GOOD QUESTION: What’s One Transportation Metric Shippers Should Pay More Attention To?
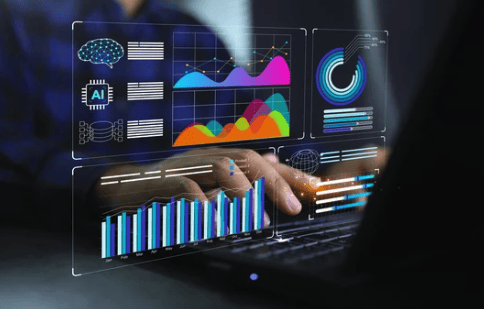
While on-time delivery remains a top answer, industry insiders point out other transportation metrics that merit attention and closer consideration.
Perfect order ratio measures the ability to deliver products and services as promised. It is the percentage of orders delivered on time, in full, undamaged, and defect free as a percentage of the total orders delivered. And I like to add: No billing errors from your carrier.
–Nicole Glenn
Founder & CEO
Candor Expedite, Inc.
The time it takes to empty a container at a warehouse. The ability to make sure containers are emptied in time results in less exposure to fees like per diem.
–Toni Ann Careccio
Chief Customer Officer & Board Member
PortPro
On-time delivery, always. The entire goal of the supply chain is to create a delightful customer experience.
–Michael Johnson
CEO
Metrc
Fuel surcharges. Prices are volatile and can fluctuate significantly, affecting shipping costs. By tracking fuel surcharges via getting quotes from carriers, monitoring prices, and negotiating with carriers on lower surcharges, shippers can save money on shipping costs.
–Chella Palaniappan
President, Client Services
Trigent Software
Missed appointments. Shippers who drive more than 97% of all activity through a transportation management system can see scheduled load fulfillment rates of over 90%, implying missed appointments are less than 10%. This reduces labor, improves inventory accuracy, minimizes detention fees, reduces CO2 emissions, and improves retail on-time and purchase order fulfillment scores.
–Barak Bar-Cohen
Founder and CEO
Sojo Industries
First-pass yield is the number of shipments that cycle through without further handling. If a shipment is rebooked/rescheduled, or the corresponding documentation must be revised/resent, it’s considered a defect. If your overall rolling throughput yield is low, a shipper will be challenged to leverage automation or enjoy handling costs from 3PLs.
–Andrew McLoone
Executive Director
PSA BDP
Rate of land consumption. It is critically essential to sustainable operation because excessive land use for transportation infrastructure can lead to environmental degradation, habitat loss, and increased carbon emissions.
–Giorgio Ferdinandi
Head of Procurement
Linnea SA
Your carbon footprint. Incorporate sustainability into carrier selection. Partner with providers who offer dashboards or applications that track emissions so you can identify and act on opportunities to reduce environmental impact.
–Phil Sullivan
VP, NA Enterprise Managed Services
Odyssey
Your customers’ satisfaction with the carriers you are selecting. There can be assumptions the receiver/customer is happy, but if the carrier is not doing a good job on delivery (product condition, driver attitude, on-time, etc.) then you may lose that customer to another supplier.
–Mitch Luciano
CEO
Trailer Bridge
It needs to be on-time delivery performance if shippers can only focus on one transportation metric. Customer experience is foundational for every business. Delivery performance is the last thing that customers see and heavily influences their perception of the entire buying experience and the overall relationship with the business.
–Chris Jones
EVP of Industry
Descartes
Location of Inspection and Fumigation Services. Streamlining regulatory processes through efficient dockside USDA and Customs inspections not only accelerates clearance but also minimizes unnecessary transportation distances and wait times. This optimizes shipment costs by avoiding offsite cargo transfers and reloads.
–Carla Stone
President
World Trade Center Delaware
Shipment quality. Poor shipment quality requires excessive manual labor for unloading—needlessly adding time and costs. Similarly, damaged goods, having absorbed order acquisition, fulfillment, and transportation costs, exacerbate shipment quality issues by further eroding margins.
–Rob Small
Senior Solutions Expert, Supply Chain
Inmar
Tender lead time to ship date. Provide carriers ample time to meet your expected ship date, which includes scheduling appointments, confirming shipping details, arranging drivers, and finding backhauls. In general, more lead time results in better service and pricing.
–Michael Link
Chief Supply Chain Officer
RJW Logistics Group
Time to book. Faster booking—via services like autobooking—enables a better shipper experience and more transparency with buyers, ultimately resulting in better customer retention.
