Stacking Up Pallet Pros and Cons
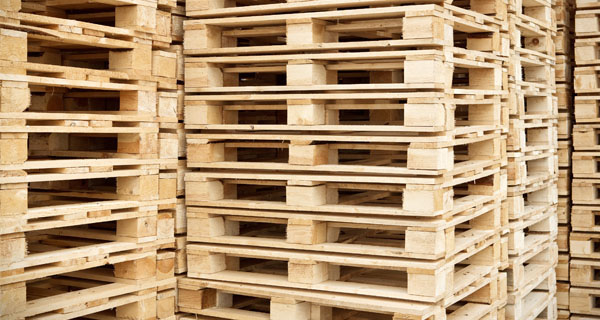
As shippers look to uncover efficiencies and economies in their supply chain, pallet management presents an area ripe for picking.
Walk into any warehouse, manufacturing, or retail facility, and pallets are hard to miss. Strewn here and stacked there, these denizens of industrial space are part of the transportation and logistics clutter that often goes unseen. While attention focuses on shrink-wrapped SKUs laden with value, the equal-opportunity pallet sits in quiet diffidence, fulfilling its supporting role.
Without the pallet there is a clear void in the warehouse and the supply chain. For such a simple piece of equipment, it stirs rabid debate and attracts a lot of interest— often after the fact and for the wrong reasons. When materials handling systems fail, or pallets fall apart with contents in tow, shippers and consignees take note.
But when companies attend to pallet management proactively and appreciate how materials handling impacts other areas of the supply chain, as well as the bottom line, efficiency gains and cost savings can be considerable. It all begins with understanding and appreciating the iconic wood pallet’s role.
“The wood pallet is still ubiquitous because it is cheap, renewable, and recyclable,” says Derek Hannum, director of marketing at CHEP, an Orlando-headquartered pallet company. CHEP serves as a pooling resource by issuing, collecting, and conditioning more than 300 million pallets— handling three million equipment moves each day— from a global service center network.
In the pool, the company delivers ready-for-use pallets and containers from its service centers to customers, who load their goods and ship their products through the supply chain. When shipments reach their destination, the consignee off-loads the goods and returns the pallets or containers to the nearest service center.
don’t Knock Wood
CHEP’s familiar blue wood block pallet connects retailers, distributors, manufacturers, growers, and transportation and logistics service providers across countless industries, throughout the entire length of the supply chain. The company’s product line carries an assortment of styles and dimensions, both wood and composite plastics that meet varying operational standards for different regions around the world.
“We aren’t really a wood pallet company,” says Hannum. “We consider ourselves material agnostics.” CHEP invests a great deal of money in researching alternatives to wood for applications that range from open pool use to fast-moving consumer packaged goods.
With so many different freight types and pallet varieties on the market, neutrality is important. At the end of the supply line, demand ultimately dictates preference.
Manufacturers often favor one shipping platform type for consistency and cost reasons. In certain industrial sectors, such as food and beverage, electronics, and pharmaceuticals, it makes sense for companies to operate closed-loop pallet networks among carriers, vendors, and competitors, pooling equipment that meets specific shipping requirements. This practice eliminates variability and builds consistency.
Regardless of materials handling preference upstream in the supply chain, end customers generally specify the pallet type they want, and suppliers comply. The reasons are manifold. Pallet quality, like an inbound routing guide, is a sometimes-overlooked requirement that has an impact on loading and unloading time, product quality, safety, and total cost.
As you like it
Customers running sophisticated automated storage and retrieval systems require quality pallets that won’t jam warehouse machinations. Consignees with minimal staffing need to ensure that pallets are unloaded as quickly as possible. Defective pallets create longer inbound loading times, increase freight damage risk, add touches to product, lead to bottlenecks farther along in the supply chain, and cost money. When vendors supply non-compliant platforms to their customers, they are often charged penalties.
“The pallet receiver dictates influence in the buying equation,” says Hannum. “Retailers want to ensure the pallet is easy to handle with pallet jacks instead of forklifts. Costco, for example, demands all inbound loads come in on a block-style pallet rather than a stringer.”
