Highlighting DC Efficiency
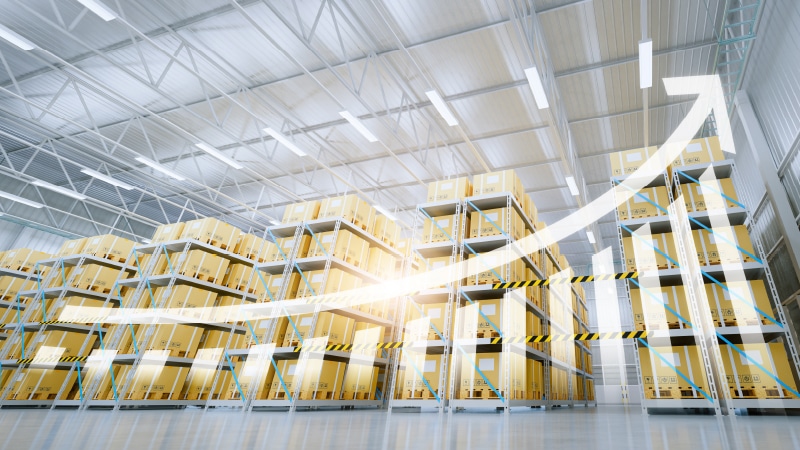
Consumer demand for order fulfillment speed and accuracy highlights the central role distribution centers now play in the supply chain. DCs are stepping up by tapping into sophisticated technology and resources to transform and optimize operations and boost efficiencies.
For years, distribution centers attracted little attention. They often were dark, dirty, and dingy. The buildings were hot in the summer, cold in the winter, and senior management rarely visited.
Distribution centers were “a back-closet kind of operation,” says Gary La Point, professor of supply chain practice at Syracuse University. “That has all changed now.”
“Today, the DC is the gem in the crown for a lot of companies,” says La Point, a former warehouse supervisor for Xerox. “It’s where a lot of supply chain technology—robotics, new picking systems, new warehouse designs—is being developed. It’s a showcase for what you can do.”
Multiple factors contribute to the DC’s increased prominence. One is that “inventory is very expensive and companies realized they weren’t paying much attention to this huge expense item,” La Point says.
Another factor, which has particularly accelerated the advances DCs have made in recent years, is the transformational shift that has occurred in consumer expectations.
Ecommerce Intensifies Focus on DC Efficiency
DC efficiency intensified in importance with the rise of ecommerce and increased expectations for faster and more accurate order fulfillment, especially after the pandemic.
“Many companies feel the pressure to optimize operations and increase productivity to meet customer expectations,” says Abdil Tunca, senior principal analyst, Gartner Supply Chain Practice.
“Also, inefficiencies started turning into capacity issues,” he says. “Growing demand for faster response, increases in volume seasonality, and the introduction of new products are pushing the limits of warehouse capacity.
“Warehouses are under pressure to process more inventory faster than before, leading in many cases to capacity constraints,” Tunca adds.
Technology Enables Improvements
A host of developments are helping to create much-sought-after DC efficiencies.
“After the pandemic, businesses started investing more in process standardization, error and waste reduction, and technology such as automation, robotics, inventory management systems, and labor management systems,” Tunca says.
“We also see some of the early AI use cases such as dynamic warehouse slotting, predictive maintenance, and advanced analytics in logistics through warehouse management systems,” he adds. “In today’s competitive market, these solutions have started becoming a necessity rather than an option.”
Historically, distribution centers have faced major inefficiencies in the amount of travel required to operate inside their walls—including workers both walking and driving equipment, such as forklifts, great distances, La Point says.
Particularly problematic is when deadheading occurs, meaning neither the worker nor machine is carrying any product during their travel. “Someone driving a forklift with nothing on the fork is not productive—they’re inefficient,” La Point says.
“In the old distribution centers, all kinds of deadheading took place, but there is a lot of effort now to reduce walking time, travel time, and deadheading time,” he says. “You find a lot of DC efficiencies from there.”
In addition, mistakes are one of the most serious causes of inefficiency. For instance, when workers pick the wrong part and that part is then shipped, it’s “a disaster,” says La Point, leading to labor hours and costs to fix the error.
“The most important efficiencies in distribution centers now are about picking the right part and minimizing missed picks,” La Point says. Technologies—such as pick-to-light systems, smart glasses, and RFID solutions—play a key role in those efforts.
Here’s a look at two providers of equipment solutions that demonstrate the importance of combining technological advances and improved processes to solidify efficiency gains in the distribution center.
