Keep Your Cool
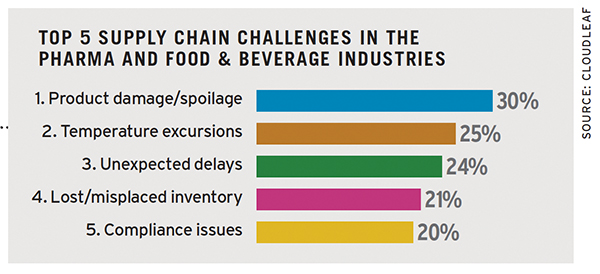
Product damage or spoilage, which most often occurs in transit, is the No. 1 supply chain challenge for the pharma and food and beverage industries (see chart), according to a Cloudleaf survey. This highlights a great need to maintain visibility throughout a product’s journey once it leaves the warehouse.
Most (87%) survey respondents in the pharma industry say they don’t have 100% visibility into the condition of products during the last mile, and nearly half of respondents claim to use manual processes to achieve visibility. In transit to distribution was unanimously the most likely point for spoilage to occur, Cloudleaf says.
Products are easier to control during the initial phases of distribution because they sit in local storage before shipment, the report says. The more handlers and transitions there are when the product leaves the warehouse, the less visibility there is, which increases the chance of spoilage.
Pharma industry respondents lost $95 million per year in medical inventory due to spoilage caused by cold chain failure. They lost 202,600 doses of medical inventory annually on average, with 6% losing 1 million doses or more, the report says. On average, $71 million in fresh food is lost per year due to cold chain failure. This reaches $179 million for companies with 1,000 or more employees.
Complete visibility means having a clear understanding of where products are at each point in the supply chain, what condition they’re in, whether they’re in compliance with regulatory requirements, and whether they will arrive on time and in the same condition as when they were shipped, Cloudleaf reports.