WMS Enables Automation Orchestration for High-Volume E-Commerce Fulfillment
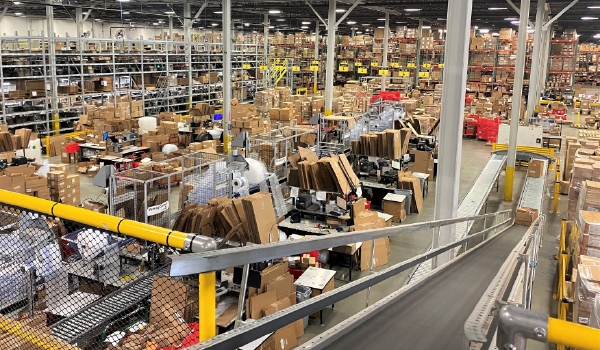
Case study in leveraging a warehouse management system to get the most out of a substantial, physical automation investment, in an existing distribution center.
THE CHALLENGE
“Order picking can constitute a significant portion of our operating costs. Processing orders quickly and accurately is a competitive advantage,” said Zander Brekke, Executive VP and General Counsel, of Mud Pie in Stone Mountain, GA. “We needed a WMS capable of bringing the brains to the machinery that is the company’s lifeblood.”
Inc. Magazine twice listed the innovative wholesale company as one of America’s fastest growing private companies. Responding to increased demand, Mud Pie made sizeable investments in physical automation at its 250,000-square-foot distribution center. But, they had not thoroughly considered enterprise system integration.
Mud Pie turned to QSSI, a respected technology development and consulting company, led and staffed entirely by professionals with firsthand warehouse operations experience. When QSSI was first engaged, Mud Pie had already implemented conveyor and sortation systems for piece picking, packing, and shipping, but the conveyance and sortation systems lacked the desired visibility and operational insights. Similarly, the company needed “intelligent” support for their automated storage and retrieval software.
The SOLUTION
“Steel is steel,” said Russ Schumacher, QSSI’s VP of Application Services, referencing the hard reality of working with an existing complex conveyor system. “You adapt the software to the steel, not the other way around.” To ensure that Mud Pie would see maximum returns from their significant capital investment, QSSI developed a multi-pronged strategy, involving both people and infrastructure-driven processes.
For example, QSSI made labor more efficient with task interleaving and wave planning. Schumacher’s team also equipped Mud Pie’s people with the right tools for the task at hand. They were there at every step of the transition—from pick-and-pass to more complex order picking/restocking methodologies (zone-batch-wave), using tablets and wireless handheld devices with pick-to-light technology.
With the implementation of the QSSI WMS (“PowerHouse”), Mud Pie gained insights into automation performance metrics (pile-on, pod-station visits, throughput, etc.) and order sequencing.
Diverse retailers mean diverse customer orders, which can lead to severe inefficiencies in how search and travel tasks are performed. It’s critical for a wholesaler to differentiate between oversized, non-conveyable items and conveyable items for warehouse pick flow.
In response, the QSSI team concentrated on the operational logistics of splitting an order. PowerHouse introduced pick pod selection and path planning protocols to improve automation controls. Pod repositioning protocols address the replenishment process.
Mud Pie continues to grow its business exponentially. Subsequent warehouse floor expansions (9,000 new locations!) build on the original efficiencies introduced by QSSI. The facility now contains four levels for picking. With Mud Pie, the QSSI team developed and implemented a high-bay, narrow-aisle picking concept to maximize the space for a new conveyor system: an impressive 24 pick modules, each 28 feet in length.
The PowerHouse dashboard was pivotal to the success of the narrow aisle picking concept. “When you can see all, you can direct all,” said Schumacher. “And, more importantly, you can direct with specificity.”
To learn more:
[email protected]
732-805-0400
qssi-wms.com