Gorbel’s Dock Door Solutions Provide Far-reaching Benefits
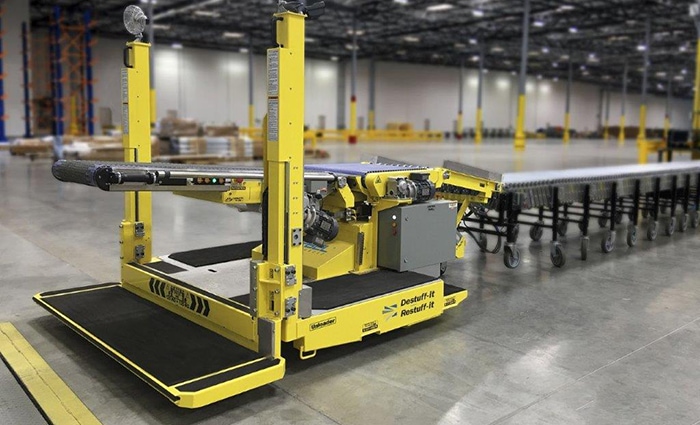
Gorbel’s portable ergonomic conveyor systems—Restuff-it™ and Destuff-it™—help workers unload floor-stacked products from trailers and containers.
The dock door area is a critical focal point of the distribution center. In fact, it helps set the tone for the entire operation. If the process at the dock door is an efficient one, it bodes well for the rest of the DC and can create new efficiencies elsewhere in a facility.
Gorbel, a crane, ergonomic lifting, and fall protection manufacturer based in Fishers, New York, offers portable ergonomic conveyor systems—Restuff-it™ and Destuff-it™—that are built to maximize efficiency at this deceptively complex juncture in the shipping journey.
Both systems help workers unload floor-stacked products from trailers and containers, and Restuff-it™ is a bi-directional unit that also helps with loading products.
The Restuff-it™ and Destuff-it™ systems help clients unload trailers much more quickly than before, reducing the number of workers needed for the process and cutting labor hours by approximately 50%—supercharging efficiency and creating a clear return on investment, says Anton Sawatzky, warehouse solutions sales manager for Gorbel.
“We work closely with our customers, and we know how much speed and safety at the dock door matter to them,” Sawatzky says.
Gorbel’s solutions are the only ones in the dock door field that have both a pivoting conveyor that ensures easy access to the conveyor and a platform that raises and lowers to ensure operators never have to reach above their heads for lifting, Sawatzky says.
Together, those features make unloading and loading at the dock door not only markedly safer but also markedly more efficient, he adds.
Flexible Solutions Boost Safety
In addition, the solution is fully mobile. So, instead of needing to dedicate the system to a single dock door, clients can use the solution at multiple doors, moving from trailer to trailer without the down time of waiting for a truck to pull away an empty trailer and restage the dock with a full one.
The solutions also boost safety. The dock door remains the place where the largest percentage of warehouse injuries occur, Sawatzky says. The difficulty of the work can limit the labor pool for open positions. Gorbel’s solution makes the work more appealing and provides a competitive advantage with the workforce.
“Using a machine to reduce the strain of lifting and twisting when workers are carrying a box—all while they’re under duress because they’ve got to move as quickly as possible to meet the budgeted timing for the work—helps a great deal with employee retention,” Sawatzky says.
“Warehouses can differentiate themselves with a focus on making the work safer and easier,” he adds.
Restuff-it™ and Destuff-it™ are drop-in solutions, but Gorbel team members walk clients through the systems and how to incorporate them into their unique operation to take advantage of the efficiencies they can introduce, Sawatzky says.
Often, Gorbel will provide a solution on a rental basis, helping clients to get acquainted with it and understand how quickly products come out of the trailer so they can make necessary adjustments elsewhere in their operations to maximize their gains.
“From a customer service perspective, right from day one we bring a lot of experience with dock door solutions to the table and bring ideas to the customer that will make them as efficient as possible,” Sawatzky says. “We know the difference that our solutions can make for them.”
Engineering Innovation: Emphasizing Agility and Efficiency in Automation
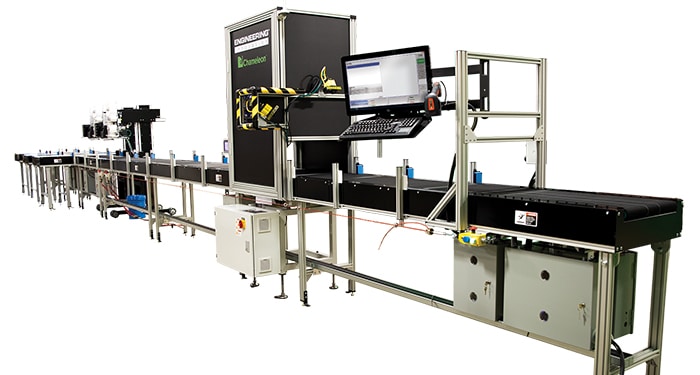
Engineering Innovation’s Chameleon parcel-processing solution can shift and change as volume and market requirements fluctuate.
