Conformance vs. Compliance: Their Key Differences
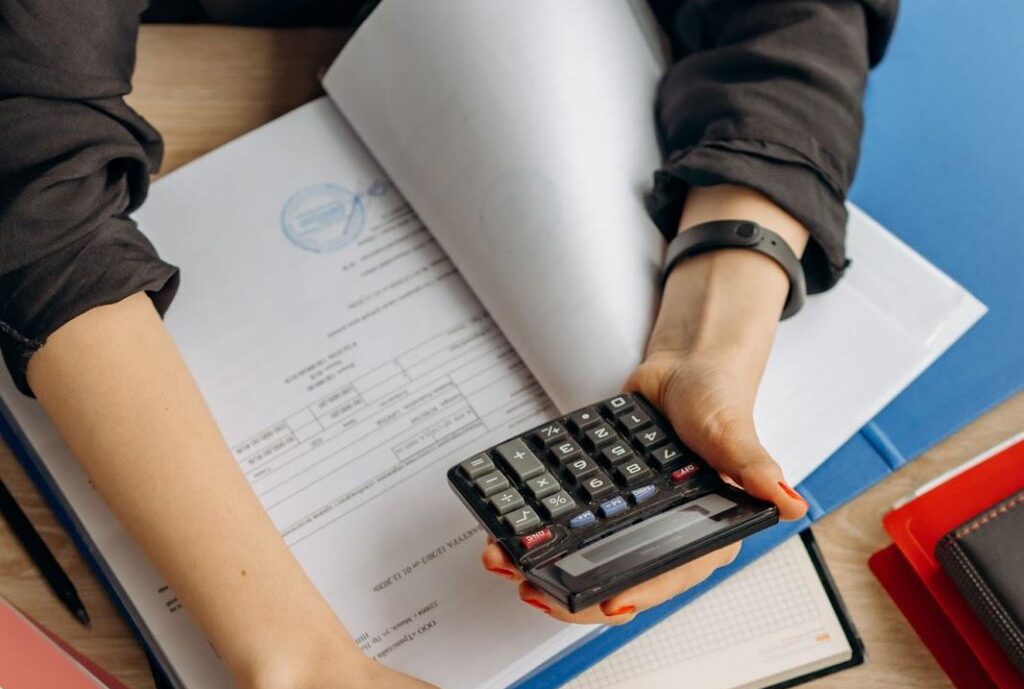
As supply chain managers navigate the intricate landscape of industry norms and regulations, the terms conformance vs. compliance often surface, each carrying its distinct meaning and application. These concepts are pivotal in ensuring that products and services meet prescribed standards and legal requirements.
This article aims to demystify these terms, illustrating their practical implications in various industries, particularly focusing on the medical device manufacturing supply chain.
Understanding Conformance and Compliance
In the realm of industry, particularly noticeable in sectors like medical device manufacturing, the distinction between conformance and compliance is often nuanced yet significant.
Conformance typically pertains to the adherence to certain voluntary standards or procedures, whereas compliance is generally associated with meeting legal and regulatory obligations. The subtle distinctions between these two can profoundly impact how companies approach quality, safety, and regulatory adherence.
For conformance, consider it a company’s voluntary adherence to certain standards or processes to ensure quality and efficiency. An example could be a tech company conforming to ISO certification standards to ensure their quality systems are up to par, even if not legally mandated.
In contrast, compliance is more about meeting legal obligations. A medical device company, for instance, must comply with specific legal and safety regulations to ensure that their products are safe for public use.
Conformance
Conformance refers to meeting the specifications or criteria set by a standard or test method, which is often voluntary. It implies that a product, service, or process has met the requirements and specifications defined by a certain standard, albeit not legally mandated.
For instance, a company in the food logistics industry might conform to certain preparation and storage standards to ensure quality, although these standards aren’t enforced by law.
Compliance
On the flip side, compliance indicates the adherence to legal and regulatory requirements. It’s about fulfilling an external authority’s legislative and contractual requirements. For example, in medical devices, companies must comply with stringent regulations and standards set by regulatory bodies to ensure the safety and efficacy of their products.
