Global Logistics Reboot: A New Beginning
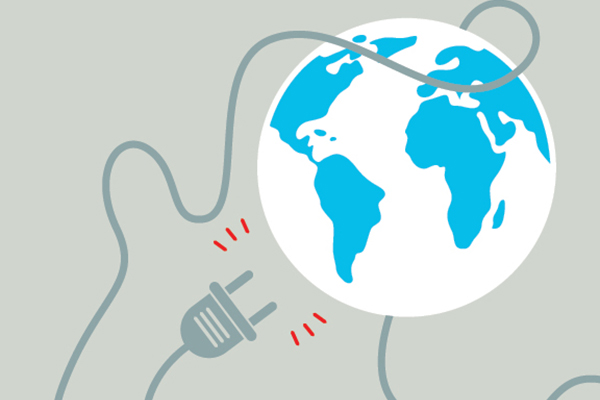
Global logistics moves to “the next normal” after an upheaval in product flows over the past year.
After a year overtaken by the pandemic, many of us long for a return to normal, or at least a shift to a new normal.
A Changing Roster Of Countries
The global logistics sector, however, can’t count on a return to normal, whether new, old, or otherwise. Instead, it faces a new beginning.
“Companies will need to replace linear, point-to-point supply chains with real-time digital networks,” says Jim Tompkins, founder and chair of consulting firm Tompkins International. These networks will need to integrate planning and execution to reduce lead times and transportation costs and boost customer satisfaction.
The upheaval in product flows over the past year, mostly driven by the pandemic, is behind this new logistics world. For many companies, demand plummeted in the first few months of the pandemic, only to come roaring back later in 2020.
“The result was enormous imbalances in conveyances like containers, unreliable shipping lead times, escalating freight rates, and increasing uncertainties in global trade,” says Hau Lee, professor at the graduate school of business at Stanford University.
More than three-quarters of those responding to a July 2020 Institute of Supply Management (ISM) survey indicated lead times for inputs from China had been extended. For products from Europe, 83% reported longer lead times.
Industry observers say these imbalances will only gradually abate over 2021. One reason? It will be some time before the sudden drop in passenger flights—they were off by 66% in 2020, according to IATA—reverses. Many of these flights also transport cargo.
Redundancy, Resilience, Agility
The upheaval wrought by the pandemic highlighted how companies that had been approaching their supply chains strategically were better able to navigate disruption, says Ricardo Ernst, professor of global business, operations, and global logistics at Georgetown University. Moving forward, the supply chain function will play a more strategic role at many organizations.
To remain relevant and successful, supply chains will need to place a higher priority on resilience, redundancy, and agility. Cost and efficiency will remain critical, but they no longer will be the only focus. “It’s an important shift in how companies assess supply chains,” Ernst says.
Nearly 90% of supply chain professionals responding to a recent Gartner survey say their organizations plan to invest in supply chain resiliency (see chart). Resilience, according to Gartner, is the ability to adapt to structural changes by modifying supply chain strategies, products, and technologies.
A similar number of respondents to the Gartner survey indicate they also plan to invest in agility within the next two years. Paul Dittman, assistant department head of supply chain with the University of Tennessee at Knoxville, identifies three elements to supply chain agility: physical, digital, and process agility.
Physical agility could include, for instance, contingency capacity to meet demand surges. Digital agility looks at technology that can provide visibility and automation. And process agility would include functions like supplier management.
Ask “What If?”
How can organizations boost resilience? They do it “by taking an intelligent, comprehensive look when deciding where to source parts, and asking ‘what if,'” says Bobby Bono, partner and industrial manufacturing practice leader with PwC.
For instance, what if the country in which suppliers are located, or the transportation system there, shuts down? “This will change the calculations on supply chains in both the short and long term,” Bono says.
To increase redundancy, some organizations are holding more buffer inventory. Others are building extra capacity in production, and some are increasing the number of suppliers.
“The diversification of the supply base can result in reshoring or multi-sourcing or building a regional supply chain,” Lee adds.
Opinions are divided on the degree to which companies actually will shift to regional and thus shorter supply chains. The companies that make this shift will need to contend with numerous obstacles.
Many customers are more swayed by low pricing than by domestic sourcing and production, particularly in industries with intense price competition, such as retail and fashion. Some U.S.-based manufacturers considering reshoring production would need to reestablish manufacturing capabilities that no longer exist in the country.
When evaluating supply sources outside China, companies also need to consider both the size of the Chinese market, at about 1.4 billion, and the growing Asian middle class. The global middle class will swell to 4.9 billion people by 2030, from 1.8 billion in 2009, the OECD estimates. Two-thirds are expected to reside in Asia, up from 28% in 2009. The largest share will call China home. Many organizations will benefit by maintaining a manufacturing presence in this region.
Despite these concerns, the pandemic does appear to be accelerating a shift in manufacturing away from China, a trend that began even before coronavirus became a household word. Manufacturing imports from China dropped in 2019, reversing the previous trend, according to the Kearney Reshoring Index.
At the same time, imports from other Asian low-cost countries jumped by $31 billion. Most of the products that were part of this shift had been impacted by tariffs imposed on Chinese goods, Kearney noted.
One way to reduce the customs duties levied on many Chinese products coming into the United States, and mitigate the risk that comes with keeping production mostly within a single country, is through a “China Plus One” strategy, Lee says. That is, companies importing goods from China also partner with a supplier located in another country.
Two countries likely to benefit from companies’ move to add supply sources outside China are Mexico and Vietnam, Lee says. While both countries saw manufacturing downturns in 2020, they had largely rebounded by year end, according to Trading Economics.
