Global Supply Chain Strategies: Certain Uncertainty
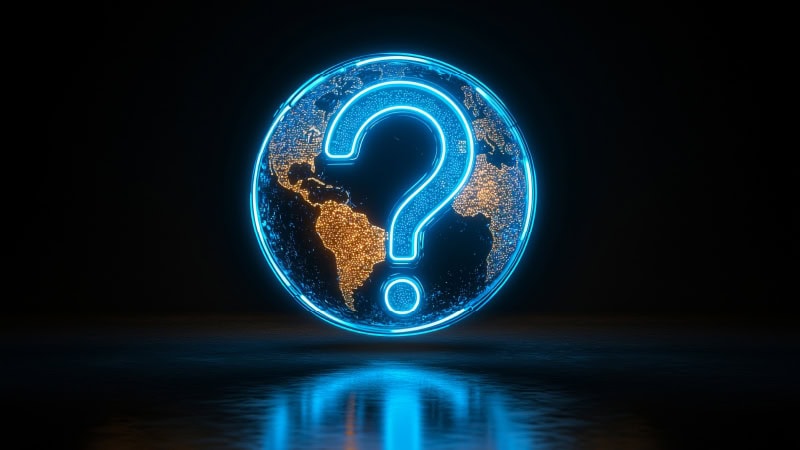
Global trade faces mounting uncertainties, from shifting geopolitical tensions to the ever-present risk of natural disasters. To stay resilient, organizations must cultivate leaders with geopolitical expertise, enhance supply chain redundancy, and leverage technology for faster, data-driven decision-making in an unpredictable landscape.
For supply chain and logistics professionals, “uncertainty is the devil,” says Alan Amling, a professor in the Global Supply Chain Initiative at the University of Tennessee, Knoxville.
A lack of stability makes it difficult to reach informed short-term decisions, let alone long-term, larger investments in physical locations or supply networks, where the economic implications extend beyond the next election cycle.
Yet, uncertainty is the only certainty for the foreseeable future, Amling says, given the frequency of natural disasters, a fluctuating geopolitical environment, and evolving immigration regulations.
But there’s a bright spot: Even amidst the uncertainty, people will continue to need things and companies will continue to make and distribute products.
While the specific disruptions and politics will change, supply chain professionals confront the same basic challenges they’ve always faced: reducing costs, minimizing risk, and improving customer service, says Richard Thompson, international director, supply chain and logistics with JLL.
To meet these challenges and thrive in today’s fluctuating global supply chain environment, several attributes are critical. Companies need a strong understanding of the practical impact of geopolitics, a diversified supplier base, and a robust trade platform.
Outsourcing Costs Rise
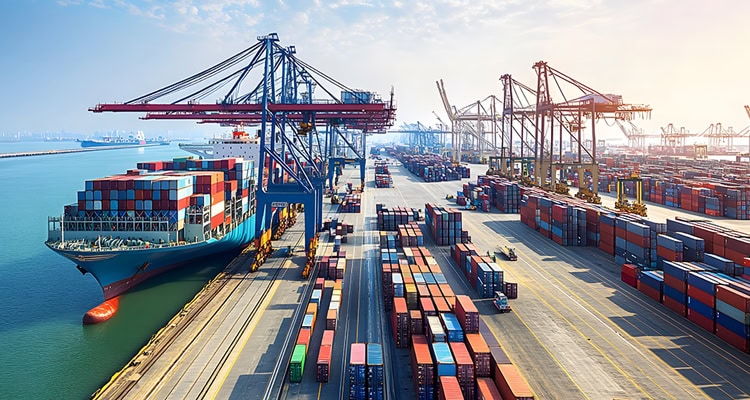
Global trade and transportation is becoming more uncertain for many businesses due to increased geopolitical tensions, tariffs and trade barriers, and lengthening supply chains.
The decision by many American companies to outsource manufacturing has contributed to today’s challenges. Over the past four decades, China has become the greatest manufacturing hub in human history, says Nick Vyas, founding director of the Global Supply Chain Institute at the University of Southern California. Producers and consumers saved money, but supply chains became less resilient and less able to respond to uncertainty.
