How to Reduce Costs by Integrating Packaging with Distribution Center Operations
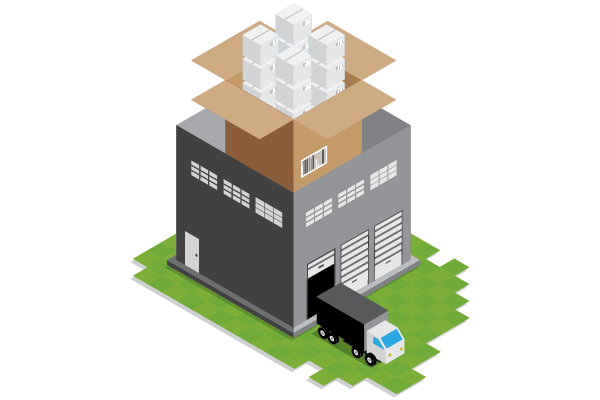
Product packaging is often handled as a discrete supply chain function, separate from warehousing and distribution. But companies can capitalize on considerable efficiency and economy gains by driving toward greater integration of these functions. In fact, performing final packaging in the distribution center can reduce combined warehousing, logistics, and freight costs by 30 percent and order-to-delivery cycle times by seven days.
Instead of outsourcing packaging to contract packagers, shippers that bring the process in-house or partner with capable 3PLs can better control raw material use and resource allocation at different touchpoints within the supply chain—while eliminating costly transportation legs.
Many retailers are pushing the need for more strategic packaging solutions that take advantage of niche e-commerce channels or marketing opportunities. For example, greater control over packaging operations at the DC level allows companies to specify customization closer to demand, thereby accruing economies of scale transporting and storing goods with the least amount of value-add farther up the supply chain.
Partnering with 3PLs often allows shippers to align packaging needs with transportation and logistics operations to find places and opportunities where they can optimize the process. Packaging can be a burning platform for strategic change—lean best practices, sustainability efforts, labor utilization, even DC design. 3PLs that have the right resources and expertise can help shippers make this aspect of their business a competitive differentiator.
Un-bundling Benefits
Companies that pay close attention to packaging operations can uncover myriad economies upstream and downstream in the supply chain. Among the benefits:
Lower Freight Costs. In a traditional scenario, products ship out to the contract packager, then back to the DC for final distribution. These additional runs hike freight costs an estimated 38 percent. Eliminating these legs on an $8-million spend saves $3 million, not to mention the added environmental benefit of taking trucks off the road and reducing carbon emissions.
Lower Inventory Carrying Costs. Using an outside contract packager can add seven days to the distribution cycle. Worse, companies typically lose visibility of their product, creating uncertainty about the amount of product available for sale. Manufacturers deal with this uncertainty by adding inventory, which, in turn, adds warehousing, labor, and financing costs.
Reduced Labor and Equipment. In a combined packaging/distribution operation, labor and rolling stock are deployed where they’re most needed at any given time, across multiple functions. Cross-trained workers can address peak demands in the DC or the co-pack area. Management costs are also reduced, and the functions can share security, clerical, maintenance, and other facility staff.
Reduced Damage. The more product is moved, the greater the potential for damage. If it’s a liquid product, the chance of shrinkage is even higher because damage to one bottle can destroy multiple cases.
Reduced Material Costs. Companies can streamline material spend—for example, purchasing bulk corrugate at a commodity price—by bringing packaging in-house and integrating it with DC operations. Those that have pursued a Lean path can operate in a more just-in-time fashion, making smarter decisions about procurement, storing less packaging materials, and avoiding packaging obsolescence when lines switch over.