–Heather Hoover-Salomon
CEO
uShip
That’s So Yesterday
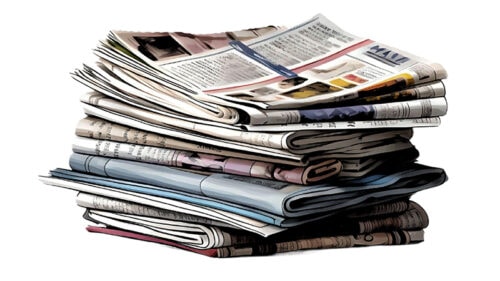
While traditional transportation performance metrics have a place in process improvement, relying on them alone is a bit like reading yesterday’s newspaper.
Shippers today have an opportunity to leverage global positioning in predictive analytics, enabling more accurate estimated arrival times than ever before, and integrating comprehensive risk assessments of financial, social-political, and climate risks.
–Tony Harris
SVP & Chief Marketing & Solutions Officer
SAP Business Network
On Time in Full. It is a combined metric bringing together two key variables, which when fully executed upon brings an optimal customer experience. When either variable is below expectations, it can equate to significant losses in revenue.
-Theo Bielowicz
Director of Sales,Transportation & Logistics
Brother Mobile Solutions
On-time pickup percentage of their carrier partners. Scrutinizing this critical yet often overlooked metric can improve production planning, reduce dwell times, and increase on-time delivery percentages, all of which will drive greater supply chain efficiency.
–Tyler Brown
Director of Business Development
Arrive Logistics
Chain of custody completeness. Amid recent ESG regulations like the UFLPA and German Supply Chain Act, missing product information documenting chain of custody is leaving shipments vulnerable to lengthy port detentions and hefty fines. Retailers must make sure these records are complete before shipping.
–Eric Linxwiler
Sr. Vice President, Retail Solutions
TradeBeyond
Perfect order delivery is a valuable metric that analyzes data points which can measure the performance of the entire process of the movement of goods throughout the supply chain from manufacturer to end customers. It looks at performance indicators such as on-time delivery, order fulfillment, production efficiency, and other critical data elements that can help identify where a failure occurred. This can help create procedures and processes that can be implemented to minimize disruptions and interruptions in the future.
–Steve Dombroski
Director of Food and Beverage Markets
QAD
Optimized turnaround times remain essential as delays can create unnecessary costs, disrupt supply chains, and hurt customer satisfaction. Shippers can tap on the skills, network, flexibility, and resourcefulness of established logistics service providers to overcome transportation issues and ensure the seamless and timely movement of goods from origin to destination.
–Shanaka Fernando
Managing Director
GAC North America – Logistics
On-time pickup metric. If the product does not ship in time to hit the carrier’s linehaul schedule from origin, regardless of mode, the shipment has a high likelihood of not meeting the consignee’s delivery expectation.
–Melissa Somsen
Chief Commercial Officer
AFS Logistics
Carbon emissions. As the world becomes more conscious of environmental sustainability, measuring and reducing carbon emissions in transportation is crucial. It helps mitigate climate change and supports the adoption of greener practices within the supply chain.
–George Maksimenko
Chief Executive Officer
Adexin
On-time delivery. Depending on your sector, you can be fined if something arrives late. Specifically, visibility into that last mile of delivery is key. Further, your customer experience should be a major, if not the ultimate priority—the ability to enhance on-time delivery adds value from that perspective as well.
–Bryan Gerber
Founder & CEO
HARA Supply
Digital isn’t really digital. Most digital platforms lack skilled employees with deep logistics knowledge to back up their work. Digital is wonderful when you have the human intelligence to adapt and understand the always-moving freight industry.
–Drew Herpich
COO
TI & NTG
On-time delivery rate is a key metric more shippers should be paying attention to. Situations occur daily that delay a shipment, but communication is key and delivery times can be adjusted.
–Eric Vasquez
Owner
Veterans Logistics Group
Freight policies/freight recovery. Unmanaged freight cost recovery can quickly erode profit margins. Smart companies revisit their policies frequently. Without doing so, macro-economic climate changes can create a revenue wave without carrying margin with it. This was the case for many companies in 2022.
–Eric Elter
Director of Information and Technology Services
KDL Logistics
Shippers should be tracking their carbon footprint. While the SEC has tabled their earlier Scope 3 emissions proposal, it is highly likely to come back in some form.
