Raw Materials Inventory: Explanation, Benefits, and Tips
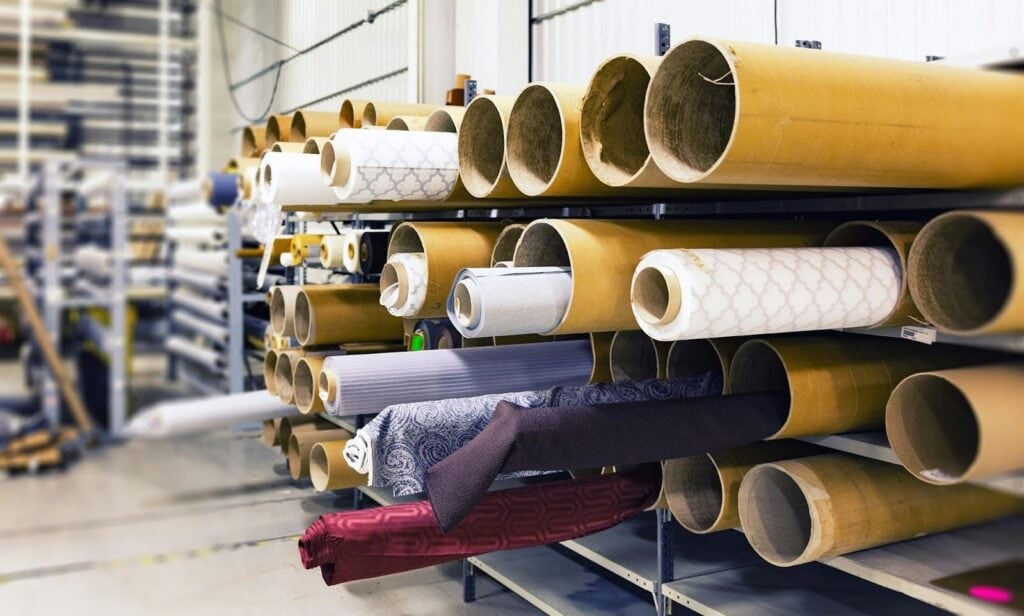
Understanding how to manage raw materials inventory is crucial for smooth business operations. By implementing best practices like regular audits, using software, and improving inventory turnover, businesses can control costs and optimize their production process.
Small business owners rely on raw materials inventory to keep production running smoothly. Managing these materials ensures you have enough supplies to meet customer demand without overstocking. Efficient raw material inventory management helps streamline the production process, reduce costs, and avoid delays in manufacturing.
Calculating raw materials inventory can be challenging for those new to tracking raw materials. Keeping accurate records of beginning raw materials inventory, raw materials purchased, and ending raw materials inventory is crucial for maintaining proper inventory management.
In this blog, you’ll learn how to manage raw materials inventory, calculate it, and apply best practices for your business.
What Is the Raw Materials Inventory?
Raw materials inventory refers to the raw materials that a business uses to produce goods. These materials can include everything from direct raw materials inventory like metal or fabric to indirect materials like cleaning supplies used in manufacturing. Without accurate tracking, a business might struggle to meet production needs.
Raw materials are just one part of a company’s inventory. Other categories include finished goods and work-in-progress inventory. For example, a furniture maker might count wood as raw materials, while a completed chair represents a finished product.
Importance of Raw Materials Inventory
Accurate raw materials inventory is essential for smooth production and timely customer order fulfillment. When businesses carefully track their materials, they avoid production delays caused by shortages and reduce the need to hold too much stock.
Maintaining correct inventory levels also supports cost management and optimizes the supply chain. Businesses can control operating costs and free up cash flow by ensuring they have just enough stock to meet demand.
Accurate raw materials inventory management leads to better decision-making in purchasing and production planning.
How to Calculate Raw Materials Inventory
Tracking raw materials inventory accurately is key to maintaining smooth production and managing costs. Proper calculations ensure you always have enough raw materials without overstocking.
Beginning Raw Materials Inventory
Beginning raw materials inventory refers to the total amount of raw materials a business has at the start of an accounting period. This figure is crucial for tracking inventory changes over time.
To record it, businesses should conduct physical raw materials counts and maintain clear records on their balance sheet.
An inventory management software can simplify tracking by automating this process and ensuring up-to-date records.
Raw Materials Purchased
New purchases of raw materials during the accounting period are added to the inventory.
It’s important to keep accurate records of raw materials inventory purchased, including dates, quantities, and costs. This ensures that businesses can easily manage raw material inventory and account for the materials used in production.
Recording purchases properly helps maintain optimal stock levels and avoid material shortages.