Sturdier four-way block pallets, often made out of a harder wood, allow for greater flexibility in maneuvering loads in tight places where pallet jacks can access the platform from any direction. Alternatively, two-way stringers require forklifts and more time adjusting equipment. Most pallet pooling companies use block pallets exclusively, says Hannum.
Nirvana, an upstate New York-based bottled-water producer, made the decision to switch from traditional wood stringer pallets to CHEP’s block pallet system about three years ago, says Mo Rafizadeh, vice president of Nirvana. The company bottles water from a proprietary spring located on 2,000 acres in the Adirondack Mountains.
“Cost wasn’t an issue,” he says. “We were concerned because we couldn’t double-stack standard wood pallets without using a piece of plywood in between.”
Nirvana’s transition to CHEP pallets was based on operational efficiency, and the time and cost savings gained by not having to deal with loading concerns.
Demand-Driven Nirvana
The changes have been noticeable, says Rafizadeh. Nirvana’s palletizer doesn’t get as many rejects or stuck loads as in the past. Workers can turn CHEP pallets around easily, whereas standard wood pallets require adjusting a lift truck’s forks. Additionally, double-stacking pallets without having to insert a flat piece of wood saves labor and source/disposal expense. These factors, combined with CHEP’s pooling service taking care of pallet maintenance, have contributed to marked improvements.
But Nirvana is also something of an anomaly. It rents from two different pallet-pooling companies. In fall 2010, Nirvana began shipping some product with CHEP’s foremost competitor. Orlando-based iGPS provides plastic pallets with embedded radio frequency identification (RFID) tags, enabling shippers and consignees to track shipments through different touchpoints along the supply chain. Nirvana rents the iGPS pallets by the day; then returns the assets to the pallet provider’s pool.
Some consignees want as much information about their shipments as possible. “They want more data, and more accurate and reliable advanced shipment notices,” explains Rex Lowe, president of iGPS.
Keeping it Clean
iGPS has gained growing customer traction among fast-moving consumer goods companies and pharma shippers, largely because of its “clean” platform profile and the RFID track-and-trace technology embedded in its pallet-pooling system.
“Shippers place product with its license plate on a unit load,” Lowe says. “They attach that to the iGPS pallet, which has a programmable number embedded inside. Linking this tracking information allows us to follow the pallet anywhere in the supply chain. The technology is available, whether shippers want to take advantage of it or not.”
Users can turn the RFID on or off, or simply use a bar-code scanner instead. Tracking functionality incorporates redundancy that enables shippers to have full confidence in where a pallet is coming from or going to.
But the sophistication of iGPS pallets isn’t necessary for every company. And if shippers are moving volumes outside the network or outside North America— the pallet company’s primary operating area— the value proposition is less advantageous.
Nirvana partnered with iGPS primarily because a major grocery chain customer specified that requirement in its shipping instructions. For the bulk of its freight, the bottled-water company relies on CHEP.
Material Difference
Pool providers, regardless of pallet material, offer shippers a viable alternative to owning and maintaining a seemingly non-essential piece of logistics equipment. The value of having a third party manage asset allocation and maintenance is easily tenable.
But not every supply chain partner is part of a pool. Shipment volumes or facility locations might not warrant a dedicated service. Or, as with Nirvana, a customer may stipulate a non-standard shipping platform.
“CHEP pallets provide additional flexibility for moving out-of-network shipments,” says Rafizadeh. This means working with companies that are not a part of the pool. Given the cost that can be tied up in pallets, shippers are wary of using more expensive plastic types for one-way moves in which the pallets won’t return or could be exchanged for inferior pieces of equipment. This is a foremost distinction between wood and plastic options.
Over the past few years, a pallet war of sorts has erupted between CHEP and iGPS over the efficacy of wood and plastic. Each company stakes its claim to a number of arguments that cover durability, sustainability, cost, traceability, and safety, among other contentions. Both sides carry pros and cons.
Compared to wood, plastic pallets are more expensive, but are lighter and therefore cost less to move freight. Shippers can build more optimal loads because of the weight displacement. Plastic is impervious to insect infestation and fluid contamination; however, it carries fire-code restrictions and can bend under heavy loads.
Wood pallets are less expensive and have a greater load-bearing stiffness, but require fumigation and fire-retardant applications for certain shipment types.
