Work in Progress (WIP) Inventory: Definition, Importance, and Calculations
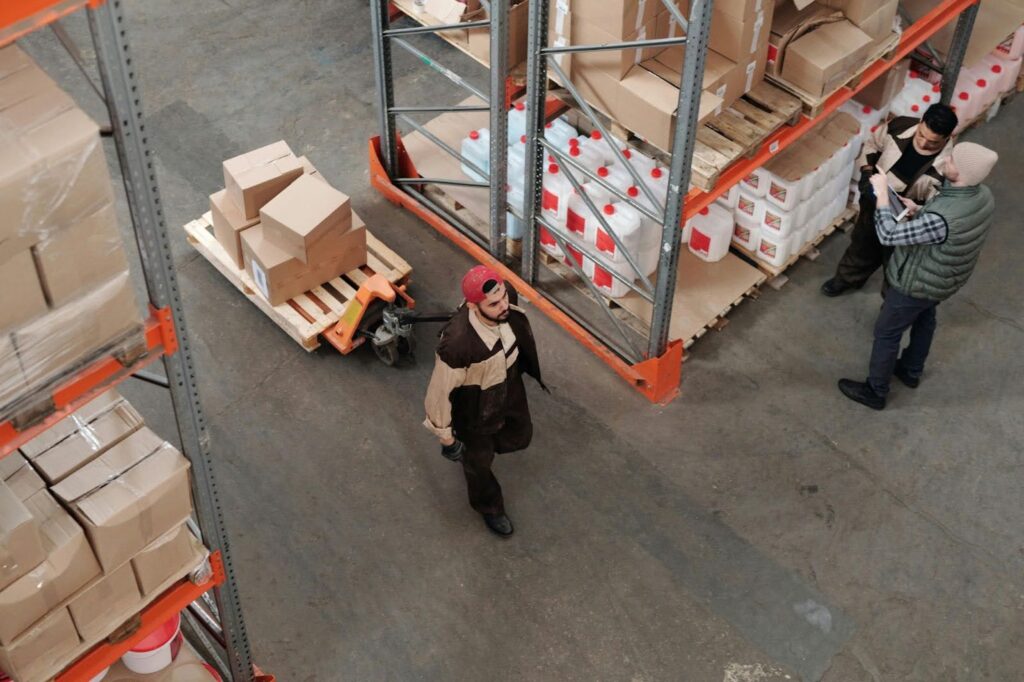
Understanding and managing work in progress inventory is essential for keeping your production process efficient and reducing manufacturing costs.
Running a successful business means keeping operations smooth, and that starts with managing inventory effectively. For manufacturers, work in progress inventory is one of the most critical areas to focus on.
Neglecting it can lead to delayed orders, inefficient production processes, and excess costs. Without proper oversight, businesses often struggle with tracking WIP inventory, causing production delays or stockpiles of unfinished goods.
Understanding and managing this type of inventory is essential for keeping manufacturing costs in check and ensuring a seamless supply chain management process.
In this blog, we will break down what work in progress inventory is, why it matters, and how you can manage it efficiently.
What Is Work in Progress (WIP) Inventory?
Work in progress inventory refers to items currently in the manufacturing process but not yet completed. These are products that have moved beyond raw materials but haven’t reached the finished goods stage.
For example, partially assembled cars on a factory floor or unbaked cakes in a bakery are considered WIP inventory. These inventory types play a critical role in the production process, acting as a bridge between raw materials inventory and finished goods inventory.
Managing it well ensures efficient transitions between stages, keeping the flow of production smooth. Ignoring process inventory leads to bottlenecks, delayed deliveries, and higher manufacturing costs.
Importance of Managing Work in Progress Inventory
Properly managing work in progress inventory is essential for maintaining efficient production processes and meeting customer expectations. Effective management ensures resources like labor costs, raw materials, and overhead are used optimally, preventing delays and excessive storage.
Well-organized WIP inventory management directly impacts cost management by reducing unnecessary holding costs and improving production speed.
Additionally, it plays a key role in supply chain operations, ensuring that each production stage is completed on time. Businesses with too much WIP inventory or poor management often face financial strain and production inefficiencies.
How to Calculate WIP Inventory
Efficiently managing work in progress inventory involves calculating its value accurately. Missteps here can lead to incorrect reporting on the balance sheet and affect financial decisions. Let’s break down the steps.
Beginning Work in Progress Inventory
Beginning WIP inventory refers to the value of partially completed goods at the start of an accounting period. It sets the foundation for calculating overall WIP. Businesses often track it using previous records, typically noted in the previous accounting period. Consistent updates and accurate inventory cycle counts help ensure accurate data for future calculations.
Raw Materials Used
Accounting for raw materials used is crucial for calculating WIP inventory. It includes all materials consumed during the manufacturing process. Keeping detailed records of material use prevents discrepancies and helps maintain a smooth production process. Proper tracking avoids unnecessary delays due to missing raw materials inventory.
Direct Labor Costs
Including direct labor costs in WIP is important. Labor costs reflect wages paid to workers who physically handle production. Businesses should use time-tracking systems or payroll data to ensure accurate cost allocation. Tracking direct labor helps businesses determine true production costs incurred for unfinished goods.
Manufacturing Overhead Costs
Manufacturing overhead costs include expenses beyond labor and materials, such as utilities, rent, and equipment depreciation. Allocating these costs to WIP requires a standardized approach. Many companies calculate overhead costs as a percentage of labor or materials. This ensures fair distribution across all stages of production.
Ending Work in Progress Inventory
Ending WIP inventory refers to the value of partially completed items at the end of the period. Businesses should conduct physical inventory counts or use automated systems to assess the remaining WIP value. Regular audits help businesses monitor their current WIP inventory for accuracy in financial reporting.
