Are Manufacturers Ready to Reshore?
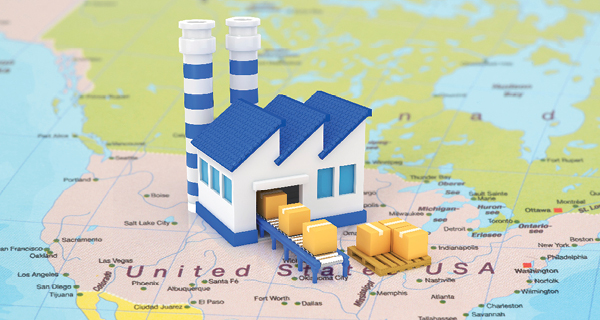
The answer is yes… and no.
We have all heard the talk about the possibility of a manufacturing revitalization in the United States. While it is happening in some sectors, the chances of a wholesale national shift occurring are more rhetoric than reality in the current market.
The Cyber Supply Chain: Assessing Your Risk
“More accurately, corporate executives are adopting a carefully considered production flow strategy,” says Morris Cohen, professor of manufacturing and logistics in the Operations, Information and Decisions Department, University of Pennsylvania’s Wharton School. “Companies are strategically shifting manufacturing centers for a variety of reasons, including easier access to current or emerging markets and to sources of innovation.”
In most cases, the reshoring decision is less about the cost of labor to manufacture and produce goods and products, and more about the overall total cost, which includes strategic assessments about supply chain risk, logistics, customer proximity, quality, and many other factors. Manufacturers are evaluating tradeoffs that affect their global performance through their impact on local performance metrics, such as the landed cost for each product in each market in a way that accounts for current market conditions, technology trends, supply availability, and competitive factors.
“We’re focused on shaping an integrated supply chain solution and the intelligent optimized flow of goods from the manufacturing facility to warehouses, distribution centers, and customers,” confirms Frank Guenzerodt, president and CEO of Dachser USA, a global logistics service provider. “That includes all aspects of product supply or raw materials across the entire supply chain, not just transportation.”
A greater emphasis on supply chain management strategies at the executive level has changed the manufacturing market, according to Rosemary Coates, executive director of the Reshoring Institute, a group that provides research and support for companies bringing manufacturing jobs and services back to America.
“The decision to reshore, nearshore, or offshore manufacturing is more thoughtful today than it was 10 to 15 years ago,” she says. “In the past, many decisions were knee-jerk reactions to competitor actions; there was little evidence that various incentives were carefully considered. Today, executive leaders are analyzing and measuring the tradeoffs much more carefully.”
Here’s a summary look at the “production flow” that is occurring across the global manufacturing market, and how it affects reshoring in the United States.
Rebuilding the U.S. Middle Class
In 2014, 60,000 manufacturing jobs were added in the United States, compared to 12,000 in 2003, as a result of reshoring (American companies returning to the United States) or through direct foreign investment (foreign companies moving production to the United States), according to theReshoring Initiative, a non-profit organization founded in 2010. The net increase of at least 10,000 jobs in 2014 was the first net gain in at least 20 years. In contrast, as many as 50,000 jobs were offshored last year, a decline from about 150,000 in 2003, the organization reports.
“These numbers likely reflect the evolving supply chain strategies that manufacturers in the United States, as well as foreign companies, are putting to work,” says Coates. “For some U.S. manufacturers, economic patriotism will be a tipping point as to whether or not to reshore. Executives recognize that over the past 15 years, we put a giant hole in the middle class. We have to fix that because it’s not a sustainable economic profile in the long term.”
Walmart is doing its part to develop a stronger manufacturing base by pledging to purchase approximately $250 billion in U.S.-made products by 2023.
“Walmart’s U.S. manufacturing initiative is particularly significant, primarily because of the company’s sphere of influence,” explains Coates. “Walmart is the mother of all supply chains. The company influences virtually every part of the manufacturing industry. As a result of Walmart’s initiative, plastics, small motors, apparel, and other products are coming back. Rebuilding these industrial sectors will have a magnifier effect across all kinds of American manufacturing—and we know that Walmart is a retail trend-setter that other retailers are sure to follow.”
As a result of Walmart’s pledge, a number of companies have expanded manufacturing operations in recent years. In 2015, Bell Sports brought its bike helmet production back to the United States. The firm now sells 100-percent Made in the USA helmets at Walmart.
Other examples include the new K’nex line of K-Force Build and Blast toys, which are molded by its Hatfield, Pa.-based injection molding company, Rodon Group LLC. General Electric (GE) opened three factories in Mattoon, Ill., and Circleville and Bucyrus, Ohio, to manufacture GE energy efficient soft white bulbs that are sold exclusively at U.S.-based Walmart stores. And Giti Tires established a facility in Chester County, S.C., to produce tires for Walmart.