Both pallet types are sustainable depending on perspective, and pooling reusable assets is green by default. Soft and hard timber used in wood pallets is a renewable resource that comes from the earth and is recyclable. Plastic pallets last longer, are lighter in transport, and are also recyclable.
The characteristics and qualities that shippers prioritize ultimately dictate pallet preference. Certain applications favor one type over the other. “Heavily automated industries that require precise equipment, or those that emphasize packaging reduction, may be better suited to plastic,” acknowledges Hannum.
As companies explore innovative ways to eliminate secondary packaging by shrink-wrapping SKUs tight to the pallet, plastic has a hard and smooth edge over wood.
“The iGPS pallet is flat and even,” says Lowe. “This design means shippers can remove slip sheets— corrugated or plastic— and slat boards that lay on top of stacked pallets, which represent an extra disposal cost.”
Composite platforms are also generally preferable for international shipments where the rigors of transport can pose durability and product integrity concerns ; however, there is a cost trade-off if the pallet isn’t returned. And from an asset-tracking standpoint— RFID use, for example— wood is not appropriate.
But wood still remains the most popular pallet option on the market, thanks to its economy and tensile strength. “Wood is very durable and rigid, and can support heavy loads,” says Hannum.
When pallet pooling enters the mix, economies become even greater, regardless of whether a skid is plastic or wood. Challenges arise as well. Keeping track of assets and preventing shrinkage are ongoing problems.
“Pooling is a marathon, not a sprint,” says Hannum. “Leakage is a concern within the pool, so there is constant capital inflow. We’re exploring better asset control.”
Pallets Prove Their Metal
While wood and plastic duke it out in the materials handling world, aluminum is quickly gaining traction as a popular means of shipping and stowing freight. Metal skids have traditionally been used for heavier freight and global shipments. But innovation and engineering are making aluminum pallets a much more pallet-able solution for shippers.
“Engineering and structural design make our product unique compared to other metal providers,” says Young Lee, executive director of AL Pallets USA, a Carson, Calif.-based company that began operations in 2002. The company has created a patented aluminum product that is lighter and carries the same load capacity as heavier types on the market.
In terms of advantages, aluminum pallets are light, easily sanitized, non-corrosive, durable, and can be easily handled by one person— a consideration that is often forgotten. They are also fireproof, which can help reduce insurance rates. But their real value is in weight displacement.
Compare a nine-pound, ultra-light AL pallet, a 65-pound wood pallet, and a 50-pound plastic pallet, each ferrying air freight at $1 per pound. The shipping platform creates a major price differential.
There is a cost, however. AL Pallet’s lighter, one-way air model averages about $30 a unit, while its heavier, re-usable sister product sells for around $60. Each price is variable depending on the amount of customization required.
“The cost depends on specifications,” explains Lee. “A four-way, rackable, one-ton-plus, reusable pallet, for example, costs more than a standard air logistics pallet.”
Compared to wood and plastic, that’s a lot of money tied up in one piece of materials handling equipment— let alone a fleet.
Still, AL Pallets is building a growing roster of customers that includes Samsung, Nokia, and LG. Electronics, pharmaceuticals, and automotive parts are among the company’s target industries, largely because these products are shipped via air and are sensitive to dust and magnetics. Aluminum is anti-static and anti-magnetic.
Metal pallets also offer potential return on investment. Currently, all of AL’s pallets are manufactured in Asia. When a company ships a one-off air logistics pallet from Shanghai to Dallas, for example, the consignee can scrap the pallet and redeem as much as $9 per unit as part of a company-sponsored buy-back program. One business in India receives aluminum pallets, scraps the metal, and subsidizes its entire payroll with this new revenue stream, according to Lee.
The one concern, given aluminum’s scrap value, is the threat of pallet theft— a lesser consideration for wood and plastic.
Making Pallets A Priority
What is unique about pallets is that shippers often only perceive them as absolute costs— a business necessity and a capital expense. Companies don’t necessarily pay attention to a pallet’s strategic function and use, or how investing in a pallet management system can bring tangible returns.
With so many different pallet options and services to consider, diligent shippers can find the best match that will help them locate hidden supply chain costs— beyond even the warehouse floor— and drive further efficiencies and economies.