Legal Obligations and Regulatory Standards
Navigating legal obligations and voluntary standards is integral in industries like medical device manufacturing. Companies must balance their commitment to quality, showcased through conformance to certain voluntary standards, with the mandatory compliance to legal and regulatory requirements.
For instance, medical devices must comply with explicit safety and quality regulations defined by regulatory authorities to ensure the users’ safety and the product’s efficacy.
Furthermore, the intertwining of conformance and compliance becomes evident when companies voluntarily adopt certain standards to align with or exceed legal requirements.
This proactive approach accentuates their commitment to quality and positions them favorably in the competitive market landscape. Quality control measures, industry certifications, and adherence to international standards often become differentiating factors companies leverage to gain a competitive edge.
The balance between conformance and compliance can be further illustrated in the automotive industry, where manufacturers often voluntarily conform to certain environmental and safety standards to not only comply with legal requirements but elevate their brand reputation and customer trust.
They integrate cutting-edge technologies and innovative practices to meet and exceed compliance standards, showcasing their commitment to quality and safety.
Quality Control
Quality control is pivotal in both conformance and compliance landscapes.
For conformance, quality control might involve adhering to voluntarily adopted standards like ISO certification, ensuring products or services meet certain quality benchmarks.
In compliance, quality control is paramount in ensuring that products or services meet the stringent legal and safety regulations, a non-negotiable imperative especially vital in industries like medical device manufacturing.
Quality control transcends the validation of product or service quality, encompassing process efficiency, risk management, and customer satisfaction. It’s a comprehensive approach ensuring the end product’s quality and the efficacy and safety of the processes leading to its creation and delivery, marking its universal application across conformance and compliance spectrums.
ISO Conformity Assessment and Certification
The International Organization for Standardization (ISO) is renowned globally for developing and publishing international standards, ensuring quality, safety, and efficiency across various industries.
ISO certification signifies that a company has met specific criteria, showcasing its commitment to delivering quality and value. These certifications are sought after by companies aiming to align their operations with international standards, instilling confidence among stakeholders and customers.
Achieving ISO certification entails a rigorous process where companies are assessed based on the specific ISO standard’s criteria. It’s a testament to the company’s adherence to defined protocols, quality assurance, and safety guidelines.
ISO certification isn’t just a badge of honor but a strategic tool that empowers companies to improve efficiency, mitigate risks, and foster innovation.
ISO certification also plays a pivotal role in international trade. Companies with this certification have a competitive edge in global markets as it signifies the entity’s adherence to universally recognized quality and safety standards.
For instance, in medical device manufacturing, an ISO-certified company assures its global clientele of its devices’ impeccable quality and safety, facilitating smoother trade relations and market access.
Non-Compliance Consequences
Non-compliance can have serious implications for companies, leading to penalties, damage to reputation, and even business closure. Regulatory bodies enforce stringent measures to ensure companies adhere to the prescribed legal and safety regulations, ensuring quality and safety.
FAQs
Dive into the following frequently asked questions for a clearer insight into conformance vs. compliance.
What is the difference between compliance and conformance testing?
Compliance testing ensures adherence to legal requirements, while conformance testing checks alignment with voluntary standards.
What is the difference between compliance and non-conformance?
Compliance is following required laws and regulations, non-conformance needs to meet set standards or specifications.
What is the difference between conformity and compliance audits?
Conformity audits evaluate adherence to standards; compliance audits assess adherence to legal and regulatory requirements.
Does conformity mean compliance?
No, conformity relates to meeting standards, while compliance is about adhering to laws and regulations.
Conformance vs. Compliance Industry Standards Conclusion
Understanding their distinct roles and applications is paramount in the intricate dance of conformance vs. compliance.
While conformance revolves around voluntary adherence to standards, enhancing quality and efficiency, compliance is anchored in meeting legal obligations, a cornerstone in regulated industries like medical device manufacturing.
Balancing the two ensures regulatory adherence and drives quality, innovation, and competitiveness in today’s dynamic business logistics and supply chain landscape.