The current geopolitical environment adds to the concerns. For U.S.-based companies, the proposed tariffs threaten to boost costs, while any retaliatory tariffs will also impact demand, says Srini Rajagopal, vice president, logistics product strategy with Oracle. The war in Europe also impacts supply chains, as Ukraine exported components some manufacturers need for production.
Questions around immigration policy in the United States also keep supply chain professionals up at night. Depending on the changes implemented, it’s possible several million people will exit the work force, Rajagopal says.
The Endless Aisle
Online shopping, which has given rise to endless aisles of products, also changes global supply chains, says Kimberly Reuter, CEO of CSG Consulting. Rather than a hub-and-spoke structure, a company might source directly from a manufacturer, or have an order arrive pre-packaged and then ship it to the consumer.
This means the customer experience, including delivery, starts at the product’s origin. Few customers differentiate between the product and the supply chain, Reuter says. Instead, many will penalize the manufacturer if, for instance, an item arrives late.
The End of De Minimis?
The $800 de minimis value—the maximum amount before duties are assessed on most packages coming into the United States—remains in effect as of mid-February 2025, but could change. Lowering this number has been a topic of conversation among policy makers in the United States for years.
While the regulation’s original purpose was to allow travelers to bring back personal goods, the de minimis exemption has been used for many ecommerce shipments, Reuter says. More than one billion packages each year fall under the $800 amount, the Congressional Research Service found.
Any significant, sustained change to the threshold will impact not just consumers, but Customs officials, who will have to obtain more information on all these packages. That will require new technology and processes, as well as time to implement, Reuter says.
The Right Side of Change
The various changes impacting global supply chains are neither good nor bad in themselves. “It depends what side of it you’re on,” Amling says. “If you’re on the wrong side of it, get on the right side.”
Start with people. Ensuring a global supply chain organization is on the right side of the changes begins with people. No amount of technology or money will compensate for supply chain leaders who aren’t able to manage through the current disruptions, says Omar Kazzaz, with Kazzaz Advisory Group. Effective supply chain leaders are proactive, and understand geopolitics and strategy.
They also have “an impeccable ability to connect the dots,” he says. That is, they need to be able to understand how events occurring on the other side of the world, such as a disruption in a trade route, can impact their own supply chains.
These professionals also need to connect with suppliers, forwarders, and other business partners who are similarly proactive and insightful. When a business hits a bottleneck, it’s only a matter of time before the impact ripples out to its partners, Kazzaz says.
Remove silos. Having the right people will be of little value if few understand the company’s strategy or decisions. About 35% of the friction in supply chains today is waste resulting from siloed data and information, Vyas says. Many companies hesitate to share information with suppliers and customers due to a lack of trust.
“I’ve seen cases where they don’t even share the data within a department,” he says. The lack of visibility can hamper decision-making and lead to unproductive actions.
Communication between computer systems, as well as between systems and people, is also essential. These connections help ensure one accurate version of the truth.
Private trading networks, an emerging technology, enable partners to share information while limiting what each can see.
“They achieve that collaboration without giving away the jewels,” says Jonathan Colehower, managing director with the global supply chain practice of UST, a provider of digital solutions.
Organizations that share information, particularly in multi-tier supply chains, can learn of potential problems before they spiral beyond control. The company championing use of a private trading network may need to help its partners, especially smaller ones, implement it.
The ability to pivot. In today’s environment, the ability to leverage change as an opportunity is a major competitive edge, says Don Hicks, CEO of Optilogic, a supply chain company.
This requires the ability to create options that allow an organization to pivot, Amling says. Artificial intelligence can help supply chain organizations develop options and assess their impact so they can react quickly and intelligently to changes.
For instance, a U.S. automaker may engage in scenario planning to identify the potential impact of measures to address tariffs, such as moving a plant from China to Vietnam.
Resilience enables organizations to absorb adversity, says Michael Zimmerman, partner in the strategic operations practice with Kearney, a global consulting firm. It comes from redundancy, such as extra inventory and productive capacity, and multiple supplier and logistics partners.
Agility builds on resilience by using these attributes to quickly adapt to disruption, Zimmerman says. For example, a company may work with a partner to shift to a new logistics route and avoid delays.
