From Earnings to Ergonomics: Optimizing Warehouse Labor
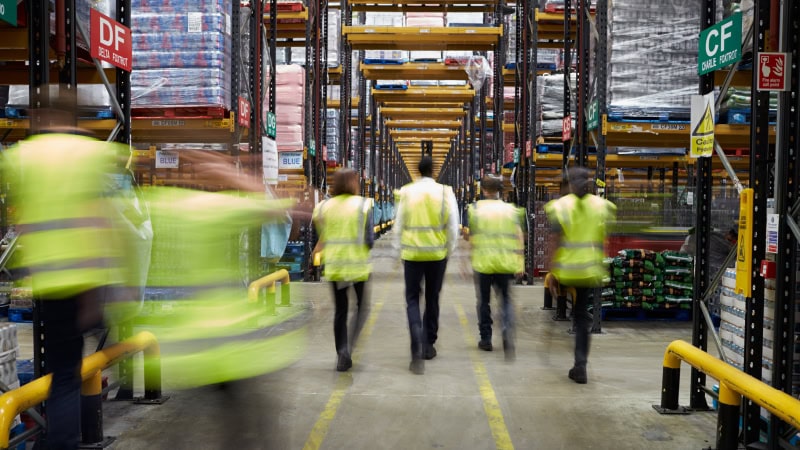
As warehouse labor plays hard to get, organizations turn to a growing range of tools and technologies to support worker safety, boost their productivity, and make their jobs easier, more efficient, and even more enjoyable.
A few decades ago, warehouse workers were mostly assumed to be at either the beginning or the end of their careers, says Mark Fralick, chief technology officer with Softeon, a supply chain solutions provider. Recently, however, these roles have become more professional, with better pay and greater opportunities for advancement.
“Training workers who are on the floor to become managers and leaders—that has been a big change,” Fralick says.
Even as these roles became more professional, companies did not pay much attention to tools that could improve the actual jobs of warehouse workers. That’s changing as the labor landscape has grown more competitive.
To attract and retain warehouse employees, supply chain organizations are taking steps to make these jobs safer, less physically taxing, and more productive and enjoyable.
Warehouse employees have always been important both to supply chain performance and to their companies overall. More recently, their significance has increased, due in part to the growing “urgency of fulfillment” as consumers become accustomed to rapid, accurate deliveries, says Akash Gupta, co-founder and CEO of GreyOrange, a provider of warehouse fulfillment solutions.
The location of many newer warehouses also comes into play. “We put the warehouses a lot closer to where the consumer is,” says Andre Luecht, global strategy lead for transportation, logistics, and warehouse with Zebra Technologies Corporation. That typically means facilities located in suburbia rather than the generally less-expensive exurbs.
Another factor is the turnover rate for many warehouse workers, which can approach 200%, says Matthew Hart, founder and CEO of Soter Analytics, which leverages AI-driven wearables. That drives up hiring and training costs.
Newer employees also tend to be less productive, as well as at greater risk of injury as they learn their jobs.
Technology for Workers
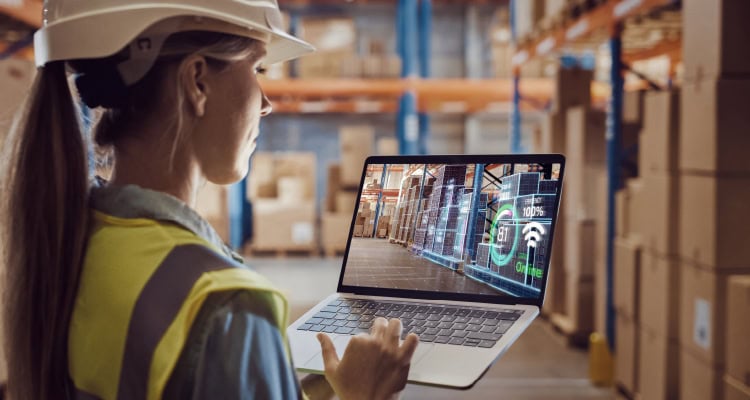
Software such as Korber’s Slotting Solution optimizes inventory placements in warehouse storage areas to increase order picking and replenishment efficiency. Benefits include improved staff productivity, higher order throughput and more efficient use of storage space.
