Get IT Together
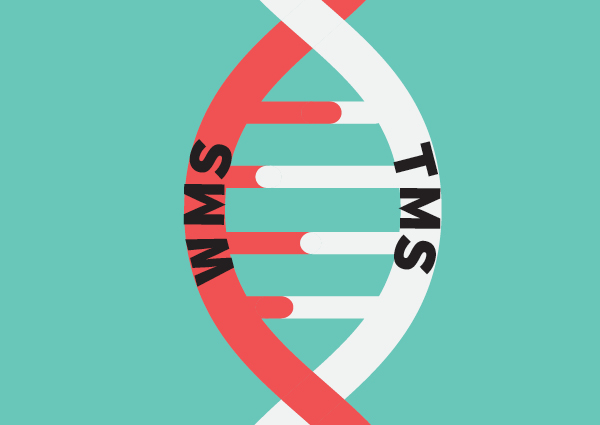
Integrated WMS and TMS solutions increase visibility and communication and optimize the movement of goods.
A supply chain operation with unreliable communication between its warehouse and transportation components is like a perpetual fire drill: Every day is filled with surprise, uncertainty, and scrambling to keep up with the unforeseen, says Evan Garber, CEO of EVS, a Colorado-based warehouse management and supply chain technology company.
Responding to E-Commerce Demands
“A lack of integration is a lot of people saying, ‘Shoot, I forgot,'” Garber explains. “If a truck is going to be two hours late, for example, and somebody forgets to let the dock know about it, that dock is blocked for two extra hours, keeping another truck from using it. It just causes chaos.”
As a result, organizations increasingly have embraced the need to integrate their warehouse management and transportation management systems. Integration sharpens visibility, accuracy and speed, preventing the chaotic fire drills that can keep an organization from operating at optimum efficiency.
The largest, most successful companies–“the thought leaders”–have been using integrated systems for at least the past five years, notes Eric Lamphier, senior director of product management for Manhattan Associates, an Atlanta-based supply chain software company. And the practice continues to spread to mid-tier organizations and beyond.
Separating from Silos
“Companies that are aspiring to great supply chains are seeing leading companies integrating their systems and concluding that they have to do it too,” Lamphier says. “Companies can’t operate in silos anymore. They need a much more unified experience.”
National DCP, an Atlanta-based supply chain management company that serves Dunkin’ Donuts franchisees in 51 countries, works with Manhattan Associates to integrate its warehouse management system (WMS) and transportation management system (TMS). The company “has benefited greatly from having an integrated ecosystem,” says Chris Lafaire, senior vice president of information technology for National DCP. It projects the integration will reduce annual transportation costs by 3 to 7 percent, improve backhaul opportunities by 10 to 20 percent, and drop waste and spoilage by 10 to 20 percent, according to Manhattan Associates.
Better visibility is the key. “In the past, we used a TMS software and a separate WMS software, which always caused interface issues,” Lafaire says. “Since we integrated our transportation management and warehouse management system using Manhattan’s middleware, we have eliminated all the interface issues, data discrepancies, and inventory problems we faced in the past. We have benefited from having accurate inventory and transportation information across all our systems.”
Optimization and Visibility
Companies can sync their WMS and TMS operations in two ways: by integrating two existing systems or by adopting a unified WMS-TMS solution. Ultimately, the main goal is to align the operations.
A WMS orchestrates inventory in the entire warehouse. It knows what inventory is present and what’s coming in and going out. It tells warehouse workers what to pick and where to store items. However, if the WMS doesn’t know the details of inventory arrivals and when trucks will be ready for departure, the ceiling on efficiency is low.
“When the orchestrator of your inventory doesn’t talk to your TMS, then people are picking and packing for shipping, but don’t have a good idea of where they should be staging the inventory and when the truck is coming to pick it up,” Garber says.
In contrast, when the WMS and TMS communicate, warehouse operators can make decisions to ensure that items are picked and prepared at the ideal time. “When the order arrives, the departure dock is scheduled and the warehouse management system can tell pickers where they need to go, what they need to do, and when they need to pick,” Garber says. “When the truck shows up, the inventory is ready.”
If the truck shows up and the inventory isn’t ready, a company can incur late fees. They can also start to have problems with carriers and even customers. “That’s why it’s important to orchestrate data from the initial customer request all the way through warehouse scheduling and out the door to transportation,” Garber says.
A warehouse operation cannot be optimized without integration with its transportation end.
“The more information you have about what comes in and out of the system, the better off you will be,” Garber says. “If you’re willing to optimize within the four walls of the warehouse, but don’t know when trucks are scheduled, it’s hard to achieve truly efficient operations. The more information is shared, the more you can optimize.”
“You can’t have end-to-end supply chain visibility without strong integration between your WMS and your TMS,” agrees Dave Giblin, vice president of operations for ODW Logistics, a third-party logistics provider based in Columbus, Ohio.
“Take the simple example of a WMS generating a tracking number for an outbound shipping order,” Giblin says. “If that information is not transitioned to the TMS, it may track the order, but it doesn’t link that order back to the WMS.