Ending Raw Materials Inventory
At the end of an accounting period, businesses must calculate ending raw materials inventory. This value reflects the amount of unused materials left in stock.
Companies can perform inventory counts or use automated tracking methods to assess ending inventory. Regular assessments help ensure that enough raw materials are available for future production without tying up too much capital in excess inventory.
Raw Materials Inventory Formula
To calculate raw materials inventory, use the following formula:
- RMI = Beginning Raw Materials Inventory + Raw Materials Purchased − Ending Raw Materials Inventory
Each component plays a key role. Beginning raw materials inventory gives you a starting point, while raw materials purchased add to that figure. Subtracting ending raw materials inventory shows how much material was consumed during the period.
This formula helps businesses track the movement of their raw materials throughout the production process.
Benefits of Accurate Raw Materials Inventory
Accurate raw materials inventory management offers several advantages that keep businesses running smoothly and efficiently. Here are the key benefits you’ll gain by staying on top of your materials.
- Improved Production Efficiency: Managing your raw material inventory accurately prevents production delays. Having the right materials when needed ensures a continuous manufacturing process, leading to better use of resources and labor.
- Cost Savings: Properly tracking raw materials inventory helps reduce excess stock and minimize waste. It keeps inventory costs down and frees up cash for other critical business operations.
- Better Supply Chain Management: Efficient raw materials inventory management helps businesses respond to supply chain disruptions. By maintaining optimal stock levels, you avoid material shortages that could slow down production.
- Enhanced Financial Reporting: Accurate raw materials count reflects true inventory value on your balance sheet. This leads to more precise financial statements and improved decision-making regarding expenses and future investments.
- Reduced Risk of Overstocking: Accurate tracking ensures businesses avoid over-ordering materials. Too much raw inventory ties up capital and increases the risk of items becoming obsolete or expired.
In short, keeping accurate raw materials inventory improves production, cuts costs, and strengthens supply chain management for better business outcomes.
Raw Materials Inventory Management Best Practices
Effective raw materials inventory management is critical for smooth operations and cost control. Here are the best practices to manage your inventory more efficiently.
Regular Inventory Audits
Conducting regular audits ensures accurate records of your raw material inventory. Audits involve counting materials physically and comparing them to digital records. Using periodic inventory systems or cycle counting helps businesses stay updated without halting operations.
Use of Inventory Management Software
Inventory management software simplifies tracking and automates the process of recording raw materials inventory. These systems offer features like automated alerts for low stock, real-time inventory data, and inventory turnover ratio analysis, ensuring optimal stock levels.
Demand Forecasting
Accurate demand forecasting allows businesses to manage their raw materials better by predicting future needs. Tools like historical data analysis and trend projections help avoid material shortages and maintain an efficient supply chain.
Just-In-Time Inventory Systems
Just-in-time systems minimize excess stock by ordering raw materials only when needed. This reduces costs related to storage and obsolete materials. Successful implementations include manufacturing companies that prioritize lean production processes for efficiency.
Common Challenges in Raw Materials Inventory Management
Managing raw materials inventory can be complicated, especially for businesses with fluctuating demand. Here are some common challenges and strategies to overcome them:
Inaccurate Inventory Records
Businesses often struggle to record raw materials inventory accurately. This can lead to shortages or overstocking. Implementing an automated management system or conducting regular audits ensures that your raw materials inventory account reflects real-time stock levels.
Demand Fluctuations
Unpredictable demand makes it hard to maintain the right amount of raw materials. Using accurate inventory forecasting and analyzing historical data can help predict trends and maintain the proper balance of materials for production.
Overstocking and Obsolescence
Excessive inventory leads to higher costs and risks of materials becoming outdated. Utilizing just-in-time inventory systems helps reduce overstock and keeps inventory costs low by ordering materials only when necessary for the production process.
Supply Chain Disruptions
Supply chain issues can delay raw materials purchased, affecting production schedules. Building relationships with multiple suppliers and maintaining safety stock can help mitigate the impact of disruptions in the supply chain.
Poor Inventory Turnover
A low inventory turnover ratio ties up capital and storage space. Regularly assessing your raw materials inventory turnover and adjusting your purchasing strategies can ensure faster movement of inventory and better cash flow.
Conclusion
Understanding how to manage raw materials inventory is crucial for smooth business operations. By implementing best practices like regular audits, using software, and improving inventory turnover, businesses can control costs and optimize their production process.
You’re now equipped with strategies to better manage your raw material inventory. From tracking direct materials to handling indirect raw materials inventory, you can improve inventory accuracy and meet demand efficiently.
Proper inventory management will help you avoid shortages and overstocking, ensuring better financial health for your company.