What is MRP? History, Definition, and How it Works
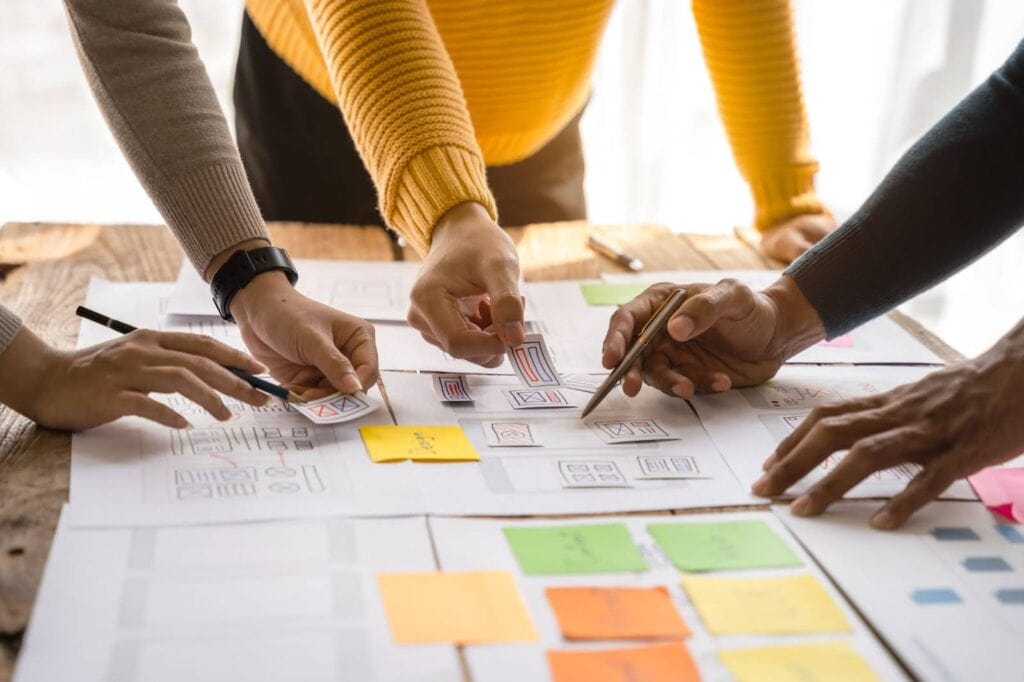
Running a manufacturing process without an organized system often leads to chaos—too many raw materials or not enough to meet customer demand. That’s where material requirements planning (MRP) comes in.
So, what is MRP? It’s a planning system that helps production managers calculate the materials needed, schedule production efficiently, and balance inventory levels with actual demand. MRP systems ensure that manufacturers have the raw materials needed for production while preventing unnecessary stock. MRP integrates with ERP systems to enhance overall business efficiency by unifying various departments such as finance, HR, and customer relationship management.
Due to demand fluctuations and supply chain issues, small business owners and logistics directors often struggle to maintain smooth production cycles. This guide will explain how MRP evolved, how it works, its pros and cons, and future trends to help businesses make informed decisions.
MRP History
Material requirements planning (MRP) was first developed in the 1960s to help manufacturers schedule and optimize manufacturing processes, balance inventory levels, and efficiently meet demand. The system aimed to reduce waste by organizing raw materials based on demand forecasts and production schedules.
Over time, MRP systems evolved into MRP II, adding capacity planning and shop floor control to enhance production control.
By the 1990s, enterprise resource planning (ERP) emerged as a more comprehensive system. It integrated material requirements planning with finance, human resources, and supply chain processes to unify operations across the entire organization and improve coordination and decision-making.
What is Material Requirements Planning?
Material Requirements Planning (MRP) is a system designed to calculate the raw materials needed and schedule production processes efficiently. MRP helps in creating a detailed production plan to ensure material availability by aligning inventory levels with actual demand, helping businesses avoid surpluses and shortages.
MRP breaks production into detailed steps using a bill of materials (BOM) and generates master production schedules for accurate timelines. By tracking inventory records and automating material requirements, MRP helps streamline the manufacturing planning process.
Many companies rely on MRP software to optimize resource allocation, reduce carrying costs, and enhance overall efficiency across their production schedules and supply chains.