Work in Progress Inventory Formula
The formula for calculating WIP inventory is:
- WIP Inventory = Beginning WIP Inventory + Production Costs Incurred − Ending WIP Inventory
Each component must be tracked to get a clear understanding of the total WIP value, which impacts your company’s balance sheet and overall profitability.
Effective Strategies for Managing Work in Progress Inventory
Maintaining control over work in progress inventory ensures smooth operations and cost savings. Here are some proven strategies.
- Regular Inventory Audits: Routine audits help businesses track process inventory levels accurately by identifying discrepancies and ensuring records align with physical stock. Audits prevent overstocking and shortages, ensuring smooth flow through the production cycle.
- Inventory Management Software: Using inventory management software automates the tracking of WIP inventory. This improves accuracy and speeds up reporting, helping businesses track beginning WIP inventory cost more effectively.
- Lean Manufacturing: Adopting lean principles minimizes excess WIP inventory and maximizes production efficiency. By streamlining processes, businesses can avoid unnecessary steps, reduce waste, and improve flow. This approach aligns production with demand for optimized process inventory management.
- Setting Realistic Goals: Setting clear, attainable goals prevents overproduction and underutilization of resources. Managing WIP inventory with achievable targets helps businesses avoid too much or too little stock, keeping the beginning WIP inventory cost in check throughout the production process.
- Effective Communication: Effective communication between departments ensures proper resource allocation and reduces production delays. Streamlined collaboration prevents bottlenecks, especially when handling the flow of WIP inventory.
Using these strategies helps businesses avoid the pitfalls of poor WIP management, ensuring an efficient and cost-effective production cycle.
Benefits of WIP Inventory Management
Efficient work in progress inventory management offers significant advantages for businesses. It improves production efficiency, cuts down on costs, and keeps operations running smoothly.
Let’s explore the key benefits.
Improved Production Efficiency
Managing WIP inventory ensures smoother production processes by tracking raw materials and unfinished goods effectively. Keeping a clear record of current WIP inventory helps reduce bottlenecks and production delays.
A streamlined manufacturing process prevents disruptions, allowing companies to meet production goals efficiently, which ultimately results in faster delivery of finished products to customers.
Cost Savings
Accurate WIP inventory accounting reduces waste and unnecessary expenses. By properly tracking manufacturing costs like raw material costs and overhead costs, businesses can avoid excess purchases and storage costs.
Effective WIP inventory management leads to significant cost savings by optimizing resource use, avoiding overproduction, and keeping total manufacturing inventory under control.
Better Financial Reporting
Proper work in progress inventory management allows for more accurate financial data. By keeping track of WIP inventory value and ensuring the data is reflected on the balance sheet, businesses can produce clearer financial reports.
Accurate WIP data provides insight into total manufacturing costs and ensures transparency for stakeholders regarding production expenses and the current asset value.
Enhanced Supply Chain Management
Managing work in progress inventory ensures a steady flow of partially completed goods through the production cycle, preventing bottlenecks and delays. This approach supports the entire supply chain, ensuring timely delivery of finished products and meeting customer demands efficiently.
Properly controlled WIP avoids shortages or surpluses, ensuring that materials flow efficiently between suppliers and manufacturers, resulting in more timely deliveries of finished goods.
Increase in Customer Satisfaction
Proper management of WIP inventory helps businesses meet deadlines and deliver products on time. By avoiding production delays and backlogs, companies can keep customer expectations in check. Consistent, on-time delivery increases customer satisfaction, which in turn builds trust and loyalty.
An organized WIP inventory system ensures production runs smoothly, directly impacting customer experience positively.
Common Challenges in Work in Progress Inventory Management
Managing work in progress inventory presents several challenges. These challenges, if not addressed, can cause delays and increase costs.
Let’s take a look at the common issues and how to address them:
Inaccurate Tracking of Inventory Levels
Failing to accurately track work in process inventory leads to delays, shortages, or overstocking of raw materials and unfinished goods. Poor tracking increases process inventory costs and impacts production efficiency.
To avoid this, businesses must use reliable tools and conduct regular inventory cycle counts. Keeping the current WIP inventory value up to date with audits ensures accurate reporting. Consistent tracking also provides a clear WIP inventory example for better decision-making.
Inefficient Production Process Scheduling
Inefficient scheduling causes bottlenecks, leading to increased work in process inventory and production slowdowns. When schedules don’t match resource availability, unfinished goods accumulate, driving up process inventory costs. By optimizing schedules, businesses can ensure continuous production.
Adjusting production timelines based on demand forecasts and resource availability prevents delays. Proper scheduling ensures that the business calculates WIP inventory more accurately and avoids costly inefficiencies.
Lack of Coordination Among Departments
Poor coordination between departments leads to imbalances in work in progress inventory. Miscommunication between procurement, manufacturing, and sales teams can disrupt the flow of materials, leading to either surplus or shortage of inventory.
Businesses can improve coordination by using integrated planning systems and better communication tools, ensuring all departments are aligned in managing WIP inventory effectively.
Conclusion
Understanding and managing work in progress inventory is essential for keeping your production process efficient and reducing manufacturing costs. By effectively tracking beginning WIP inventory costs, allocating manufacturing overhead costs, and accurately calculating the ending WIP inventory value, businesses can ensure smooth operations.
Proper WIP management also supports the timely delivery of finished goods and helps control total costs. By applying the strategies discussed, you can now confidently handle your work in progress inventory, improving your production flow and minimizing associated costs.
These practices will not only streamline your production cycle but also strengthen your overall business operations.