Process Manufacturing: Definition, Benefits, and Industries
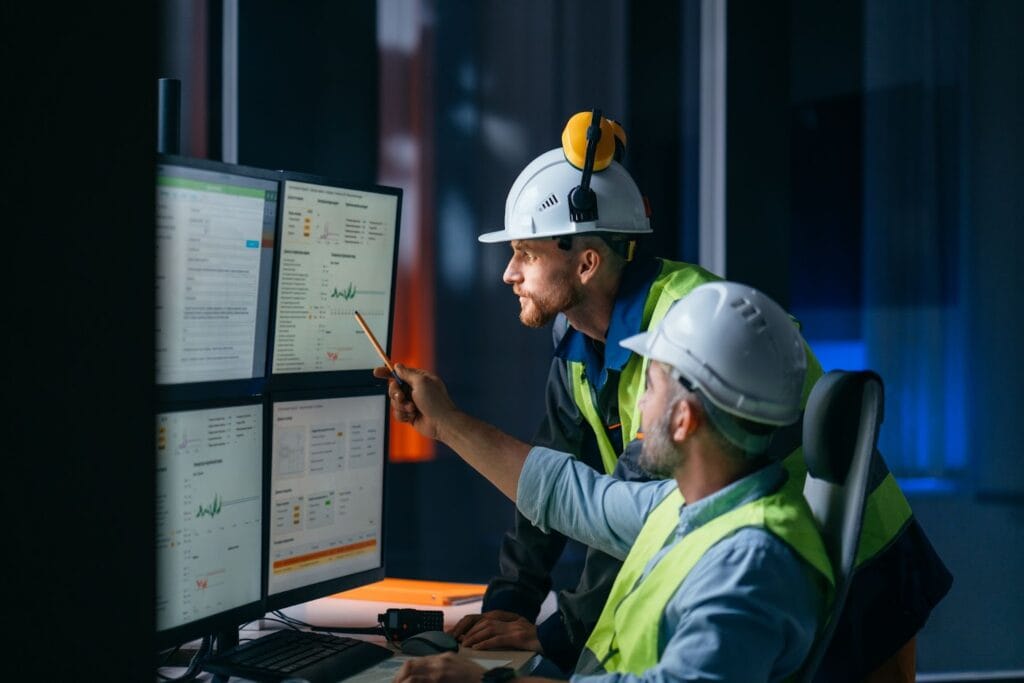
Manufacturing is the process of creating a finished product from raw materials or ingredients. This action is accomplished by using machinery, human labor, and other tools, with some manufacturing requiring chemical processes.
There are various methods of manufacturing systems linked with producing final goods. Process is one of the main manufacturing methods. Modern manufacturing processes, which integrate advanced technologies like automation and robotics, are transforming product design and production by enhancing efficiency and sustainability. In this article, we break down all you need to know about process manufacturing, including its benefits and disadvantages.
Read on to learn about process manufacturing and explore the primary industries that use it.
What Is Process Manufacturing?
Process manufacturing refers to producing finished goods by combining components, ingredients, and raw materials under specific thermal and pressure conditions according to recipes or formulas. The output of this production process is final goods that can’t break down into smaller units, with the process being irreversible.
Process manufacturers often utilize biological, thermal, or chemical processes to produce finished goods in bulk quantities. This aspect sets process manufacturing apart from other processes like discrete manufacturing, which relies on assembling components to make the final good.
The ultimate objective of process manufacturing is to create homogenous final products in bulk quantities. So, the finished products typically appear, feel, and function the same without distinctions. Process manufacturing requires the company’s management to set rigorous quality control standards.
The flow of successive steps is essential in process manufacturing, with the conclusion of one phase triggering the commencement of the next. Process manufacturers rely on tracing and scheduling tools or software to ensure optimal operating efficiency.
Many of today’s manufacturing processes stem back to the dawn of the Industrial Revolution in the 1800s when manufacturing transitioned from labor-centered to man-and-machine-made. As technology progresses, production processes become easier to grasp and follow.