Definition of MRP
Material Requirements Planning (MRP) is a computer-based system that helps manufacturers plan and schedule the materials and components needed to produce finished goods. It is a critical tool for effective manufacturing and supply chain management, enabling companies to optimize their production schedules, reduce inventory costs, and improve overall operational efficiency. By aligning material requirements with production schedules, MRP systems ensure that the right materials are available at the right time, preventing delays and minimizing waste. This systematic approach to material requirements planning helps businesses maintain a smooth and efficient manufacturing process, ultimately leading to better resource utilization and higher productivity.
The Importance of MRP
MRP plays a crucial role in managing supply chains and keeping operations on track. Key benefits include:
- Improves production efficiency: Ensures raw materials are available when needed, preventing production delays, reducing idle time, and optimizing resources such as labor, machinery, and materials for smoother operations and higher productivity.
- Minimizes stockouts and overstock: Prevents shortages and excess inventory by syncing sales forecasts with actual inventory requirements, ensuring businesses only store what’s necessary, reducing storage costs, and improving overall inventory control.
- Advances customer satisfaction: Maintains accurate delivery schedules by ensuring production timelines align with demand, allowing businesses to meet customer expectations for timely deliveries and avoid delays in fulfilling orders.
- Reduces manufacturing costs: Lowers operational expenses by avoiding excess raw materials, minimizing outdated stock, and preventing costly production stoppages caused by insufficient inventory or unexpected material shortages.
How Does an MRP Work?
MRP uses data such as production schedules, inventory data, and sales forecasts to calculate the material requirements for upcoming orders. It generates a comprehensive plan for production scheduling that outlines when to procure materials and when to begin production to schedule production efficiently.
Steps in the MRP Process
An MRP process consists of key stages that keep production moving smoothly. Here’s how it works:
- Gathering Inputs: MRP pulls essential data from demand forecasts, the master production schedule (MPS), inventory data, and the bill of materials (BOM) to ensure accurate material calculations and avoid production interruptions.
- Planning Requirements: The system calculates required materials and components, accounting for lead times and dependent demand, ensuring all necessary resources are available in time to support seamless production plans and avoid delays.
- Generating Outputs: MRP produces purchase orders for materials, work orders for production tasks, and updated production schedules that align with customer demand, preventing inefficiencies and ensuring resource allocation matches production timelines.
MRP Inputs
Accurate MRP performance relies on critical inputs that guide the planning process. These inputs provide data necessary for calculating material requirements and maintaining efficient production workflows.
- Demand Forecasts: Estimates future customer demand by analyzing market trends, historical data, and sales patterns to help businesses predict production needs and reduce uncertainty in material planning and inventory management
- Inventory Data: Tracks current stock levels of raw materials, components, and finished goods, ensuring the system can effectively balance existing inventory with material requirements to avoid shortages or excess stock.
- BOM (Bill of Materials): A comprehensive list that specifies every part, component, and raw material required to manufacture a product, serving as a crucial blueprint for calculating material needs accurately.
- Master Production Schedule (MPS): Details which products need to be manufactured and their production timelines, helping businesses align production tasks with resource availability and forecasted demand for smooth operations.
MRP Outputs
The outputs generated by an MRP system provide actionable instructions for managing production and inventory. These outputs ensure that materials and tasks are aligned with production goals.
- Order Recommendations: Generates purchase orders for materials and components needed to complete the production cycle, specifying quantities and delivery timelines to avoid material shortages or production halts.
- Production Schedules: Outlines timelines for when each production task must be completed, ensuring that all resources are available and utilized efficiently to keep operations running smoothly without delays.
- Inventory Reports: Offers real-time insights into stock levels and future material needs, providing visibility into inventory trends to support effective decision-making and avoid overstock or inventory gaps.
- Work Orders: Provide detailed instructions to production teams, specifying tasks, deadlines, and required resources to guide daily production operations and ensure each product is manufactured as planned.
Benefits of an MRP System
MRP systems help businesses optimize production processes by improving resource allocation and reducing inventory levels. This boosts overall manufacturing efficiency and ensures businesses can meet demand consistently.
Let’s discuss the key advantages of an MRP system:
- Inventory Optimization: Maintains appropriate inventory levels to avoid overstock and shortages. Accurate material planning prevents excess stock, reducing carrying costs and freeing up cash flow for other operational needs.
- Cost Savings: Reduces unnecessary expenses related to overproduction and surplus raw materials by ensuring purchase orders align with sales forecasts, helping businesses optimize procurement and avoid wasteful spending.
- Improved Production Efficiency: Ensures timely availability of materials during production schedules, preventing bottlenecks and minimizing downtime to keep the manufacturing process efficient and on track.
