10 Tips: Optimizing E-Commerce Fulfillment Operations
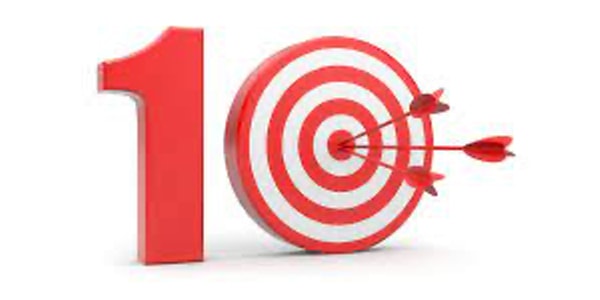
E-commerce sales are projected to continue rising steadily. In this environment, it is more important than ever for retailers and brands to fill orders quickly, seamlessly, and cost-effectively. Here’s how your fulfillment operations can optimize performance.
1. Allocate sufficient resources for fulfilling orders. Picking, packing, and shipping online orders is resource-intensive. E-commerce fulfillment operations can require two to three times the space and labor of traditional warehousing operations, so factor these requirements into your plans up front.
2. Maximize picking capacity. Design your warehouse to increase storage density and maximize picking capacity. E-commerce facility design typically incorporates higher ceiling heights (36 feet or higher), narrow aisles, and high-density storage solutions.
3. Plan for growth and fluctuations. Since your business is always growing and evolving, it is important to build flexibility into fulfillment operations. Design your fulfillment solution with scalable space, staffing, processes, and technologies, so you can ramp up and down quickly and easily. If you plan to add additional sales channels (i.e., brick-and-mortar stores, subscription services, third-party marketplaces), make sure your fulfillment operations can support multiple channels and order profiles. And always keep safety and ergonomics in mind as you design processes.
4. Invest in advanced technology. Automation, large-scale mechanization, and robotics can help fulfillment operations achieve peak performance. With the right solution, you can improve productivity, reduce labor dependency, control operational costs and flex to accommodate business fluctuations. When implementing new technology, make sure you have the right back-end infrastructure to support these initiatives—systems, leadership, etc.
5. Take a strategic distribution approach. The closer products are to the end customer, the faster and more economically they can be delivered. Utilizing two or more distribution centers in strategic locations can help you deliver orders to consumers more quickly and cost-effectively—often within two days via ground service. Another option is to locate your fulfillment centers to ensure ready access to parcel service providers.
6. Optimize inventory. Map out processes for receiving, replenishment, inventory slotting, and pack out to ensure optimal efficiency and service levels. If you store products in multiple locations, utilizing an order management system (OMS) can provide visibility enterprise-wide and help determine the optimal fulfillment source for each order. An OMS can also help you provide customers with real-time inventory availability and order tracking information.
7. Consider postponement. Moving value-added services such as kitting, labeling, and embroidery closer to the customer allows you to delay product configuration or customization until the last possible moment. This can often help you be more responsive to customer demand, better manage inventory, expand product offerings, and get to market faster.
8. Explore your parcel options. Record volume will continue to drive up parcel rates and surcharges, so your best bet to control costs is through efficiency and optimization. You may be able to broaden your carrier strategy with regional carriers or postal workshare options or take advantage of zone skipping to sortation hubs. Distribution modeling and rate shopping software can help to find the most efficient and cost-effective shipping options to meet service expectations.
9. Anticipate returns. To provide hassle-free returns and quick refunds, ensure that your information systems, distribution network and transportation capabilities work in tandem. Returns processing can be labor-intensive and require experienced employees with strong decision-making skills to evaluate merchandise and determine next steps, so factor that into your staffing plans.
10. Commit to continuous improvement. Look for ways to improve efficiency at every step in the fulfillment process. Quality methodologies such as Lean Six Sigma can help to increase efficiency, improve throughput, ensure accuracy, and control costs.
SOURCE: Bobby Hays, Regional Vice President, Operations, Saddle Creek Logistics Services