue currently impacting chemical logistics,” says Mike Skinner, vice president of ChemLogix, a Blue Bell, Pa.-based 3PL. “Rail car capacity is being consumed by materials going in and coming out of the expanding fracking industry.”
Shale product that can’t fit on the rails moves on bulk tank trucks. Space is limited, however, because bulk trucks are also being used to move products related to fracking. Increased output due to lower energy prices, combined with equipment and driver shortages, has resulted in a difficult squeeze.
The rebounding U.S. economy and growing petrochemical market are forcing chemical shippers and logistics providers to get creative, says Kriewaldt. During the recession, companies stopped building rail cars because of a lack of demand for additional capacity.
As the economy picked up, manufacturing resumed. The long lead time for rail cars, however, makes it difficult to keep pace with demand, especially for the specialty equipment needed to ship chemicals. As a result, transportation costs are rising.
“In 2009, you could lease a tanker car to haul petrochemical products for $500 per month,” Kriewaldt says. “In May 2014, prices hovered around $2,400 per month to lease a car. That’s a good indication of rail car demand.”
The higher prices are not only inflating costs overall, but also pushing companies to turn cars around faster. The amount of time it takes to unload a car and return it to the plant isn’t fixed, so companies are focusing on what they can change.
“It comes down to working extra hours and shifts,” Kriewaldt says. “Companies have extended their receiving hours to expand capacity without an increased number of tanks.”
A locomotive shortage is also a factor. The railroads have been using the power units to move petroleum, rather than grain and fertilizer, to the detriment of U.S. and Canadian farmers.
Regulations for Rail
Because shale production growth is relatively new, state and federal regulations are still taking shape—particularly related to transportation, in the aftermath of several high-profile accidents.
In 2013, a train carrying tank cars full of oil from North Dakota’s Bakken Oil Field derailed in Quebec and exploded. After the crash, Canada announced orders to phase out or retrofit older rail cars classified as DOT-111—a type that is particularly vulnerable to damage during a crash—by 2017.
“The accidents prompted a review of existing rail car infrastructure,” Riggs says.
While a boon to safety, phasing out older cars will strain capacity even more.
While big changes in rail transportation of oil and natural gas may be coming, overall usage of rail combined with trucks is on the rise.
Intermodal Leads the Way
Improved infrastructure has boosted the use of intermodal in chemical logistics, with the mix of rail and truck reducing carbon footprints and easing capacity issues.
“Intermodal transport is growing in popularity,” Riggs says. “It reduces the number of trucks on the highway, and it’s greener.”
With nearly 25 million containers moved annually, intermodal’s growth rates outpace those of all other transportation modes, according to the Intermodal Association of North America. Domestic intermodal container volume has doubled in the past 10 years.
Although infrastructure has improved, speed is still a factor for companies opting to combine transportation modes. “Intermodal generally takes longer, so transit times are an important service factor,” Riggs says. “Some operations can’t accept adding an extra day or two to their schedule.”
If companies can afford the extra time, however, using rail for a portion of the journey can reduce shipping costs from 15 to 40 percent, according to a Weber Logistics whitepaper.
Safe and Secure From Start to End
Complex safety needs impact every facet of chemical warehouses, from design to operation. When shipments arrive at the warehouse, workers verify each product’s stockkeeping unit number, then confirm that the correct hazards are listed.
Each chemical carries unique storage requirements, so safety protocols and conditions vary from product to product. For example, some chemicals must be stored in temperature-controlled rooms, while others shouldn’t be stored next to one another because the vapors can interact and cause problems such as harmful fumes.
“We review every potential chemical customer’s safety data sheet to ensure the hazards indicated are suitable for our systems and facility,” Weber’s Emmerling says.
Weber’s 220,000-square-foot Southern California chemical warehouse facility includes 13 storage rooms with temperatures ranging from 45 to 90 degrees. Maintaining the proper temperature is critical. “If temperature control is breached, the product may be compromised,” Emmerling says.
To mitigate risk from spills, the rooms are cordoned off by ramps that act as dikes to contain spills or water used in fighting a fire. In-rack sprinkler systems also help to quickly diffuse any incidents.
Pacific Coast Warehouse Company’s 75,000-square-foot Chino, Calif., facility stores chemicals including flammables, poisons, and aerosols, among others. The rooms are separated by several automatic closing fire-rated doors, and floor-to-ceiling aerosol cages. All staff, including janitors, customer service representatives, and managers undergo routine training sessions. In addition to the training, flowcharts located throughout the warehouse spell out the protocol to follow if a spill occurs.
Chemical warehouses also use special equipment, including EE-rated forklifts, which are spark-proof to protect against fire. “All of the electronic components are housed separately,” Waring explains.
Authorized Personnel Only
Tracking who has access to the facility represents an important component of product safety. “Check-in and check-out procedures are in place,” Waring says. “When a driver arrives for a pickup or delivery, we use an identification verification process to authenticate the purchase orders or delivery numbers.” Warehouse staff also check driver identification before they load or unload product onto the trailer.
Safety precautions continue on the road. Trucks must be labeled accurately with the type of chemical being transported, and the level of hazard associated with it. “If an accident occurs, drivers need to know what they are dealing with—for example, whether there is a safety issue if, say, a gallon of material escapes,” says Riggs. “The labeling is critical.”
To demonstrate their commitment to safely storing and transporting chemicals, many 3PLs have joined the Responsible Care initiative, an industry program launched in Canada in 1988. The ACC oversees the U.S. portion of the program.
Belonging to Responsible Care helps ensure logistics providers’ processes are aligned with both clients—many of whom belong to the ACC—and carriers.
For C.H. Robinson, adhering to the standardized protocols affirms communication between its ChemSolutions division, carriers, and shippers so all parties know exactly the types of chemicals in transit, and the precautions needed to ensure safety.