Technology can help supply chain organizations support their warehouse employees. Tools include pick-to-light systems that enhance worker productivity, wearables that can make jobs safer, gamification apps that can boost morale, and cobots that can make their jobs easier.
Many warehouse workers spend about 60% of their time picking, says Adam Kline, senior director of product management with Manhattan Associates, a provider of supply chain solutions. On top of this, about 40% of each pick is non-value-added work that typically includes traveling.
“Technology provides a huge opportunity to drive optimization,” he adds. For example, a hybrid pick cart lets workers complete multiple functions—such as picking, replenishment, and cycle counting—in one rather than multiple runs.
Another benefit of many tech solutions that increase worker productivity, like robotics, is their ability to slash required training time from weeks to hours. “A worker could literally come in off the street having never picked in a warehouse before, and by the end of day one be fully productive,” says John Santagate, senior vice president, robotics with supply chain solutions provider Körber.
With many of these tech tools, workers no longer need to immediately learn where certain products are kept or how the aisles are laid out. Instead, they can refer to a screen that shows a graphic of the product and quantity to be picked.
Here’s a look at some tech tools that are contributing to warehouse worker safety and productivity.
Pick-to-light optimizes warehouse operations. “Getting the most out of the warehouse labor force has been a key goal,” says James Wilkinson, CEO with Balance One Supplements, a family-owned supplements business.
The company struggled with labor scheduling and planning, and wanted to improve workflow volume and the rate of errors occurring during item picking.
“Pick-to-light software was a crucial addition for us,” Wilkinson says. Warehouse pickers simply follow the light, eliminating time they’d otherwise spend searching for product locations.
Picking times have dropped by 25% because warehouse pickers receive visual cues that tell them where items are located, which accelerates their ability to find specific items.
Balance One also minimized stockouts by 30% through an improved inventory management system and replenishment process. In addition, overtime costs fell by up to 15%.
“Pick-to-light software has transformed our warehouse,” Wilkinson says. The software helped Balance One optimize its labor force and improve accuracy, while the data and analytics allow quick responses to different business situations.
“With pick-to-light, we were able to elevate our warehouse operation to new levels of efficiency, responsiveness, and cost-effectiveness,” he notes.
Slotting streamlines effort and material flow. Slotting solutions help optimize warehouse worker efforts. “Workers put items into places where they need to be, creating a more optimized pick flow,” explains Santagate.
A common example is placing fast-moving items where they’re easily accessible. Workers can complete their jobs with fewer steps, which can lower frustration. And material moves through the warehouse more quickly.
Leveraging mobile devices. For workers using mobile devices, such as handheld scanners, the goal is to optimize the ergonomics of the interactions, Fralick says.
Touch screens also can help, particularly when paired with navigation software to let workers know, for instance, when to move to another aisle. “The solution gives hints so workers don’t have to decode things in their head to determine whether they need to move left or right,” he says.
Text-to-speech systems help heterogeneous workforces. As more workforces become heterogeneous, warehouse management systems that incorporate text-to-speech capabilities in a worker’s native language can let them quickly know which task to tackle next, says Suresh Bhaskaran, senior director, product management, with Softeon. This cuts frustration while increasing efficiency.
Computer vision and AI. When it comes to computer vision solutions driven by artificial intelligence, “the floodgates have opened,” says Chandler Grant, senior innovation manager with Kenco, a third-party logistics provider based in Chattanooga, Tennessee.
“While information is power, gathering it has, until recently, been cost-prohibitive due to the expense of purchasing and installing sensors,” he says.
Now, however, artificial intelligence can, for instance, analyze security camera feeds for information related to safety and operations, while mobile robots or drones can patrol routes while monitoring inventory status and housekeeping concerns.