–Joe Adamski
Senior Director
ProcureAbility
Average transportation costs. Not just the rate, but understanding how transportation costs impact a dealer’s inventory turn, customer satisfaction, and even the floor plan, can help improve a dealer’s bottom line.
–Mary Bartlett
Director of Business Development
Montway Auto Transport
Tender acceptance/rejections. This can give shippers an idea on if the market is trending in favor of carriers or shippers. If tender acceptance is high, then that can be a good time to do annual bids.
The shipper can use their own shipment data to track this metric, but if they do not have a nationwide network then it may be best to use publicly shared information from industry data sources.
–Eric Masotti
President, Logistics
Trailer Bridge
Supply chain flexibility is essential as market conditions can change rapidly. Drivers, dispatchers, trucking companies, and brokers all discuss dwell time as it impacts the entire network, and often not just that single trailer or truck. All too frequently, one delay pushes out the entire network.
–Sean Burke
CCO
Echo Global Logistics
Driver parking.While it may seem like a simple answer, this shortage affects many links of the supply chain. From driver hours (being wasted to find a legal truck stop) to shipper bottlenecking (an issue made worse by missed appointment times), the men and women moving America and beyond would become more efficient if this obstacle were greatly diminished or eliminated.
–Evan Wheeler
VP of Brokerage Operations
TA Services
Invoicing accuracy. While most invoices will match what a shipper had been quoted, some will not. Those invoices that don’t, can represent systemic issues, either with the shipper or carrier, that will warrant a deeper dive into root causes.
–Kevin Day
President of LTL
AFS Logistics
On shelf availability (OSA) from the store and product utilization/consumption in the home but visible not just to retailers but everyone in the supply chain (using ambient IoT). Demand chain metrics should be accessible and used to orchestrate the next generation of supply chains.
–Antony Yousefian
VP Climate & Circularity
Wiliot
Network emissions are an emerging metric in goals across forward-looking organizations. While each organization is at a different stage in its decarbonization process, logistics leaders can show their c-suite the potential emissions reduction opportunities in their network today. A trusted partner can accelerate setting science-based targets and decarbonizing transportation networks.
–Jenny Vander Zanden
Chief Operating Officer
Breakthrough
Delivery and delivery-to-promise dates. Are we delivering on customer service demand at the risk of spending more on transit, cost per case, CO2 emissions, human energy, or electrical power? Provide a choice to the consumer, retailer, and distributor then deliver to that model.
–Ann Marie Jonkman
PMP, Senior Director, Global Industry Strategies
Blue Yonder
Average cost per shipment impacting their COGS (cost of goods sold). Then dependent on the mode, LTL ($/Lb), parcel ($/Pkg), truckload ($/mile) and international ($/container).
–Dean Jones
Chief Channel Development Officer
AFS Logistics
Dwell on This
Dwell time is clearly the one thing shippers need to dwell on. On port containers, the dwell cost is at times as much as the final mile cost. Per the Department of Transportation report, dwell time at shippers’ docks costs carriers $1.1 to 1.3 billion per year. Essentially it shows a lack of planning at various levels in an organization and creates an impact on future RFPs in the form of increased carrier rates. And while the penalty cost is bad, the greater impact is on the reputation of the shipper.
–Reo Hatfield
VP of Corporate Services
TA Services
Paying more attention to dwell time can give shippers early warning of potential backups in the supply chain, allowing them to work with logistics partners to identify and reduce bottlenecks. Container dwell times at ports or railyards can be a useful indicator for overall supply chain health as well.
–Tony Pelli
Practice Director, Security and Resilience
BSI
High dwell times indicate inefficiencies in logistics processes, leading to potential delays and increased costs.
–Srini AV
Transportation and Global Trade Practice Director
Gaea
Considering dwell time information at the very start of a shipper/carrier relationship results in stronger overall plans.
–Kelly Williams
Enterprise Product Lead
Trimble
By reducing dwell time, you can reduce detention and demurrage charges, improve your capacity utilization, streamline operations, and overcome driver shortage issues, ultimately improving your overall performance. It also has a positive impact on all aspects of the supply chain, reducing environmental impact and supply chain imbalances.
–Amit Prasad
Chief Data Science Officer
Transportation Insight
Getting drivers in and out of pickup facilities efficiently is critical. Ensure the carrier receives accurate information regarding service requirements, shipment details, and capacity needs. Check each shipment for proper in-transit packaging, stage the freight for convenient access, and have the driver’s paperwork complete and ready.
–Chase Smith
Vice President, Carrier Services
MODE Global