“The program conveys trust that we’re accurately communicating shipment requirements,” Buelt says.
LMS also views Responsible Care as an important tool to build confidence. “We’re a non-asset-based company,” Meetre notes. “But we want chemical shippers to know we take their business just as seriously as they do.”
Core methods for ensuring safety include the Plan-Do-Check-Act system, which requires companies to plan for hazards, enact the plans, check progress, and correct any issues. The Act portion requires buy-in from senior management, who are required to review the system and share results with stakeholders.
Participating companies undergo audits to ensure they are adhering to Responsible Care standards.
“LMS customers know our management systems and all of our processes are audited every other year, and they know if an issue arises with any of their shipments, we are required to handle it as they would handle it,” Meetre says. “It gives them peace of mind that their provider knows the chemical industry, and is prepared if a problem occurs.”
The next evolution underway for Responsible Care is the Product Safety Code, a measure being implemented in phases from 2014 through 2017. The code seeks to heighten safety protocols surrounding chemical production and handling, including transportation and warehousing. For example, participating companies must work to create a culture that values safety and accountability. The ACC provides auditors to check compliance.
Protective Measures
In the wake of the Sept. 11 terrorist attacks, new security measures affecting chemical shippers have been implemented. For example, Congress passed the Chemical Facility Anti-Terrorism Standards (CFATS) to buttress security.
“Different chemicals require differing levels of security based on government and agency requirements,” Emmerling says. “Certain chemicals are of interest to various government entities because of the products’ characteristics and what they might be used for.”
Special protections for sensitive chemicals might include caging them to prevent unauthorized access.
The Department of Homeland Security (DHS) outlines three measures that constitute risk: the severity of consequence if an attack occurs, the vulnerability of a facility to attack, and the level of threat that exists against a facility.
To comply with CFATS, facilities must meet DHS-set performance standards that vary depending on the warehouse. “Security measures that differ from facility to facility mean that each presents a new and unique problem for the adversary to solve,” DHS documentation states.
A slew of government agencies in addition to DHS—including the Environmental Protection Agency and the Occupational Safety and Health Administration—oversee chemical production and storage facilities.
“As safety regulations evolve, government agencies continually monitor compliance. Scheduled and unscheduled audits have become common in some parts of the country,” says Jacobson’s Strane. “Being prepared daily for these types of audits is a necessity. Since 2012, one of our operations has been visited by various compliance agencies more than 20 times.”
Managing security issues is all in a day’s work for warehouse providers.
Technology Causes a Reaction
The improved technology and tracking abilities that come along with centralized planning systems is opening the door to new opportunities for chemical shippers.
“With the increased use of technology to follow shipments in transit, it is no longer a novelty for our orders to be tracked from the time we place them to the moment they are delivered,” ChemLogix’s Skinner says. The sensitive nature of the materials being shipped makes robust tracking critical.
Benefits of adopting technology include the ability to automate freight execution and payment, receive notifications for important events along the way, and access centralized information, which facilitates tracking.
LMS operates centralized command centers that track the movement of all containers. “Command centers help integrate data, staff, decision-making, and visibility,” Meetre says.
In addition to stationing personnel at customer sites around the country, LMS runs a central hub in St. Louis. “The workers who staff that hub review all customer activity to identify opportunities to combine shipments and manage truck capacity,” Meetre says.
For example, if a truck is half-full with a load from one company, LMS can fill the rest of the truck with another company’s load bound for the same destination, provided the products are compatible.
The practice is particularly helpful in the age of tightened truck capacity. It also lowers a company’s shipping costs and reduces its carbon footprint. “This effort requires centralized visibility of client freight throughout North America,” Meetre says.
Customers also have the option of using their own transportation management system to take advantage of the information LMS gathers.
“If they’re using another system, our planners on-site have the capability to send those shipment opportunities to our collaborative command centers,” Meetre says. “It’s a holistic, centralized approach to freight management in the chemical industry.”
LMS has adopted other techniques to mitigate capacity issues, particularly with regard to refrigerated trucks, needed to securely transport temperature-sensitive materials. To find capacity, LMS has leased a dedicated fleet of refrigerated and hazmat certified trucks, managing the freight while a partner runs the trucks.
For example, Bluestar Silicones, a France-based silicone manufacturing company with U.S. offices in East Brunswick, N.J., frequently needs to ship products from the East Coast to the West Coast.
“We encounter occasional problems sending full truckloads to the West Coast, especially during the agricultural growing season,” says David Docherty, North American supply chain and logistics manager for Bluestar Silicones USA. “LMS has been extremely proactive helping us work around those issues.”
Can’t Stand the Heat
When Bluestar had to move a special type of insulation used on deep-sea pumps from Ventura, Calif., to Houston, the company needed to ensure temperate conditions during transport.
“The product could not exceed 90 degrees, but it had to travel through the U.S. Southwest and New Mexico,” Docherty says. “LMS worked with us on getting reefers to ensure the product was kept at the right temperature.”
Also of concern was ensuring the shipment didn’t idle at a desert rest stop, where the temperature could potentially rise and ruin the product. “LMS employed a team of drivers to ensure the door-to-door move was made uninterrupted,” Docherty says. “There was no stopover.”
“Managing chemical logistics is all about centralizing freight, optimizing it safely, adhering to all the regulations and equipment requirements, and providing shippers with 100-percent visibility,” Meetre says.
LMS also promotes safety by ensuring carriers have acceptable safety ratings and appropriate insurance levels. The company uses a real-time feed to monitor carrier Compliance, Safety, Accountability scores, which weigh factors such as safe driving, vehicle maintenance, and insurance status.
When sensitive, potentially dangerous chemicals are traveling across the supply chain, putting safety first is the only way to do business.