Process Manufacturing vs Discrete Manufacturing: Definitions and Differences
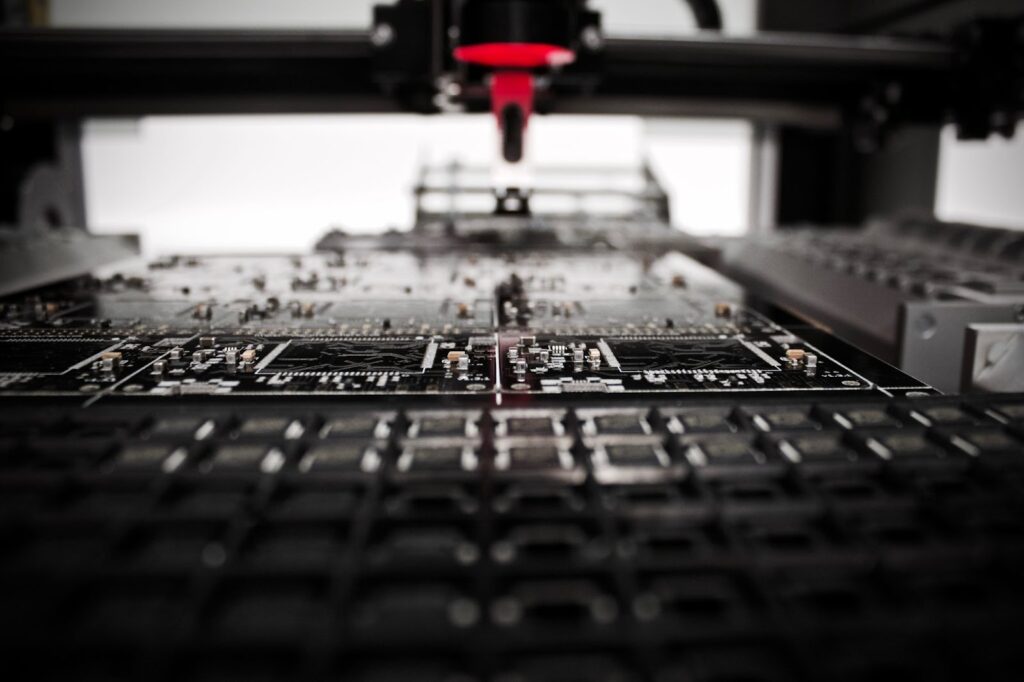
Manufacturing is the large-scale process of converting raw materials into finished products, utilizing factors of production, including human labor and machinery. Depending on the product requirements, you can use various manufacturing processes to get the desired output.
Discrete manufacturing and process manufacturing are the most common production methods. In this article, we explore the two manufacturing processes, highlighting the key differences and similarities.
What Is Process Manufacturing?
Process manufacturing involves mixing raw ingredients using specific recipes and conditions to produce finished goods. The production formula in process manufacturing results in a particular volume of desired output rather than single units. So, process manufacturing typically occurs in bulk quantities.
Often, ingredients in process manufacturing undergo an irreversible physical process or chemical reaction that changes the form of the original components.
This production method is commonly used in process industries with bulk output, including:
- Pharmaceuticals
- Cosmetics
- Food and beverages
- Specialty chemical products
- Paints and coatings
- Personal care products
- Plastics
Consider the production of tomato ketchup—the primary ingredients that make ketchup include sugar, tomatoes, seasoning, vinegar, and water. The basic step of producing tomato ketchup involves filtering the water, adding and blending the ingredients, and sterilizing the packing jars. After the final step of the manufacturing formula, you can’t separate the finished product into the initial components.
Since process manufacturing is unique and requires specialized production activities, you should consider taking advantage of an Enterprise Resource Planning (ERP) solution. It helps you streamline your operations, guarantee high quality, meet compliance, safeguard the safety of consumers, and ensure timely deliveries.
Key Features of Process Manufacturing
There are various features to consider while selecting a reliable ERP solution for process manufacturing. Below are critical aspects of this production method.
Lot Tracking and Traceability
Process manufacturers typically operate in highly regulated industries, so tracking and traceability are vital considerations. ERP software for process manufacturing should offer end-to-end batch traceability, allowing you to respond effectively to any issue that may arise along the production line.
Batch/Recipe Management
Considering the complicated nature of process manufacturing recipes, your ERP solution should support the generation of new formulas, manage new recipes, meet quality control provisions, and track production data.
If you’re a batch process manufacturer, you need a recipe formulation function to cut down on time spent on laborious calculations and expensive mistakes. It’s easier to handle numerous versions of formulae and recipes and keep track of modifications with the help of industry-specific unique ERP solutions.
Shelf Life
The shelf-life of products in process manufacturing is a growing concern. It’s essential to have built-in, ready-to-use functions in your ERP solution that notify you whenever your products are approaching or surpassing their expiration date since raw materials and finished products lose their usability after a specified period.