Some manufacturers are able to overcome labor disparities with help from federal and state government incentive programs. One example is the U.S. Department of Commerce Economic Development Administration’s (EDA) $2 million grant to the Brooklyn Navy Yard Development Corporation (BNYDC) to create space for manufacturers and startups. With EDA’s investment, BNYDC will renovate 250,000 square feet of space in Building 77 at the Brooklyn Navy Yard into industrial suites for new and growing green manufacturing companies.
In 2015, Peoria, Ill.-based Caterpillar announced plans to begin independently manufacturing vocational trucks in Victoria, Texas. Caterpillar launched its first vocational truck, the CT660, in the North American market in 2011. It has since added two more models—the CT680 and CT681—to the lineup. To date, Caterpillar has worked with Navistar for the products’ design and build, which are currently manufactured in Escobedo, Mexico. Production of the truck is set to begin in Victoria in 2016.
Another example is Todd Shelton, a men’s clothing manufacturer, which is reshoring production back to the United States from Japan. The company has balanced high labor and fixed costs with improved product quality, increased innovation, and greatly reduced lead times since it began manufacturing in-house, according to an in-depth report prepared by the Reshoring Institute.
Automakers Drive Back
Several auto manufacturers are also moving production to U.S. soil, demonstrating Cohen’s “manufacturing production flow” scenario that has begun to emerge across the global manufacturing industry.
For instance, Ford is moving medium-duty F-650 and F-750 commercial truck manufacturing operations from Mexico back to the United States, in Avon Lake, Ohio—a first for the company in the way of reshoring. The announcement is tempered by the move of Ford’s Focus and C-Max cars from a plant in Wayne, Mich., to Mexico. “We are committed to leveraging our global manufacturing footprint and will continue to invest where it makes the best sense for our business,” says Karl Henkel, a Ford spokesman.
Several other notable manufacturers have brought some production back to the United States, including GE’s reshoring of appliances from China to Kentucky and Motorola’s smartphone from China to Texas.
A Chemical Reaction
The chemical manufacturing industry is in the midst of a production shift as well. “In the chemical industry, it’s all about energy prices right now,” says Glenn Riggs, senior vice president of corporate logistics and strategy for Odyssey Logistics & Technology Corporation (Odyssey), a global logistics solutions provider.
“In the past, chemical manufacturers typically outsourced production to take advantage of low energy and labor costs,” he adds. “With the availability of low-cost energy in the form of natural gas in North America, the manufacturing tide is turning.”
Companies announced 246 projects worth $153 billion in potential capital investment as of September 2015, according to the American Chemistry Council (ACC). That’s an increase of 97 projects and $72 billion from March 2013. By 2023, the study notes, additional output from $153 billion in capital investment will generate $113 billion per year in new chemical industry shipments.
Why is this important? Because chemical products such as PVC, vinyl chloride, ethylene glycol, styrene, and polystyrene are key to the manufacture of a vast range of products from food packaging to footwear, tires to trash bags. Interestingly, firms based outside the United States initiate more than 60 percent of the capital projects, according to the ACC study.
“Low energy prices have sparked foreign investment in U.S.-based chemical manufacturing, as a way to develop a reliable, regional supply chain for production with excess for export,” Riggs adds.
Foreign Companies Outsource to the United States
For European companies, North America represents a lower-cost and lower-risk manufacturing alternative to production at home, according to Cohen’s study. It also provides much-needed proximity to their customer base.
Germany-based Airbus is one example. The company recently opened its first manufacturing facility in Mobile, Ala. Airbus expects to deliver the first U.S.-made Airbus A321 commercial aircraft in spring 2016. By 2018, the facility will produce between 40 and 50 single-aisle aircraft per year.
“With the addition of our U.S. facility to our production network in Europe and Asia, we have strategically expanded our worldwide industrial base,” says Airbus President and CEO Fabrice Brégier. “It enables us to grow our already significant presence in America—the largest single-aisle aircraft market in the world—and to be closer to U.S. customers and key supplier partners.”
In addition to the new Alabama manufacturing site, Airbus assembles commercial aircraft at modern facilities in Hamburg, Germany; Tianjin, China; and Toulouse, France. The company traditionally builds its A320-type planes in Hamburg and Toulouse. It opened a site similar to the Mobile final assembly line in Tianjin in 2008.
Similarly, Innovate Manufacturing, a China-based company, renovated a 30,000-square-foot building to support injection molding operations in Knoxville, Tenn.—the first U.S.-based facility for the company. Mexico-based Nutec Group, a producer of high-temperature insulation fibers used in the fire protection, metal, glass, automotive, and petroleum industries, is also building its first U.S.-based advanced manufacturing facility in Huntersville, N.C.
“We chose North Carolina for its utility and transportation advantages, and the state contains an exceptional workforce,” said Gerardo Muraira, operations director for Nutec, in a press announcement. “In addition, we can service our customer base quicker, and provide more cost-effective transportation.”