The advance of innovation is constant and rapid in today’s distribution centers, and those who operate DCs must be ever prepared to accommodate that progress, says Don Caddy, CEO of Engineering Innovation, an Indiana-based provider of automated mail and parcel sorting equipment.
“Whatever you’re doing today, in one year or two years it’s going to be different,” Caddy says.
“There’s just too much changing in the world for that not to be the case,” he notes. For that reason, Engineering Innovation’s products each have a modular design that makes them readily adaptable.
Companies operating DCs should emphasize a dynamic approach in today’s climate. “You need to work with vendors that can be responsive so that you can make incremental changes to your process more rapidly,” Caddy says. “You don’t want to be stuck with a solution that becomes outdated and you say, ‘Yeah, we could do it better, but we’re still paying off this project so we can’t throw it away yet.’
“Change is constant—processes change, people have new ideas, and the industry is just moving too rapidly for people to get locked into a huge investment that starts out with a benefit but ends up being an albatross,” he says. “That’s why while we’re helping our customers automate, we also have to make sure we’re helping them be agile.”
For example, an Engineering Innovation customer bought one of the company’s automated sorting machines solely to scan and sort packages but later developed a need to weigh those packages before scanning them.
Instead of requiring a new machine, Engineering Innovation spent a day adapting the equipment, and “that machine suddenly became a different machine,” Caddy says.
Rather than eliminating labor with automation, Engineering Innovation focuses on multiplying the effectiveness of labor, including by improving accuracy.
Engineering Innovation integrates its solutions with customers’ existing processes rather than attempting to change the way they operate and asking them to rearrange their approach around Engineering Innovation’s equipment.
“We tend to be more targeted, and we go in and ask, ‘How can we help without disrupting your entire operation? How can we make the people you have be more effective and then leverage your available staff to get more done?’” Caddy says.
Engineering Innovation offers solutions that can provide “the most bang for our clients’ automation dollar,” says Caddy.
Spotlighting Long-term Success for Customers
“We want to focus on things that machines do well that can help people do what they do better and more accurately,” Caddy says.
“One of the big keys is establishing a relationship with customers and actually visiting and talking to them about what they do, how they do it, and what their goals are. Because we understand that, it allows us to help them as much as possible,” he notes.
In that way, Caddy says Engineering Innovation emphasizes long-term success for its clients.
“Sometimes, customers will come to us wanting product A and then we go and look at their operation, and we see that there’s a way bigger opportunity to do something with product B,” Caddy says. “We take the consultative approach, so that we can find those opportunities for them. We play the long game of supporting customers and helping them succeed as much as possible.”
Take a Strategic Approach
Gorbel and Engineering Innovation each stress the importance of integrating new solutions with a strategic purposefulness. Too many DCs are transformed without that considered intent.
“I’ve seen companies that spend tens of millions of dollars reconfiguring their DCs, but fail to consider that culture aspect of it,” says La Point. “They never achieve the level of productivity they were supposed to achieve.”
Similarly, some companies take large existing buildings designed for another purpose—often manufacturing—and adapt it as a distribution center. The building inevitably will not have been designed in a way that allows for maximizing DC efficiency.
For instance, a former manufacturing plant likely will have dock doors on opposite sides of the building—a problem for a distribution facility.
Technology brings opportunities but companies must be smart and strategic in how they adopt those solutions.
“Technologies have different maturity and adoption levels, benefits, and risks, and they mean different things to different supply chain domains and participants,” Tunca says.
“Companies struggle to find, evaluate, and prioritize the most relevant innovative technologies for their needs,” he adds. “Once they prioritize their needs, the goal should be to look for the best fit for the business rather than the best solution in the market.”
A concerted and complete effort is necessary to identify and realize new DC efficiencies.
“The correct approach maintains a balance between people, processes, and technology,” Tunca says. “Organizations sit on this three-legged stool; achieving a balance requires a holistic and strategic approach. Businesses should align their goals, communicate effectively, and continuously adapt their strategies to optimize their DC operations.”