Modern supply chain technology. Trying to make informed, timely decisions in a dynamic supply chain environment without robust technology is becoming difficult, Rajagopal says.
A modern technology platform should be able to connect the supply chains of the company and its suppliers, providing a digital thread across entire transactions. The platform should also provide a system of record, visibility to the goods in the chain, and the ability to address challenges and exceptions before they balloon.
The platform’s forecasting ability should help determine the amount of warehouse and transportation capacity needed. It also should identify opportunities to save money by, for instance, identifying transactions eligible for any benefits from trade agreements, Rajagopal says.
Sourcing and product design. As companies look for new sourcing options, procurement—historically, a support function—is shifting to a more strategic role. “Today, procurement has a seat at the strategic table, all the way up to the C-suite,” says Priya Anand, director of logistics services at Jabil, a provider of supply chain solutions.
Procurement leaders are driving new investments in supply partners, as well as dual- or multi-sourcing strategies that can mitigate risk and help their companies get ahead of disruption, she adds.
Product design can also minimize the risk companies will be subject to a tariff or run afoul of regulations, Colehower says.
For example, apparel producers often are restricted from importing cotton from certain parts of the world, such as the Uyghur region in China. Technologies including AI can help them redesign their products with alternative materials.
Rethink the Distribution Network. When designing distribution networks for today’s global environment, the real estate phrase “location, location, location” doesn’t apply. Instead, it’s about “proximity, people and power,” says Thompson. Companies need proximity to inbound suppliers, outbound customers, and labor, as well as power.
For example, if a company shifts sourcing from China to India, its products may arrive at the East Coast ports in the United States, rather than the West Coast ports. The distribution network will need to consider both the inbound and outbound product flows.
Rather than move fully finished products near the consumer market, companies may bring their products in an unfinished state and postpone final production, Colehower says. So, a company might make a basic printer and postpone final assembly of the power supply until it’s in the market, given differing electrical outlets between countries. This limits the investment in inventory, protects against market risk, and improves production throughput because the focus is on one size and/or style.
The Question of Nearshoring

Automation has driven job losses in manufacturing, but it may also help bring jobs back in less labor-intensive industries such as automotive, aerospace, and semiconductors.
Will the current supply chain disruptions accelerate U.S.-based companies’ interest in nearshoring or reshoring? Experts are divided.
To be sure, the closer products are made to end consumers, the less time and money spent transporting them, and the less risk of disruption. “This sort of shift back to regionalized sourcing and manufacturing makes all the sense in the world, regardless of tariffs, regardless of a pandemic, regardless of geopolitics,” Thompson says.
If America can work productively with Mexico and Canada, the three countries together could become a robust force and reduce their reliance on China and Southeast Asia, Reuter says. At the same time, “it takes a little while to turn the ship,” she adds.
Moreover, labor shortages and a lack of manufacturing knowledge may mean it’s not viable to produce many products in the United States. “You can’t just bring someone from the street and say, ‘Start making this tomorrow,’” Kazzaz notes. Reshoring on a major scale won’t happen.
Many of the job losses in manufacturing over the past few decades have been due to automation, rather than globalization, Amling notes. Ironically, automation may help bring jobs back in industries that are less labor-intensive and automated, like automotive, aerospace, and semiconductor manufacturing.
“It’s through modern automation solutions that the United States can regain our manufacturing mojo in select industries,” he says.
Keep an Eye on the Basics
Tactics such as adding buffer stock and diversifying suppliers boost the resilience of global supply chains, yet they also increase costs.
“You need to be very measured and very balanced about how you execute these initiatives, or you will end up going out of business the old-fashioned way, which is by being uncompetitive,” Amling says.
Because even solutions to today’s global supply chain challenges can introduce new challenges, no problem is ever permanently solved. Instead, supply chain organizations must continually evaluate multiple scenarios and prepare contingency plans.
As Kazzaz notes, “Supply chain managers are never done.”