The Fit and Fix of Nearshoring
From automobiles to medical devices, Mexico is fast becoming the manufacturing mecca for companies looking to gain closer access to customers in the Americas.
“We’re seeing considerably more nearshoring activities, as opposed to reshoring,” confirms Dachser’s Guenzerodt. “Much of that trend originates from Asia’s disappearing labor cost advantage as compared to areas such as Mexico, which brings some U.S. manufacturers closer to their primary consumer.”
Thanks in large part to the North American Free Trade Agreement, Mexico offers U.S. and foreign manufacturers many of China’s low labor benefits, combined with proximity and lower risk.
One of the biggest growth areas has been in the automotive industry. Mexico produced 292,271 vehicles and exported 234,668 autos in August 2015, according to the Mexican Automotive Industry Association. Nearly every automaker, both U.S. and foreign, is adding manufacturing capabilities in Mexico.
For instance, Daimler and the Renault-Nissan Alliance are building a plant in Aguascalientes in central Mexico to produce next-generation premium compact vehicles from Mercedes-Benz and Infiniti. The new plant will have an initial annual production capacity of more than 230,000 vehicles, with the first vehicle rolling off the assembly line in 2017.
Audi is currently building its first plant in Mexico, which will provide the automaker with its first North American manufacturing capacity by the end of 2016. Italian tire company Pirelli opened its first manufacturing plant in Mexico several years ago to meet demand in the Americas. The company projects that the plant will produce 5.5 million tire units by 2017.
Autoneum Holding AG, a provider of acoustic and thermal management solutions for vehicles, has begun construction of a new plant in San Luis Potosi, Mexico. The decisive factor behind the expansion of its production capacities in Mexico is the prevailing high demand from international automobile manufacturers for lightweight and multifunctional components. Mando is building a new auto parts manufacturing plant in Arteaga City, Mexico, which will begin operation in 2017. The company’s supply networks range from Volkswagen, Honda, and Mazda to Kia, GM, and Ford.
The Rest of the Story
While automobiles and parts make up a large part of Mexico’s manufacturing production growth, they are only part of the story. In Guaymas, Mexico, Chromalloy built a new gas turbine engine machining facility for aircraft engine components. Zenith Electronics Corporation has plans to discontinue sourcing picture tubes for projection TV sets in the Far East and begin manufacturing them in Mexico.
The already strong medical manufacturing sector in Mexico is also expected to continue growing. Currently, Mexico exports a majority of its manufactured medical devices to the United States and Canada.
While nearshoring will continue to happen given the technical capabilities and low labor costs in Mexico, it will do little to solve the U.S. manufacturing market, Coates argues.
“We love it when companies rationalize their manufacturing to the continent where they are going to sell their products,” she notes. “But the problem with locating in Mexico is that it’s not America. Setting up manufacturing in Mexico won’t help rebuild the U.S. manufacturing economy.”
Many industry analysts agree that wholesale manufacturing reshoring in the United States is unlikely, though they look optimistically at today’s more balanced growth.
“Companies are applying the concept of total cost of ownership and supply chain risk and complexity in far more strategic ways,” says Joel Sutherland, managing director with the Supply Chain Management Institute, School of Business Administration at the University of San Diego, and host of the Reshoring Institute. “These factors are often somewhat intangible with hidden costs, such as corruption or the loss of intellectual property.”
Still, the primary reason for putting a manufacturing plant in a particular location is likely proximity to existing or emerging consumer markets. China, for example, offers one of the largest consumer markets in the world—so it makes sense to produce in China for their local market. The question is whether it makes sense to produce in China for another market such as the United States.
“We live in a just-in-time delivery world,” says Sutherland. “Business success depends on an effective supply chain system that considers multiple factors including wage rates, skilled labor availability, production costs, government regulations, economic stability, controlled risks, and much more.”
As manufacturers continue to refine their production flow strategies based on comprehensive supply chain management analysis, expect to see some continued reshoring of manufacturing in the United States, though likely not the wholesale return that some might hype.
The Cyber Supply Chain: Assessing Your Risk
How safe is your supply chain data? A University of Maryland Robert H. Smith Business School website can help answer that question. It provides guidelines to measure and assess cyber supply chain risk based on, and part of, ongoing research, and is funded by the National Institute of Standards and Technology.
The research findings “identify cyber security framework and associated supply chain risk management’s practice guidelines,” according to Dr. Sandor Boyson, director of the Supply Chain Management Center, and research professor at the Robert H. Smith School of Business.
“Users take a series of assessments,” explains Boyson. “The site helps analyze IT systems, supply chain systems, and insurability systems. It also offers an executive dashboard that explains the results and how they compare with other companies.”
It takes 30 to 40 minutes to complete each assessment. Because the assessments are interdisciplinary, it helps to have members of the IT, supply chain, and risk management departments available to help answer questions. The insurance assessment section might be of particular interest to publicly traded companies.
To take the completely anonymized assessment go to: https://cyberchain.rhsmith.umd.edu