A Mobile Cure for the Warehouse Blues
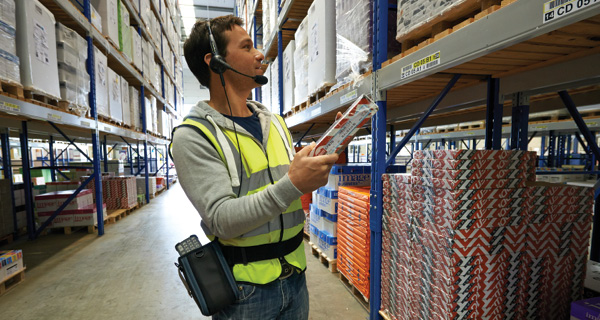
Companies are under constant pressure to improve warehouse efficiency and reduce errors. Mobile communications technologies help them rise to the challenge.
As the speed of business increases, and e-commerce fulfillment operations grow, companies face mounting pressure to improve warehouse efficiency, productivity, and accuracy. "Materials are moving faster, and the supply chain has to run leaner," says Mark Wheeler, director of warehouse solutions at Schaumburg, Ill.-based telecommunications equipment provider Motorola Solutions. "Warehouse accuracy and speed are more important than in the past, and errors are more disruptive."
Warehouse managers have had to adapt their operations to accommodate significant changes in the supply chain.
"Customer demand for personalization is driving an increase in the number of stockkeeping units, leading to intensified need for inventory visibility, accuracy, and efficiency," states From Cost Center to Growth Center: Warehousing 2018, a new report from Motorola. "Meanwhile, regulations call for more accurate product tracking and tracing, while growth of omni-channel transactions creates the need for increased inventory control; flexibility; and faster, more accurate fulfillment."
Mobile devices and applications such as rugged tablets, bar-code scanners, picking systems, and improved Wi-Fi capabilities specifically designed for the warehouse environment are helping warehouse managers and logistics personnel better meet such challenges. These devices and applications enable companies to track assets and shipments, boost picking and packing productivity and accuracy, execute transactions and processes, collaborate with internal and external partners, and improve supply chain functionality, productivity, and efficiency overall.
"Automated mobile tools in the warehouse are becoming essential for logistics, supply chain, and transportation management," notes Steve Wimsatt, director of business development and vertical markets at Sunnyvale, Calif.-based Ruckus Wireless Inc., a Wi-Fi networking equipment manufacturer.
E-commerce growth is a significant contributor to the demand for more speed and efficiency in the warehouse. The online retail market grew 17 percent globally over the past five years, and shows no sign of slowing down, according to consulting firm A.T. Kearney’s 2013 Global Retail e-Commerce Index Report. Meanwhile, market research company eMarketer’s latest forecasts predict worldwide business-to-consumer e-commerce sales will increase by 20 percent in 2014 to reach $1.5 trillion.
Managing Complexity
As consumers grow more comfortable ordering products on their laptops and mobile devices, warehouse operations become more complex. Instead of shipping one large pallet to a retail store, for example, a warehouse may now be tasked with shipping hundreds of small orders to individuals located all over the country—or even the world. At the same time, consumers are demanding faster delivery speeds.
Over the past few years, Brentwood, Tenn.-based third-party logistics (3PL) company OHL has experienced significant growth across all verticals, but specifically within the e-commerce sector, says Rob Thyen, OHL’s vice president of engineering. OHL serves a broad range of customers, and occupies 33 million square feet in more than 130 warehouses across the United States and Canada.
"E-fulfillment represents about 30 percent of our contract logistics business today, and it is our fastest growing segment," says Thyen. "It also presents unique challenges, such as high order and SKU counts. Those challenges push us to drive productivity and better manage our labor force to minimize errors."
In most of its warehouses, OHL uses Motorola handheld scanners for picking and putaway tasks. The 3PL also recently began testing new voice-driven software from South Jordan, Utah-based technology provider Wavelink Speakeasy. The device-based, multi-modal solution requires no middleware component or voice-specific hardware.
"The technology is resident on the Motorola scanners, so it has no interface, which eliminates the upkeep, support, and maintenance other information technologies require," says Thyen.
Using the voice-driven system has helped OHL increase picking productivity and accuracy. "The system verbally directs users to each new location, aisle, or bay, leaving little room for error," Thyen explains.
The technology is also proving beneficial when onboarding new personnel. "In one pilot, it took new employees three to four weeks of onboarding before they achieved the picking level of the rest of the workforce," says Dave Hauptman, OHL’s vice president of product management and marketing. "With the voice technology overlay, that time dropped to five to seven days."
Faster onboarding will be a significant boon to OHL’s operations, especially during the busy holiday season. "If we can perform faster, we benefit our end customers and save them money," says Hauptman.