Definition of Process Manufacturing
Process manufacturing is a type of manufacturing process that involves the transformation of raw materials into finished goods through a series of continuous or sequential processes. This method is particularly prevalent in industries such as food and beverage, pharmaceuticals, and chemicals. In these sectors, the production of goods often relies on specific recipes, formulas, or chemical reactions to achieve the desired end product. By utilizing raw materials like liquids, gases, or powders, process manufacturing ensures that the final products are consistent and meet stringent quality standards.
Characteristics of Process Manufacturing
Process manufacturing is characterized by its reliance on continuous or sequential processes to produce goods. This type of manufacturing involves the use of raw materials, such as liquids, gases, or powders, which are transformed into finished products through a series of chemical reactions, mixing, or blending processes. Industries that require a high degree of precision and consistency, such as pharmaceuticals and chemicals, often employ process manufacturing. The focus on maintaining uniformity in the production process ensures that each batch of products meets the same quality and performance standards.
Examples of Process Manufacturing
Examples of process manufacturing are abundant in various industries. In the food and beverage sector, the production of bread, beer, and soft drinks are classic examples. These products are created through specific recipes and processes that ensure consistency in taste and quality. In the pharmaceutical industry, the production of tablets and capsules involves precise formulations and stringent quality control measures. Similarly, the chemical industry produces detergents and cleaning agents through complex chemical processes. These examples highlight the diverse applications of process manufacturing in creating everyday products.
Types of Manufacturing Processes
Manufacturing processes can be classified into several types, each with its unique approach to producing goods. The main types include discrete manufacturing, repetitive manufacturing, batch process manufacturing, and continuous process manufacturing. Each type caters to different production needs and industries, ensuring that manufacturers can choose the most efficient method for their specific requirements.
Discrete Manufacturing
Discrete manufacturing is a type of manufacturing process that involves the production of distinct and individual items. This method is commonly used in industries such as automotive, aerospace, and electronics, where the production of goods involves the use of assembly lines and the creation of individual components. Discrete manufacturing is characterized by the use of a bill of materials to track the production of each component and the assembly lines to produce the final products. This approach allows for the efficient production of complex items, ensuring that each component is meticulously crafted and assembled to meet precise specifications.
Key Benefits of Process Manufacturing
Process manufacturing comes with various perks that boost production and efficiency. Here are some key benefits of process manufacturing.
It’s Cost Effective
Instead of making items by hand or constructing complex individual products requiring many distinct components, process manufacturers seek to generate goods in bulk that may be produced without requiring a substantial quantity of human labor. Lean manufacturing plays a crucial role in reducing waste and optimizing processes, further enhancing efficiency. A well-executed production line results in decreased labor costs, more efficiency, and improved profit margins.
Moreover, investing in effective Enterprise Resource Planning (ERP) software reduces overhead and other expenses. With this software, you input data once, and it synchronizes in real-time across all departments. The software also helps to save time on administrative tasks since you enter vital details and monitor KPIs digitally rather than the conventional pen and paper, allowing you to return to work on the main floor quicker.
Easy Allocation of Costs
One of the most significant advantages of process-based manufacturing systems is that they enable logical administration of all aspects of the production line. This allows businesses to direct their resources at the right time, where needed.
Also, perceiving each step as a vertical process makes it simpler for managers to determine how to make adjustments when required and collect data from various points along the process to influence their decisions.
Improved Communication and Staff Morale
Implementing an efficient process manufacturing ERP solution places you and your staff will be on the same page. When the processes that define your company’s production targets and procedures are transparent, your team knows what they need to do, and supervisors can assess their performance accordingly.
Smooth communication methods also allow personnel to offer frequent feedback, enabling managers and engineers to make manufacturing processes even more efficient, improving staff motivation, and keeping everybody focused on the objectives.