“Without that exchange of data, the company misses out on an opportunity for the end-to-end connectivity that not only provides visibility to the product’s location, but also provides the ability to do detailed line-item cost reporting, cost accounting, and predictive analytics. It is difficult to achieve those benefits without a strong integration between the WMS and the TMS.”
For National DCP, a key criteria to an effective WMS-TMS integrated platform is “the use of a central location to manage all the interfaces and integration points that can provide visibility to any potential issue,” Lafaire says
When a WMS and TMS are not integrated, one tends to lead the other, resulting in an imbalance in the operation. With a unified platform, however, organizations can look at warehouse and transportation management holistically, rather than as two pieces that need to be reconciled.
“When your visibility is in one place—not in a TMS and also in a WMS—the status of orders, shipments, carriers, deliveries, and planned arrivals is unified in one converged platform,” Lamphier says.
Customer Service and Personnel
An integrated WMS-TMS is crucial to maintaining strong customer service. Without integration, warehouse operations work too reactively to maintain a tight schedule. Workers are constantly rushing to catch up to prepare orders and load trucks, inevitably leading to late deliveries. Without visibility, the warehouse is always surprised, and “you don’t want surprises,” Garber says.
“If the systems are providing all that information, then you can avoid surprises,” Garber says. “Of course, mistakes and last-minute things happen, but they can be minimized and become exceptions rather than the way the warehouse operates.
“Then you can optimize and take care of exceptions when they occur,” he adds. Integrated systems allow for automated feedback loops that raise alarms throughout the supply chain when issues arise somewhere in the warehouse or transportation system.
“Without tight integration, you’re going to either have bad alerts or no alerts at all,” says Bill Grannis, vice president of information technology for ODW Logistics.
In addition, using an enterprise-level WMS and TMS with standardized methodology allows for open systems and open transactions with vendors and customers.
“When operations run manually or with in-house software it’s hard to reach out to vendors, customers, and suppliers when everything is one off,” Grannis says. “It’s a huge advantage to operate with a state-of-the-art, integrated WMS/TMS solution.”
Warehouse operations, including those with a WMS, often emphasize keeping workers busy and efficient. “But when it comes to your own fleet or even the assets that you’re contracting with and tendering to the TMS side, it’s important to ensure the warehouse workers and drivers are in the know and effectively utilized, so you don’t waste resources,” Lamphier says.
Integration Challenges
One chief challenge to integration is that existing WMS and TMS technologies often are not compatible. In particular, WMS technology tends to be older, less sophisticated, and less amenable to integration. As a result, integration typically means an overhaul of existing systems.
“That’s why integrations are hard,” Garber says. “You have to say goodbye to the old and hello to the new. And that means making an investment.”
It can be challenging to wed the mindsets of the warehouse and transportation departments, which are accustomed to worrying about their own roles in relative isolation.
“That’s not sustainable,” Lamphier says. “And that’s where we’ve seen the rise of the chief supply chain officer who’s being more thoughtful and holistic around the idea that the company can do an optimal job in warehousing, but fall on its face and drive poor customer service and high costs in transportation. They’ve got to be mindful of the whole enterprise.”
A company might process fewer orders at a different sequence in the distribution center with the warehouse management system, and that might cost 5 percent more. “But if the company saves 45 percent on transportation spend and customers receive their goods more rapidly, then the business wins,” Lamphier says. “Decision makers are setting forth these kinds of more thoughtful objectives.”
National DCP saw benefits from using Manhattan’s standard features rather than using customized software specific to its business practices. That is “one key success criteria” for the company’s integration experience, notes Lafaire.
“Every company believes it is unique, but by tailoring and adapting some business practices we can leverage proven integration and features on the Manhattan software,” he notes.
Organizations looking to adopt an integrated WMS/TMS solution should map out their processes, goals, and opportunities for improvement.
In addition, they should “fully vet whether the solution they are architecting will be able to fulfill their specific needs,” Giblin recommends.
“Companies sometimes get a shiny object in front of them and say, ‘Hey, this looks great. We’re going to get this.’ But then it doesn’t fit what they are trying to accomplish,” he notes.
Whatever the steps to get there, all companies should consider integrating their warehouse management and transportation management systems software to boost operational efficiency and improve customer service.
Responding to E-Commerce Demands
The Amazon effect and the rise of e-commerce is a clear factor driving companies to adopt an integrated approach to warehouse and transportation management. Demand patterns are changing and that “has changed the mindset of shippers, even those who aren’t yet doing a lot of e-commerce,” says Eric Lamphier, senior director of product management for Manhattan Associates.
“Shippers are striving to be faster and more consumer-centric,” Lamphier says. “They want to know, with a level of certainty, that they have delivered on the promises they made to customers that goods would be delivered on time.
“That concern for customer service is driving modernization, new systems implementations, and WMS-TMS integrations,” he adds.
The need for speed is spurring the rise of a waveless optimization model that solves problems as they arise and contemplates orders and shipments continuously throughout the day rather than optimized in batches via a more linear approach.
“For that to happen, systems have to be able to talk to each other constantly,” Lamphier says. “An effective WMS/TMS integration is essential.”