Pergolux’s Transparent, Global Supply Chain
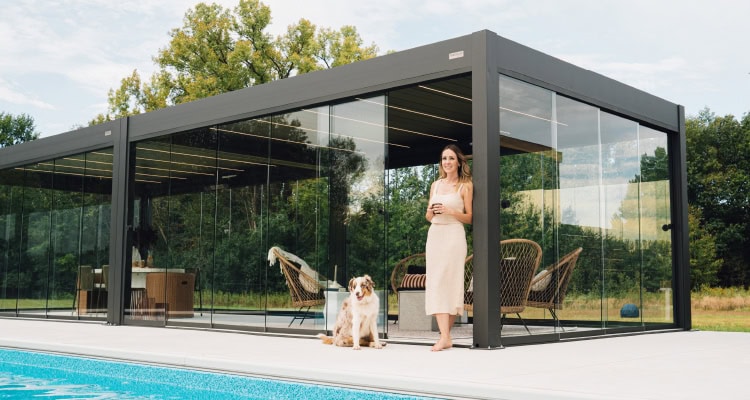
By sourcing and operating in multiple locations around the world, pergola company Pergolux is able to offer personal customer service and quick delivery at an affordable price.
Pergolux designs, makes, and offers pergolas in more than a dozen countries, including the United States. It leverages a China+ strategy, with factories also in Poland and Vietnam, as well as some operations in the United States, says Tim Heneveld, country director with the Norway-based firm.
With an eye on tariffs, Pergolux began shifting some operations from China more than one year ago, Heneveld says. The company also began making strategic purchases to minimize the impact of future tariffs.
Pergolux also continually evaluates adding suppliers or manufacturing facilities. As the cost of relying on others and operating a diverse supply chain increases, it may make sense to consider boosting internal sourcing and manufacturing capabilities, Heneveld says.
Artificial intelligence is helping Pergolux with everything from demand planning to warehouse layouts. “With data-centric information, AI can really help and save a lot of time and analytical manpower,” he adds.
As important, Pergolux is transparent about its diverse supply chain. By sourcing and operating in multiple locations, while monitoring and auditing for sustainable manufacturing practices, Pergolux is able to offer a premium product at an affordable price.
“That transparency,” Heneveld says, “is what the consumer is reliant on.”
Dangerous Goods Shipping: Make Certain You are Compliant
By Erin Gaul, Senior Consultant, Labelmaster
Here’s a hot take from someone who has worked in dangerous goods (DG) for 30 years: the secret to maintaining a strong compliance function is simple—employee education and training. A well-trained and confident workforce means a safer supply chain and a more compliant and profitable company.
To build a knowledgeable workforce that takes ownership of safe practices, companies should:
- Invest in employee training. DG shipping can come with high pressure situations that require serious accountability. Regular education on regulations ensures compliance and builds confidence within teams, allowing them to shine.
- Develop the right DG leaders. Appointing a knowledgeable DG ambassador within your organization helps drive best practices and fosters an ongoing culture of compliance.
- Provide hands-on learning. Practical experience with modern DG tools and technologies helps teams stay ahead of regulatory changes and industry advancements. This also increases employee satisfaction and reduces overall stress, as employees will feel that they are properly equipped to understand shipping requirements.
Shipping incidents—such as leaking packages, improper labeling or packaging failures—can result in serious safety hazards. We’re talking danger to the public, environmental damage and negative press for your brand.
Well-trained and educated employees are critical thinkers, able to recognize potential shipping risks early and take preventative action to avoid accidents that could tarnish the company’s image. And when employees receive the right education on DG shipping, they feel empowered to deliver better service and stronger overall job performance. This also means they are less likely to make mistakes that result in disciplinary action, which also helps reduce employee turnover.
Here are three proactive steps to improve your compliance.
- Work with a DG specialist and ask for an assessment of your shipping operation. An assessment will help identify deficiencies that could lead to errors and violations. It will also identify your modal training needs. Even if the assessment results in No Deficiencies, you will have peace of mind in your operation.
- Create a corrective action log and commit to it. This shows your due diligence and allows your quality management system to become engaged. It also proves to any federal auditor to you are actively working on a solution to a problem they’ve identified. For example, consider installing DGIS, a hazmat shipping software, to avoid paperwork errors.
- Train your employees to the regulations and to the processes you’ve established. Audit your processes twice a year and try to poke holes in them with different scenarios.