- Better Resource Allocation: Distributes labor, materials, and machinery effectively using master scheduling, optimizing production capacity, and preventing resource overburdening during peak periods.
- Advanced Customer Satisfaction: Strengthens customer trust by ensuring timely deliveries through accurate delivery schedules, reducing order delays, and meeting expectations for faster order fulfillment.
Disadvantages and Challenges of an MRP System
Despite its many advantages, MRP systems come with challenges that businesses must address to ensure smooth implementation and operation.
Here are the potential challenges to look for:
- Initial Setup Costs: Investing in MRP software and necessary hardware can be expensive, particularly for smaller manufacturing companies. Customizations, staff onboarding, and infrastructure upgrades often add to upfront implementation expenses.
- Complexity: Requires comprehensive training for human resources to handle inventory data efficiently and navigate the planning system properly. Lack of expertise can result in costly errors and delays in production operations.
- Reliance on Data Accuracy: Errors in inventory records or inaccurate forecasted demand can cause material shortages or overstock, leading to disruptions in production planning and increased carrying costs for surplus materials.
- Software Maintenance: Regular updates and system maintenance are crucial for maintaining MRP functionality. Outdated existing systems can cause downtime, disrupting production timelines and affecting overall business continuity.
Who Uses MRP Systems
Many industries rely on MRP systems to keep their operations streamlined and ensure efficient supply chain management. These systems benefit businesses of all sizes that want to effectively manage inventory and maintain smooth production cycles.
- Small to Medium-Sized Manufacturers: Manage production processes and inventory with limited resources by using MRP material requirements to optimize resource allocation, reduce costs, and maintain competitiveness in the manufacturing market.
- Large Manufacturing Enterprises: Coordinate complex production schedules and global supply chains by leveraging MRP II system capabilities, ensuring effective capacity planning and resource distribution across multiple production facilities.
- Logistics Directors: Oversee material requirements planning and procurement, using MRP systems to enhance supply chain efficiency, reduce material lead times, and ensure timely deliveries for uninterrupted production flows.
- Suppliers in Manufacturing Chains: Collaborate with large manufacturers to provide timely raw material deliveries by syncing their MRP software with client schedules, ensuring smooth production cycles and meeting deadlines consistently.
MRP systems can be tailored to fit different industries and business sizes, offering cloud-based MRP software options for smaller businesses or more robust enterprise-level systems for larger organizations.
MRP in Manufacturing
MRP systems are essential tools in the manufacturing sector for managing production schedules, controlling inventory, and planning material procurement. These systems streamline operations and ensure every resource is utilized effectively.
- Production Planning: Aligns material availability with scheduled production tasks, ensuring timely resource allocation and preventing delays caused by missing components, which helps maintain efficient production schedules and avoid downtime.
- Lean Manufacturing: Minimizes waste by producing only necessary quantities, supporting just-in-time processes, and preventing overstocking of raw materials, which improves overall inventory control and optimizes resource use in the manufacturing process.
- Supply Chain Coordination: Synchronizes operations between manufacturers and suppliers to maintain seamless supply chain planning, reduce material lead times, and minimize disruptions in production due to delayed resource deliveries.
MRP Systems
MRP systems are designed to automate the production planning and scheduling process, taking into account factors such as sales forecasts, current inventory levels, bills of materials, and the master production schedule. These systems provide a comprehensive view of the manufacturing process, enabling companies to make informed decisions about production, inventory, and supply chain management. By integrating various data points, MRP systems help businesses streamline their operations, reduce lead times, and improve overall efficiency. This holistic approach to production planning ensures that all aspects of the manufacturing process are aligned, from material procurement to final product delivery, resulting in a more cohesive and responsive supply chain.
Legacy vs. Modern MRP Software
Legacy MRP systems were typically on-premise solutions that required significant investment in hardware and software. They were often inflexible and difficult to integrate with other business systems. Modern MRP software, on the other hand, is cloud-based and offers greater flexibility, scalability, and integration with other business systems. Modern MRP software also provides real-time visibility into the manufacturing process, enabling companies to respond quickly to changes in demand or supply chain disruptions. This shift from traditional to modern MRP systems allows businesses to leverage advanced technologies, such as AI and machine learning, to enhance their production planning and inventory management capabilities, ultimately leading to more agile and efficient operations.