OHL is currently testing the voice technology in a limited number of warehouses, but Thyen foresees widespread use in the future.
OHL also plans to pilot new rugged tablets to provide greater visibility into its labor management system.
Wi-Fi can help make warehouse processes more efficient by allowing universal access to real-time inventory information, and reducing counting and picking errors. But because warehouses are often filled with metal structures, RF obstacles, competing handheld Wi-Fi devices, and limited Ethernet cabling, they can be hostile environments for Wi-Fi networks. Maintaining consistent, high-speed Wi-Fi connections is an ongoing challenge.
"Warehouses have to overcome all the interference, reflections, and other obstacles to RF connectivity to ensure they maintain strong connections," Wimsatt explains.
Oh GIve me a HOme
Another challenge is roaming. In a large warehouse, objects tend to move quickly and cover a lot of ground. "The Wi-Fi connection has to smoothly hand off from one point to the next," says Wimsatt. "If workers lose connectivity, they have to stop, and it becomes a productivity sink."
Lincoln, Neb.-based Kawasaki Motors Manufacturing Corporation, a subsidiary of Kawasaki Heavy Industries Ltd., produces popular consumer recreation and utility machines. But the company’s vast warehousing operations were struggling with radio frequency and data capacity issues, and continuous disconnections.
"We view Wi-Fi as a strategic tool for optimizing operations as part of our continuous improvement practice, because we use it daily to run our manufacturing operations," says Paul Kramer, IT manager for Kawasaki Motors.
Kawasaki Motors needed a dependable Wi-Fi infrastructure to support a variety of applications that utilize handheld mobile devices, including Apple iPads and bar-code scanners mounted on forklifts. Workers use these devices to feed inventory data into the company’s enterprise resource planning system.
The facility installed a new high-speed Smart Wi-Fi system from Ruckus Wireless in 2013. "Coverage and connectivity immediately improved, with higher data rates than we had previously experienced, and fewer access points deployed," says Kramer. "Ultimately, the Smart Wi-Fi system allowed us to lower the cost of our supply chain management processes while speeding our production environment."
Through the use of dual-polarized directional antennas, Ruckus Wi-Fi access points are also capable of transmitting and receiving Wi-Fi signals at different angles. This is important to users of low-powered handheld devices, who are continuously changing the orientation of these tools, notes Wimsatt.
Antwerp, Belgium-based Katoen Natie recently began using Ruckus Smart Wi-Fi products to support its in-house warehouse management system (WMS). The international logistics service provider and port operator for clients ranging from consumer goods and industrial manufacturers to chemical companies was relying on a legacy Wi-Fi system that delivered spotty coverage, and suffered from erratic performance, dropped connections, and problems adapting to obstacles and interference.
"Conventional Wi-Fi technology was simply unable to adapt to our constantly changing RF environments," says Ian De Winter, telecom director for Katoen Natie. "In today’s warehousing environments, a reliable wireless system is no longer negotiable."
Today, Ruckus access points support Katoen Natie’s workers using Wi-Fi handheld scanners to unload, pick, pack, and ship products.
"Our WMS requires Wi-Fi, and during peak season, when we have thousands of workers in the facility, the connection simply cannot fail," says De Winter. "Having thousands of people doing nothing for 10 minutes when the connection drops costs us a lot of money."
Full Steam Ahead
As e-commerce continues to grow, the pressure to improve warehouse efficiency will likely intensify. Today’s consumers have little tolerance for errors or long delivery times.
"We have all had the experience of shopping online and receiving the wrong item," says Wheeler. "This is how retailers lose customers—errors are just not acceptable. Companies looking to operate more productively need tools to enable efficiency. Generally, that means ergonomic, task-oriented technology such as wearable scanning or voice-directed interaction tools."
The pressure to improve warehouse operations can also present an opportunity. Warehouse operators are adopting a forward-looking view of their facilities, according to From Cost Center to Growth Center: Warehousing 2018, which surveyed warehouse IT and operational personnel in the manufacturing, retail, wholesale, and 3PL market segments.
"Instead of seeing it as a pure cost center in which operational focus is placed almost exclusively on wringing out inefficiencies and inaccuracies in order picking, companies increasingly view the warehouse as a powerful asset that can drive profitable growth for the business with a heightened focus on improving inbound, storage, and outbound materials handling," the report states.
Mobile technologies can go a long way in driving companies toward that goal. They can also enable flexibility, which is key in today’s unsettled supply chain environment.
"The retail and e-commerce fulfillment landscape is changing," says Hauptman. "Today, when a company makes a strategic decision, it moves fast. Mobile technology is vital because it enables businesses to operate warehouse facilities that can react quickly to that changing landscape."