An ERP solution that solves shelf-life issues allows your company to enhance consumer safety and comply with industry-specific regulations.
Disadvantages of Process Manufacturing
While process manufacturing boasts its fair share of perks, it also comes with various drawbacks. Here are some disadvantages of process manufacturing.
Costly and Time Consuming Machinery Maintenance
With the continuous production nature of process manufacturing, machinery breakdowns are typical at any time. Such breakdowns can occur during production, resulting in profit losses and downtime. Also, machinery maintenance can be costly and time-consuming, especially for new technicians.
To help prevent unanticipated downtimes, you can install IoT sensors in your equipment to receive notifications when they require a tune-up or full-on maintenance.
Customizing Difficulties
If your company needs to create customized products for each consumer, a single recipe is unlikely to yield satisfactory results. Process manufacturing is ideal for firms that make standardized products in bulk quantities.
However, this is not the case for bespoke production. You must find a flexible ERP solution that features all the essential production tools for your industry.
What Is Discrete Manufacturing?
Discrete manufacturing employs a nonparallel production method to create a finished product. This production method is called ”assembling manufacturing” since it involves creating a finished product from distinct individual parts or units of production.
Some of the industries that utilize discrete manufacturing include:
- Automotive
- Tech and electronics
- Clothing
- Machinery
- Military systems
- Furniture
- Toys
The assembling processes occur in various production phases and at different workstations. For instance, smartphone manufacturing features various components; LCD screen, motherboard, camera, battery, and more. These components are assembled independently in distinct production stages before being built into a single product in the final stage.
Discrete manufacturing uses Bill of Materials (BOMs) to list the components that make up the finished product, keeping the typically complicated manufacturing process under control.
Key Features of Discrete Manufacturing
A discrete manufacturing ERP system offers a unique set of resources, but there are key features to remember when shopping for ERP software applications for your company.
Here are the key features of discrete manufacturing.
Material Requirement Planning
Efficiently plan and distribute resources, including labor, raw materials, other inventory items, equipment, and tools, to the priority jobs and projects. To obtain the optimal production methods, use quality control and purchase planning.
Inventory Management
To avoid unanticipated shortages or unnecessary overstocking, receive real-time inventory notifications. Some programs even allow you to set minimum quantity thresholds to avoid running out of production components entirely. You may also use inventory management software to set minimum stock levels for every commodity so that when you reach these levels, you’ll replenish your inventory automatically.
Supply Chain Management
Gain real-time insight into your supply chain, expedite goods and material flows, improve supplier relationships, and reduce system defects.
Disadvantages of Discrete Manufacturing
Despite its numerous benefits, the major downside of discrete manufacturing is that it involves complex processes.
Complex Manufacturing Processes
Unlike process manufacturing which features a single production formula, discrete manufacturing has numerous unique production paths for every finished product.
Machined components may have several pathways, and optimization involves selecting the best path for each product. For example, this might imply altering process equipment run orders depending on supply or maintenance schedules or returning items for overhauling or repairs following an inspection.
Comparing Process Manufacturing With Discrete Manufacturing
One of the easiest ways to tell apart discrete and process manufacturing is to start with the final product and work your way back. Discrete manufacturing produces output products like mobile phones and clothes. Such products feature pieces assembled using various fixings and may be disassembled subsequently.
Conversely, process manufacturers create products you can’t disassemble into separate components, such as soft drinks and paints. Instead, these items are formed from elements combined in an irreversible process.
Unlike discrete manufacturers who rely on BOMs, process manufacturers utilize formulae or recipes to specify the components of their products.
FAQs
Let’s look at the frequently asked questions of process manufacturing vs. discrete manufacturing.
What are the four types of manufacturing processes?
Manufacturing involves several processes, but four primary processes are a cornerstone of manufacturing across most industries.
These manufacturing processes include:
- Casting and molding
- Machining
- Joining
- Shearing and joining
What is the difference between a process-oriented industry and a discrete manufacturing-oriented industry?
Process-oriented industries rely on recipes and formulae to create final products that you can’t disassemble through physical or chemical reactions.
On the other hand, discrete manufacturing-oriented industries are assembly-based, using distinct manufactured components to create finished goods through sequential production steps.
What is the difference between discrete and continuous manufacturing?
Process manufacturing depends on multiple distinct formulae or processes to make a product, while continuous manufacturing assembles components in a predetermined end-end method to generate a unique product.
Final Thoughts: Process Manufacturing vs. Discrete Manufacturing
Discrete and process manufacturing industries are worlds apart. Their methods, procedures, compliance, terminology, and so on differ significantly. So, manufacturing has no one-size-fits-all ERP software.
Whether you utilize process manufacturing or discrete manufacturing, you’ll want to find an ERP software that is particularly well-fitting for your manufacturing model. It will cut implementation time and costs because the demand for modification will significantly drop.