Choosing the Right MRP System
Choosing the right MRP system depends on several factors, including the size and complexity of the manufacturing operation, the level of customization required, and the need for integration with other business systems. Companies should consider the following factors when selecting an MRP system:
- Scalability: Can the system grow with the business?
- Flexibility: Can the system be customized to meet specific business needs?
- Integration: Can the system integrate with other business systems, such as ERP and CRM?
- User interface: Is the system user-friendly and easy to navigate?
- Support: What level of support does the vendor provide?
By carefully evaluating these factors, businesses can select an MRP system that aligns with their operational needs and supports their long-term growth and efficiency goals.
MRP vs. ERP
Many confuse MRP systems with enterprise resource planning (ERP), but these systems address different operational needs. Businesses need to evaluate whether to implement MRP and ERP systems based on their operational requirements, as both improve efficiency but serve unique purposes within an entire organization.
- Material Requirements Planning (MRP): Focuses solely on production planning, managing inventory levels, and calculating material requirements to ensure manufacturing resource planning aligns with customer demand and production goals.
- Enterprise Resource Planning (ERP): Integrates multiple departments such as human resources, finance, and supply chain management, providing a unified control system for overall business operations, including manufacturing orders.
MRP boosts production schedules, while ERP offers a comprehensive resource planning approach for broader business functions. Depending on needs, businesses may choose one or use both for maximum efficiency.
MRP I vs. MRP II
Traditional MRP (MRP I) emerged as a material requirements planning tool for managing inventory and scheduling production. It relied on master production schedules, inventory requirements, and BOMs to accurately predict material needs.
MRP II expanded on this by adding capacity constraints, financial tracking, and shop-floor coordination. It provided more control over the entire manufacturing process, ensuring seamless integration with resource planning and improving task synchronization.
Modern MRP software blends features from MRP I and MRP II, helping businesses maintain optimal inventory control while addressing broader challenges in the manufacturing sector.
How MRP Enables Effective Inventory Management
MRP enables effective inventory management by providing a comprehensive view of the manufacturing process and enabling companies to optimize their production schedules and inventory levels. MRP systems can help companies to:
- Reduce inventory costs: Minimize excess inventory and avoid stockouts by aligning material procurement with actual production needs.
- Improve inventory turnover: Optimize production schedules and inventory levels to ensure a steady flow of materials and finished goods.
- Enhance supply chain visibility: Provide real-time information about inventory levels and production schedules, enabling better decision-making and coordination.
- Boost customer satisfaction: Ensure that products are available when needed, leading to timely deliveries and improved customer trust.
By integrating MRP with other inventory management systems, companies can gain a comprehensive view of their inventory and make informed decisions about production, inventory, and logistics. This holistic approach to inventory management helps businesses maintain optimal stock levels, reduce carrying costs, and improve overall operational efficiency.
How to Implement an MRP System
Introducing an MRP system requires understanding business needs, proper software selection, and ongoing staff training to optimize production planning and resource allocation.
- Assess Business Needs: Evaluate inventory management processes, identify material shortages, and determine how MRP can improve scheduling production based on actual customer demand and future inventory requirements.
- Select the Right MRP Software: Research cloud-based MRP software or local systems based on company size. Ensure the chosen system supports scalability and offers effective inventory management for changing production goals.
- Train Staff and Monitor Progress: Teach employees how to use the control system and monitor data accuracy. Regularly review the capacity planning processes and make necessary adjustments to maintain optimal performance.
Accurate data and continuous system evaluation are crucial for meeting long-term production goals and avoiding inefficiencies.
The Future of MRP
MRP systems are evolving through automation and AI-driven resource planning that adapts to changes in customer demand. Predictive algorithms improve inventory management systems by anticipating future production needs.
Cloud-based MRP software enables real-time access, allowing businesses to track manufacturing orders and production schedules remotely. Enhanced customization and automated material planning are also driving improvements in manufacturing efficiency, making MRP systems more adaptive and precise.
Conclusion
Understanding what MRP is helps businesses improve production planning and maintain better inventory control. By aligning material requirements planning with actual demand, MRP systems optimize the master production schedule and reduce carrying costs.
These systems ensure businesses meet demand efficiently by organizing material requirements and reducing delays. MRP material requirements planning not only improves operational workflows but also minimizes inventory levels to avoid surplus.
Whether integrated with an ERP system or used independently, MRP supports master scheduling and balances independent demand. Businesses that aim to streamline operations and boost performance can greatly benefit from adopting a robust MRP system.