Cobots and robots boost worker productivity. Mobile robots can drive worker productivity through a range of approaches. Some include screens that direct workers to, for instance: Pick Shirt A from Location B, scan to make sure it’s the right one, place it in Tote C, and then head to the closest next robot for the next pick.
Goods-to-person robotics bring work to the employee, eliminating much of the walking they’d otherwise have to do. “That drives productivity and efficiency,” Santagate says.
Like their robot cousins, cobots, which are designed to work safely alongside humans, can play a crucial role in enhancing efficiency and safety for warehouse workers, says Michel Spruijt, president of Brain Corp International, an autonomous technology company. By assisting with repetitive and labor-intensive tasks, such as picking and packing, cobots drive efficiency. Their ability to collaborate with human workers reduces the time workers need to spend on these tasks.
By handling tasks that are physically demanding or potentially hazardous, such as lifting heavy objects, cobots can reduce the risk of injury. They can also operate continuously without fatigue, ensuring consistent performance while minimizing strain on workers.
WMS: The brains of warehouse operations. Warehouse management systems (WMS) continue to add value as the brains of warehouse operations. And, by incorporating technologies like artificial intelligence and machine learning, a WMS can identify patterns in work execution, so warehouse managers can intelligently redistribute labor, making employees’ workloads more even and efficient.
Ensuring warehouse resources, such as workers, robots, or conveyor systems, take the right actions at the right times has become critical, given the growth in ecommerce orders, which are notoriously unpredictable, along with the demand for next- or same-day delivery.
Assume, for instance, a product that was supposed to take off is, instead, languishing, while a different product is moving like gangbusters. Adjusting requires “real-time orchestration” of available resources through the use of sophisticated algorithms, rather than the static plans of the past, Gupta says.
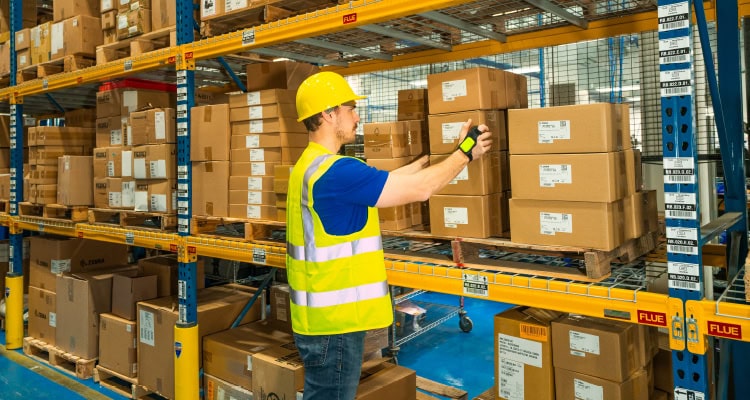
Tools such as Zebra’s RS2100 wearable scanner increase worker comfort and dexterity. Its back-of-hand design and unique mount leaves the palm unobstructed, providing complete freedom to handle items. And the low profile enables easy picking in tight spaces.
Solutions to improve safety. The past 10 years have seen significant jumps in technology solutions that can enhance worker safety and protection. These include ergonomic improvements such as exosuits, adjustable pallet stands, training devices, and lift-assist devices.
Today’s autonomous guided vehicles (AGVs) tend to be better for worker safety than powered industrial vehicles (PIVs) “AGVs are driven by a concrete set of instructions, following predictable paths and making predictable movements,” Grant says. “They have safety sensors that mandate that they travel at x speed when an object is y far away. If anything enters that zone of protection, the vehicle will stop.”
In contrast, PIVs are subject to the whims of the person driving them.
The current focus on safety also encompasses tools that can reduce or eliminate jobs that can lead to injuries over time. For instance, some jobs require workers to push carts weighing hundreds of pounds up and down concrete warehouse floors. This strains worker’s bodies, which isn’t good from a health, nor a productivity standpoint.
Tools such as slotting solutions, robotics, and voice picking can remedy this, often by reducing the distances employees must travel.
