Ensuring a Sustainable Supply Chain
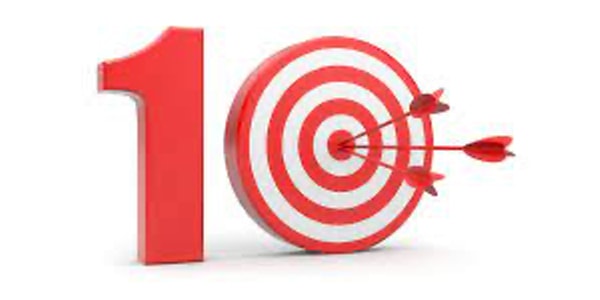
The Ukraine conflict, COVID-19, and rising inflation have drawn attention to the fragility of global supply chains. With all eyes on logistics, operations leaders have additional reason to examine supply chains from the ground up. Here’s how to start.
1. Map your supply chain upstream and downstream. Any exercise to improve supply chain operations must include identifying upstream and downstream partners. Gain as much knowledge as possible. Learn about geographic exposure, climate goals, and sustainability metrics already being tracked.
2. Align stakeholders. The data and know-how needed to improve sustainability is dispersed across partners and teams. You’ll need everyone’s help to adjust contracts, optimize production, and create reports, so get buy-in early.
3. Establish a baseline. Since every supply chain is different, measuring Scope 1, 2, and 3 emissions is the most powerful way to determine your strengths and weaknesses. Scope 3 emissions, in particular, are tied to your supply chain, so they’re critical to monitor. Use automated carbon accounting technology to ensure consistency.
4. Identify your pain points. Once equipped with data, identify operational vulnerabilities and risk, which differ significantly depending on industry. For example, agricultural supply chains are more exposed to physical risks, like extreme heat and drought, while electronics supply chains are vulnerable to shifting policy. Look at your top emissions source and products with the highest footprints. Consider inputs produced in-house vs. procured from external vendors. Investigate how you move and package goods.
5. Improve operational efficiency. Reducing downtime and improving throughput across your operations are good for your bottom line and sustainability. Switching to electric vehicles requires less maintenance than internal combustion engine vehicles, which reduces downtime, maintenance costs, and fuel spend. Simple route optimizations, which are easy to identify with route optimization software, can save fuel and money.
6. Reduce resource waste. There are almost always areas within a supply chain where you can reduce or optimize resource usage. Concrete and cement producers are looking at ways to reuse hazardous wastewater. Clothing retailers are creating entire product lines out of scrap materials. Packaging can often be reused or repurposed.
7. Develop a supplier engagement plan. Establish sourcing standards and a supplier code of conduct that require emissions disclosure and carbon reduction targets. The United Nations Global Compact provides advice on this topic. Rather than dropping suppliers who are new to sustainability, help them begin their sustainability journey and share best practices so that you can improve together.
8. Help decarbonize suppliers. As part of supplier engagement, consider crowdfunding or investment initiatives to direct capital to your value chain. For example, helping your raw materials supplier install on-site renewable energy will reduce your Scope 3 emissions and make them more resilient to energy price swings and outages.
9. Track your progress. Track and celebrate wins. Set a specific carbon reduction target or net zero plan, so that you can measure the impact of your work. With your baseline and reduction target, you’ll be able to monitor persistent hotspots and areas where you’ve made the most progress.
10. Communicate results internally and externally. Sharing progress drives accountability and growth. Send internal updates to stakeholders, publish an annual sustainability report, or participate in more formal climate disclosures. Existing customers will be pleased that your operations are more resilient, and prospective customers may choose you thanks to your sustainable supply chain.
SOURCE: Saleh ElHattab, CEO & Founder, Gravity Climate