Is the Logistics Sector Ready for the COVID-19 Vaccine?
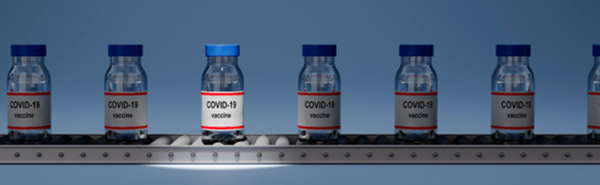
The last mile will have to accommodate the reliable distribution of the billions of vaccines that providers will manufacture and ship in 2021. Here are the obstacles facing the supply chain.
The December peak season brought a new set of challenges. As COVID-19 vaccines received FDA approval in late 2020, logistics operators faced the daunting task of distributing vaccines around the world. While the FDA was able to fast-track the approvals process and many vaccines have already shipped, changes in the last mile are still ongoing to accommodate more reliable distribution of the billions of vaccines that providers will manufacture and ship in 2021.
The supply chain faces the following obstacles:
1. Supply Chain Cold Storage
Vaccines require proper storage conditions at all points in the supply chain to ensure their efficacy when they reach the patient. This isn’t usually overly challenging—the flu vaccine requires refrigerated storage between 35°F and 42°F, for example.
The leading COVID-19 vaccine has more stringent requirements. The Pfizer and BioNTech mRNA-based vaccine requires cryogenic storage below -90°F. Cold storage has been underserved in global industrial real estate for decades, and cryogenic cold storage even more so. Low availability makes it difficult to regionally distribute and store vaccines.
Other leading vaccines, such as Moderna’s mRNA vaccine, have more standard storage requirements and last up to six months in a standard freezer. Ideally, ongoing upgrades to last mile capabilities and varying storage requirements between vaccine types will be enough to avoid significant disruptions in vaccine distribution.
2. Dry Ice Shortage
Due to a lack of cold storage availability, Pfizer ships directly to health agencies and hospitals. Storing vaccines at appropriate temperatures is challenging enough for the supply chain, but near impossible for the medical facilities where patients will receive the vaccines. Once removed from cryogenic storage, the vaccine lasts about five days.
The solution to this problem is special packaging from Pfizer, which can maintain appropriate cryogenic storage temperatures for up to 30 days if refilled with dry ice every five days. Dry ice is typically created by freezing CO2 byproducts recovered from oil and gas and ethanol production. These sectors have been making less fuel over the past year because of the pandemic, resulting in less available CO2 needed for dry ice production.
3. Distributing Related Equipment
The medical supply chain still hasn’t recovered fully from the shortage of personal protective equipment (PPE) it experienced in early 2020 at the onset of the pandemic. Many medical professionals still struggle to reliably source N95 masks, gloves, face shields, gowns, and other critical PPE needed to protect medical workers as they vaccinate the public.
In addition to the standard PPE, the vaccine rollout has caused a rush on other ancillary gear needed in vaccination operations, such as alcohol wipes, syringes, needles, and bandages. While manufacturers of these goods fortunately had time to prepare, it’s currently unclear how well the supply chain will hold up to long-term vaccination efforts over the next several months.
Bending But Not Breaking
The supply chain has been preparing for this moment since successful vaccine development began to appear likely. Logistics providers, airlines, ground carriers, healthcare networks, and manufacturers have all come together to find innovative ways to bring vaccines from the production floor to the people who need them.
While vaccine distribution isn’t without its obstacles, 2021 still looks much more positive than the year before.