“The more a warehouse can bring the products to workers, optimize their pick paths, and reduce the physical walking that workers have to do in the facilities, the less strain you can put on them,” Santagate says.
CCTV and virtual reality boost safety. Closed circuit television (CCTV) enhanced with AI can collect data that lets managers zero in on a potential danger areas, Hart says.
For instance, a camera might show that a blind spot at a particular corner is causing numerous near misses between forklifts and employees. Artificial intelligence automates the process of analyzing the CCTV footage, so managers can more quickly and easily identify the near misses and their locations. Once the problem and its location have been identified, an effective solution can be developed.
The data can be anonymized, keeping the identity of any employee private. The focus is on making work safer, and not on employee behavior, Hart says.
The Protex AI solution, for example, processes video feeds to autonomously identify and report safety incidents and near-misses.
Virtual reality (VR) is being used in interesting applications, such as training simulations. These simulations train an individual on the proper operation of large machinery that would be unsafe to operate without practice.
One notable example is pilot training; Kenco is considering this for forklift training, Grant says.
Attracting, retaining, and engaging workers. Organizations with engaged employees perform better on just about every metric. This includes profitability, productivity, safety incidents, and turnover and absenteeism, according to a recent Gallup report.
One way supply chain organizations can boost employee engagement is through gamification, or integrating game elements, like friendly competition and points, into the work world.
“It’s not just money that motivates, it’s also being able to enjoy your job and some friendly competition,” Kline says. Gamification can turn a tough job into something better.
Using tools and technologies that support workers can pay off in increased safety, productivity, morale, and performance. Says Santagate: “Labor management plays a significant role in driving an operation’s future value.”
Wear It’s At
Wearables can help warehouse workers do their jobs more safely and efficiently. For instance, wearable computers with dual voice picking capabilities are useful for moving large objects, as many can be worn on an arm or clipped to a belt with a ring scanner.
“The user does not have to juggle a mobile computer at the same time,” says Kevin Beasley, chief information officer with VAI, an ERP provider.
An emerging solution is visual wearables that enable augmented reality and can assist warehouse workers in their jobs. One example is software that can help workers load pallets more efficiently and effectively.
For instance, the Soterspine (pictured) can identify body motions that can create cumulative musculoskeletal injuries, such as lifting objects from the floor using lower back muscles.
And as the technology behind VR/AR progresses, the headsets will become more lightweight with more battery capacity and processing power.
While it’s hard to predict what programs will be developed for logistics once workers can wear these headsets casually throughout an entire workday, potential options include programs that guide users to destinations and display holographic models to demonstrate optimal product positioning atop pallets or within freight containers.
MERCEDES DRIVES PRODUCTIVITY WITH ROBOTS
In its quest to roll out humanoid robots, Austin, Texas-based Apptronik says it will collaborate with Mercedes-Benz on “identifying applications for highly advanced robotics in Mercedes-Benz Manufacturing.”
The car maker’s goal is to automate low-skill manual labor tasks that tend to be physically demanding and, therefore, hard to staff. These tasks will likely include moving totes or assembly kits to production lines, as well as inspecting parts.
The pilot plans to leverage the Apollo (pictured), which is Apptronik’s commercial bot that has been purpose-built for mass manufacturing. The company says its humanoid will start in plants and warehouses and eventually extend to other applications, including construction and retail.
The Mercedes announcement follows other efforts to combine humanoid robotics with factory objectives. Amazon is testing its Agility Digit bots for warehouse fulfillment tasks, while BMW is partnering with Figure to reportedly use humanoids for assembly work.
In many cases, facility design drives the benefits of using the humanoid form factor. Instead of redesigning facilities, equipment, or processes to accommodate a uniquely sized and configured robot, this approach does the opposite: it tailors the automation to the existing environment.
To that end, the Apollo should fit right into the existing space at Mercedes-Benz. Apptronik says its bot measures 5 feet 8 inches tall, weighs 160 pounds, and features the ability to lift 55 pounds.