Simple Product Base
Process manufacturing aims to make production as simple as possible without compromising quality. Mass production plays a crucial role in this by producing large quantities of standardized products rapidly and efficiently. Process manufacturers set up a production process by converting every step into a formulation or recipe concept that their production line can systemize and use to create final standardized goods.
An automated production line employs templates to manage its processes and decrease human error, and any faults may be monitored, documented, and traced. So, making necessary production line adjustments is easier with the right ERP software.
Improved Safety
Like quality, process manufacturing ERP solutions include several safety modules to reduce industrial accidents and injuries. Such solutions can also assist you in completing safety audits, complying with safety standards, and providing a clear overview of high-risk points to maintain a safe working environment. Keeping your staff safe while also achieving your production targets is vital.
Disadvantages of Process Manufacturing
Although process manufacturing comes with various perks, it also has some drawbacks. Below are the disadvantages of process manufacturing.
Limited Creativity and Room for Customizing
With the high level of automation and standardized processing procedures, process manufacturing technology inhibits creativity. Flexible production standards allow your staff to employ creativity to accommodate specific market niches.
Conversely, process manufacturing relies on a single formulation for all products. If your company needs to create intricate or unique goods for each client, a single recipe is unlikely to yield satisfactory results.
It’s Capital Intensive
Many process manufacturers are drawn to the cost-cutting advantages of incorporating automation and technology in their production facilities. Although the benefits might help save expenses and eventually enhance profits, there can be capital-intensive upfront costs.
It is essential to thoroughly assess the long-term advantages of incorporating various forms of technology into your process manufacturing plant to establish whether the initial costs will be worthwhile.
Process Manufacturing Industries
Various industries utilize process manufacturing to create finished products. Below are some of the most common process manufacturing industries that produce popular commodities and examples of each.
Bulk-Drug Pharmaceuticals
Bulk-drug pharmaceuticals specialize in manufacturing and distributing over-the-counter and prescription drugs, which need excellent quality control management, sophisticated formulation development, and lot monitoring.
Since government authorities often regulate patents and intellectual property, the industry dramatically emphasizes development and research.
Chemical, Tire, and Continuous Process Manufacturing Industries
The chemical, tire, and process (CTP) sector is an essential component of the manufacturing industry as it converts raw materials into final and intermediate products. The sector utilizes process manufacturing, batch manufacturing, and firmly integrated supply chains, distinguishing CTP from other industries.
For instance, refinery outputs can be distributed straight to a chemical plant, a petroleum chemical facility, or used as a raw material in tire manufacturing.
Cosmetics and Personal Care
The cosmetics and personal care industry is highly competitive and relies on extensive research and innovation to develop new products. This industry produces final goods such as sunscreens, beauty creams, toothpaste, and hair products.
Like other process manufacturers, cosmetics manufacturers need mechanisms for quality assurance, regulatory compliance, batch tracking, and producing recipes and formulations that match consumer expectations.
Food and Beverage, Food processing
The food processing industry features process manufacturers and packaging companies that produce food and beverage products, including:
- Dairy and meat products
- Commercial baked goods
- Sauces
- Alcohol
- Juices
Additive manufacturing is increasingly used in this industry to create customized food products through a layer-by-layer material application process, allowing for complex designs and minimizing waste.
This segment of the process manufacturing realm heavily focuses on recipe development and maintenance, but it also needs systems for keeping and upholding health regulations and quality control measures.
Nutraceuticals
Nutraceuticals is a term coined from merging the words “nutrients” and “pharmaceuticals” to mean any food-derived product that provides additional health advantages, including prevention and treatment, in addition to the actual nutritional content in meals.
This industry includes companies that manufacture nutritional products, supplements, and other botanical products. The scope of nutraceuticals and associated items varies according to the source. These goods can be classed according to their natural origins, pharmacological conditions, and chemical composition.
While the nutraceutical industry is less regulated than pharmaceuticals, many manufacturers provide standard manufacturing certifications for their companies. The certifications include organic, vegan, vegetarian, gluten-free, and non-GMO.