Regionalization and Reshoring
As they develop a new approach to globalization, companies need to recalibrate expectations, reevaluate priorities, and consider anew what they expect from each region.
In the past, for instance, companies often viewed Asia as their base for manufacturing and Latin America as a source of raw materials. Now, however, companies may crunch the numbers and realize it makes sense to shift some manufacturing to Mexico, given its proximity to the North American market.
“Most companies are doing ‘controlled reshoring,'” Lee says. This could mean that critical, lower-volume products are reshored, while products produced in larger, stable volumes remain offshore to capture economies of scale. Or it might mean a domestic site builds products while they’re in the launch phase and demand is uncertain. Production then would shift to an offshore site once demand is larger and steadier.
“Smart use of multiple sites is the best way to go forward,” he adds.
Embrace E-commerce
Also straining supply chains over the past year has been the tsunami of customers shifting their business online. While this trend had been underway already, the pandemic accelerated it by several years.
It’s not just domestic online sales that are growing. Online cross-border transactions are set to jump by 24% in 2020, according to The Paypers, a Dutch source of news on global payments. Cross-border e-commerce orders, which often involve small orders that require many processing steps, tend to be more complex than even domestic e-commerce orders.
The jump in e-commerce, along with the shrinking availability of labor, is accelerating companies’ move to digitization and automation. Automation and mobile robotics can help process the “eaches” that characterize e-commerce orders.
However, robotics and automation won’t be a panacea just yet. Many solutions today can handle only one or a few steps in the production process.
In apparel manufacturing, for instance, it’s possible to automate fabric production, cutting, and sewing. A bottleneck appears, however, when it’s time to flatten the fabric to feed it into the sewing machine, which remains a mostly manual process. Where advancements are speedier and more comprehensive, companies will have more choices in designing their global supply chains.
Similarly, blockchain has the potential to streamline financial flows and provide a full record for tracing and tracking. However, gaining all its benefits requires an extensive supply network. Many companies across multiple industries still need to work on developing these.
Monitor Trade Agreements
Several recently inked trade agreements may eventually alter product flows in various parts of the globe. The Regional Comprehensive Economic Partnership (RCEP), signed in late 2020 by the 15 members of the Association of Southeast Asian nations and five partners, will connect about 30% of the world’s people and output (see chart).
The agreement is expected to boost the efficiency of many Asian economies, linking their strengths in technology, manufacturing, agriculture and natural resources, ASEAN said.
Across the Indian Ocean, the African Continental Free Trade Area agreement (AfCFTA) went into effect on Jan. 1, 2021. It links the countries across Africa, eliminates 90% of tariffs, and creates a single market across the continent. Together, the countries boast an estimated 1.3 billion people and a combined gross domestic product of $3.4 trillion.
Much work remains in building infrastructure and developing a customs workforce across the African continent, among other initiatives. As progress in these areas proceeds, it’s hoped the agreement will bolster the competitiveness of African industry.
Sustainability and Social Issues
Interest in environmental, social and governance (ESG) practices, which has been growing, gained further momentum over the past year. “Organizations are taking a strong stand,” notes Bob Hawkey, director, operations transformationwith consulting firm Grant Thornton, with more companies including ESG requirements in their supplier contracts.
In part, their action is a response to investor interest. The 425 institutional investors from across the globe who responded to a 2020 survey by Blackrock, an asset management firm, say they plan to increase the level of sustainable assets under management from 18% in 2020 to an average of 37% by 2025.
The August 2020 port explosion in Beirut, Lebanon, which killed more than 200 people, also highlighted the critical role of ESG, and the need for transparency and accountability on shipped goods. Going forward, “businesses will need to demonstrate that their supply chains are fit-for-purpose and ‘clean,'” says Matthew Margetts, director of sales and marketing with Smarter Technologies, an IoT company.
The supplier-customer relationship will change yet in another way, Lee says. Suppliers will be more than just sources of materials and products. Many employees with suppliers that have implemented mature manufacturing have also mastered the skills and expertise needed to improve manufacturing processes and product design.
As a result, supplier bases will be “not just the source of materials and products, but also the source of innovations,” Lee says.
Even as the world changes, the ability of companies to gain a competitive edge by leveraging the innovative power of their suppliers and supply chains remains.
A Changing Roster Of Countries
It’s not just supply chains that are changing. The countries many companies evaluate when deciding where to locate operations or search for suppliers continues to evolve, as well. The following are some of the countries currently identified as potential partners.
Cambodia
One of the signatories to the Regional Comprehensive Economic Partnership (RCEP), Cambodia’s economy is expected to grow by four percent in 2021, after contracting by an estimated two percent in 2020, because of the pandemic, the World Bank says.
China
China appears poised to remain a significant supply source. And given its population of 1.4 billion, it likely will form a sizable market for some companies, says Hau Lee of Stanford University.
India
Like China, the size of India’s consumer market—about 1.37 billion people—is enticing. In February, Tesla announced it would establish an electric vehicle manufacturing plant in Karnataka, India.
Mexico
Mexico likely will see an increase in manufacturing, says Tompkins of Tompkins International says, although he doesn’t expect it to significantly impact where manufacturing is done. In 2020, foreign direct investment into Mexico dropped by less than 10 percent, compared to the 37 percent drop experienced throughout Latin America and the Caribbean, Santander Bank reports.
Vietnam
Vietnam is one of the few countries not expected to experience a recession because of the pandemic, the World Bank says. To be sure, growth has slowed. Before the pandemic, annual GDP growth averaged about six to seven percent; that’s expected to drop to 2.8 percent for 2020.