Data Warehousing System Puts an End to Paperwork
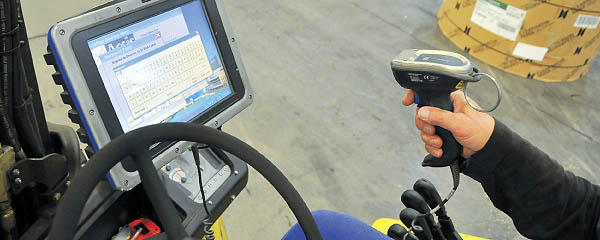
Paper distributor and converter Roosevelt Paper wraps up manual information processes, and implements an automated data collection and management system to streamline operations.
Founded more than 75 years ago in a modest Philadelphia warehouse, Roosevelt Paper has grown into one of the nation’s largest distributors and converters of fine printing papers. Today, the company serves a global network of customers from its headquarters in Mount Laurel, N.J., and three divisions in the Cincinnati, Chicago, and Philadelphia metropolitan areas. Each division provides a varied inventory and extensive in-house converting capabilities.
Faced with workflow inefficiencies, Roosevelt implemented a paperless data warehousing system that transformed its operations and positioned the company to better manage growth, respond to market variations, and maintain a leading position in its field.
“As a paper converter, we transform large rolls of paper into smaller rolls or sheets—whatever the customer needs,” says John Gordon Jr., CIO at Roosevelt. “In our previous workflow, if there was a change order—and there are always change orders—the staff reprinted paperwork, then gave it to the appropriate personnel. We performed a constant paperwork shuffle—in the production office, shipping department, and on the plant floor—with the drivers and machine operators. Our processes were paperwork-driven, and not as efficient as they needed to be.”
All the paperwork and manual transfer created a high risk for errors. Orders were incorrect when the latest change was not communicated to the driver or machine operator. Wrong paper was sometimes pulled for orders. Shipping destinations were changed at the last moment, and if not communicated quickly or efficiently, shipments moved to the wrong destination. “We were losing 4,000-pound rolls of paper,” says Stan Kilian, project manager at Roosevelt. “We needed to improve our processes.”
Building a Solution
Roosevelt called on Marlton, N.J.-based Acsis Inc., a systems integrator and supply chain solutions provider, to help solve the problem. “Roosevelt needed a system to automate all its processes, from materials receiving through shipping,” says Larry Sawyer, Acsis’ vice president, strategic accounts.
Acsis recommended Everett, Wash.-based Intermec Technologies for the hardware component of what would become the paperless data warehouse solution.
One major advantage of working with Intermec was that it could provide everything Roosevelt needed from a single source. “Intermec offered a total solution—mobile computing devices, printers, scanners, and the wireless infrastructure,” Gordon says. “Instead of having to use several different vendors for the equipment, we were able to deal with one, which helped minimize issues.”
Roosevelt uses Intermec’s CV60 truck-mounted computers to receive and move product, SR61 scanners to read barcodes, and PX4i wireless printers to produce both permanent and in-process labeling. The technology tools identify and track goods anywhere within the Roosevelt supply chain.
“The SR61 scanners feature a proprietary scan engine, which delivers more accurate results than other models we have tried,” says Kilian.
“We recently installed the wireless printers, even though the original ones we purchased from Intermec were still going strong after 17 years,” adds Gordon. “Those workhorses were getting old, and it was time to upgrade.”
All About Operations
Automating all warehouse and plant floor processes has given Roosevelt an operational advantage. “With the weak economy, it’s helpful that the data warehousing system we’ve built gives us the ability to respond agilely to market changes,” Gordon says.
The new system allows Roosevelt to do more with less. “Automating processes resulted in tremendous advantages for Roosevelt,” says Sawyer. “Providing workers access to real-time information allowed the company to increase throughput while reducing labor.”
Before the automated system, Roosevelt supervisors were encumbered by lag time and shuffling paper among departments. “The new system directs each worker to their next task,” says Sawyer.
When an operator logs on at a workstation, the system displays orders in the correct handling sequence. The driver assigned to those workstations knows in exactly what order to pull the rolls. “Every process is prioritized,” explains Gordon.
The system of scanning and checking each item helps prevent mistakes. If a worker tries to scan a roll out of order, the system will indicate an error.
“Checks and balances are in place that weren’t possible with a manual system,” says Kilian.
The same principle holds for shipping. When supervisors prepare a shipment, they include details about which orders are part of that load. If the driver puts the wrong paper roll or skid on the load, the system identifies the mistake when workers scan the bay card that reports the item’s location.
“If workers scan the wrong roll, the system notifies them of the mistake, and those goods can be removed from the truck,” explains Kilian. “We aren’t losing two-ton rolls anymore. Our inventory is accurately tracked.”
Roosevelt also conducts numerous automated quality checks before shipments leave the facility. “If the system rejects an item for quality reasons, processes are in place to put the goods back into inventory or scrap them,” Gordon says.
The Total Process
The process begins with electronic data interchange (EDI) transactions Roosevelt receives from its paper mill suppliers. EDI manifest transactions for the mill shipments are electronically sent to Roosevelt to help automate the receiving process.
When the goods arrive from the mill, workers scan their barcodes, which links them to the enterprise resource planning (ERP) system and confirms that the shipment matches the order. “Goods now enter inventory in real time; this used to be a manual process,” says Gordon.
Before automation, the process—from loading dock to front office, with information manually keyed at each place—could result in one- to three-day delays in tracking inventory and providing visibility to sales staff. Now Roosevelt has real-time integration between the warehouse management system and back-end ERP system.
Full Functionality
“This is a complete system,” says Gordon. “First we automated the receiving process, then the relocation process, then cycle counts; and the system is now a full data warehousing management system.
“The visibility it provides operations is significant,” he adds. “From the time we receive the paper to the time we ship it and every step in between—from order entry to scheduling to manufacturing to shipping and service—we have complete operations visibility.”
As an added benefit, the new system and equipment empower Roosevelt employees.
“One shipping worker had a job that entailed identifying and labeling all the goods coming from production, then allocating them to an order or sending them to stock,” he recalls. “After we trained him on the new equipment, he said, ‘We just did in two minutes what used to take me 40.'”
With efficiency gains that significant, Roosevelt Paper’s warehousing operations are on a roll.