Manhattan Active WMS for a Leading USA Retailer
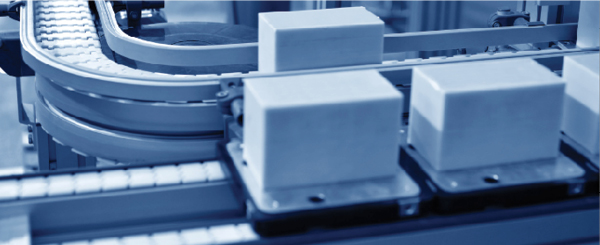
A major retailer sought to modernize their supply chain operations with a cloud warehouse management system and turned to ITOrizon as their system integrator. The result was a seamless integration.
The Goal
The customer had an all-encompassing goal to modernize their supply chain operations on a cloud platform while expanding their warehouse throughput to their retail stores and delivering an authentic omnichannel experience with initiatives such as BOPIS.
The warehouse management solution got identified as the first application for the supply chain transformation journey. The customer chose Manhattan WM Active as their new WMS solution with a strategy of phased deployment by warehouse and selling channel. Overall, 4 phases were planned, starting with their West Coast DC operations.
The DC is a 600,000-square-foot facility split between retail and e-commerce channels. It is a fully automated warehouse equipped with:
1. Put-to-light stations
2. Print and apply machines
3. Case sealers
4. Fluid loading lanes
5. Conveyors with routing capabilities
Their existing supply chain ecosystem is very rich and supported by a mix of on-prem and cloud products such as JDA, Oracle RMS, Manhattan Distributed Order Management (DOM), Manhattan Integration Framework (MIF), and Manhattan Extended Enterprise (EEM).
The Challenges
1. Retrofitting existing integrations with new cloud WMS software
- Leverage existing integrations across their SCM ecosystems and bring the new WMS (MA Active) as a “plug and play” with minimal time and effort
- Design the new WMS—MHE integrations by repurposing the old MHE integration code
- Lack of technical subject matter experts for in-house legacy SCM applications and cloud WMS implementation specializations
2. Designing and implementing existing warehouse business use cases to a new system
- Configuration and setup were drastically different than that of the old WMS. On top of that, the look and feel of the new WMS was also different
The Solutions
As the customer’s prime system integrator, ITOrizon got a blanket contract to establish the new warehouse operations, implement the new WMS and required integrations, and ensure fully functional systems as part of their commitment.
ITOrizon analyzed the existing warehouse processes and the end-to-end business processes across all SCM systems to get the complete picture before establishing the new processes or proposing any configurations in WMS.
Our team went the extra mile to carefully review and cross-verify configurations to detect the gaps and bugs ahead of schedule. One such situation occurred in PIX design where existing integrations could not scale up for the new WMS PIX features. The ITOrizon team proposed an alternative design without impacting the project schedule.
We spent extensive time developing SCI to present the receiving, shipping, allocation, packing, inventory analysis, and inventory reconciliation statistics to build customer confidence in the new WMS.
ITOrizon’s cloud expertise, specifically with Google Virtual Private Cloud, was used to set up the replica copy of the production WMS DB. This allowed us to access the PROD (live) data, analyze the operations process, and troubleshoot data inconsistencies to take proactive measures.
To learn more:
email: [email protected]
phone: 770-769-0829
web: www.itorizon.com