Cold Chain Automation Surges; AI Hits the Back Office; DCs Go Mega & Other Supply Chain News
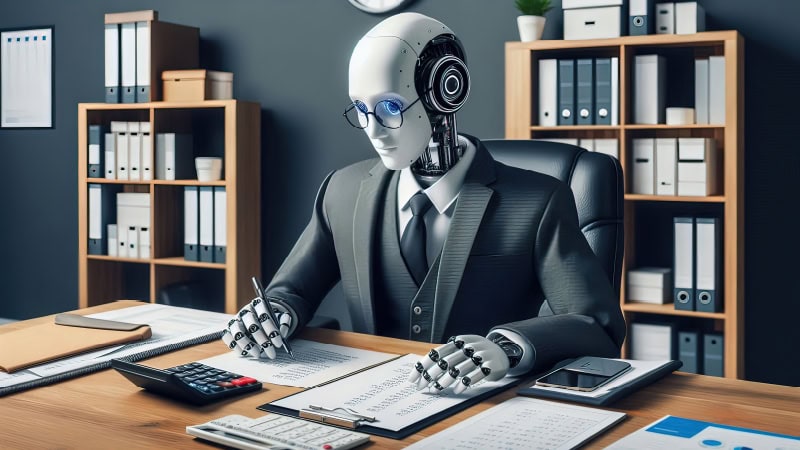
What’s trending in logistics and supply chain today? Here’s a roundup of research findings that are making waves.
AI: The Back-Office Backbone?
As further proof that artificial intelligence (AI) is reshaping logistics operations, a new study looks at its importance for back-office functions in the supply chain—with 98% of respondents saying AI is useful, important, or vital to their business.
The survey, conducted by Deep Analysis and co-sponsored by Hyperscience and the Council of Supply Chain Management Professionals (CSCMP), reveals that companies are leveraging AI-powered solutions to streamline workflows, reduce errors, and enhance overall decision-making for back-office tasks.
Here are some key findings from the survey:
- 82% of survey respondents report a high volume of manual processes still in use, highlighting automation opportunities.
- 70% say they are willing or very willing to invest in an AI-optimized system for back-office functionality.
- 45% of organizations are using AI, with 13% in the operational stage and 32% in the advanced or transformational stage.
- 34% of respondents are motivated and planning to pilot AI solutions but have not yet fully deployed them.
Despite widespread enthusiasm for AI, challenges remain. Many organizations struggle with legacy systems, data accuracy, and the need for skilled talent to maximize AI’s potential. Nearly 65% of respondents say their organizations are not fully prepared to implement AI at scale.
Mega Momentum
Bigger is better. That seems to be the consensus in the U.S. industrial real estate market, according to recent CBRE data that shows a notable rise in mega distribution center leases—1 million square feet or more—in 2024, driven by strong online sales nationwide.
The mega trend picked up pace with 49 such leases signed last year, up from 43 in 2023. This increase follows the first decline in mega leases in 2023, after peaking at 61 in 2022 during the pandemic-driven surge.
Overall, 40 of the top 100 industrial real estate leases were renewals, up from 30 the previous year. “This rise in lease renewals underscores a strategic shift in the market,” notes John Morris, president of Americas Industrial and Logistics at CBRE. “Companies are focusing more on stability and efficiency by extending existing leases in key logistics hubs.”
Additional insights from the report include the following:
Market share shifts (See chart below):
- Retailers and wholesalers now make up 38% of the top 100 leases, up from 30% previously.
- Food and beverage, automotive, and building materials sectors saw declines.
- EV manufacturers and building materials suppliers were less active compared to 2023.
- 3PLs maintain a strong presence, with 28 leases signed among the top 100.
Top markets for mega-lease activity:
- Inland Empire
- Pennsylvania’s I-78/81 Corridor
- Dallas-Fort Worth
Leasing Activity by Sector
OVERHEARD
Five to Thrive
Five competitive characteristics are needed for future readiness, according to a recent Gartner poll of top supply chain practitioners across industries and geographies. Chief supply chain officers say they need these characteristics to manage the future drivers of influence on the supply chain. They are:
1. Agility
2. Resilience
3. Regionalization
4. Integrated ecosystems
5. Integrated enterprise strategy
Interestingly, the survey shows just 29% of supply chain organizations have developed at least three of these key characteristics. How does your organization stack up?
Embracing Cold Chain Automation
The cold chain sector is experiencing a surge in automation—with the cold chain warehouse automation market expected to exceed $2 billion in revenue by 2030 (see chart, below)—as companies race to meet growing demand for efficient, reliable temperature-controlled logistics. That’s the takeaway from the latest Warehouse Automation Report from technology insights firm Interact Analysis.
Cold storage logistics has traditionally relied on manual labor—a costly and inefficient approach in a sector where precision and speed are critical. Today, automation is changing the game, with cold storage facilities turning to advanced automation solutions to keep goods moving seamlessly. Automated storage and retrieval systems (AS/RS), autonomous mobile robots (AMRs), and AI-driven warehouse management systems (WMS) are now optimizing everything from inventory tracking to order fulfillment.
The report highlights the following key drivers behind the boom in cold chain warehouse automation:
- Ecommerce growth: Online grocery sales are increasing, requiring faster, more reliable fulfillment.
- Rising labor costs and shortages: Automation helps reduce reliance on manual labor in harsh cold storage environments.
- Stringent food safety regulations: Tech-driven tracking can improve compliance and reduce waste.
- Energy-efficiency concerns: Smart automation helps minimize cooling costs and optimize storage space.
Automation in cold storage also comes with challenges: High upfront costs, integration complexities, and a need for specialized equipment can slow adoption, the report notes. What’s next? Interact Analysis predicts the industry will see greater adoption of AI-powered analytics, robotic picking solutions, and energy-efficient cold storage innovations.