Paints and Coatings
Paint and coatings are manufactured through a complex chemical process, including raw materials like resin, solvent, additives, and pigment. Paint and coat manufacturers often make bulk quantities and do rigorous testing before preparing the finished product for sale.
Paint manufacturers often have their wastewater treatment plant treat liquid waste and by-products from the production process. So, the process doesn’t conclude with the completion of the final product. Instead, it continues to waste treatment and recycling of by-products.
Semiconductor Fabrication
The semiconductor industry includes manufacturers that create and produce semiconductors and devices such as transistors and integrated circuits. Semiconductors are the forgotten heroes of the technology realm, powering everything from entertainment gadgets and cellphones to automobiles and thermostats.
Specialty Chemicals
The specialty chemical manufacturing sector is a distinct segment of the chemicals industry that’s customer-centered, creating products based on their performance or function instead of their chemical composition.
Specialty products manufactured by chemical producers include:
- Polymers
- Resins
- Lubricants
- Inks
- Adhesives
This market’s manufacturers emphasize compliance, risk evaluation and management, quality assurance, and efficient formula management. The government strictly regulates specialty chemical manufacture and distribution to decrease the hazards caused by specific chemicals in the process.
Steel and Aluminum Processing
Steel and aluminum processing is the backbone of most economies. Process manufacturers often recycle the metals, with some using traditional mineral ores as raw materials in a way similar to other mineral-based industries.
Products from the steel and aluminum industries feed other industries. Aluminum and steel are raw materials utilized to produce various other items, including heavy machinery, construction materials, and railway wagons.
Textiles
The textile industry centers primarily on designing, developing, manufacturing, and distributing textile and fabric materials such as yarn, cloth, and apparel. The raw material can be natural or synthetic, utilizing chemical industry products.
Like many other industries, textiles are subject to national and international regulations that manufacturers comply with to guarantee high quality, safety, and sustainability.
FAQs
With the breakdown of process manufacturing, it’s time to dig into the frequently asked questions.
What does manufacturing mean?
In the realm of business, understanding the manufacturing meaning is crucial for companies aiming to optimize their production processes and enhance overall efficiency. Manufacturing, in essence, refers to the systematic transformation of raw materials into finished goods through various processes. It encompasses the entire production cycle, from the initial conception of a product to its final assembly. Comprehending the manufacturing meaning in business involves a strategic focus on production costs and exploring cost reduction strategies.
Manufacturing costs play a pivotal role in shaping a company’s financial landscape. Direct and indirect costs are important to understand. Direct costs, involving expenses directly tied to the production of goods, and indirect costs, which encompass overhead expenses not directly attributable to specific products, constitute the two primary components of manufacturing costs. Conducting a thorough manufacturing cost analysis is essential for businesses aiming to identify areas for improvement and implement effective cost reduction strategies. This analysis not only helps in understanding the intricacies of production costs but also provides insights into streamlining processes, optimizing resource utilization, and ultimately achieving more economical and sustainable manufacturing practices across various industries.
What are the main types of manufacturing processes?
Manufacturing processes are a sequence of steps that include complicated operations, skilled labor, machinery, efficiency, and raw materials to produce a finished product. There are six main types of manufacturing processes, including:
- Repetitive Manufacturing
- Discrete Manufacturing
- Job Shop Manufacturing
- Continuous Process Manufacturing
- Batch Process Manufacturing
- 3D Printing
What are some examples of manufacturing processes?
Some of the top manufacturing processes markets are:
- Automotives
- Mobile phones
- Oil
- Metals
Final Thoughts
Process manufacturing can be the key to growing your manufacturing plant. However, manufacturing is a highly specialized industry that necessitates a more exceptional standard of specialization. So, companies progressively rely on ERP software and automation solutions to enhance routine processes and minimize manufacturing bottlenecks.
If you want to realize the benefits of process manufacturing, the easiest way is to choose a reliable ERP solution to implement and monitor the necessary interventions.